Comprehensive Guide to the Small Jeweler's Torch
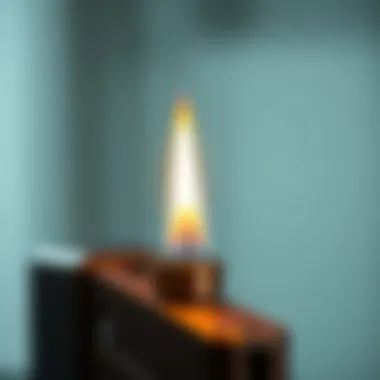
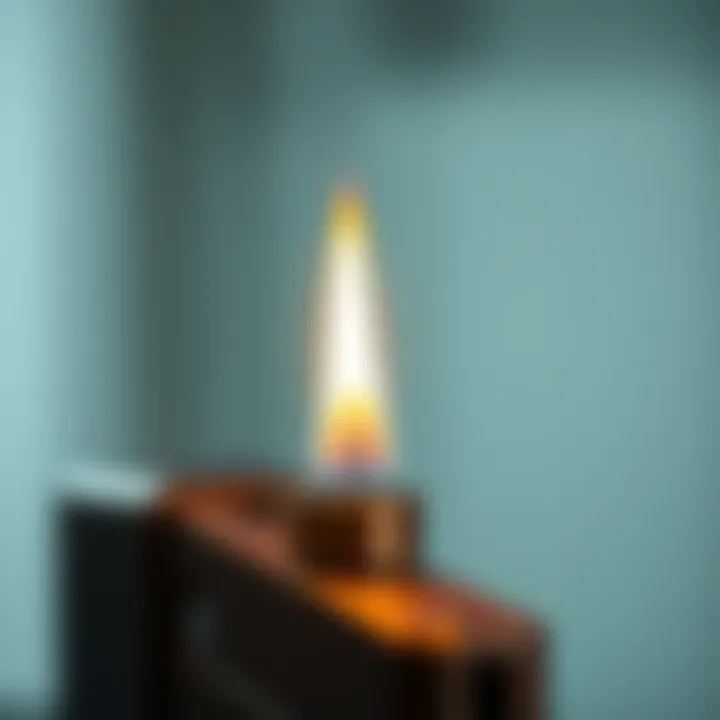
Intro
In the realm of jewelry making, the small jeweler's torch serves as a linchpin of creativity and precision. Understanding its various aspects is pivotal for both enthusiasts and seasoned experts alike. In this guide, we will peel back the layers on this essential tool, shedding light on its types, functions, and best practices for safety and maintenance.
A small jeweler's torch is not just a mere implement; it's a bridge between raw materials and exquisite pieces of art. By exploring its multifaceted nature, you can elevate your craft to new heights. Whether you’re repairing a treasured family heirloom or creating a striking new piece from scratch, having an in-depth comprehension of your torch can make all the difference.
This comprehensive guide aims to provide a detailed exploration into the world of the small jeweler's torch.
Types of Small Jeweler's Torch
Overview of Torch Types
Jeweler’s torches can be categorized broadly into a few distinct types, each suiting different needs and preferences. Understanding these types can help you choose the right one for your specific requirements.
- Butane Torches: These are portable, user-friendly, and ideal for small tasks. Typically, they are lightweight and can easily fit in a toolbox or drawer.
- Propane-Oxygen Torches: This combination offers a hotter flame, making it suitable for larger and more complex projects. Propane is often used in conjunction with oxygen for a more intense heat.
- Acetylene-Oxygen Torches: Known for their high temperatures, these torches are the heavyweights in the jeweler's toolbox. They’re excellent for soldering and melting metal, catering to advanced techniques.
In-Depth Look at Each Type
- Butane Torches: Simplistic and effective, they are perfect for beginners. Butane torches are easily adjustable, have a good flame control, and simplify tasks like soldering in simple jewelry repair or crafting tasks. One major advantage is that they do not require external oxygen sources, making them great for smaller workshops or home setups.
- Propane-Oxygen Torches: With an ability to reach higher temperatures than butane torches, they are ideal for more demanding projects. Many jewelers prefer this type for its versatility in heating larger workpieces or making intricate designs that require precision guidance. The additional oxygen support elevates the efficiency of the flame.
- Acetylene-Oxygen Torches: For jewelers aiming at intricate craftsmanship, these torches can create a flame temperature of over 3,500 degrees Fahrenheit. They are the go-to tool for professionals dealing with complex jewelry designs, metal art, or thorough repairs. However, they require a more significant setup and safety measures due to the high intensity of the flame and the gas involved.
Remember: Choosing the right torch is crucial. Match your torch type with the projects you aim to execute, and you will streamline your work while ensuring safety.
Exploring the tools available means understanding their strengths and weaknesses. Each torch type has significant merits that appeal to different levels of artistry in jewel crafting.
