A Deep Dive into Small Rock Drills: Design and Use
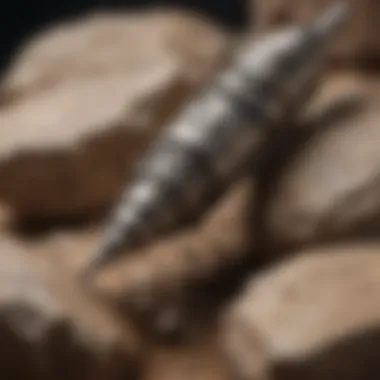
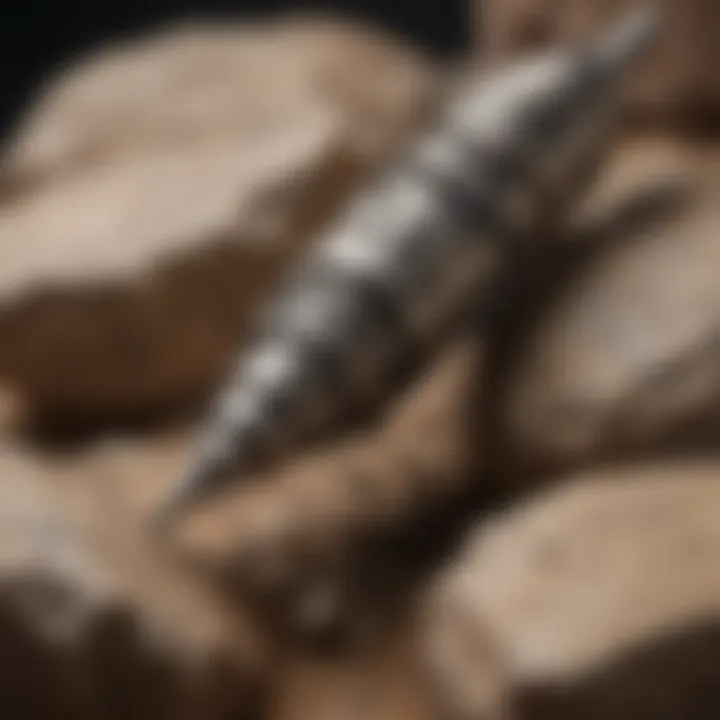
Intro
The world of small rock drills is far more intricate than one might initially presume. These devices, which appear quite unassuming, play a critical role in various fields such as geology, mining, and even construction. They are necessary tools that help professionals and collectors alike navigate through tough terrains and extract valuable geological specimens.
As we delve into this guide, we'll unravel the essence of small rock drills, uncover their designs, applications, and the nuances involved in their operations. With advancements in technology shaping the efficiency and reliability of these tools, having a comprehensive understanding is paramount.
Not only does this article aim to provide detailed insights on the subject matter, but it also intends to enhance appreciation for the intricacies involved in rock drilling endeavors. Whether you're a seasoned collector or a newcomer in the field, this guide is tailored to offer valuable information that resonates with your experience.
Types of Collectibles
Overview of Collectible Categories
In the realm of small rock drills, there is a rich variety of collectibles that enthusiasts often seek. Understanding these categories can assist in identifying what may be of interest for either practical usage or as part of a collection. Here are some prominent types:
- Vintage Drills: Tools that hark back to earlier designs, often rich in history and craftsmanship. Many collectors find joy in restoring these artifacts.
- Industrial Drills: Modern machines primarily used in mining or construction settings, these tools boast advanced technology but may lack the nostalgic value.
- Miniature Replicas: Tiny versions of larger drills serve decorative purposes or can be educational tools for teaching about geological processes.
In-Depth Look at Each Category
- Vintage Drills
Collectibles in this category often possess unique engineering feats that speak volumes of their era. Think of a classic hand-cranked drill from the late 1800s, showcasing intricate gears and craftsmanship. Their value not only lies in their aesthetic appeal but also in the stories they carry. - Industrial Drills
The evolution of technology is represented well through industrial rock drills. These machines are typically designed for power and efficiency, featuring tools like the Atlas Copco DM45. Collectors often appreciate these models for their functional prowess and reliability in challenging conditions. - Miniature Replicas
These attractive little tools capture the eye. Not only do they provide insight into the workings of larger machines, but they are also visually appealing items to display. Their simplicity and charm can often mislead many into thinking they lack value, but they can be surprisingly sought after in dedicated circles.
"Collecting goes beyond acquisition; itβs about contextualizing the narratives encapsulated within every tool."
Identification Techniques
Essential Tools for Collectors
For anyone aspiring to venture into the world of rock drilling collections, knowing your tools is essential. Here are some must-have items:
- Magnifying Glass: This is key for examining fine details on older models, where manufacturers often applied unique features that could indicate age.
- Caliper: A reliable method to measure and identify specific dimensions, allowing collectors to compare tools accurately.
- Camera: Documenting acquisitions with photos ensures you keep meticulous records, which is valuable both for insurance and historical contexts.
Identification Methods for Rocks and Minerals
When we discuss small rock drills, they often operate in various geological settings, making an understanding of the material essential. Hereβs how to go about it:
- Visual Inspection: Observe color, texture, and structural attributes. Different rocks tell different stories.
- Scratch Test: Evaluate hardness using common items to ascertain minerals, which can provide insights into which drill would be most effective.
