Understanding Rock Cutting and Polishing Machines
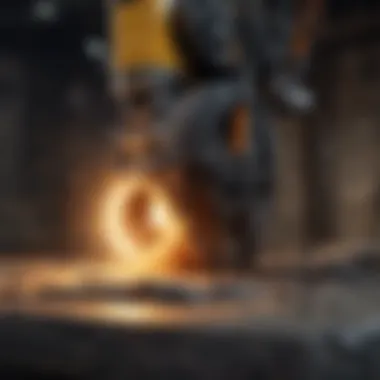
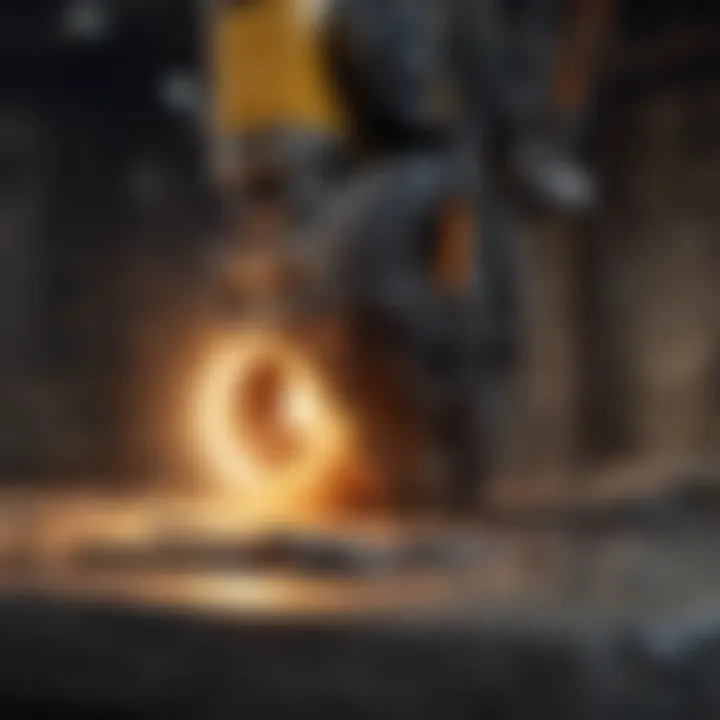
Intro
Rock cutting and polishing machines are significant tools in the realm of geology and mineral collection. These machines serve not only as vital equipment for professionals but also as hobbyist aids in transforming raw specimens into beautifully finished collectibles. Understanding their functionality and applications is crucial for anyone interested in enhancing their rock and mineral collections.
This section provides an overview of the types of collectibles in the field, essential tools for identifying rocks, and the techniques employed for their classification. By examining these elements, we aim to enrich the appreciation for these natural specimens and the processes that refine them.
Types of Collectibles
Overview of Collectible Categories
When considering rock and mineral collections, varied categories come to the forefront. Collectibles can range from common specimens to rare and unique finds. They may include:
- Minerals: Crystals and their formations, showcasing unique colors and structures.
- Rocks: Varied rock types, such as igneous, sedimentary, and metamorphic.
- Fossils: Remnants of ancient organisms, often prized for their historical significance.
- Gemstones: Treasures like garnet, quartz, and diamonds, valued for their beauty and rarity.
Understanding these categories helps collectors focus their efforts and tailor their collection strategies according to individual interests and market demand.
In-Depth Look at Each Category
- Minerals: Each mineral possesses distinct characteristics including hardness, luster, and cleavage. Familiarity with common minerals such as quartz and feldspar enhances collecting abilities.
- Rocks: Knowledge of rock formation processes lets collectors recognize different rock types. For example, granite presents as an igneous rock, while limestone is sedimentary.
- Fossils: Fossil collecting is a unique niche, as specimens range from imprints to full skeletons. Familiarity with paleo-environment helps in understanding the geological context.
- Gemstones: The gemstone category often requires deeper knowledge of clarity, cut, and carat weight for proper valuation. Recognizing factors that affect both appearance and worth can guide purchasing decisions.
"A meticulous eye for detail transforms casual collecting into a more fulfilled experience."
Identification Techniques
Essential Tools for Collectors
Proper identification of rocks and minerals is essential for any collector. Using the right tools can make this process much easier:
- Hand Lens: A simple yet effective device for magnifying details of specimens.
- Mohs Hardness Kit: Helps determine the hardness of minerals, crucial for identification.
- Field Guide: Reference books or apps that provide information about local geology and mineralogy.
- pH Strips: Used to test the acidity or alkalinity of rocks, aiding in identifying certain mineral types.
Identification Methods for Rocks and Minerals
Various methods can help in identifying minerals and rocks. Some common techniques include:
- Visual Inspection: Noting color, luster, and form is the first step in identification.