Understanding which torch fits your needs begins the journey of mastering jewelry creation. Let’s move forward into the intricacies and functionalities that each torch type offers as we continue to develop your skills and knowledge, incorporating up-to-date safety tips and maintenance insights tailored for jewelers.
Prolusion to Small Jeweler's Torch
The small jeweler's torch stands as a pivotal instrument in the craft of jewelry making and repair. It acts as a bridge between raw materials and the exquisite pieces often seen in showcases. For enthusiasts, both budding and seasoned, understanding the small jeweler's torch elevates not only their skills but also their appreciation of the intricate art of jewelry.
In this article, we will delve into several critical aspects of the jeweler's torch, equipping readers with the knowledge needed to harness its potential effectively. By exploring its definition, historical background, types, safety measures, and much more, we look forward to enhancing your understanding of this essential tool.
Definition and Purpose
A small jeweler's torch primarily serves the purpose of heating materials to temperatures suitable for various methods such as soldering, welding, and bending metals. Without this crucial device, the craft would face significant limitations, as some techniques rely heavily on pinpoint heating — something that larger torches or everyday flame sources cannot easily provide.
Moreover, these torches are designed for precision. When creating intricate designs or repairing delicate pieces, jewelers need control over not just the temperature, but the type of flame produced. Different applications demand different flame types – from a soft, gentle flame beneficial for delicate soldering to hotter flames necessary for stronger bonds. The mere act of regulating flame becomes an art in itself, demonstrating the mastery a jeweler can achieve with adequate knowledge.
Historical Evolution of Jewelers' Torches
The story of jeweler's torches stretches back centuries, catalyzed by the evolving nature of materials and techniques. Early jeweler's torches were primitive, often relying on charcoal fires or simple blowpipes, which posed limitations in terms of accuracy and control.
As time went on, innovations introduced more refined tools. In the 19th century, the advent of gas lamps began to shift the landscape for jewelers significantly. The shift allowed for better temperature control and opened up new horizons in the crafting of intricate pieces.
In the modern era, the development of portable, butane and propane torches offered flexibility and ease of use that was previously unimaginable. These advancements enabled jewelers to operate in various environments, from home workshops to on-site repairs at fairs or markets. These changes not only influenced the craftsmanship but also made it more accessible to hobbyists, facilitating a broader appreciation for jewelry making as an art form.
As we move further into this guide, it will become clear just how integral the small jeweler's torch is for anyone serious about the jewelry trade.
Types of Small Jeweler's Torches
When it comes to jewelry making, understanding the various types of small jeweler's torches is paramount. Each type serves distinct purposes and presents its own set of advantages and challenges. A jeweler's torch is not just a tool; it embodies the very essence of craftsmanship, allowing artisans to create intricate designs and perform repairs with utmost precision. Choosing the right torch can influence not only the outcome of a project but also the efficiency and safety of the entire process.
Butane Torches
Butane torches are often the go-to choice for many jewelers, especially those who are just beginning their journey into the world of jewelry making. These torches are generally compact, portable and easy to use, making them particularly well-suited for smaller projects or on-the-go work. There's a certain straightforwardness to using a butane torch; fill it up with butane, ignite, and you are in business.
Butane torches provide a clean burning flame, which is a fabulous advantage when working with delicate materials like the thin wires or soft stones. However, one must note that they might not generate enough heat for larger pieces or thicker materials. Jewelers must be mindful of the limitations, particularly when it comes to soldering processes that require more robust heat sources.
Some common brands of butane torches include the Blazer GT8000 and the Zeno Mini Torch. It might be worth checking out user reviews to find the one that best suits specific needs, especially for those trying to find a balance between affordability and performance.
Propane Torches
Propane torches offer a step up in heat intensity compared to butane. They are suitable for heavier-duty projects where a more intense flame is required. Many professional jewelers prefer propane torches due to their ability to provide higher temperatures, making them ideal for soldering larger pieces of metal or dealing with more challenging materials.
The setup for a propane torch can be a bit more involved, requiring safe handling of the propane tanks. Jewelers using these torches must ensure their workspace is well-ventilated and equipped with proper safety measures. Despite these considerations, the versatility and power of propane torches make them a reliable choice for many artisans.
Torches like the Harris 25B and the Blazer Pro are popular in the jewelry community, both known for their reliability and efficiency. A bit of research would go a long way in ensuring that the selected propane torch meets the specific needs of projects.
Alternative Fuel Sources
In addition to the conventional butane and propane options, there exists a realm of alternative fuel sources that can be utilized. These include natural gas and even electric torches. Electric torches, while less common, offer a level of precision and control that can be appealing for particular tasks where flame adjustment is crucial.
Natural gas is often accessed in workshop settings where plumbed gas sources are available, providing a constant supply and eliminating the need to constantly refill canisters. However, one must take great care to ensure proper installation and safety precautions to mitigate any hazards associated with gas sources.
