Polishing Jewelry with a Dremel: Techniques and Insights
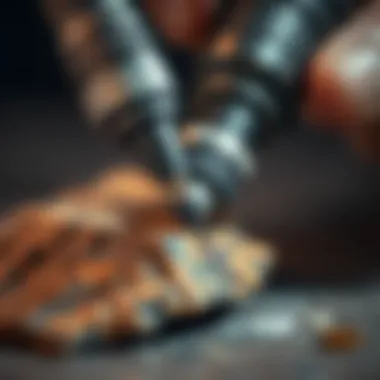
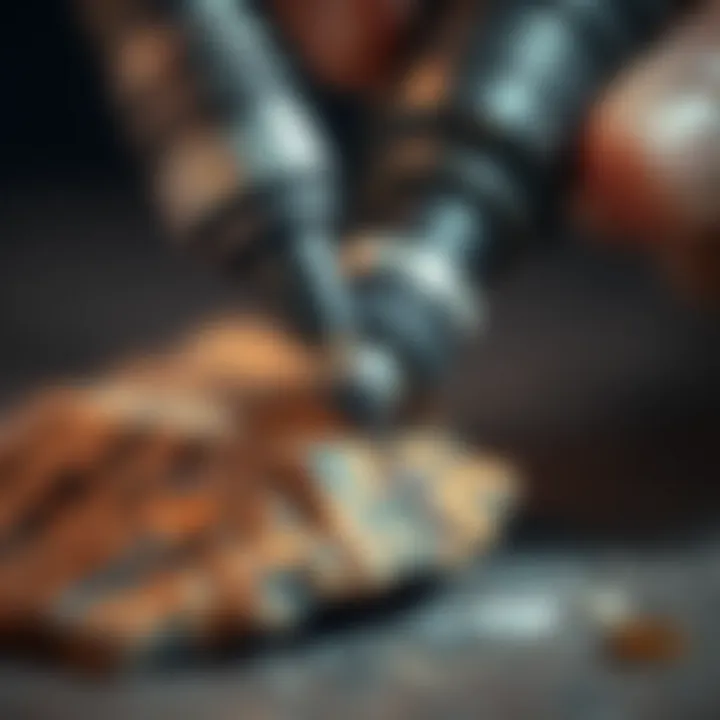
Intro
Polishing jewelry is an art, not just a craft, especially when one opts for a Dremel tool. This versatile instrument can elevate a simple piece of clutter to a shining treasure, reflecting light as it dances upon its surface. Whether you are a hobbyist with a small collection or someone who occasionally dabbles in custom work, understanding the nuances of using a Dremel for polishing can significantly enhance your results.
Imagine the satisfaction of transforming an old, dull ring into a sparkling gem. The right techniques and tools can make all the difference in achieving the desired shine and longevity of your jewelry. In this guide, we shall explore essential methods for polishing various materials, safety precautions to take, and tips that seasoned jewelers have picked up over the years.
Just like a seasoned traveler knows the shortcuts of a winding road, a proficient user knows how to navigate the complexities involved in polishing jewelry with a Dremel. From the right attachments to safety gear, everything counts in creating that flawless finish. So, let's dive in deeper; it’s time to get your Dremel revved up and ready to polish!
Intro to Jewelry Polishing
Jewelry polishing is not just a task; it’s an art form that breathes life back into pieces that may have dulled over time. For enthusiasts and professionals alike, the process of polishing jewelry carries immense weight. It transforms worn metals and gemstones into vibrant reflections of brilliance, allowing each piece to regain its rightful shine. This article aims to delve comprehensively into the intricate process of polishing jewelry with a Dremel tool, highlighting techniques and insights that will enhance any jewelry polishing experience.
The Importance of Polishing cannot be overstated. Over time, jewelry naturally accumulates dirt, oils, and scratches from regular wear. If neglected, these can cause irreparable damage. Polishing not only helps in removing these imperfections but also protects the surface from further wear, thus extending the life of the jewelry. Plus, a well-polished piece can significantly elevate its perceived value. Imagine a ring that sparkles like new—this is the impact that effective polishing can have.