- Scratch Test: This involves scratching the specimen with a known material to gauge its hardness.
- Reaction to Acid: Some minerals react to acids; observing this can assist in identification.
By employing these identification techniques, collectors can deepen their understanding of their specimens. This knowledge not only enhances the collecting experience but also fosters a greater appreciation for the natural world.
Preface to Rock Cutting and Polishing
Rock cutting and polishing machines are essential tools in geology and mineralogy. They play a crucial role in transforming raw rock specimens into polished, visually appealing pieces of art, suitable for display or further scientific examination. The insights into these machines go beyond just their mechanics; they encompass historical developments, technological advancements, and practical applications. By unveiling the intricacies of these machines, we can appreciate their significance in various fields such as education, industry, and hobbyist activities.
Definition and Purpose
Rock cutting and polishing machines are devices designed specifically to shape and refine rock materials. Their main purpose is to cut raw rock into manageable sizes and polish the surfaces to enhance their aesthetic qualities. The process involves several stages, including cutting, grinding, and polishing, which collectively aim to reveal the natural beauty of the rock.
Benefits of using these machines include:
- Improved efficiency in processing rocks
- High precision in cutting, allowing for intricate designs
- Enhanced surface finish, making specimens more appealing
- The ability to handle a variety of rock types, catering to diverse needs
These machines are pivotal for collectors who aim for quality specimens and for professionals who require precise geological samples.
Historical Context
The evolution of rock cutting and polishing machines corresponds with the advancements in technology and the increasing demand for rock materials. Early methods of shaping stones involved hand tools and simple techniques, which were both labor-intensive and time-consuming. With the advent of the industrial revolution, mechanized equipment began to emerge, significantly improving the efficiency and precision of rock processing.
In the late 19th century, devices like the saw were commonly used, but only for basic cuts. As technology progressed into the 20th century, the introduction of diamond blades and automated machines marked a turning point in the field. Today, modern machines incorporate advanced features like computer numerical control (CNC), allowing for exceptional precision and complex designs.
The significance of these developments is evident in the way they contribute to the appreciation of geology and its aesthetics, making rock cutting and polishing machines indispensable in both academic and personal collections.
Types of Rock Cutting Machines
Understanding the various types of rock cutting machines is crucial for anyone interested in rock processing. Each machine type serves specific functions and offers unique advantages, impacting how tasks are carried out in both home and industrial settings. Knowing these distinctions enhances decision-making and efficiency.
Diamond Wire Saw
The diamond wire saw is a popular choice for cutting hard stones like granite and marble. It utilizes a wire embedded with diamond particles, offering precise and clean cuts. The precision reduces waste material, promoting a more efficient use of the rock. This method is less aggressive than traditional saws, which can lead to fewer fractures in the material being cut.
In terms of speed, diamond wire saws provide a faster cutting rate compared to other methods. The use of water as a coolant during cutting minimizes dust, creating a healthier working environment. However, the initial investment can be significant, which is an important consideration for hobbyists and smaller operations.
Bridge Saw
Bridge saws are another staple in the rock cutting industry. They feature a fixed frame that supports a diamond blade, allowing for remarkable stability during cutting. This stability is essential for creating large slabs, commonly seen in countertops and tiles. The bridge saw can make vertical, horizontal, and angled cuts, offering versatility in applications.
Moreover, many bridge saws come with automated features, enhancing efficiency and reducing manual labor. Such machines can be programmed to cut complex shapes and designs, which is beneficial for both industrial applications and unique custom projects. The requirement for a dedicated workspace and power source should be considered when opting for this type of machine.
Tile Cutter
Tile cutters are designed for smaller scale projects and are especially useful for cutting ceramics and softer stone tiles. These tools are generally more affordable and compact than their larger counterparts. Many tile cutters use either a rotary blade or a manual scoring mechanism. The simplicity of these machines makes them accessible for hobbyists, especially for those just starting with rock processing.