Beyond these, innovations are continuously emerging, including eco-friendly options that prioritize sustainability while maintaining efficiency. This evolving landscape emphasizes the importance of staying updated on new technologies and methodologies in torch options.
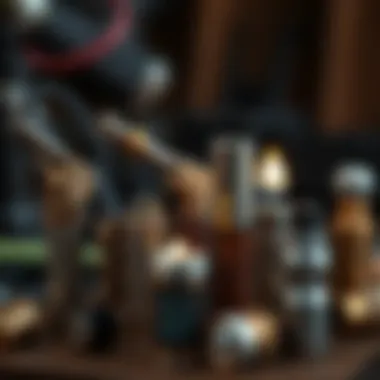
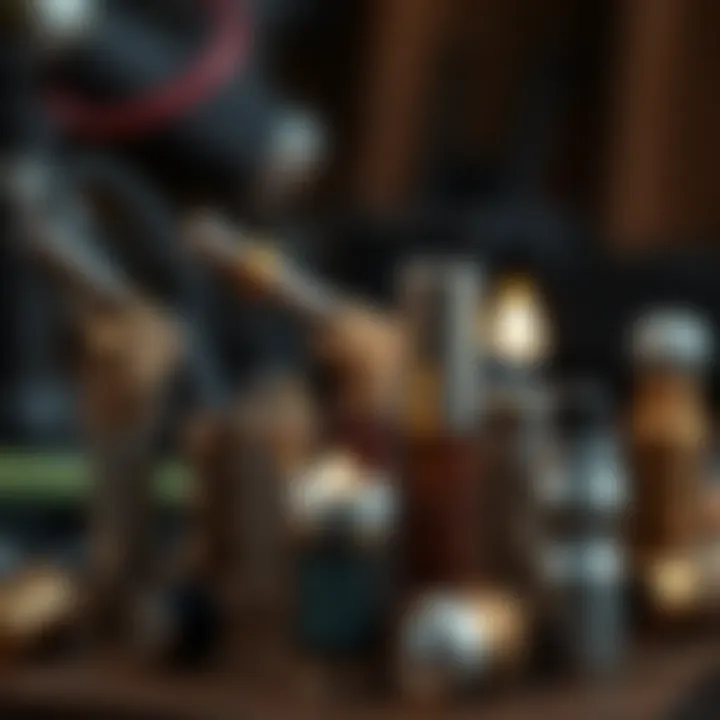
The right choice of torch can significantly influence both the safety and quality of your jewelry work; invest time in understanding your options.
By grasping the basics of these different types of small jeweler's torches, artisans can not only enhance their craft but also ensure that they are working in the safest and most effective manner possible.
Understanding the Components of a Jeweler's Torch
In any intricate art form, the tools one uses significantly shape the outcome. This axiom rings especially true for jewelers, where every flame can make or break a piece of artistry. Understanding the components of a jeweler's torch is a foundational aspect that can empower jewelers to harness their tool’s full potential. Knowing the parts and their functions not only increases skill but also enhances safety and efficiency in flame work.
Torch Body and Design
The torch body is where it all begins. It’s essentially the structure that holds everything together. When selecting a jeweler’s torch, design plays a crucial role. Many times, the ergonomics of the torch can influence how comfortable the user feels while working for extended periods. For instance, a torch with a well-balanced grip can reduce fatigue and allow for more precise control.
Material choice is also an important consideration. Metal vs. plastic? A metal body often withstands changes in temperature better than plastic. A good design also minimizes the risk of accidents; parts should fit securely, and controls should be intuitive.
"A comfortable torch can be the unsung hero in achieving a flawless piece of jewelry."
Fuel Sources and Their Storage
Fuel choice is another vital component of a jeweler’s torch. Butane and propane are the two most common fuels, each having its own advantages and shortcomings. Butane, for example, is often favored for its higher heat output, which can be particularly useful during intricate soldering tasks. Conversely, propane is generally more affordable and offers a longer burn time, which is perfect for larger projects that require sustained heat.
Storing these fuels safely is equally crucial. Always keep fuel canisters in a cool, dry place away from direct sunlight. A locked cabinet or a designated toolbox is ideal to prevent any accidents. Mismanagement of fuel can lead to leaks or even explosions, so handling with care is of utmost importance. Here’s a simple checklist for safe storage:
- Store in a cool, ventilated area.
- Keep out of reach of children and pets.
- Use proper containers designed for fuel storage.
Nozzles and Flame Types
When it comes to flame, nozzles can significantly alter performance and precision. Different nozzles produce varying flame types—whether a soft bushy flame for gentle tasks or a hot, pinpoint flame for precise soldering. The nozzle shape takes center stage when determining the flame’s characteristics.
