Mastering Jewelers Coping Saws for Precision Crafting
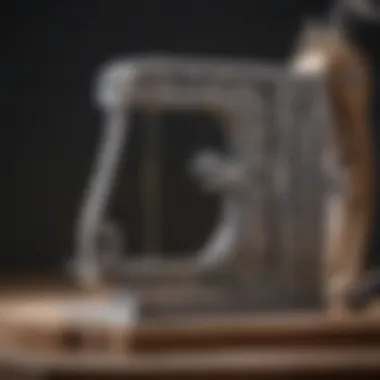
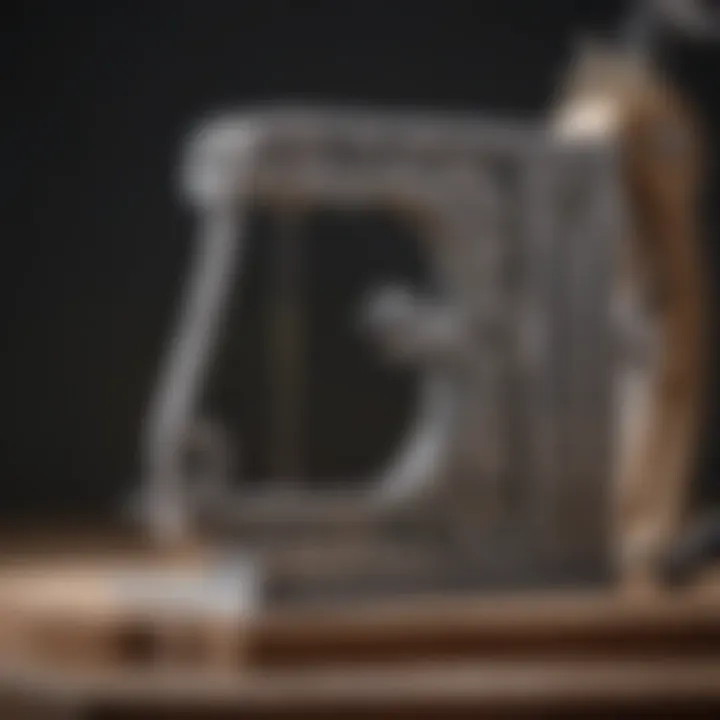
Intro
In the intricate art of jewelry making, jewelers coping saws stand out as indispensable tools for precision and creativity. Designed to cut intricate patterns and curves in various materials, these saws give jewelers remarkable control over their work. However, navigating the complexities associated with this essential tool can be daunting for both newcomers and seasoned artisans alike.
There is more to these saws than meets the eye. Their design, usage, and maintenance play pivotal roles in achieving not just aesthetic beauty in the final product, but also functionality that reflects the artisan's skills. By thoroughly understanding the intricacies of coping saws, jewelers can enhance both their craft and the quality of their creations. This article aims to delve into these central aspects while shedding light on maintenance practices, as well as advanced techniques that can elevate one's work to the next level.
Let’s embark on this journey to explore the multifaceted world of jewelers coping saws.
Types of Coping Saws
Overview of Saw Types
Despite their seemingly straightforward design, coping saws come in a few variations that suit different needs. Standard coping saws are commonly used and often made of high-carbon steel. Meanwhile, Scroll saws, while they differ in function, can serve some of the same purposes as coping saws in terms of intricate cutting.
Moreover, there are specialized coping saws customized for specific tasks, like the Fretsaw, known for its fine blade and capability to make detailed cuts.
In-Depth Look at Each Type
- Standard Coping Saw
- Scroll Saw
- Fret Saw
- Features: Wooden or plastic handle, a U-shaped frame.
- Uses: General jewelry making, cutting metals, plastics, and wood.
- Features: Electric-powered, utilizes finer blades.
- Uses: More suited for complex designs, often used in woodcraft as well.
- Features: A thinner blade, offering precision cuts.
- Uses: Ideal for delicate materials and intricate designs.
Despite the slight variations, each of these saws serves a purpose that aligns with a jeweler’s needs, ranging from basic cuts to detailed craftsmanship.
Techniques for Effective Usage
Essential Features of Coping Saws
When considering the best coping saw, look closely at features like the blade type, tension adjustment, and the frame's integrity. Each of these elements contributes to the saw’s effectiveness. For instance, a well-adjusted blade tension allows for smoother cutting while minimizing the risk of breakage during elaborate work.
Mastering the Basics of Use
Proper grip and angle are fundamental when handling these saws. A relaxed yet firm grip provides better control, which is necessary when navigating tight arcs in your design. Likewise, adjusting your working posture helps maintain balance and reduces fatigue during those longer projects.