When it comes to techniques for polishing, there are various methods depending on the material at hand. Each type of metal or gemstone has its properties that require tailored approaches. A thorough understanding of these differences can prevent damage and enhance the overall appearance of the piece.
Integrating the right tools also plays a critical role in achieving desired results.
Understanding the Importance of Polishing
Before we get into the technical aspects, let's consider why regular polishing is essential. First and foremost, it helps in maintaining the aesthetic appeal of the jewelry. Just as one maintains their car’s shine, jewelry requires the same attention. A good polish will remove tarnish buildup which can be particularly prevalent on silver pieces. Not only does polishing restore luster, but it also protects against potential abrasions. When introducing your jewelry to friends or family, first impressions matter. A beautifully polished piece can significantly enhance its attractiveness, serving as an instant conversation starter.
Another vital aspect is the practical side of jewelry ownership. Keeping pieces polished can help in avoiding costly restoration down the line. The difference between a simple polish and a complicated restoration can often be equivalent to day and night in terms of cost and effort.
What is a Dremel Tool?
When discussing polishing, it's crucial to introduce the Dremel tool. This versatile rotary tool is well-loved by both hobbyists and artisans. Not limited to just polishing, the Dremel can cut, grind, and sand various materials, making it a pivotal instrument in jewelry making and maintenance. Its robust range of attachments unlocks a world of possibilities, from fine engraving to smooth surface finishing, making it ideal for a variety of jewelry projects.
Dremel tools come in different models, each equipped with unique features. Being lightweight and easy to maneuver, they allow for precision work, even on intricate designs. Choosing the right Dremel model depends on your specific needs, be it heavy-duty polishing or delicate touch-ups. Understanding its components and functions will undoubtedly give you a head start into the art of using this tool effectively.
In summary, this article will be your comprehensive guide to the ins and outs of polishing jewelry with a Dremel. From understanding the significance of polishing and the flexibility of the Dremel tool, to safe practices and techniques tailored for various materials, you'll become equipped with knowledge that turns the task into a rewarding craft.
Getting Started with the Dremel
Starting out on your journey with a Dremel tool can feel like getting the keys to a treasure chest. It unlocks a world of creativity and precision, especially when it comes to polishing jewelry. Understanding the ins and outs of this powerful tool is foundational for anyone looking to refine their techniques. Whether you're a seasoned jeweler or a hobbyist, getting a grip on how to effectively use a Dremel will elevate your polishing game. In this section, we will explore how to select the right Dremel model, identify essential attachments, and set up a proper workspace that encourages both safety and efficiency.
Selecting the Right Dremel Model
When it comes to Dremels, one size doesn’t fit all. It’s crucial to choose the right model based on your specific needs and budget. Not every job requires a high-powered machine. If you're just getting into jewelry polishing, a basic model like the Dremel 3000 might suffice, offering versatility and manageable power without overwhelming you.
However, if you're looking to tackle more intricate jobs or heavy materials, consider the Dremel 4300, which provides advanced features like a variable speed and integrated LED lights for enhanced visibility. The choices are plentiful, and each model has something unique to offer. Keep in mind the following pointers when picking out your Dremel model:
- Power: Higher RPM (revolutions per minute) means a more robust tool, but it can also be harder to control for fine work.
- Versatility: Some models come with additional features like attachments or a flex shaft, making them more versatile in applications beyond jewelry.
- Comfort: Your Dremel should feel comfortable in your hand. Look for ergonomic designs, especially if you plan on polishing for extended periods.
Essential Attachments for Jewelry Polishing
Attachments are like icing on the cake. They can significantly enhance your Dremel's effectiveness. When it comes to polishing jewelry, right attachments are essential for achieving that coveted shine. Here are a few must-haves:
- Polishing Wheels: Felt or cotton wheels are essential for applying polish and buffing the surface to a high gloss.
- Drill Bits: For cleaning out hard-to-reach areas on your pieces, smaller drill bits provide the precision needed.