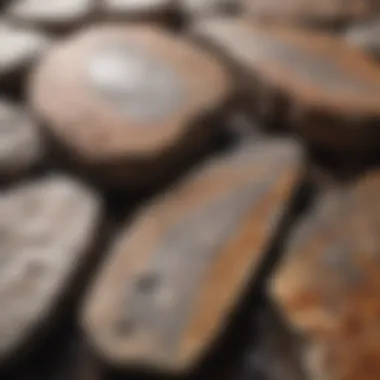
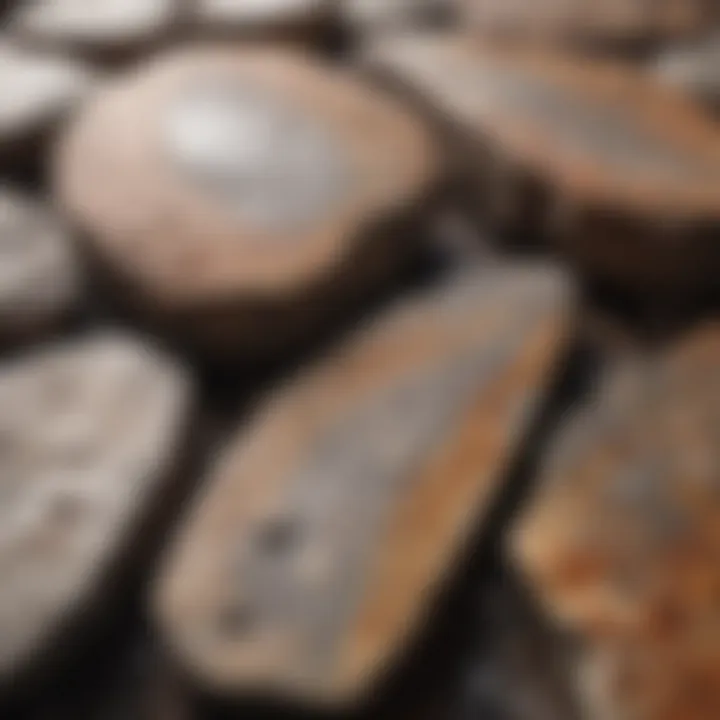
However, while tile cutters are easy to use, they do have limitations in terms of the thickness and hardness of the material they can effectively cut. Understanding these limitations is critical for anyone wishing to expand their rock collection or work on specific projects.
Choosing the right type of rock cutting machine not only impacts efficiency but also the quality of the final product. Evaluating the unique needs and resources available can significantly enhance the rock processing experience.
Polishing Machines: An Overview
Polishing machines play a critical role in the rock processing domain. They are designed to refine the surface finish of cut rocks and minerals, producing aesthetically pleasing results essential for various applications. In the context of this article, the overview of polishing machines sheds light on their functionality, types, and significance for rock collectors and professionals in geology. Understanding their importance leads to a deeper appreciation for the craftsmanship involved in the hobby and industry.
Benefits of Polishing Machines
- Enhanced Aesthetics: Polishing machines can transform dull stone surfaces into vibrant, glossy finishes, revealing the natural beauty of the rock. This enhancement is crucial for collectors aiming to showcase their specimens attractively.
- Surface Improvement: Beyond aesthetics, these machines remove surface imperfections, scratches, and blemishes. This results in a smoother surface that highlights the rock's features better.
- Increased Value: Well-polished rocks often command higher prices in the market. Collectors and dealers recognize that the quality of the finish can significantly influence perceived value.
- Versatility: Polishing machines can handle a variety of stones, including granite, marble, and semi-precious stones. This versatility makes them invaluable tools for both hobbyists and professionals alike.
Considerations in Choosing Polishing Machines
When selecting a polishing machine, several factors should be taken into account:
- Type of Machine: Different types of polishing machines cater to specific polishing needs. Understanding the distinctions can help users choose the most appropriate one for their projects.
- Power and Speed: The power and speed of a machine significantly affect its performance. A suitable machine should balance efficiency with manageable operational power.
- Portability: Particularly for hobbyists, having a machine that is easy to move can be beneficial.
- Cost: Budget considerations are always essential. Evaluating the cost against the functionality and quality of the machine will aid in making a sound investment.
"The outcome of polishing significantly affects the visual appeal and marketability of a specimen; hence, the right machine is crucial."
Rotary Polishers
Rotary polishers are among the most common types of polishing machines used in rock processing. They operate using a circular motion that allows a polishing pad to rotate against the stone surface. This action efficiently grinds and smooths the rock, making it suitable for various materials, including softer stones.
The key advantages of rotary polishers include:
- Ease of Use: These machines are relatively straightforward to operate, making them ideal for hobbyists.
- Consistency: They offer a consistent finish, which is particularly important when working on multiple pieces.
- Affordability: Generally, rotary polishers are more cost-effective compared to other advanced polishing machines.
Vibrating Polishers
Vibrating polishers utilize a different mechanism where a vibrating plate provides the polishing action. This type of machine can produce fine finishes and is particularly effective for delicate stones and fossils.
Some considerations regarding vibrating polishers include:
- Gentle Polishing: This makes them suitable for softer stones that might be damaged by more aggressive polishing methods.
- Time Efficiency: Vibrating polishers can sometimes achieve high-quality finishes in a shorter time frame when polishing finer details.
- Variability in Finish Quality: While they are effective for many applications, users may need to focus on technique and pad selection to achieve desired results.
In summary, understanding the polishers available is key for rock enthusiasts and professionals. Both rotary and vibrating polishers have their unique advantages and applications, which can greatly enhance the quality of rock specimens.