- Use of Acid: Some minerals react to acid, and understanding these reactions helps collectors make educated estimations.
Understanding these identification skills can vastly improve the collector's journey and ensure well-rounded knowledge that can be shared with peers. This guide aims to equip you with these essentials and invite a deeper connection with the world of small rock drills.
Intro to Small Rock Drills
Small rock drills hold a significant place in various fields such as mining, construction, and geological survey. Understanding them is not merely an academic exercise; it's a need rooted in practical applications. As professionals and enthusiasts navigate the complexities of geology, these tools emerge as essential allies. Their design and functionality dictate not just efficiency but also safety and potential successes in their respective ventures.
Definition and Purpose
In simplest terms, a small rock drill is a portable tool that's used to bore into rock, primarily for tasks that require precision and control. Whether itβs creating holes for blasting in mining or making core samples for studies, these devices serve pivotal purposes.
When we talk about their purpose, it's important to recognize the various forms they manifest in: pneumatic, electric, and hydraulic. Each type is tailored for specific circumstances and environments, allowing users to tackle different rocking conditions effectively. Think of them as the Swiss Army knives for rock drillingβadaptable, reliable, and indispensable in both amateur and professional hands.
Historical Context
To appreciate the modern small rock drill, one must take a step back in time. The inception of rock drilling can be traced back to ancient civilizations that used rudimentary tools fashioned from wood and stone. The pursuit to penetrate hard rock is as old as construction itself, serving crucial roles in infrastructure developmentβfrom roads to buildings.
Over the centuries, innovations occurred; the 19th century saw the advent of steam-powered drills. Then, in the 20th century, the shift to electrical and pneumatic drills revolutionized the industry. These advances made drilling not just faster, but also safer, as operators could maintain a greater distance from dangerous explosive sources.
Each evolution reflects a response to the changing demands of industries engaged in rock excavation, demonstrating how technology grows hand-in-hand with human needs. The historical backdrop isnβt simply about the machinery; it showcases humanityβs unwavering quest to understand and manipulate our world.
"The development of drilling technology has been a window into the broader technological advancements of society itself."
Understanding this context gives depth to our current appreciation of small rock drills; observing how far weβve come helps inform the direction we should aim toward in the future.
Types of Small Rock Drills
When it comes to small rock drills, understanding the various types is key to grasping how they operate and their specific uses. Each type, be it pneumatic, electric, or hydraulic, has its own set of strengths and considerations. These distinctions not only affect performance but also influence the overall user experience, which is essential for anyone involved in rock drilling activities. Grasping the nuances of these drill types can assist rock and fossil collectors in selecting the right equipment for their unique needs, thereby enhancing their drilling efficiency.
Pneumatic Rock Drills
Pneumatic rock drills are powered by compressed air, making them a favored choice in many mining and construction settings. Their light weight and high power output make them quite attractive for work in confined spaces or steep terrain.
The operation of pneumatic drills runs on a principle that many might find fascinating. As air rushes through the drill, it creates a hammering effect that breaks up the rock. This mechanism is efficient, enabling the drills to perform rapid and effective drilling tasks, particularly in harder geological formations.
Benefits of Pneumatic Rock Drills:
- Portability: Their light weight allows for ease of transport.
- Versatility: They can be adeptly used in various fields, from mining to geological surveys.
However, itβs not all sunshine and rainbows.
Using pneumatic drills can sometimes lead to overexertion and fatigue, particularly if the operator is not acclimatized to the strenuous nature of the work. Additionally, the reliance on compressed air means operators must ensure a steady supply, which can be a limitation in remote locations.
Electric Rock Drills
Electric rock drills stand as a testament to modern engineering. They operate using electric power, which offers a clean, quiet, and efficient alternative to their pneumatic counterparts. Many users appreciate how electric drills contribute less to noise pollution, making them suitable for urban settings or work that requires less disturbance.
These drills are often equipped with advanced features like variable speed settings and electronic controls, granting users the ability to customize their drilling experience.
Key Considerations for Electric Rock Drills:
- Stable Power Supply: Electricity provides a consistent power source, crucial for prolonged use.
- User-Friendly: Their intuitive design makes them easier to operate for novices.
That said, electric drills do come with their own set of challenges. They often require a reliable power source, and when operating in the field, this can become a logistical challenge. Moreover, they may not be as effective in extremely rugged terrains compared to pneumatic drills.