- Diamond Burrs: These are invaluable for more intricate work, particularly on gemstones or harder metals.
- Sanding Discs: Perfect for smoothening rough edges before the final polishing stage.
It can be tempting to buy every attachment out there, but it's wiser to start with a select few that cater specifically to your jewelry projects. Once you have the basics down, you can expand your collection as needed.
Setting Up Your Workspace
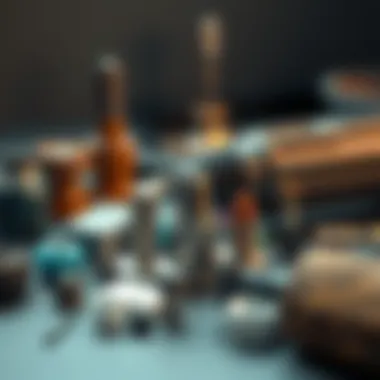
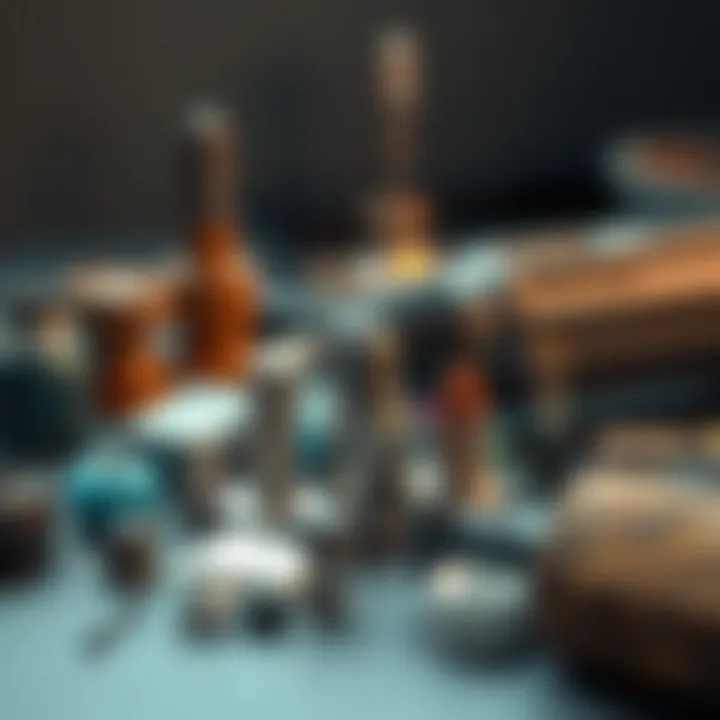
A well-organized workspace is not just a luxury; it’s a necessity when working with a Dremel tool. To ensure that you can work efficiently and remain safe, consider the following:
- Good Lighting: Bright, diffused lighting can help prevent mistakes and ensure you see every detail.
- Sturdy Surface: A solid workspace such as a dedicated table or bench prevents wobbling and keeps your projects stable.
- Clear Area: Avoid clutter. This will minimize your chances of accidents and give you space to maneuver comfortably.
- Ventilation: Polishing can create dust and fumes. Ensure your workspace is well-ventilated, or consider using a dust mask.
“A clean and organized workspace is half the battle won.”
Make it a habit to clean your work area regularly. Organizing your tools and attachments can save you time and help prevent mishaps.
By allowing yourself to get comfortable with your Dremel model, appropriate attachments, and a safe workspace, you're setting the stage for success. Once you're up and running, the possibilities for polishing jewelry become boundless, leading to some truly stunning results.
Techniques for Polishing Various Materials
Polishing jewelry effectively requires an understanding of the different materials involved. Each material has its unique characteristics that influence the techniques and tools used during the polishing process. By mastering the specific methods for various materials, you can achieve excellent results while preserving the integrity and beauty of your pieces. In this section, we will explore approaches for polishing metals, gemstones, and organic materials, offering insights that can elevate your jewelry craftsmanship.