Machine Components and Specs
Understanding the components and specifications of rock cutting and polishing machines is crucial for both users and collectors. The right components contribute significantly to the machine's performance, durability, and efficiency. Each element plays a specific role, impacting the quality of the finished product and ensuring that operations proceed smoothly. This section highlights the key components, their benefits, and considerations for selecting the appropriate machines for various applications.
Cutting Blades and Tools
Cutting blades and tools are the heart of rock cutting machines. They determine the effectiveness and precision of the cutting process. Diamonds are often used in blades because of their hardness, making them suitable for working with tough materials like granite and quartz. The design of the blade also matters. For instance, continuous rim blades provide a smooth cut, while segmented blades allow for quicker cuts but might create more rough edges.
Benefits of using high-quality blades include:
- Enhanced durability: Good blades last longer and reduce the frequency of replacements.
- Improved efficiency: Quality blades cut quickly and accurately, saving time.
- Versatility: Some blades can handle a variety of materials, making them useful for different projects.
It is essential to match the blade type with the material being cut. A mismatch can lead to damage to the blade and the material. Users should consider not only the hardness of the blade but also its intended application, as this affects both cutting speed and quality.
Speed and Power Requirements
The operational speed and power of rock cutting and polishing machines are vital considerations. The speed at which the blade rotates determines how efficiently it can cut through various rock types. Higher speeds are often more effective for softer materials but can create issues when working with harder substances.
Key factors to keep in mind regarding speed and power include:
- Motor power: A more powerful motor allows for higher speeds, enabling efficient cutting of more complex and harder materials.
- Operation control: Variable speed settings provide versatility for different materials, allowing users to adjust according to specific project needs.
- Heat management: Faster operations often generate more heat, which can affect both the machine and the material. Therefore, a machine with good heat dissipation is preferable.
Operational Process
The operational process of rock cutting and polishing machines is critical for achieving optimal results in rock processing. Understanding this process allows hobbyists, collectors, and professionals to effectively utilize their equipment for the best outcomes. Key elements such as setup, cutting techniques, and polishing procedures play significant roles in the overall efficiency and quality of work.
Setup and Calibration
Proper setup and calibration of rock cutting and polishing machines ensure accuracy and precision in operations. Before starting any project, it is important to check that all components are assembled correctly. This involves ensuring that the cutting blades are securely attached and aligned.
Calibration helps in achieving the right cutting depth and angle. Many machines have specific settings that must be adjusted based on the type of rock being processed. This is especially important for hard stones, where even slight misalignments can result in excessive wear on tools and poor quality cuts. Investing time in setup can lead to smoother operations and better finishes.
Cutting Techniques
The choice of cutting technique significantly influences the efficiency and quality of the cut. There are various techniques available, depending on the machine type and the nature of the rock. Some common methods include:
- Straight Cuts: Best for general slicing of rocks into manageable sizes.
- Curved Cuts: Useful for creating intricate designs and shapes.
- Notching: Ideal for preparing edges for additional stonework or for gluing pieces together later.
It is important to select the appropriate technique based on the desired outcome and the hardness of the stone. Understanding how to operate the machines effectively can prolong the lifespan of the tools and ensure superior finishes.
Polishing Procedures
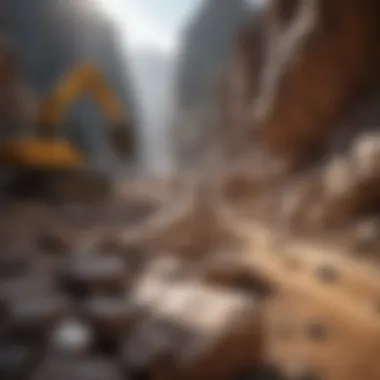
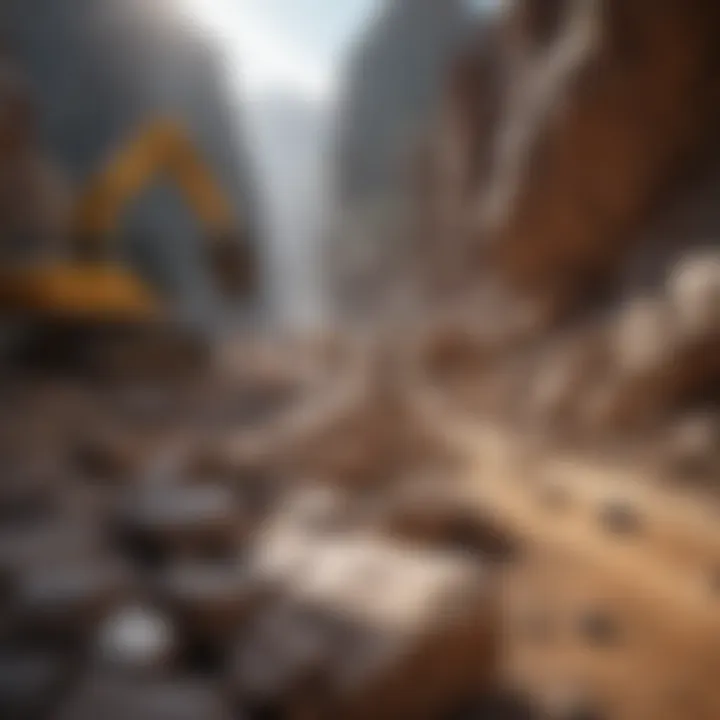
After cutting, polishing becomes the next critical step. Polishing machines, whether rotary or vibrating, require their own set of procedures to achieve that high-gloss finish that is often desired for display pieces. Key steps in polishing include:
- Surface Preparation: Remove dust and any residues from the cutting process.