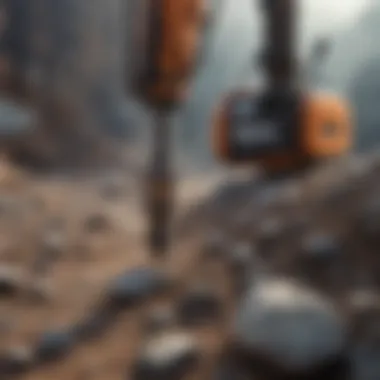
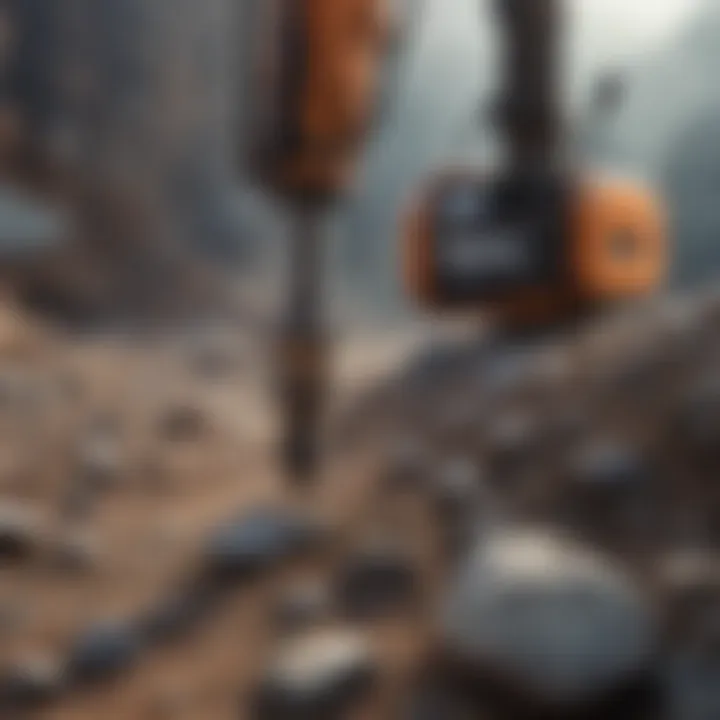
Hydraulic Rock Drills
Hydraulic rock drills utilize pressurized hydraulic fluid to drive their operations. This type provides powerful drilling capabilities, typically seen in larger-scale projects. The force generated by hydraulic systems allows for exceptional penetration rates, making them ideal for difficult geological conditions.
Often these drills are seen on large construction sites or mining operations where it is critical to break through tough rock layers quickly.
Advantages of Hydraulic Rock Drills:
- High Power Output: They can handle more extensive drilling tasks effortlessly.
- Durability: Built for heavy-duty performance, these drills tend to have a longer lifespan.
However, hydraulic drills are not necessarily the best option for smaller projects or on-site uses due to their weight and size. They often require specialized operators and can entail higher operating costs just due to their sheer power and complexity.
In summary, the choice among pneumatic, electric, and hydraulic rock drills depends heavily on the specific context and expected tasks. Each type has its pros and cons that align differently depending on the projects at hand. Understanding these distinctions is vital for any user, especially for rock collectors aiming to deepen their knowledge and improve their practical skills.
Key Components and Mechanisms
Understanding the key components and mechanisms of small rock drills is essential for anyone interested in rock collection, geological surveys, or construction. This section digs into the three pivotal elements: drilling tools, power sources, and control systems, each contributing significantly to the drill's overall function and effectiveness.
Drilling Tools
Drilling tools are the heart and soul of any rock drill. They dictate not only the efficiency of the drilling process but also the quality of the samples obtained. The type of drill bit chosen impacts the depth and speed of penetration into the rock. Common materials for drill bits include tungsten carbide and high-speed steel, known for their durability and reliability under pressure.
When selecting drilling tools, factors like rock hardness, geological formations, and project specifications must be considered. For instance, in softer formations, a flat-bottomed drill bit might work wonders, whereas harder rock may require more robust, specialized bits, like those designed for core drilling.
Power Source
The power source determines the drill's capabilities, and various options are available depending on the project's needs. Pneumatic systems, powered by compressed air, offer high portability and effectiveness in remote locations. Electric models, on the other hand, provide a steady power supply and are favored in more controlled environments such as construction sites. Then we have hydraulic drills that deliver exceptional force, ideal for larger projects requiring hefty penetration power.
Choosing the right power source can greatly influence productivity. An electric drill might not be cut out for a rugged mining site, just as a pneumatic drill may struggle in a confined space where a stable electrical supply is available. Thus, understanding the nuances of each power source plays a pivotal role in achieving optimal drilling performance.
Control Systems
Control systems are what tie everything together, offering usability and safety for operators. Advanced small rock drills now come with sophisticated control mechanisms that help monitor the drilling process in real-time. These systems can filter noise, track depth, and manage power distribution.
Furthermore, modern control systems often integrate sensor technology to provide feedback on the drill's performance. This way, users can adjust operation dynamics, translating to reduced wear and extended equipment longevity. Incorporating user-friendly interfaces has also become a norm, allowing even novices to handle drills effectively with minimal training.
"Choosing the right components can mean the difference between smooth operations and costly contracts."
This adage holds true across various drilling applications, emphasizing the importance of thoroughly understanding how these components work collectively.
In summary, recognizing these key components and mechanisms is of utmost importance to anyone working with small rock drills. The right mix can lead to enhanced efficiency, lower operational costs, and improved results in rock-related endeavors.
Applications of Small Rock Drills
The applications of small rock drills represent a vital facet within the broader context of geology and construction. These drills arenβt just tools; they play a significant role in various industries that hinge on the ability to penetrate rock for exploration or development. Understanding their applications aids in appreciating their importance to tasks such as mining and construction and drives home the necessity for ongoing technological advancements in this arena.
Mining Operations
Mining operations were perhaps the first arenas where small rock drills found their footing. The intricate nature of the underground rock layers requires precision and efficient drilling to access valuable minerals and resources. Small rock drills, like the Atlas Copco BBD or the Sandvik DXR, are tailored for this environment, offering powerful drilling capabilities without contributing to excessive surface disruption.
These drills facilitate a variety of tasks such as:
- Exploratory drilling to locate mineral deposits.