Moreover, adjusting flame size is another critical feature. A jeweler who understands what each type of flame can achieve holds the key to creating beautifully crafted pieces. For example:
- A neutral flame is ideal for most soldering tasks, as it heats evenly.
- An oxidizing flame can be useful for metals that need a bit more heat.
- A reducing flame is best when working with materials that require deoxidizing.
Understanding these nuances not only elevates a jeweler’s craft but can also mitigate problems like overheating or improper melting of materials.
How to Use a Small Jeweler's Torch
Using a small jeweler's torch is not just about igniting a flame; it's about mastering a valuable skill that can enhance the beauty and durability of your creations. Whether you are a budding jewler or a seasoned artisan, knowing how to properly use a torch is pivotal. The torch serves various purposes in jewelry making, from soldering intricate pieces to efficiently welding components together. A clear understanding of how to operate this tool makes your work more efficient and elevates your craftsmanship.
Setting Up the Work Area
Your work area is your sanctuary. A well-organized setup can make or break your projects. First, choose a flat, stable surface that is resistant to heat. A metal surface, such as a steel table or a ceramic tile, works well—avoid anything flammable like wood or plastic.
Ensure you have good ventilation to disperse any harmful fumes. A fan or a window open can make all the difference. Consider using a fireproof mat underneath your work to contain any mishaps. Also, keep your tools arranged conveniently within arm's reach. A organized space isn’t just safer; it lets your mind focus on the task at hand.
Tip: Always keep a bucket of water or a fire extinguisher nearby when using a torch to ensure you can react swiftly should an emergency arise.
Ignition and Flame Control
Starting your torch involves striking a perfect balance between safety and functionality. Each torch might have different ignition methods—some have an automatic igniter while others might need a lighter or striker. Always refer to the manufacturer’s guidelines for specific instructions.
Once ignited, adjusting the flame is crucial. Typically, there are two controls: one for the gas flow and another for the airflow, which mixes with the gas. A brighter, hotter flame yields precision for fine work, whereas a larger, softer flame is better for broader soldering or fusings.
Practice manipulating the flame to achieve the ideal size and characteristic for your task. You want a controllable flame that doesn't flare or dance around, as that can lead to uneven heating and potential damage to your work.
Techniques for Different Jewelry Projects
The use of a jeweler's torch varies significantly depending on the project at hand. Each technique requires a different approach to flame control and material handling.
- Soldering: Typically involves joining two metal pieces using solder and is best conducted with a small, focused flame to prevent overheating adjacent areas.
- Fusing: This process requires the torch to actually melt the metal together without the need for additional solder. A slightly hotter flame that is evenly distributed can help achieve seamless results.
- Welding: For welding operations, you may want to use a larger flame to melt metal quickly. This helps in building up layers of material in a controlled manner.
Experiment with each of these techniques to understand how heat affects different materials, and adjust your approach accordingly. Each project is a learning opportunity, revealing nuances in your technique and improving your understanding of the torch’s capabilities.
Safety Practices When Using a Jeweler's Torch
Using a jeweler's torch is as much an art as it is a science, but it's vital to understand that safety practices are the bedrock of effective jewelry making. This section addresses various safety aspects that should be at the forefront of any jeweling endeavor. Understanding how to protect yourself can mean the difference between enjoying your craft and facing unfortunate incidents.
Personal Protective Equipment
When working with a jeweler’s torch, your first line of defense is personal protective equipment (PPE). This gear is essential to shield you from potential hazards such as burns, accidents, or exposure to harmful fumes. Here are some crucial items you should consider:
- Safety Goggles: Protect your eyes from sparks and harmful light emitted during the flame process. Ideally, look for goggles that meet ANSI Z87.1 standards.
- Heat-Resistant Gloves: Choose gloves that can withstand high temperatures. Leather or Kevlar options are popular among professionals for their durability and protection.
- Apron: A flame-resistant apron helps guard against hot debris and splashes of molten metal. An apron made of heavy cotton or leather is advisable.
- Proper Footwear: Closed-toe shoes, preferably steel-toed, protect your feet from falling objects or burning material.
In addition, it's wise to tie back long hair and avoid loose clothing to minimize fire risks.