- Choosing the Right Polish: Different stones require different types of polishing compounds.
- Application: A uniform application of polish is crucial to prevent uneven surfaces.
- Buffing and Finishing: This step ensures that the final product not only looks good but is also protected from future wear.
Proper polishing can turn a raw rock into a stunning piece of art, highlighting its natural beauty and features.
Following these operational processes meticulously can transform the rock processing experience, ensuring high-quality results and enhancing the satisfaction for collectors and hobbyists alike. Efficient operation ultimately leads to the creation of remarkable pieces that can be appreciated for their craftsmanship and natural allure.
Applications in Various Fields
Rock cutting and polishing machines serve critical roles across a range of fields. Their applications can be classified into several categories including geological research, hobbyist and collector use, and industrial applications. Each field benefits uniquely from these machines, underlining their importance in processing natural specimens.
Geological Research
In geological research, precision and accuracy are paramount. Rock cutting and polishing machines allow researchers to obtain samples with minimal material loss. This is essential for conducting analyses that rely on the integrity of the sample. The use of cutting-edge technology in machines enhances the ability to prepare thin sections for petrographic studies, which is vital in understanding rock formations, mineralogy, and the geological history of an area.
Additionally, scientists utilize these machines to produce polished samples for educational purposes. Students in geology programs often engage with polished samples to identify minerals and rock types, understanding their characteristics and formations. The clarity achieved through polishing can illuminate features that contribute to educational discussions.
Precision in cutting and polishing directly relates to the quality of geological research outputs.
Hobbyist and Collector Use
Hobbyists and collectors significantly benefit from rock cutting and polishing machines. Those who carve geological specimens often look for equipment that allows them to refine their materials. These machines help hobbyists create beautiful, polished stones for personal collections or sale. The aesthetic appeal of polished rocks can significantly increase their value, allowing collectors to maximize their investments.
Moreover, many enthusiasts appreciate the hands-on process of cutting and polishing. Engaging with the raw material provides an immersive experience, allowing collectors to develop a deeper understanding of geology. Rock shows and exhibitions often feature polished stones, demonstrating the skill and appreciation of those who use these machines effectively.
Industrial Applications
In industrial contexts, rock cutting and polishing machines play a vital role in production processes. Industries such as construction and stone manufacturing utilize these machines to create materials for architectural and decorative purposes. The ability to create precise cuts ensures materials fit various designs, enhancing building aesthetics.
Furthermore, large-scale operations rely on automated systems for efficiency. Machines designed for high-volume production can handle significant quantities of stone, reducing labor costs while meeting the demands of the marketplace. The sustainability of production also becomes a consideration, as advanced machines contribute to minimizing waste material. By efficiently processing rocks, industries can ensure the responsible use of natural resources.
In summary, the applications of rock cutting and polishing machines across geological research, hobbyist endeavors, and industrial operations highlight their versatility and necessity. Each domain benefits from advancements in technology, facilitating better outcomes in research, enhancing collections, and driving industrial productivity.
Maintenance and Care of Machines
Proper maintenance and care of rock cutting and polishing machines is crucial for ensuring their longevity and optimal performance. These machines are significant investments for geology professionals, hobbyists, and collectors. Regular upkeep not only extends the equipment's lifespan but also enhances productivity, reduces the likelihood of breakdowns, and ensures that the quality of work remains high. In this section, we delve into the specific tasks required for routine maintenance, along with common troubleshooting strategies.
Routine Maintenance Tasks
Routine maintenance tasks are essential for keeping rock cutting and polishing machines in top shape. Here are some common maintenance practices:
- Cleaning: After each use, machines should be cleaned thoroughly. Dust, rock debris, and slurry remnants can accumulate and affect performance. A proper cleaning routine will help prevent corrosion and wear on blades and saws.
- Inspection of Components: Regular checks of key components such as cutting blades, polishing pads, and belts are vital. Look for signs of wear or damage, and replace parts as necessary to maintain effective operation.