- Production drilling to create access points for extraction.
- Blasting preparation, where drills create holes for explosives.
Moreover, modern mining technology has honed in on the maximization of drilling speed and accuracy while minimizing operational downtime. This is particularly crucial in the context of fluctuating market demands where efficiency could spell the difference between operative viability and extinction.
Geological Surveys
In geological surveys, small rock drills serve a different yet equally crucial purpose. Their role in obtaining core samples can't be overstated. Geologists rely on these samples to assess ground conditions and determine the structural characteristics of rocks before any construction activities begin.
The utility of small rock drills in geological surveys includes:
- Sampling: Collecting core samples that provide insights into the rockβs composition and structure.
- Assessment of Risks: Understanding potential geological hazards that could affect construction projects.
- Environmental Assessments: Evaluating the impact of proposed activities on the surrounding area.
Such surveys are foundational for making informed decisions, ensuring that the built environment interacts seamlessly with its geological context, all while adhering to necessary sustainability practices.
Construction Projects
Lastly, small rock drills are indispensable in a multitude of construction projects. From urban development to infrastructure expansion, drilling is often a prerequisite to laying foundations, installing utilities, or even tunneling.
In construction, the utility provided by drills can be summarized succinctly:
- Foundation Preparation: Drilling for deep foundations or support structures to ensure stability.
- Utility Installation: Creating pathways for plumbing, electricity, and data lines underground.
- Tunneling: Facilitating subsurface structures such as transit systems or pipelines.
The ability to adapt tools to various soil and rock types, along with ongoing innovations in drill design, allows for significant efficiency increases. This adaptability not only boosts productivity but also leads to innovative solutions to problems like worker safety and environmental challenges.
"The right small rock drill can be the difference between a smooth operation and a site marred by delays."
As the industries evolve, so too will the applications of small rock drills, cementing their status as indispensable tools across multiple sectors.
Factors Influencing Performance
Understanding the factors influencing performance is crucial when it comes to small rock drills. These elements play a significant role in determining not just the efficiency of the drilling process, but the longevity of the equipment itself. By grasping these influences, users can make informed decisions, ensuring that their drilling operations are both effective and sustainable.
Rock Types and Conditions
When drilling occurs, the type of rock and the conditions under which one is working can drastically impact performance. Hard rocks like granite or basalt pose different challenges than softer sedimentary rocks such as limestone or sandstone. For instance, harder rock requires more power and greater durability in drill bits. If an operator is using a pneumatic rock drill, they might find that their drill struggles with tougher material, leading to slower progress and potential wear.
Furthermore, environmental conditions canβt be overlooked. Wet conditions can cause mud accumulation, hindering drilling efficiency, while dry, dusty environments might lead to overheating of the drill. Temperature also plays a crucial role; too hot, and drills can overheat, too cold, and they might not operate at peak efficiency. Accurate assessment of these conditions often translates into better planning and the choice of appropriate equipment.
Drilling Techniques
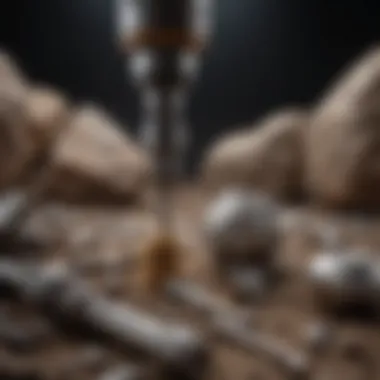
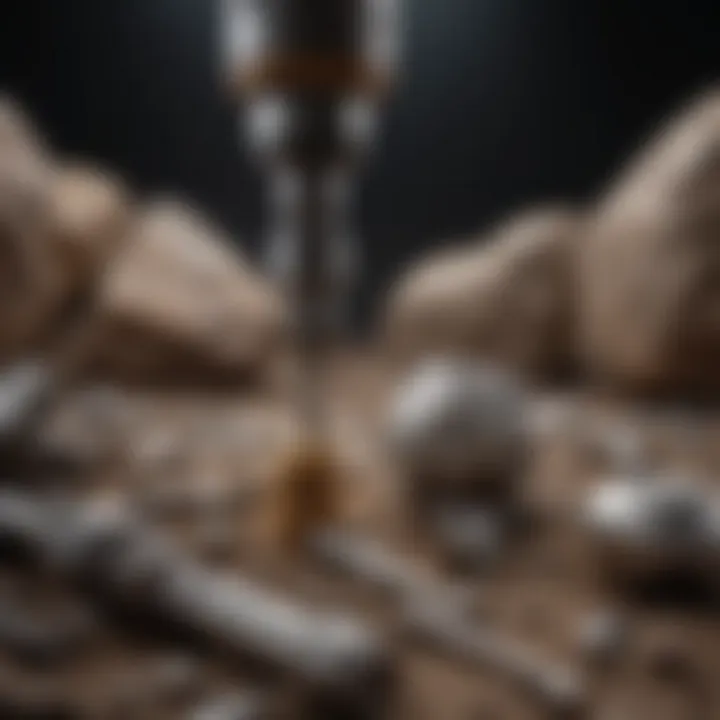
Next up is the influence of different drilling techniques on performance. Not all drilling methods are created equal; varying techniques have distinct advantages based on the project and material.
- Rotary Drilling: Best for soft rock, using a rotating drill bit that cuts through material. Itβs fast and efficient but might struggle with harder types.