Workspace Safety Measures
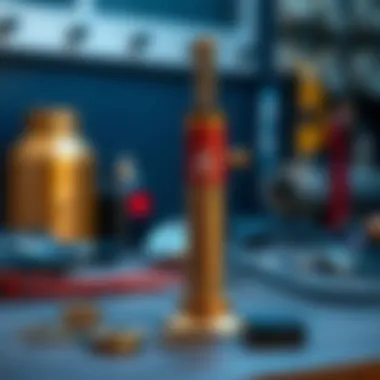
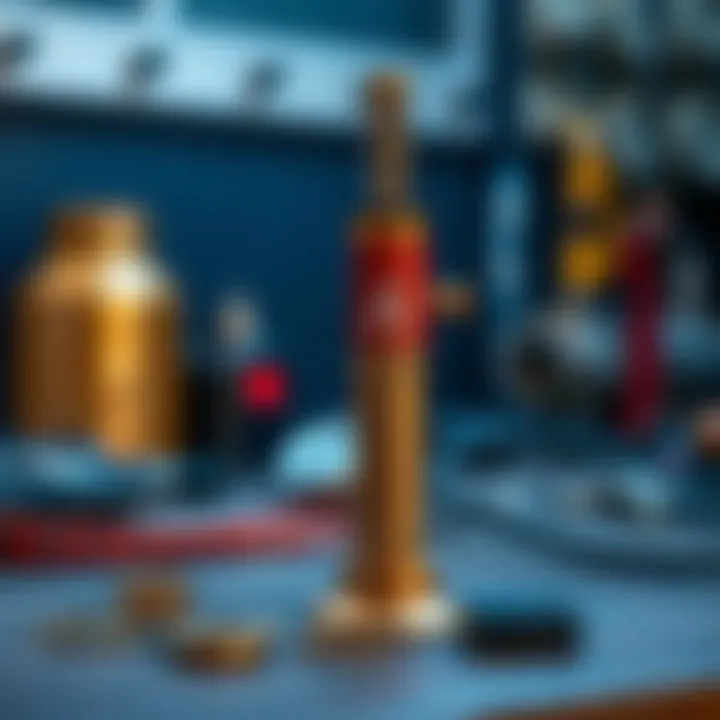
Creating a safe workspace is just as crucial as donning personal protective equipment. Your working environment should be carefully structured to enhance safety while you’re focused on your project. Consider the following measures:
- Ventilation: Working with torches can produce noxious fumes. Ensuring adequate ventilation minimizes harmful exposure. An exhaust fan or opening windows can greatly improve air quality.
- Fire Extinguisher: Keep a fire extinguisher within reach, ideally rated for all types of fires (Class ABC). This precaution ensures you're prepared for unexpected flare-ups.
- Clear Work Area: Maintain an organized and uncluttered workspace. Ensure that flammable materials, such as papers and fabric, are removed from the vicinity of your torch.
- Stable Surface: Use a sturdy, non-flammable table for your crafting. Avoid makeshift setups that could lead to accidents.
Emergency Procedures
Despite all preventive measures, accidents can happen. A well-thought-out plan can save you from panic and reduce harm in the event of an emergency. Below are essential procedures to follow:
- Know Your Exits: Familiarize yourself with emergency exits in your workspace and always have a clear path to get out safely.
- Contact Numbers: Keep essential contact information readily accessible, including poison control and local emergency services. This will allow you to act quickly if any hazardous situation arises.
- First Aid Kit: Equip your workspace with a basic first aid kit. Be aware of its contents and familiarize yourself with how to use them, particularly burn treatment supplies.
"Preparedness is the key to safety; having a plan makes you ready before the situation even arises."
- Practice Drills: Regularly review and practice evacuation procedures with anyone who may use the workspace. This ensures that everyone is familiar with emergency protocols and knows how to respond.
By implementing these safety practices when using a jeweler’s torch, you enhance not just your own security but also the overall integrity of your craft. A responsible approach to safety will allow you to focus more on your techniques and creativity without the cloud of worry hanging over you.
Key Applications of the Small Jeweler's Torch
Understanding the various applications of a small jeweler's torch in the realm of jewelry making is crucial for both novices and experts alike. This tool is not merely a source of fire; it’s a versatile instrument that enhances craftsmanship, enabling artists to mold, join, and create with a finesse that cold connections simply cannot achieve. Jewelers employ these torches for various tasks—each demanding precision and skill. The effectiveness of a jeweler's torch often relies on the technique employed and the specific type of material one is working with, making knowledge of its applications essential for achieving optimal results in jewelry projects.
Soldering Techniques for Jewelry
Soldering is perhaps the most prominent application of the small jeweler's torch. The process involves joining two metal pieces together using a filler material that melts and flows into the joint. Several techniques of soldering exist, including:
- Hard Soldering: Utilizes higher-temperature solder to join metals together. This method is robust and ideal for parts that will undergo stress.
- Soft Soldering: Operates at a lower temperature, using softer filler materials. This approach is often seen in assembling components that shouldn't bear significant force.
- Tack Soldering: A method for temporarily holding pieces in place during assembly. Jewelers can be precise about positioning before performing a final, stronger soldering technique.
Each technique serves a specific purpose, allowing jewelers to manipulate connections with care. Attention must be given to metal compatibility, as different metals require varying solder types and temperatures. A good grip extends beyond the heat; managing materials safely ensures quality production.