Polishing Metals
When it comes to metals, effective polishing is all about precision and technique. Different metals will react in their own ways when subjected to the Dremel's spinning motion with attachment bits. Let's look at a few key considerations:
- Choose the Right Bit: Attaching the correct polishing bit depends on the metal type. For instance, a cotton buff is great for a high polish on silver, whereas a felt wheel might be best for metals like gold.
- Speed Control: Adjusting the speed of the Dremel is crucial. Softer metals like aluminum can easily scratch if the speed is too high. Use a slower speed to avoid damage from heat and friction.
- Pressure Application: Be consistent with pressure; too much can lead to uneven surfaces or scratches. Light, even pressure helps in achieving a smooth finish.
Utilizing these techniques not only makes the polishing process smoother but also prolongs the life of the jewelry, allowing it to shine brilliantly.
Working with Gemstones
Gemstones require a more delicate approach. Their inherent properties, such as hardness and brittleness, necessitate tailored techniques to avoid damage:
- Identify the Hardness: Knowing the Mohs hardness scale of gemstones is vital. For instance, diamonds can withstand a lot of abrasiveness, while softer stones like opal can easily scratch.
- Use Specific Polishing Wheels: Soft polishing wheels are critical for gems like emeralds and amethyst. They are less likely to produce heat that could cause cracks.
- Slow and Steady Wins the Race: When polishing gemstones, use lower speeds and gentle touches. Care is of the essence, as gentle motions keep the gem intact and retain its luster.
Overall, taking a mindful approach to gemstone polishing will enhance their natural shine and maintain their beauty.
Handling Organic Materials
Organic materials, such as pearls or coral, present their own set of challenges due to their delicate nature. Here are a few techniques to handle these precious items effectively:
- Gentle Touch: It's essential to keep in mind the fragile structure of organic materials. Always polish using the softest attachments available, like a lamb's wool or a microfiber cloth.
- Avoiding Chemicals: Organic materials can be sensitive to certain chemicals used in jewelry cleaning. Stick to gentle methods, relying more on physical polishing rather than abrasive compounds.
- Right Conditions: When polishing organic materials, consider the environment. High heat can cause pearls and corals to lose their luster. Make sure your workspace is well-regulated in terms of temperature.
"When you know the nuances of each material, you harness the power of polishing to turn ordinary jewelry into extraordinary pieces."
To further deepen your knowledge on polishing techniques and jewelry care, you might find it beneficial to explore these resources: Jewelry Making Forum, The Gemological Institute of America, and Wikipedia's article on Jewelry.
Safety Precautions and Best Practices
When it comes to polishing jewelry with a Dremel, it’s essential to prioritize safety. Not only does this protect you, but it also preserves the integrity of the pieces you’re working on. Jewelry polishing can generate heat, dust, and potential hazards, making safety precautions and best practices crucial elements of the process. You'll want to ensure a smooth and safe experience while enhancing your skills and creativity. Moreover, taking the time to set up your workspace and gear properly leads to superior results, reduces the risk of accidents, and ensures that your jewelry remains in top shape.
Protective Gear
Diving into the art of jewelry polishing without the proper protective gear is akin to swimming in shark-infested waters without a cage. It’s a serious mistake. First and foremost, consider investing in high-quality safety goggles. These will shield your eyes from flying debris or dust particles that could cause irritation or injury. Alongside goggles, a good quality dust mask is also a must-have; think of it as your shield against the fine particulate matter produced during the polishing process.
Depending on your project, you might also want to wear gloves. Gloves not only provide a barrier against sharp edges but also minimize the risk of fingerprints or oils from your skin contaminating the surface you’re polishing. In summary, when preparing to polish jewelry, remember these essentials:
- Safety goggles: Protect your eyes from dust and debris
- Dust mask: Guard against inhaling fine particles
- Gloves: Help prevent cuts and maintain cleanliness
By donning the right gear, you can focus more on perfecting your technique rather than worrying about safety concerns.