- Percussive Drilling: This method uses rapid hammering movements to break up tough rock. Particularly effective for drilling through dense materials, though it can come at a higher energy cost.
- Core Drilling: Often used for geological surveys, core drilling allows for extraction of rock samples, providing insights about subsurface conditions. Itβs a slower process but very informative.
Operators must weigh these methods against project requirements. Choosing the right drilling technique can significantly bolster performance and efficiency, thus affecting both the timeline and cost of a project.
"Choosing the right rock drill and technique can be the difference between a smooth operation and a costly delay."
By understanding the rock composition and selecting appropriate drilling techniques, users can optimize their approach, minimizing downtime and maximizing output.
Operational Techniques
Operational techniques stand as the backbone of efficient and safe drilling practices. Understanding how to properly execute setup, drilling, and safety protocols can make all the difference in achieving optimal results with small rock drills. A well-structured approach ensures that equipment performs at its best while minimizing risks to both the operator and the environment.
Setup Procedures
Setting up a small rock drill requires precision and attention to detail. The initial steps often involve selecting the appropriate site and ensuring the drill is well-suited for the type of rock being targeted. Here are some key points to bear in mind during setup:
- Site Assessment: It's crucial to evaluate the geological conditions beforehand. Factors like rock hardness, moisture content, and potential hazards must be considered.
- Drill Placement: Position the drill where it can access the target rock effectively. This may require adjustments based on terrain and surrounding infrastructure.
- Attachment of Tools: Ensure that the drilling tools are compatible with the drill and securely attached. Loose tools can cause not only inefficiencies but also accidents.
Following these steps not only enhances drilling effectiveness but also extends the lifespan of the equipment.
Drilling Processes
Once setup is complete, the actual drilling process begins. This stage requires a methodical approach to ensure efficiency:
- Start-Up: After confirming all parameters are in place, power up the drill. Monitor all indicators for any abnormalities.
- Drilling Technique: Employ the right technique depending on rock type and drill capability. For instance, using a ''percussive'' method may be more effective in hard rock environments.
- Monitoring and Adjusting: Regularly check the drilling depth and resistance. Make adjustments to pressure and speed as necessary to maintain steady progress.
An effective drilling process relies heavily on the operator's ability to adapt to changing conditions, underscoring the need for experience and intuition.
Safety Protocols
Safety cannot be overstated in the context of small rock drills. Following stringent safety protocols can safeguard the operator against dangers inherent in drilling activities. Key protocols include:
- Personal Protective Equipment (PPE): Always wear appropriate gear, including helmets, gloves, and ear protection.
- Equipment Checks: Conduct routine inspections of the drill and associated tools before starting work. Look for wear and tear and address potential issues promptly.
- Emergency Procedures: Ensure all team members are aware of emergency protocols in case of an accident. This includes knowing the location of first-aid kits and emergency shut-off switches for the equipment.
"Prioritizing safety measures not only protects the workforce but also enhances productivity in the long run."
In summary, operational techniques are critical for achieving the intended outcomes when using small rock drills. Each phaseβfrom setup to drilling and safetyβis interconnected, contributing to the effectiveness and safety of the entire drilling operation. With proper techniques, the challenges inherent in drilling can be navigated more smoothly, leading to successful projects.
Maintenance and Care
Maintaining small rock drills is not just useful; it's essential. It ensures that these valuable tools perform optimally in various rock states. Regular maintenance improves the lifespan of the equipment, reduces the chances of unexpected breakdowns, and ultimately saves money by preventing heavy repairs. If you view your rock drill as an investment, caring for it like one should be a no-brainer. Think about it: little attention to maintenance can lead to a world of hassle down the line.
Regular Inspection
Regular inspections are a cornerstone of effective maintenance. While it might feel like a tedious task, consider it a form of preventive medicine for your equipment. These inspections typically check for wear and tear, adequacy of lubrication, and proper functioning of the components.
- Visual Checks: A quick once-over can reveal cracked cases or loose fittings. Look for any external damage that might escalate into larger issues.
- Operational Tests: Running the drill briefly can help identify unusual noises or vibrations. If something seems off, nip it in the bud.
- Lubrication Levels: This is often overlooked. Ensure that all moving parts are adequately lubricated to reduce friction and heat generation. An ounce of prevention is worth a pound of cure.
"A stitch in time saves nine" is especially true in machinery care. Address small issues before they snowball into significant breakdowns.
Repairs and Troubleshooting
Even with the best maintenance, issues may arise during the operation. Knowing how to tackle these problems can save time and ensure ongoing productivity with your rock drill.
- Identifying Problems: Familiarize yourself with common issues. For instance, if you notice decreased drilling efficiency, it may be a sign of a dull bit or improper calibration.
- Tools Required: Having basic tools on hand like wrenches, screwdrivers, and replacement parts is crucial for quick repairs. Itβs like having a first-aid kit for your rock drill.
- Troubleshooting Guide: Refer to the manufacturerβs manual for a troubleshooting guide that outlines potential issues and fixes. Follow this guide closely to avoid unintended damage.
- Replace: If a part is broken, simply replacing it may save more trouble.
- Seek Expertise: If you hit a wall and can't figure it out, donβt hesitate to consult a professional. Trying to fix complex issues without proper knowledge can lead to more injuries to both the machine and yourself.