Fusing and Welding Processes
Fusing and welding represent more specialized applications of the jeweler’s torch, particularly in delicate work. Fusing is the process of melting the edges of two metal pieces until they meld without the use of any filler material. This method is ideal for achieving seamless joints—it’s particularly favorable for precious metals.
On the other hand, welding goes a step further. It involves melting the base metals and allowing them to coalesce into a single piece. Here are some aspects to consider:
- Material Selection: Not all metals can be welded using the torch method. Understanding the metals' properties, such as melting points and heat conductivity, is vital.
- Preparation: Properly prepping the surfaces to be joined—a clean and smooth surface leads to a better bond—ensures a minimal risk of impurities affecting the weld.
These processes elevate the art of jewelry-making, allowing for designs that are intricate and solid. Melding metals in such a way can bring forth beautiful designs that would likely break apart with traditional assembly methods.
Anaerobic vs. Aerobic Techniques
In the context of using a jeweler's torch, distinguishing between anaerobic and aerobic techniques is integral for those looking to get the most out of their soldering and joining methods.
- Anaerobic Techniques: These involve processes conducted in an environment void of oxygen. When using a torch, this typically means working with a controlled flame in a specific oxygen-rich or oxygen-poor environment to avoid oxidation and achieve better results when soldering or fusing metals.
- Aerobic Techniques: This methodology comprises working with a recommended oxygen and fuel mix to allow for complete combustion. An aerobic flame is better for heating and can yield a finer point for delicate tasks but comes with the risk of effectively altering surface colors or properties of certain metals.
Each technique's application will largely depend on the desired outcome, metal types involved, and specific project requirements. Jewelers should familiarize themselves with both sides to choose freely according to the demands of their art.
Ultimately, the key applications of the small jeweler's torch provide an expansive toolkit for anyone serious about jewelry-making. Gaining proficiency in these methods not only fosters skill but also empowers creativity, allowing for innovative designs while overcoming various challenges in the medium.
For a deep dive into more soldering techniques and materials, you may explore the Craft Jewelry Community or refer to resources from GIA.
Challenges with Small Jeweler's Torches
Understanding the obstacles faced while using small jeweler's torches is crucial for any enthusiast or professional. Even the best tools, when misused or misunderstood, can lead to frustrating experiences that hinder creativity. By addressing common challenges, jewelers can avoid mishaps, ensuring smoother workflows and better results in their crafting endeavors. Whether you’re just starting out or looking to fine-tune your techniques, recognizing these hurdles will enhance your skills significantly.
Common User Errors
The road to mastering a small jeweler's torch can be bumped with a few common mistakes made by users, especially beginners. Here are some frequent errors:
- Improper Flame Adjustment: Many users struggle with getting the flame just right. A flame that is too large can scorch delicate materials, while a flame too small may not achieve the heat needed for proper soldering or fusing.
- Ignition Challenges: Sometimes, the torch doesn’t ignite on the first try, leading to frustration. Failing to follow ignition protocols can be a typical pitfall, such as neglecting to check for sufficient fuel or improperly setting the lever.
- Neglecting Safety Protocols: It's easy to get comfortable, but sometimes jewelers overlook basic safety measures. Forgetting the appropriate protective gear or failing to maintain clear workspace can lead to accidents.
This list could go on, but these issues highlight how crucial it is to pay attention to details. Regular practice and attentiveness are key to overcoming these user errors.
Material Compatibility Issues
Compatibility between materials and the torch's heat characteristics is a discussion jewelers can’t ignore. When working with different metals or stones, it’s essential to know how each reacts to high temperatures. Here are some points to consider:
- Metal Types: Various metals have different melting points. Gold, for instance, typically melts around 1,064°C while silver melts at about 961°C. Using a torch with too high heat on silver can lead to undesirable results, such as burning or warping.
- Stone Sensitivity: Many gemstones can be sensitive to heat. Soldering nearby stones without proper protection might leave them cracked or discolored. Opals, for instance, are particularly vulnerable to heat, potentially damaging the internal structure if exposed to flames directly.
- Flux and Other Materials: The choice of flux or solder compatibility can also make or break the project. An inappropriate flux may lead to oxidation or ineffective bonding, causing jewelry pieces to fall apart.
By being mindful of these material compatibility issues, jewelers can save themselves considerable time and effort.
Troubleshooting Flame Problems
The flame of a jeweler's torch is its lifeblood, and any issues with it can ripple through the entire jewelry-making process. Here’s how one might troubleshoot common flame-related problems:
- Flame Quality: If you notice a yellow flame, it might indicate incomplete combustion. Adjust the fuel-to-air ratio until you achieve a clean, blue flame – ideal for most applications.
- Flame Extinguishing: A flame that constantly goes out can be caused by a block in the fuel line or a faulty nozzle. Inspect and clean the parts before attempting to ignite again.
- Inconsistency: If the flame keeps changing its size during use, check for air leaks or issues with the fuel canister. Sometimes, a simple replacement of the canister can do wonders.