"A craftsman must not only know his tool but also how to wield it with finesse."
Furthermore, understanding the materials you are cutting is equally essential. Different metals and plastics require varying techniques and blade configurations. Take time to understand these nuances to refine your skills and boost your confidence.
Maintenance Practices
Care Guidelines for Longevity
Treating your coping saw well ensures it remains a reliable companion in your craft. Regular checks on the blade for wear and tear can prevent mishaps and guarantee continuous progress in your projects. If the blade shows signs of dullness or damage, swapping it out as soon as possible is wise.
Storing Your Tools
Lastly, proper storage can be overlooked but is crucial. Keeping your coping saw in a dry environment, away from moisture, will help ward off rust and extend the tool's life.
In summary, coping saws are versatile tools embedded deeply in the heart of jewelry making. Mastering their use involves practical knowledge and a nuanced understanding of maintenance practices. The insights presented thus far aim to equip jewelers at any point in their journey with the means to maximize their capabilities and enhance their craft.
Understanding Jewelers Coping Saws
Understanding jewelers coping saws is really essential for anyone interested in jewelry making. This tool holds a pivotal role in crafting intricate designs. By grasping the purpose, function, and historical context of coping saws, jewelers can leverage their capabilities to create more complex and elegant pieces. Not only do these saws assist in cutting precise shapes, but they also enhance the jeweler's ability to experiment and innovate. The more one knows about their tools, the better they can wield them.
Definition and Purpose
A jewelers coping saw is a specialized hand saw designed for intricate cuts in materials like metals and wood. Mostly used in jewelry design, its thin blade and fine teeth allow for precision work that is vital for creating detailed patterns and small pieces. The blade is typically held in a U-shaped frame, which provides maneuverability while maintaining the necessary tension required to cut effectively.
In practice, jewelers use the coping saw to navigate tight curves, corners, and other shapes that standard saws can’t handle. This makes it not just a saw but an extension of the jeweler's creativity. For someone creating unique jewelry, having the right tools can make all the difference.
Historical Overview
The origin of the coping saw goes way back to the medieval period when craftsmen first required a tool that allowed for more detailed woodwork. Originally, the design was adapted from the traditional frame saw. Over the centuries, its purpose evolved, and by the 17th century, it began to be employed in metalwork as well.
The construction and use of this tool went through some changes. As metalsmithing techniques advanced, jewelers started embracing the coping saw for its versatility. During the industrial revolution, mass production led to better manufacturing processes, and the quality of coping saws improved dramatically.
"The coping saw has a rich heritage, bridging the gap between functional craftsmanship and artistic expression."
Today, the coping saw continues to hold relevance, being a staple in a jeweler's toolbox. Though technology has introduced various modern alternatives, the reliability and simplicity of the coping saw remain unmatched. Understanding its history not only enriches the craft but also offers insights into mastering its use, which is essential for anyone delving into the craft of jewelry making.
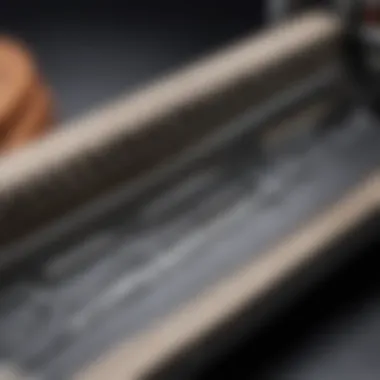
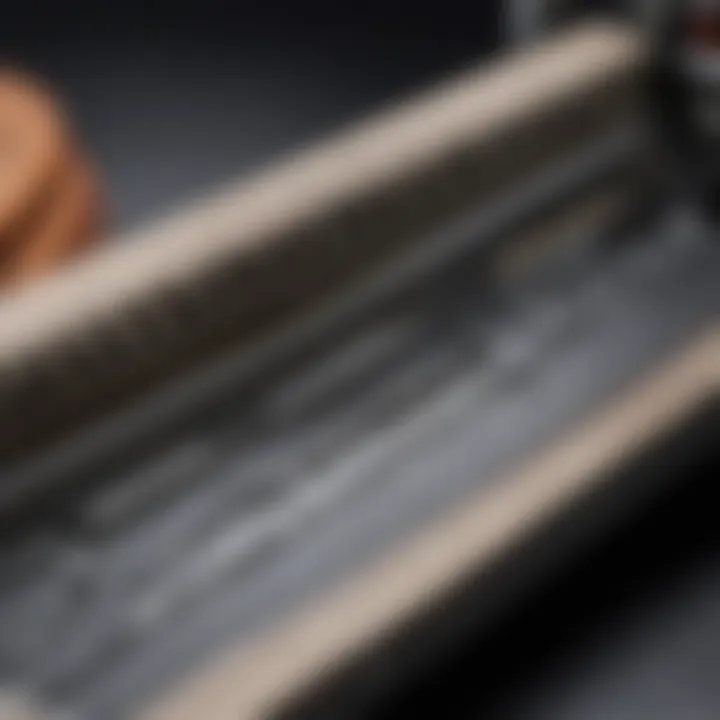
In summary, comprehending jewelers coping saws unveils a broad spectrum of applications while appreciating its historical significance. Whether someone is just starting out or has years of experience, a thorough understanding of these tools contributes to a jeweler's artistry and precision.