Workspace Safety Tips
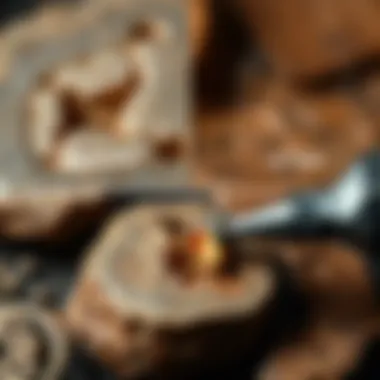
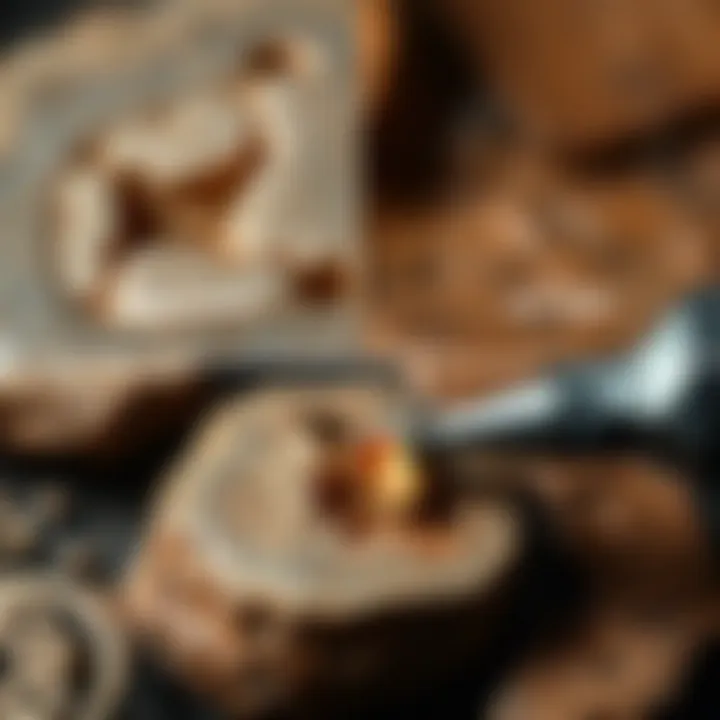
A tidy workspace is not just a personal preference; it’s vital for effective polishing and overall safety. Start by ensuring that your workspace is well-ventilated. This helps dissipate any potentially hazardous fumes released while using the Dremel and keeps the air fresh during your project. Having a clean, organized area is more than a matter of aesthetics; it minimizes distractions and reduces the chance of losing tools or accidentally knocking items over.
Think about the layout of your workspace too. Place your Dremel tool and attachments within easy reach to avoid fumbling around mid-project. Ensure there are no loose materials on the surface that might get caught in the tool or cause you to trip. If you’re using chemicals for cleaning or polishing, make sure they are stored properly and labeled clearly.
Here are some key workspace safety tips to keep in mind:
- Good ventilation: Open windows or use a fan to keep air circulating
- Clutter-free environment: Eliminate distractions for focused work
- Arranged tools: Keep essential items within reach
- Proper storage: Safely store chemicals and label them clearly
Incorporating these practices not only promotes a safer working environment but also enhances the overall polishing experience. Paying attention to these details is what separates a good jeweler from a great one. As the old saying goes, “An ounce of prevention is worth a pound of cure.” Prioritize safety, and you will pave the way for successful and enjoyable jewelry polishing endeavors.
Achieving Different Finishes
In the art of jewelry polishing, achieving distinct finishes can significantly impact the overall look and feel of the piece. Each finish brings its own unique character, highlighting different aspects of the material used. Understanding how to achieve various finishes allows jewelers—both amateur and seasoned—to tailor their creations to specific aesthetics or customer preferences.
Finishing techniques not only enhance visual appeal but also play a role in the piece's durability and maintenance. A smooth, high gloss finish might reflect light beautifully, while an antiqued finish could evoke a sense of history and craftsmanship, suggesting stories untold. This section will delve into three popular finishes: high gloss, brushed, and antiqued, each possessing its distinct qualities and applications.