- Lubrication: Many machines have moving parts that require lubrication. Using the correct type of lubricant can significantly reduce friction and prolong the life of the machine. Itβs important to refer to the manufacturer's manual for specific guidelines on lubrication intervals and products to use.
- Calibration: Machines may need recalibration after extensive use. Ensuring that settings for speed, pressure, and cutting depth are properly calibrated can prevent mishaps and improve the precision of cuts and polish.
- Storage: Store machines in a dry location when not in use. Exposure to moisture can cause rust and deterioration. Cover machines to protect them from dust and possible damage.
Troubleshooting Common Issues
Despite diligent maintenance, issues may still arise during the operation of rock cutting and polishing machines. Being able to troubleshoot these problems can save time and frustration. Here are some common issues and potential solutions:
- Poor Cutting Performance: If the machine struggles to cut through material, check the condition of the cutting blade. Dull or damaged blades should be replaced. Ensure the machine is correctly calibrated, particularly in regards to speed and pressure.
- Vibrations or Noises: Unusual vibrations or sounds might indicate loose parts or an unbalanced machine. Inspect moving components and tighten any loose screws or bolts. If a part is damaged, consider replacing it.
- Overheating: If the machine is overheating, it may be working at excessive speeds or not receiving adequate cooling. Reviewing the operational settings and ensuring proper ventilation can help alleviate this issue.
- Slurry Build-Up: If there is excessive slurry build-up, ensure that you are using the correct amount of water and that the drainage systems are clear.
- Electrical Malfunctions: For machines that are electrically operated, check all connections and circuit components regularly. If issues persist, it may be best to consult with a professional technician.
"Regular maintenance is not just about following procedure, it's about ensuring your equipment works efficiently and safely."
By maintaining rock cutting and polishing machines appropriately, users can enjoy enhanced functionality and reduced downtime. This proactive approach to machine care will ultimately yield better rock processing results, making it an invaluable part of any collection or operational setting.
Technological Advances in Rock Processing
In recent years, the field of rock processing has witnessed significant advancements. These developments play a crucial role in enhancing the efficiency and effectiveness of rock cutting and polishing machines. The integration of new technologies not only improves production rates but also boosts precision and accuracy. Consequently, this becomes increasingly important for professionals in geology and collectors who seek to maintain high standards in their processes.
Automation and Smart Technology
Automation has emerged as a transformative force in rock processing. The adoption of automated systems reduces the need for manual labor, allowing for safer and more efficient operations. Machines equipped with smart technology can analyze various factors in real-time, such as temperature, pressure, and cutting speed. This capability helps optimize performance and reduces the possibility of errors during operation.
Smart technology often utilizes advanced algorithms. These algorithms process data to adjust machine settings automatically. As a result, the quality of the cut or polish increases. Moreover, machines can perform more consistently over time. This is especially beneficial for hobbyists and professionals who require uniformity in their results.
Additionally, remote monitoring capabilities via IoT (Internet of Things) devices enable users to keep track of their machinery from anywhere. This feature helps in promptly addressing issues before they escalate, thereby ensuring minimal downtime.
"The integration of smart technology is redefining the landscape of rock cutting and polishing, enhancing productivity and precision like never before."
Sustainability in Production
Sustainability is an essential consideration in modern rock processing technology. With growing concerns about environmental impact, manufacturers have begun to prioritize eco-friendly practices. New machine designs focus on reducing waste and energy consumption. This shift not only aligns with global sustainability goals but also appeals to environmentally conscious collectors and professionals.
Current innovations include:
- Energy-efficient motors: These reduce electricity usage during operations.
- Water recycling systems: Capturing and reusing water decreases the overall consumption and minimizes waste.
- Biodegradable cutting fluids: Using environmentally-friendly fluids helps mitigate pollution risks associated with traditional chemicals.
Implementing sustainable practices has several advantages:
- Cost savings: Reduced energy consumption translates to lower operational costs.
- Regulatory compliance: Meeting environmental regulations can safeguard businesses from potential penalties.
- Positive public perception: Upholding sustainability can enhance a brand's reputation, particularly among environmentally conscious consumers.