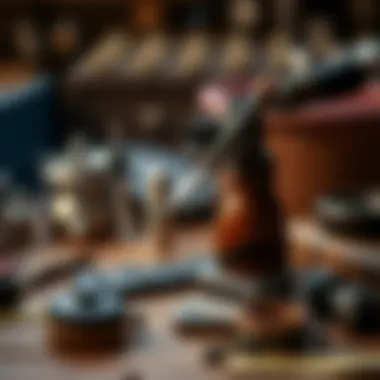
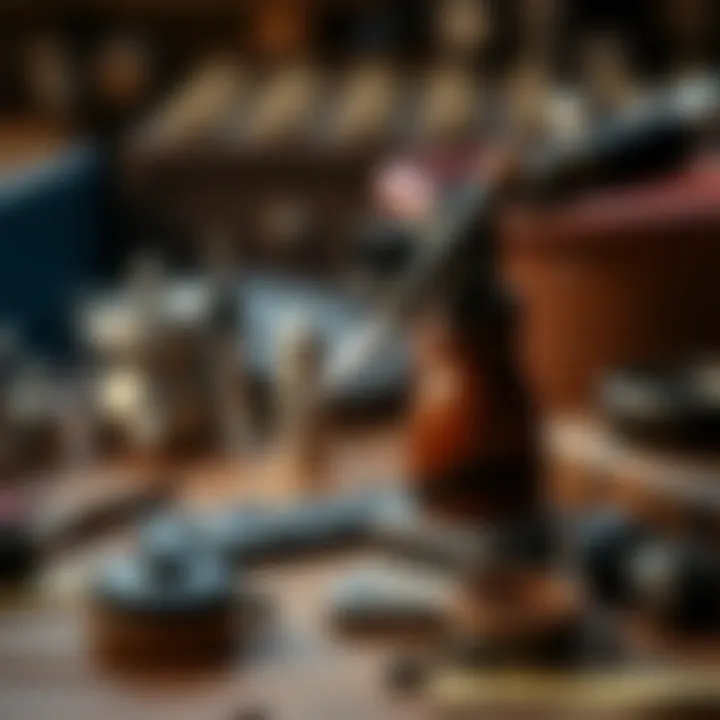
These troubleshooting tips can help save time and prevent frustration during intense moments of creativity.
"Paying attention to the problems is the first step in crafting a seamless jewelry experience. A knowledgeable jeweler is often one step ahead of potential mishaps."
By being aware of these challenges and actively troubleshooting them, both novice and experienced jewelers can elevate their work, transforming difficulties into opportunities.
For more insights into handling common issues with jeweler's torches, you might find sites like reddit.com and britannica.com helpful for community discussions and expert articles.
Maintenance and Care for Your Jeweler's Torch
Caring for your jeweler's torch is akin to keeping the gears of a well-oiled machine running smoothly. Neglecting maintenance can lead to inefficient performance, frustrating mishaps, or even dangerous accidents. In the world of jewelry making, where precision is king, keeping your tools in top condition is crucial. Routine care not only extends the lifespan of your torch but also enhances your work's quality, providing you with cleaner, more reliable flames for all your projects.
Routine Cleaning Procedures
When it comes to your small jeweler's torch, cleanliness isn’t just about aesthetics. Dirt and soot can accumulate, affecting the torch's performance. Each type of torch, whether butane or propane, has its own set of cleaning requirements. For instance, a common practice involves using a soft cloth or brush to wipe down the exterior, removing any debris after each use.
In addition to external cleaning, it's wise to inspect the nozzle for blockages periodically. If you notice uneven flame or sputtering, it may be time to give your nozzle a thorough clean. For a deeper cleanse, you can often soak components in a mild solution of soap and water, but avoid submerging any electrical parts to prevent damage.
- Tip: Use compressed air to blow out the nozzle for stubborn debris.
- Remember: Always let components dry completely before reassembling.
Storing Fuel Safely
The safety of your fuel storage is paramount. Whether you use butane or propane, understanding how to store these materials safely can prevent unexpected flare-ups or even explosions. Ideally, fuel canisters should be kept in a cool, well-ventilated area, away from direct sunlight. Placing them indoors might feel tempting for convenience, but this can promote danger during heat waves.
Moreover, ensuring that the canisters are upright and securely fastened is essential. They should not be stored near heat sources or flammable materials, as this could lead to disastrous consequences. Keeping a fire extinguisher nearby can also be a wise precaution.
Important Note: Always check for signs of leaks on fuel canisters and never use damaged ones.
When to Replace Components
Knowing when to replace parts of your jeweler's torch can save you both time and frustration in the long run. Common indicators that a component needs replacement include inconsistent flame, excessive soot build-up, or physical damage such as cracks or dents. For instance, if the flame constantly flickers or fails to stay lit, this may indicate that the nozzle or hose has become compromised.