High Gloss Finish
A high gloss finish can transform a piece of jewelry from ordinary to stunning. This kind of shine amplifies the colors and patterns found in materials like silver or gold, making them pop in a way that catches the eye. The process usually involves thorough polishing with fine-grade polishing wheels or compounds that smooth out surface imperfections while enhancing brilliance.
To achieve this finish, follow these steps:
- Start with a clean surface; use a gentle cleaner to remove any dirt or oils before polishing.
- Attach a soft polishing wheel to your Dremel and apply a fine polishing compound, such as rouge.
- Maintain steady, even pressure while moving the piece across the wheel. Avoid hovering on one spot to prevent overheating.
This shiny finish is particularly desirable in fashion jewelry, where appearance is paramount. However, it's essential to understand that such shines may require more frequent maintenance to keep them looking fresh.
Brushed Finish
The brushed finish is synonymous with subtlety and texture. It creates a matte effect with fine, parallel lines that impart a sense of sophistication and understated elegance. Jewelers often utilize this finish for pieces meant to be worn daily, as it tends to hide imperfections and scratches better than a high gloss.
Here's how to achieve a brushed finish with a Dremel:
- Use a medium to coarse sanding band or abrasive wheel to create those characteristic lines.
- Apply light, consistent pressure while moving the piece in one direction only. This might sound trivial, but direction matters. Each stroke should be deliberate.
- Optionally, follow up with a finer abrasive to soften the finish slightly, enhancing its appeal without losing the texture.
This finish is popular among minimalists and those who appreciate refined designs with a bit of grit. It's highly adaptable, working beautifully on metals and offering a unique look to organic materials.
Antiqued Finish
An antiqued finish seeks to replicate the charm of timeworn relics. It adds depth and richness to a piece, often incorporating darkened recesses that highlight intricate details. This finish is well-suited for vintage-style creations or those looking to evoke nostalgia.
To achieve this antiqued effect, jewelers often use a chemical patina to darken certain areas:
- Start with a well-polished surface; a previous finish is often necessary to achieve contrast.
- Use liver of sulfur or a commercial patina solution suitable for the type of metal you're working with. Always read the instructions carefully—safety first!
- Carefully apply the patina, letting it sit for a short time before rinsing with water.
- Once dry, a light polish with a soft cloth can reveal the high points, balancing the dark areas with brightness.
This process tells a story, enlivening the jewelry with character and history. Customers drawn to antiqued pieces often appreciate the artistry involved and the uniqueness that comes with them.
Achieving Different Finishes is a blend of technique, art, and understanding of materials. As you explore each finish, you’ll find the possibilities are vast, allowing for personal expression and creativity that mold your jewelry into something special. For additional details on polishing techniques, visit resources like Wikipedia or engage with communities on Reddit.
Common Mistakes to Avoid
Polishing jewelry with a Dremel can be a rewarding experience, but it’s all too easy to trip up. Mistakes in the polishing process can lead to disappointing results or even damage to your precious pieces. This section aims to lift the veil on some common pitfalls and how to sidestep them, ensuring smooth sailing in your jewelry polishing journey.
Overheating the Material
One of the most frequent errors jewelers—both seasoned and newcomers alike—make involves overheating the material being polished. Metal, gemstones, and organic materials have different heat tolerances, and exceeding these can result in irreversible damage. For instance, gemstones may crack or shatter, while softer metals can warp. The heat generated by the Dremel can be a silent enemy, as it builds up slowly but surely. To prevent this, periodic cooling breaks are highly recommended.