The Anatomy of a Coping Saw
Understanding the anatomy of a coping saw is crucial for both novice and experienced jewelers. Not only does it demystify the tool, but it also highlights the importance of each component in achieving precision and creativity in craftsmanship. Knowing how the parts work together allows artisans to optimize their techniques, enhancing the quality of the work produced. It's about grasping the mechanics and getting the most out of these intricate tools.
Components Explained
Frame
The frame of a coping saw might look simple, but its design plays a pivotal role in the overall functionality. Typically made from sturdy materials, the frame provides the necessary support to hold the blade securely. The key characteristic of the frame is its tension; an appropriately tensioned frame allows for smoother cuts and prevents blade breakage. This makes it a beneficial choice for precision tasks. A major unique feature of the frame is its shape, which resembles a bow, allowing for ease of maneuverability during tight cuts. However, one must also consider the disadvantage: not having enough tension may lead to crooked cuts, frustrating the jeweler’s intent.
Blade
The blade is the heart of the coping saw. It's engineered to cut through various materials, making it an indispensable tool for jewelers. The key characteristic of coping saw blades is their fine-toothed edge, ideal for intricate designs. This specificity makes the blade a popular choice among those looking to craft delicate pieces. The blades are also easily interchangeable, granting flexibility as different materials call for varying blade configurations. A unique feature worth mentioning is the variety in blade thickness and tooth size, which means a jeweler can tailor their choice to match their project needs precisely. On the downside, blades can fatigue and break; thus, keeping spare blades handy is advisable to avoid workflow interruptions.
Tensioning Mechanism
The tensioning mechanism is what keeps the blade taut within the frame, and this component is often overlooked. A properly functioning mechanism ensures that the blade stays straight when cutting, which is critical for accuracy. The key characteristic of this mechanism is its adjustability; most users can easily tweak it to attain the desired tension level. This adjustability is a major advantage, as it allows for versatility depending on project requirements. A unique feature here is often the quick-release function that facilitates fast blade changes. One must be cautious, however, as an overly tightened mechanism can lead to blade breakage or excess strain on the frame, impacting the longevity of the saw.
Varieties of Coping Saws
Standard Coping Saw
The standard coping saw is perhaps the most recognized in this domain. Its typical design allows for effective cutting across a broad range of materials, making it invaluable for jewelry artisans. Its key characteristic is the balance between maneuverability and control, which makes it a beneficial choice for a variety of crafting projects. Additionally, the standard version often comes with decent starter blades. The unique feature here is its affordability and availability, which makes it a favorite among beginners. One must be aware, however, of its limitations: for complex cuts, a standard coping saw may not provide the finesse that a more specialized tool offers.
Bow Saw
The bow saw, while widely used for larger scale cutting, has its applications in jewelry making too. It features a more robust frame that accommodates longer blades. The key characteristic of a bow saw is its power, best suited for thicker materials or rough-cutting tasks. While it's not the first choice for delicate jewelry work, its beneficial aspect lies in its ability to remove substantial amounts of material quickly. What sets it apart is the unique feature of its blade design that allows for both straight and curved cuts, albeit less finely than a coping saw. Jewelers should be cautious, though, as attempting intricate designs with a bow saw can lead to errors due to its bulkier nature.
Specialized Saws
Specialized saws are crafted for very particular cutting tasks. Upon examining these, you find tools designed explicitly for tasks such as intricate pattern cutting or working with fragile materials. Their key characteristic is tailored precision; they excel where standard saws might fall short. This makes specialized saws a popular choice among advanced jewelers looking to push their limits in design. The unique feature of these saws is their ability to provide unparalleled control over intricate cuts. Nonetheless, they often come with a steeper learning curve and can be costly, which can deter less experienced jewelers from utilizing them.
It's essential to choose the right coping saw for the specific crafting task at hand. Each saw has its strengths and weaknesses; knowing them leads to better creation.