Before making any replacements, consult the manufacturer’s manual for specific guidelines about your model. Having spare components on hand can be incredibly helpful, allowing you to swap out damaged parts quickly without cutting into your crafting time.
- Wear & Tear Signs to Watch For:
- Discoloration or charring around the flame area
- Hissing sounds that aren't typical during operation
- Difficulty in controlling the flame size
Maintaining and caring for your small jeweler's torch doesn't have to be a cumbersome task. With a little diligence and awareness, you can ensure that your torch remains a reliable companion in your quests for beautiful jewelry pieces.
Future Trends in Jewelry Torch Technology
The landscape of jewelry making is continually evolving, with technology paving the way for numerous innovations. This section discusses the future trends in jewelry torch technology, which is pertinent due to its implications for efficiency, safety, and craftsmanship within the industry. As jewelers strive for perfection and sustainability in their creations, understanding these trends becomes crucial for anyone engaged in the craft.
Innovations in Fuel Efficiency
One significant advancement on the horizon is the quest for improved fuel efficiency in jewelry torches. Traditionally, jewelers relied on standard butane or propane torches that sometimes consumed more fuel than necessary, particularly during longer working sessions. Innovations are starting to surface that focus on optimizing these fuel sources. For example, the integration of advanced combustion technologies that reduce gas consumption while maintaining a high-quality flame.
Advancements in fuel efficiency not only cut costs but also lessen the environmental impact, addressing the growing desire for sustainable jewelry practices.
Additionally, manufacturers are exploring hybrid fuel systems which combine traditional fuels with alternatives, reducing dependency on petroleum-based options. These cutting-edge designs may significantly enhance the jeweler's experience, providing longer burn times with less frequent refueling.
Developing Safer Torch Designs
Safety has always been paramount in jewelry making, especially when using torches. Recent trends indicate a significant focus on developing safer torch designs. One of the emerging concepts is incorporating electronic ignition systems that minimize the risk of unintentional ignition, a common occurrence with manual lighters.
Modern designs are incorporating more robust safety features, including automatic shut-off valves that activate when certain conditions are met, such as a tilt or drop.
The ergonomics of torches are also being reimagined. Comfortable handles and improved grip designs allow jewelers to work longer without discomfort, reducing accidents that stem from fatigue. As the industry adopts these safer designs, expect to see a reduction in workplace incidents, creating a more secure environment for artisans.
Impact of Technology on Jewelry Craftsmanship
The relationship between technology and jewelry craftsmanship cannot be overstated. With the advent of more sophisticated tools, the precision with which a jeweler can work is reaching new heights. Smart torches that interface with digital devices for temperature control and flame adjustment are entering the market, enabling jewelers to achieve consistent results across various projects.
Such innovations not only enhance the quality of craftsmanship but also broaden the scope of what is possible in jewelry design. Increased precision allows for intricate patterns and details that were once deemed too challenging or impossible. Jewelers can explore new horizons in creativity with these technological advancements.
As the craft continues to embrace these changing tides, it’s vital for jewelers—both upcoming and experienced—to keep a pulse on these future trends. Employing the latest technologies can significantly elevate both their craft and the value of their creations.
End
In the realm of jewelry making, the small jeweler's torch stands as an unparalleled tool, necessary for precision and creativity. Whether you're soldering two pieces of metal together or crafting delicate designs, understanding how to harness this equipment can significantly influence your work. The highlighted sections throughout this article shed light on various aspects of the jeweler's torch, providing clarity on its types, components, and the crucial safety measures required during its operation. In light of this, it is essential for jewelers to grasp the practical applications of this tool and the intricacies involved in its use.
Recapping Key Points
One cannot overstate the advantages tied to mastering your small jeweler's torch. Here are some fundamental takeaways:
- Types of Torches: Familiarity with the various kinds—be it butane or propane—equips jewelers to choose the right tool for each project.
- Safety First: Implementing appropriate safety practices in your workspace helps prevent accidents and ensures a smoother workflow.
- Maintenance Matters: Regular upkeep not only prolongs the life of the torch but also enhances performance, leading to better outcomes in your jewelry pieces.
These key points manifest the foundation upon which a jeweler can build their skills. They highlight how integral this tool is in producing quality work and its relevance in achieving artistic visions.
Encouraging Continued Learning
The journey in jewelry making and the exploration of the small jeweler's torch doesn't conclude here. Engaging with ongoing education and hands-on practice is vital to refine one’s craft. Join jewelry-making forums on platforms like Reddit or interact with local craft communities. Participate in workshops or online classes focusing on torch techniques to gain new perspectives.
Additionally, consider reading more specialized resources such as Britannica or conducting research via academic platforms. Such pursuits can deepen your understanding and cultivate an innovative spirit, ultimately leading to enhancements in your artistic endeavors.