Maintaining and caring for small rock drills might require a little effort, but the benefits outweigh the costs. With regular inspection and a clear repair strategy, you can enhance your equipment's life and effectiveness, which is invaluable for rock and fossil collectors striving for the best tools in their field.
Technological Advancements
The landscape of small rock drills has transformed significantly over the years, largely due to groundbreaking technological advancements. As these machines are essential in various industries, understanding their evolution and the new innovations they incorporate becomes crucial. Enhancements in performance, efficiency, and safety are hallmarks of the latest technological developments in small rock drills.
Innovative Designs
Innovative designs play a pivotal role in the efficiency and usability of small rock drills. These designs often prioritize ergonomics, allowing operators to handle equipment with greater ease and comfort. For instance, many new drills feature a lightweight construction, which reduces fatigue during prolonged use. The shift towards more compact designs also aids in accessing hard-to-reach areas.
Additionally, the incorporation of modular designs allows users to easily swap out components based on specific drilling requirements. This versatility not only enhances functionality but also lowers the overall cost of ownership since repairs and upgrades are simplified.
Another notable advancement is vibration reduction technology. Drills now feature systems designed to minimize vibrations, dramatically improving user comfort and safety. Minimized vibrations not only improve control but also extend the lifespan of the equipment by reducing wear and tear on components.
Integration of Technology
Integrating cutting-edge technology into small rock drills has revolutionized how they are operated and maintained. One of the most significant advancements is the use of smart sensors and telemetry systems. These sensors can monitor various parameters, such as temperature, pressure, and operational speeds, in real-time. By collecting this data, users can optimize performance and anticipate maintenance needs before issues arise.
Moreover, the adoption of battery technology in small rock drills signals a shift towards more environmentally friendly solutions. Modern, battery-operated drills not only eliminate the need for cumbersome cords or fuel tanks but also reduce harmful emissions commonly associated with traditional drilling methods. This transition aligns well with the growing emphasis on sustainable practices within the rock drilling industry.
"The evolution of small rock drills is not just about drilling deeper; it's about drilling smarter."
Environmental Considerations
The environmental considerations in the use of small rock drills play a pivotal role in ensuring sustainable practices within the industry. Thoroughly understanding these implications not only safeguards ecosystems but also enhances the respect for the land we operate on. As rock drills penetrate the earth, they alter landscapes, sometimes irrevocably, prompting the need to evaluate their ecological footprint. This section brings attention to the delicate balance between operational efficiency and environmental stewardship.
Impact on Ecosystems
Small rock drills can significantly impact ecosystems, particularly during geological surveys and construction projects. The process of drilling into the earth disrupts soil layers, affecting water retention and altering habitats. For example, a drilling operation in a forested area might remove vegetation, leading to soil erosion and loss of wildlife habitats. When exploring rock formations, itβs essential to conduct assessments to ensure minimal disruption to local flora and fauna.

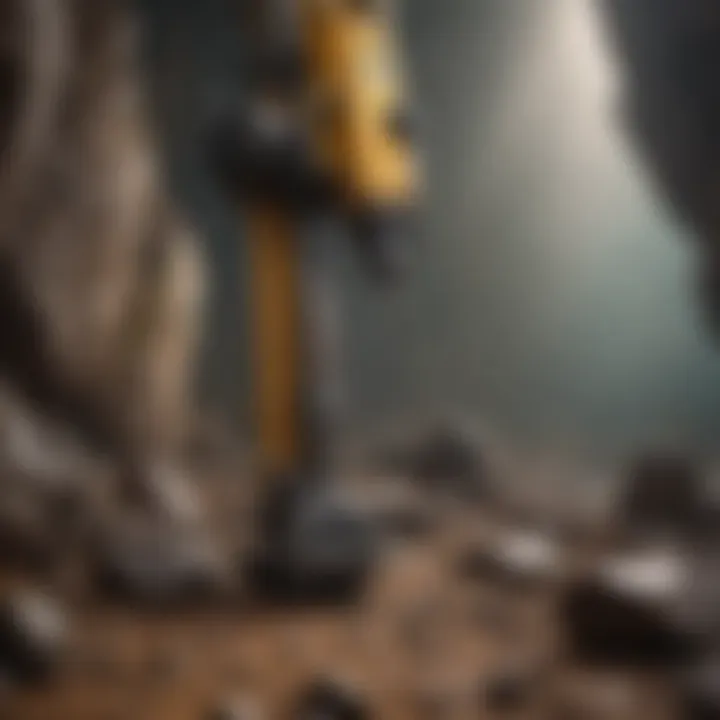
Moreover, the drilling can lead to the release of dust and pollutants into the air, which can affect both plant and animal life. Furthermore, when drilling near marine areas, the risk of sedimentation and contamination can threaten aquatic ecosystems. Thus, it is crucial for operators to adopt strategies that minimize these disruptive effects, such as conducting environmental impact assessments and adhering to regulatory guidelines.
The careful consideration of ecological impact during drilling operations protects not just the immediate area but future generations who rely on these ecosystems.
Sustainable Practices
In light of the challenges facing the environment, many companies are now opting for sustainable practices concerning small rock drills. These practices aim to mitigate adverse impacts while optimizing performance. Here are a few notable examples:
- Use of Eco-Friendly Drilling Fluids: Switching to biodegradable fluids can significantly reduce pollution during the drilling process. Traditional drilling compounds may harm the soil and water supplies, but newer alternatives help minimize this risk.