Understanding these components and varieties not only enhances one’s technical skills but also encourages creativity and innovation among jewelers. Recognizing how each part contributes to the overall function reinforces the importance of the coping saw in every jewelry maker’s toolkit.
Choosing the Right Coping Saw
Selecting the right coping saw is a pivotal decision for any jeweler. This tool is not just about cutting; it shapes your entire crafting experience. Having the proper saw can greatly influence the precision of your work and the intricate designs you can achieve. Understanding the nuances involved in choosing a coping saw will lead you to make more informed decisions, enhancing both your skills and overall satisfaction with the craft.
Factors to Consider
Material Types
When it comes to the material types used in coping saws, it's essential to choose wisely. Most saws feature either steel or high-carbon blades. Steel is commonly found, due to its durability and resistance to wear. High-carbon steel, on the other hand, delivers excellent sharpness and maintains its edge longer, a crucial factor for detailed work.
One might think that cost is the only issue, but consider the strength of the material as well. For instance, a high-carbon blade is often preferred for intricate designs due to its ability to make delicate cuts. However, it can be brittle, so users must handle it with care. With steel blades, you gain better flexibility, but they might require more frequent sharpening. Therefore, understanding these materials lays the foundation for effective usage in jewelers coping saws.
Blade Size
Blade size is another critical aspect to take into account. Coping saw blades typically range from 3 inches to 10 inches in length. The size you choose influences not only the depth of your cuts but also the curves you can navigate. Shorter blades tend to be more flexible, allowing for tighter curves, while longer blades can handle broader strokes.
A key characteristic to note is that blades with a smaller tooth count are more suitable for thicker materials, giving you that extra leverage. However, they may not be as efficient for fine details. Hence, being aware of these size related details goes a long way in customizing your tool for your specific needs.
Ergonomics
Ergonomics relates to how comfortably you can use a coping saw. If your hands are cramping after a few cuts, productivity can plummet. Many saws come with rubber grips or contoured handles designed to fit snugly in your palm, minimizing strain during prolonged use.
The right ergonomics will allow for steadier hands, which in turn leads to cleaner cuts, especially when your designs demand finesse. It's indeed a beneficial choice for any personalized tool setup as it blends comfort with functionality. However, be cautious, as overly bulky handles can throw off your grip and create imbalance, thereby affecting the overall cutting experience.
Brands to Know
Budget-Friendly Options
For those just starting out or looking to save a few bucks, budget-friendly options abound. Brands like Stanley offer reliable coping saws that won’t break the bank.
The key here is affordability without sacrificing quality. Many of these saws are adequate for light to medium crafting needs, making them popular among hobbyists. However, the downside is that they may lack the durability required for extensive use. Thus, while they are excellent for beginners, serious crafters might outgrow them sooner than expected.
Professional Grade Equipment
In the realm of professional grade equipment, brands like Fretz and Knew Concepts shine. These tools are engineered for those who demand precision and long-term reliability. With features such as adjustable tensioning and higher-quality materials, they outperform their budget counterparts.
What sets these brands apart is their emphasis on ergonomic design and durability. While they come at a higher price point, the investment is well worth it for committed artists aiming for perfection. However, for someone just dabbling in the craft, this equipment may feel superfluous.
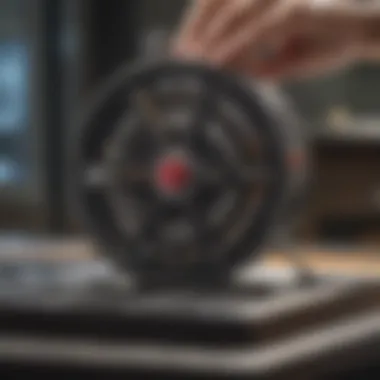
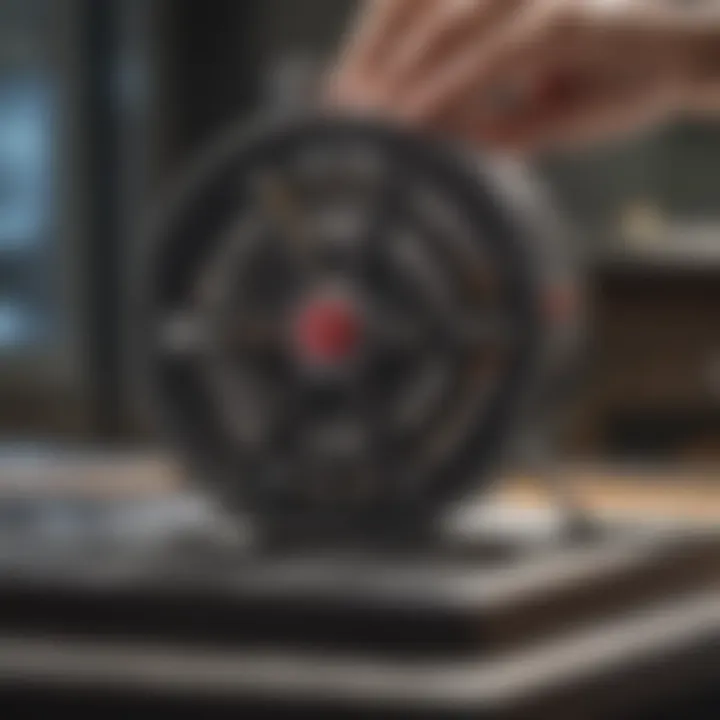
In summary, choosing the right coping saw involves understanding various factors like material types, blade sizes, and ergonomic considerations. Moreover, knowing the brands can guide you toward making wise investments that align with your crafting ambitions. Proper research will pave the road for more successful practices in jewelry design.