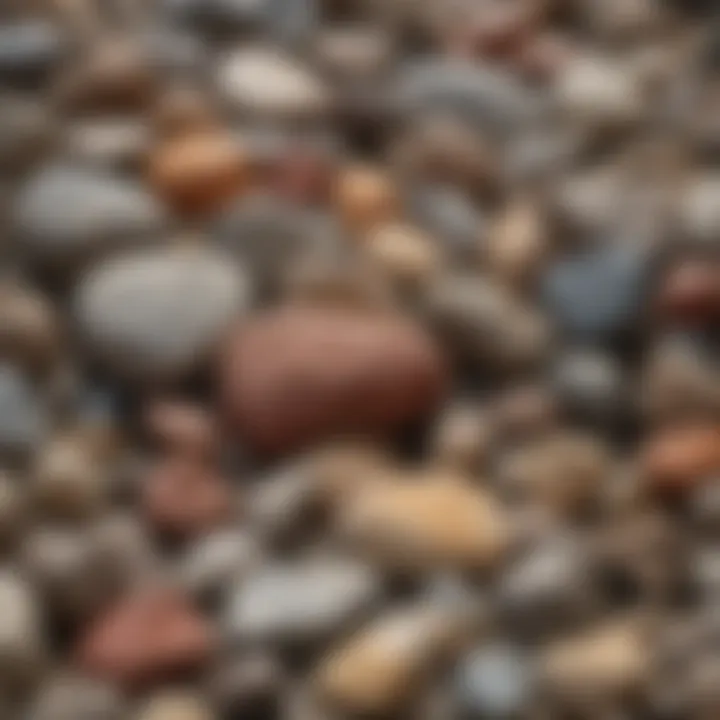
Choosing the Right Machine
Selecting the appropriate rock cutting and polishing machine is a decisive step for anyone involved in geology, whether professionals or collectors. The choice of machine can impact not only the quality of the finished product but also the efficiency and ease of the processing tasks. Not all machines serve the same purpose, and understanding the nuances of each is crucial.
The right machine enhances performance, minimizes resource wastage, and can significantly influence the final appearance of the polished rock. Poor selection may lead to machine breakdown, inefficiency in processing, or subpar finished products. Thus, careful consideration of various factors will lead to more satisfactory results in any rock-related project.
Factors to Consider
When choosing the right machine, essential elements come into play:
- Type of Material: Different machines are designed for different types of rocks. Consider the hardness and texture of the rocks you will be working with.
- Machine Size: Evaluate the dimensions of the workspace. The size of the machine should align with the available space and the scale of your projects.
- Power and Speed Requirements: Examine the energy needs of the machine. Higher power often means faster cutting and polishing, but also higher operational costs.
- Budget Constraints: Machines vary widely in price. It's vital to balance between desired features and budget.
- Maintenance and Support: Opt for machines from manufacturers that offer good after-sales support and readily available parts.
- User Experience: Consider ease of use as some machines may require advanced skills or additional training.
Comparative Analysis of Models
A comparative analysis of different models provides valuable insights into the effectiveness of each option. Factors to analyze include:
- Functionality: What specific features does each model offer? Does it serve multiple purposes or specialize in one area?
- User Reviews: Feedback from other rock enthusiasts is invaluable. Platforms like Reddit and Facebook can offer real-world experiences from other collectors.
- Performance Metrics: Compare cutting speed, polishing quality, and durability between models.
- Price-to-Performance Ratio: Does the investment align with the level of performance promised? Look beyond the initial purchase price.
- Technological Features: Examine any smart technology or automation features that might add to efficiency and ease of use.
Case Studies and Success Stories
Case studies and success stories serve as exemplars in the realm of rock cutting and polishing machines. They provide real-world applications showcasing the effectiveness and innovation within this equipment. By analyzing specific instances, readers can gain insights into the practical uses of these machines, the challenges faced, and the solutions implemented.
One primary advantage of studying these cases is the opportunity to observe technological advancements in action. For instance, examining how a geological research team utilized a diamond wire saw can reveal not only the machine's precision but its adaptability to different rock types and terrains. This deeper understanding helps potential users appreciate the value of investing in advanced technology for their projects.
Innovative Uses in Geology
In geological research, rock cutting and polishing machines are essential tools. Their capabilities extend to creating thin sections for microscopic analysis, helping scientists study mineral composition and structure. A notable case involved a geological institute that upgraded to a fully automated bridge saw. This machine significantly increased their throughput of rock samples, enabling rapid analysis and enhancing collaboration across departments. The automation of cutting processes reduced human error, resulting in consistent quality.
Moreover, a team of field geologists successfully integrated polishing machines to prepare rock specimens for educational purposes. This use not only elevated the aesthetic quality of the samples but also inspired educational displays that sparked interest among students.
Prominent Collections Enhanced by Technology
Several renowned collections have experienced remarkable enhancement through the use of modern rock cutting and polishing machines. One prestigious museum, known for its geological collection, invested in advanced rotary polishers. As a result, their specimens were not only restored to their original luster but also preserved more effectively.
The investment in technology has led to the curation of captivating exhibits, engaging visitors and raising awareness about geology as a field. The transformation was noted in social media platforms, such as Facebook and Reddit, where collectors and enthusiasts shared their admiration for the polished specimens.