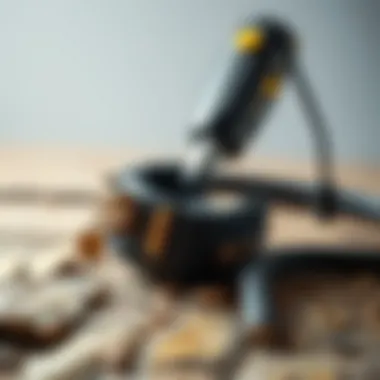
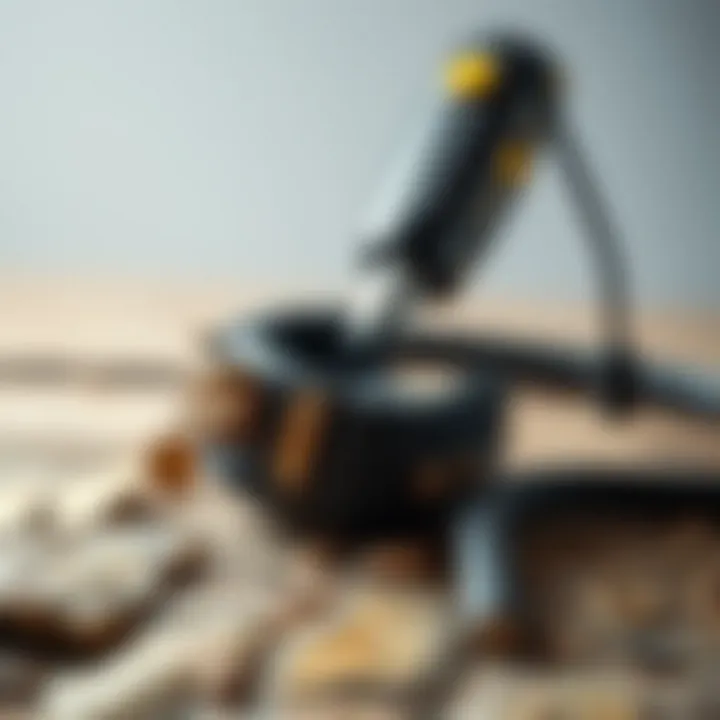
Consider the following tips:
- Check your speed settings: Always start at a lower speed when polishing and only increase it if necessary. High speeds can generate heat quickly.
- Use a light touch: Applying too much pressure can make the Dremel work harder and heat up.
- Inspect frequently: Take a moment to assess the material. If it feels warm to the touch, give it a break.
- Cool down: Use a damp cloth or dip the material in water intermittently to manage temperature.
“When in doubt, cool it out.” A little patience goes a long way in preserving your material’s integrity.
Inconsistent Pressure Application
Applying inconsistent pressure during polishing can create unwanted and uneven finishes, leaving your jewelry looking less than its best. Every polish needs a steady hand; fluctuation in pressure can lead to scratches or burn marks on the surface. The trick is to maintain an even approach while you're in the zone. Here’s how to succeed:
- Practice makes perfect: If you're new to Dremeling, take some time to practice on scrap pieces before diving into your valuable items. This can help you find the right pressure that works for you.
- Stay relaxed: Tension can make you grip the Dremel too tightly, leading to uneven applications. Keep your hands loose.
- Use both hands: If feasible, utilizing both hands can help stabilize your grip and allow for more controlled and consistent movements.
- Follow the surface contours: Whether you’re working with a ring or a pendant, always move with the grain, maintaining even pressure all along the way.
Inconsistencies in pressure might lead to a lackluster finish—what a bummer for your efforts! Always keep your touches gentle and even.
Resources for Further Learning
For more insights on polishing techniques and Dremel usage, you might find the following resources beneficial:
Mastering your technique with a Dremel is a journey filled with learning opportunities. By avoiding common mistakes like overheating and inconsistent pressure, you can enhance your skills and enrich your experience in the vibrant world of jewelry polishing.
Cleaning and Maintenance Post-Polishing
Once you’ve polished your jewelry to a shine that rivals the finest pieces, it’s crucial to consider the cleaning and maintenance stage. This phase is where you ensure the longevity of your hard work and the visual appeal of your jewelry. Proper care post-polishing helps in not only preserving the finish achieved but also in maintaining the overall integrity of the piece.