- Energy Efficiency: Implementing electric or hybrid drill models over traditional gas-powered units can decrease greenhouse emissions. In regions where electrical resources are available, this transition is not just feasible but prudent, reducing the overall carbon footprint.
- Rehabilitation Plans: Post-operation land rehabilitation is essential. This means restoring disturbed areas to their natural state, through replanting native species and ensuring that wildlife can regain habitat.
- Education and Training: Educating drill operators about sustainable practices ensures that they follow best practices on-site. Awareness can lead to more mindful operations that prioritize ecological considerations.
Incorporating these sustainable practices ultimately benefits not only the environment but also the industry as a whole. Collectors and professionals can appreciate the significance of responsible drilling, reinforcing the need for behaviors that respect both natural resources and operational integrity.
User Experiences and Case Studies
Understanding the practical applications of small rock drills often comes down to the experiences of those who use them in the field. User experiences and case studies provide a goldmine of insights that can inform potential buyers and users. It's one thing to read about features and specifications, but hearing about real-world encounters adds a level of authenticity that's hard to beat.
Practical insights from users enhance the overall understanding of how these drills operate in various environments, from construction sites to mining operations. These experiences reflect the trials, triumphs, and nuances that often escape technical manuals. Consequently, they bring forward issues such as reliability, efficiency in specific rock types, and the ergonomic considerations that make daily operations easier or harder.
When evaluating small rock drills, itβs prudent to look beyond the brochures and technical data sheets. Case studies can shine light on what works well and what doesn't, based on firsthand accounts. Are there specific drills that perform better in certain geological conditions? How does the ease of maintenance translate into downtime and operational costs in the long run? These are the kinds of details that can tip the scales in favor of one model over another, all depending on real user feedback.
Practical Insights
Real-world testimonials reveal a myriad of practical insights that can help operators make educated decisions. For instance:
- Drilling Speed: Many users have noted that pneumatic models like the Atlas Copco Cobra outperform electric versions in terms of speed in soft rock. However, they also reported that this speed comes at the expense of precision, which might be vital in geologically sensitive areas.
- Weight and Portability: Users working in confined spaces emphasize the importance of weight. Many extol the virtues of lighter models such as the Makita HM0810T for their ease of handling, suggesting that weight can markedly affect usability in tight environments.
- Maintenance Frequency: According to various operators, drills requiring lesser maintenance often lead to reduced operational disruptions. A notable case study from a mining company highlighted their switch from a traditional model to the Chicago Pneumatic CP-001 which required fewer part replacements. They reported a significant reduction in downtime, proving the solid investment.
Overall, these practical insights help craft a clearer picture of what itβs like to use small rock drills in various settings, shedding light on their strengths and weaknesses from the user's perspective.
Industry Testimonials
Industry testimonials serve as a powerful testament to the reliability and performance of these drills; they offer a modern day's word-of-mouth marketing. A few notable quotes from industry professionals can encapsulate what many feel about small rock drills. For example:
βUsing the HILTI TE 6-A22 has transformed our operations. The drillβs battery longevity allows us to work longer hours without constantly swapping out batteries. Itβs a true game-changer in rocky terrains.β β Emily Thompson, Construction Foreman.
- Flexibility in Operations: Operators often cite flexibility as a key factor. Testimonials from users suggest that models with interchangeable bits, like the Bosch GB8V-26, allow for more versatile applications without needing a complete set of different drills.
- User-Friendly Design: Many emphasize the intuitive design of modern drills. A landscape contractor noted that the compact design of the Dewalt DC33B was a significant advantage when working on projects in narrow spaces, resulting in enhanced user satisfaction.
- Environmental Efficiency: With growing concern over eco-friendliness, users are pleased with advancements in electric drill technology. As Mark Rivera, a sustainable construction expert mentions, βThe reduced noise and low emissions of the newest electric models make my work environment significantly better. Itβs a win-win.β
These testimonials serve to provide potential buyers with not just facts, but relatable experiences that help them see the real-world functionality of small rock drills in operation. In light of this, user experiences and case studies comprise an indispensable part of the conversation surrounding these powerful tools, adding depth and practical relevance to the scholarly discourse.
Economic Aspects
Understanding the economic factors that surround small rock drills is essential for anyone interested in the industry. These tools are not just technical marvels; their financial implications play a significant role in how they are designed, produced, sold, and ultimately used in the field. The economic aspects of small rock drills encompass various considerations, including cost analysis, market demand, and the overall economic impact on industries utilizing these tools.
Cost Analysis
When it comes to small rock drills, the financial side can be complex. First off, the upfront cost of acquiring these machines might appear intimidating, particularly for newer companies or smaller operations. Prices can vary widely due to factors like brand, technology, and specifications. For instance, basic pneumatic models might start at a lower price point compared to more sophisticated electric or hydraulic options that boast advanced features.
Here are some key elements to consider in cost analysis:
- Initial Investment: The purchase price of the drill is just the beginning. Buyers need to factor in operational costs, maintenance expenditures, and any necessary accessories that might raise the overall budget.
- Long-Term Value: A more expensive yet durable drill can yield better performance and efficiency, translating into cost savings over time through reduced operational failures or maintenance requirements.