Additionally, a private collector utilized specific polishing machines tailored for fragile minerals and fossils. This careful application ensured that rare pieces maintained their integrity while being displayed. The collector reported significant appreciation from peers for the quality of their collection, showcasing how the right equipment can elevate personal or public exhibits.
"In the world of geology, investment in the right machines can lead to not just preservation, but a revival of natural history for generations to appreciate."
These cases emphasize the broader impacts of rock cutting and polishing technology. They showcase how the thoughtful use of these machines transcends basic functionality, resulting in educational advancements, improved research outputs, and enriched collecting experiences.
The Future of Rock Cutting and Polishing Machines
The rock cutting and polishing machine industry is poised for substantial evolution. As technology progresses, these machines will adapt to new methods and techniques, benefitting both professional users and hobbyists. Understanding the future of this industry is essential because it influences not only production efficiency but also the overall quality of finished products. The discussion on predicted trends and innovations includes developments that will optimize the workflow and enhance the user's experience. Furthermore, the impact on collecting and trade highlights how advancements in these machines can shape the availability and quality of collectible specimens.
Predicted Trends and Innovations
The trends in rock cutting and polishing machine technology show a clear direction towards automation and user-friendliness. One significant innovation is the integration of sensor technologies. Sensors can monitor conditions such as temperature and humidity, which are crucial for maintaining optimal working conditions. This ensures that the diamonds and other abrasives used in cutting and polishing operate at peak efficiency.
Additionally, software advancements are making machines more intelligent. User interfaces are becoming more intuitive, allowing operators to set parameters with ease. In particular, advancements in CAD (Computer-Aided Design) software allow custom designs to be implemented swiftly, elevating the design potential for hobbyists and professionals.
Remote operation capabilities are another cutting-edge trend. By utilizing the Internet of Things (IoT), operators can manage and monitor machines from a distance. This can lead to better productivity and reduce downtime by allowing for immediate troubleshooting. As a result, the collective efficiency of rock processing will improve significantly.
Key Innovations to Watch Out For:
- Integration of sensor technologies.
- Enhanced user interfaces through software advancements.
- Advancement in CAD software for custom designs.
- Implementation of remote operation capabilities.
Impact on Collecting and Trade
The evolution of rock cutting and polishing machines directly influences the landscape of collecting and trade. As machines become more efficient and precise, collectors can expect higher-quality specimens. This enhancement in quality means that the appeal of certain rocks and minerals may grow, directly impacting their market value.
Moreover, the enhanced capabilities of machines enable collectors and sellers to offer rarer pieces, which would have been difficult to process previously. Collectors benefit from having access to better-polished specimens, showcasing the unique features of each rock without compromising integrity.
Economic aspects also come into play. Improved machine performance reduces the costs associated with labor and material consumption. Consequently, this cost-efficiency can lower the retail prices of polished rocks, making them more accessible to a wider audience.
End
As the future unfolds, advancements in rock cutting and polishing machines will undeniably shape both the collection and trading of geological specimens. Keeping an eye on these developments will be crucial for enthusiasts aiming to understand market dynamics and the potential for enhanced collection practices. The path ahead is bright for both commercial ventures and individual collectors alike as they adapt to these inevitable changes.
Closure
In the realm of rock cutting and polishing machines, the conclusion synthesizes the various elements discussed throughout the article. This final segment is crucial because it encapsulates the essence of the topics covered and reinforces their relevance to both novice and experienced users alike. As we have dissected the different types of machines, their operational processes, and maintenance requirements, we see that comprehending these facets is vital for effective utilization.
Summary of Key Insights
In summary, several key takeaways emerge from the article:
- Diverse Varieties: Machines vary widely, from diamond wire saws to rotary polishers, each serving distinct purposes in rock processing.
- Operational Excellence: Proper setup and knowledge of cutting techniques drastically improve outcomes. Calibration plays a large role in achieving precision.
- Maintenance Matters: Regular maintenance can eliminate common issues, ensuring longevity and reliability of the machines.
- Technological Advancements: New technologies, including automation and smart features, are shaping the future of rock processing.
- Application Across Fields: From education to industrial use, these machines have a profound impact on geological research and hobbyist activities.
These insights demonstrate the multifaceted nature of rock cutting and polishing machines, illustrating their significance in enhancing the quality of work for both professionals and enthusiasts.
Final Thoughts on Machine Selection
Selecting the right rock cutting and polishing machine is not a trivial matter. It requires a careful evaluation of various factors:
- Purpose of Use: Different tasks demand different machines. For instance, geological research may prioritize precision, while hobbyists may seek versatility.
- Budget Considerations: Costs can vary widely. Assessing budgets against machine capabilities will lead to informed decisions.
- Support and Service: Consider the availability of service support and parts for the chosen machines, as this can impact efficiency and recovery times.
- User Skill Level: Match the machine's complexity with the user's experience to reduce frustration and optimize results.