Removing Residue
After polishing, it’s common for debris or residues to cling to your jewelry. This residue can be a mix of polishing compounds, metal shavings, and even dust particles. Ignoring this step can dull the luster of your work, leading to a lackluster final product. To effectively remove any unwanted residue, follow these steps:
- Select a Soft Cloth: Choose a microfibre cloth, as it’s gentle on surfaces and effective in trapping residues.
- Wipe Gently: With a light hand, wipe down the entire surface, making sure to cover every nook and cranny.
- Use Mild Soap Solution: For tougher residue, mix warm water with a bit of mild soap. Dip your cloth into this solution, wring it out, and wipe again. Avoid soaking any pieces that could be harmed by moisture.
- Dry Thoroughly: After cleaning, ensure that the jewelry is dried completely. Water spots can create an unwanted effect on polished metals.
Important Note: Always perform residue removal with care, as aggressive scrubbing may remove the polish you just achieved.
Proper Storage Techniques
After all your effort in polishing, the last thing you want is to risk scratching or tarnishing your jewelry. How you choose to store your pieces can greatly influence their longevity. Here are some practices worth adopting for optimal storage:
- Use a Jewelry Box: Invest in a quality jewelry box with compartments. This helps keep each piece from scratching against others. Felt-lined interiors are preferable because they provide an additional layer of protection.
- Avoid Humidity: Store your jewelry in a dry place. High humidity can lead to tarnishing, especially with silver and other metals. Consider using silica gel packets in your storage area to absorb moisture.
- Separate Different Materials: If you have jewelry made of mixed materials—like metals paired with gemstones—store them separately to avoid contact that could lead to scratches.
- Cover with Soft Cloth: Even when not in use, cover your jewelry with a soft material to provide an additional layer of protection from dust and scratches.
By incorporating these cleaning and maintenance practices, you are setting the stage for your polished jewelry's durability and shine to last. The quality of care that goes into your jewelry not only reflects your craftsmanship but also enhances the appreciation of your beloved pieces.
Culmination and Continued Learning
In the world of jewelry polishing, every stroke of the Dremel can be the difference between a piece that merely shines and one that dazzles. Understanding the techniques and insights discussed throughout this article not only bolsters our skills but also enriches our appreciation for the craft. Polishing isn’t just a matter of aesthetics; it’s about preserving the integrity and story behind each piece. Every polished surface gleams with the memory of its creation.
The importance of continued learning cannot be overstated. In a field as dynamic and evolving as jewelry making, staying abreast of the latest tools, techniques, and best practices is essential. This ensures that our artistry remains sharp and competitive. The journey of mastering Dremel polishing is ongoing. Each piece that goes through this process offers valuable lessons on patience and attention to detail, not to mention a chance to refine our personal techniques. Moreover, sharing experiences and learning from others is equally vital for growth.
Resources for Further Study
Exploring extensive resources helps deepen understanding and master new skills in jewelry polishing. Here are some valuable links you may find beneficial:
- A Guide to Dremel Tools on Wikipedia
- Jewelry Making Essentials on Britannica
- Online tutorials on platforms like YouTube covering advanced polishing techniques.
- Reddit communities, like /r/jewelrymaking, where enthusiasts and experts share tips and experiences.
- Local workshops or classes; many communities have resources like community colleges offering adult education classes on jewelry making and care.
Connecting with the Jewelry Community
Finding your niche in the jewelry community can significantly boost your skills and broaden your perspective. Local clubs and online forums provide a space for sharing insights and gaining feedback on your techniques. Engaging with others allows you both to learn from their experiences and to contribute your own recommendations.
Additionally, social media platforms like Facebook host groups dedicated specifically to jewelry artisans. Networking within these channels can lead to partnerships, collaborations, and, above all, a supportive environment. Even attending local jewelry fairs or trade shows can spark inspiration and motivation, not to mention the opportunity to forge lasting connections with fellow gem enthusiasts.
Building relationships with experienced jewelers could give you practical insights that you won’t find in books. Connecting with those who have traversed this path can open doors to mentorship opportunities, helping you to hone your craft even further.