- Financing Options: Many companies offer leasing programs, allowing businesses to acquire high-quality equipment without the heavy burden of upfront costs. This can be especially beneficial for small firms still trying to establish themselves vertically in the market.
- Depreciation: Small rock drills, like any heavy machinery, depreciate over time, which can affect a company's resale strategy down the line. Being aware of the depreciation rates can aid in their financial planning.
Market Trends
The market for small rock drills is influenced by several factors, ranging from technological innovations to changes in industry demand. Being aware of these trends can help collectors, investors, and companies alike make informed decisions. Here are some noteworthy market trends:
- Technological Advancements: As with many industries, technology is rapidly evolving. New features, like automation and improved ergonomics, are becoming standard in modern drills. This not only enhances performance but also drives consumer demand for the latest models, affecting market price points.
- Sustainability Efforts: Growing awareness of environmental concerns has fueled a demand for drills that are not only efficient but also designed with eco-friendly practices in mind. Manufacturers that incorporate sustainable practices into their production processes are likely to gain a competitive edge.
- Global Demand: The rising demand for minerals and raw materials is propelling the market for small rock drills. In developing regions, these tools are essential for mining operations, which in turn affects their availability and market price.
- Market Competition: As more companies enter the industry, competition increases, leading to better pricing and more options for consumers. This competitive landscape can prompt companies to innovate, ultimately benefiting end-users.
An informed perspective regarding the economic aspects of small rock drills not only enhances strategic decision-making but also supports long-term sustainability in both business and environmental contexts.
Future Prospects
Discussing the future prospects of small rock drills sheds light on the continuous evolution and adaptation in this industry. The advancements in technology and shifts in market demands will greatly influence the designs and functionalities of these tools. Understanding these trends is crucial for rock and fossil collectors and professionals, as it helps them stay ahead in a competitive environment. By acknowledging the nuances in emerging technologies and market developments, one can certainly make informed decisions in acquiring and utilizing rock drills.
Emerging Technologies
As we look ahead, one can't overlook the impact of emerging technologies on small rock drills. Manufacturers are increasingly exploring automation and artificial intelligence to enhance the efficiency and precision of these tools. For instance, sophisticated sensors could be integrated into drills, allowing for real-time monitoring of drilling conditions. This can significantly reduce wear and tear, thereby extending the lifespan of equipment.
Moreover, 3D printing is making inroads into the creation of drill components. With this technology, manufacturers can produce lightweight, durable parts tailored for specific drilling tasks, leading to significant improvements in performance.
A noteworthy trend is the development of smart rock drills that can analyze geological data on-the-fly. These drills could potentially adapt their operation based on real-time feedback, optimizing drilling parameters for the type of rock encountered. This flexibility might just be the game changer in not only mining but also in construction projects that require utmost precision.
Potential Market Developments
Looking at potential market developments, it's clear that the small rock drill industry may see diversification in the applications of these tools. With an increasing focus on sustainable practices, more players are expected to introduce eco-friendly models powered by renewable energy sources.
The demand for skilled operators is also likely to rise as new technologies emerge. Thus, further training and education in handling advanced equipment will be paramount for professionals in this field. This development opens doors for creating specialized courses tailored to rock drill operations.
Investors will also be keeping a close eye on the global construction and mining markets. Countries that are ramping up infrastructure projects will form vital arenas for market growth. Furthermore, as urbanization continues, the need for effective geological surveys becomes more pronounced, leading to a surge in demand for efficient small rock drills.
As we approach a future ripe with innovation and opportunity, the significance of staying properly informed cannot be overstated. Evaluating these prospects helps professionals and collectors alike position themselves advantageously and cradle the evolution of small rock drills into their practices.
"In an ever-changing market, adaptability is key to survival and success."
In summary, the future of small rock drills is bright, filled with technological advancements and new opportunities. Being proactive about these developments will put users in a favorable spot to thrive in the rock drilling landscape.
Culmination
The conclusion serves as a pivotal element in encapsulating the essence of this article. It synthesizes the key insights gathered through the previous sections while reinforcing the significance of small rock drills in various contexts. Understanding the nuances of small rock drills allows not only for better operational practices but also greater appreciation for their role in the realms of mining, construction, and geological studies.
Summary of Insights
Throughout this article, we have explored the intricate details that define small rock drillsβfrom their mechanical components and types to their diverse applications. Each aspect discussed highlights how these tools are not merely instruments, but essential assets in various industries. The emphasis on technological advancements and user experiences provides a broader perspective on their evolution and relevance, demonstrating their adaptability in the ever-changing landscapes of geology and mining. The performance factors, along with maintenance and care recommendations, underline the need for diligence in preserving these tools. By maintaining proper functions and adopting best practices, users can significantly enhance the efficiency and longevity of their equipment.
Final Thoughts
In closing, the dialogue around small rock drills transcends mere technical discussions. It calls forth the need for an informed and proactive approach toward these indispensable tools. For rock and fossil collectors in particular, recognizing the impact of technological evolution on these equipment can enrich their understanding and appreciation of geological endeavors. Investing time into learning about small rock drills is not only beneficial for operational knowledge but also fosters a deeper connection between the collector and the tools that shape our exploration of the Earth's hidden treasures. As we look toward the future of geological practices, small rock drills will continue to be at the forefront of innovation, continually shaping the way we interact with the planet's geological wonders.