Techniques for Effective Usage
Understanding how to wield a copings saw effectively is crucial for any jeweler. Techniques for effective usage not only enhance precision but also protect the tool from unnecessary wear and tear. Learning the ropes involves mastering the basic cutting techniques and exploring advanced maneuvers that can make a world of difference in the finished piece. By honing these skills, jewelers can turn the seemingly straightforward act of cutting into an art form, producing intricate designs with exceptional control and finesse.
Basic Cutting Techniques
The foundation of using a coping saw begins with mastering the basic cutting technique. To start, one must position the workpiece securely. Whether it’s a soft metal or a harder material, ensure it won’t shift as you cut. It’s all about making sure the wood is stable, or else all a jeweler has is a recipe for frustration. When holding the saw, grip it comfortably with both hands, positioning your fingers properly on the frame for the least fatigue.
Making smooth, steady strokes is key here; it’s like a dance, a rhythm that emerges with practice. Instead of applying too much force, focus on letting the blade do the work. The teeth should bite the material gradually, which results in cleaner cuts. Remember, consistency is your best buddy in this stage. Once these basics are in place, a jeweler sets the stage for exploring more complex tasks.
Advanced Maneuvers
As jewelers grow more confident, they can delve into advanced maneuvers that elevate their craftsmanship. Here, precision and creativity converge to create stunning pieces.
Curve Cutting
Curve cutting is an invaluable technique in the arsenal of any skilled jeweler. The ability to create smooth curves can transform a simple design into something much more engaging. The key characteristic of curve cutting lies in its requirement for fineness and control. Often, it’s the difference between a mediocre piece and a breathtaking one. It demands patience, but the payoff is substantial: the elegance of a curvy line flowing seamlessly is quite appealing.
Unique to curve cutting is the necessity of adjusting the tension of the blade. A too-tight blade risks snapping, while one too loose leads to inaccuracies. This balance is not just technical; it is a dance of its own. One must pay close attention while navigating intricate paths, especially in materials that are prone to chipping. Yet, once mastered, it becomes a cherished tool in a jeweler’s repertoire.
Intricate Designs
Next comes the realm of intricate designs, a challenge that tests the mettle of even experienced jewelers. The charm of intricate designs lies in their complexity; they allow for profound creativity and expression. These designs often require patience and precision, as the nature of the cuts requires precision that can only be cultivated over time.
What makes these designs particularly attractive is their ability to showcase one’s unique style. Jewelers can exhibit their artistic inclinations through careful planning and execution of details. However, this art form does come with its share of pitfalls—delicate cuts can easily become a disaster if impatience sets in.
In summary, mastering cutting techniques—from basic strokes to the nuances of curve cutting and intricate designs—empowers jewelers to create with both efficiency and artistry. The journey, while demanding, is rewarding and enriches the entire jewelry-making experience.
"The true art of jewelry making lies in the ability to merge precision with creativity."
Maintenance Practices
Maintaining jewelers coping saws is crucial for ensuring their efficiency and longevity. These tools are delicate yet powerful, designed to cut through various materials with precision. Without proper care, they can wear down, resulting in subpar performance and potentially ruining intricate designs. Prioritizing maintenance not only extends the life of the coping saw but also enhances the quality of work produced by the jeweler. Think of it as polishing a gemstone; neglect leads to dulling, while proper care brings out brilliance.
Blade Replacement Tips
Replacing the blade on a coping saw is one of the most significant aspects of maintenance. The blade is subject to wear and tear, especially when used on harder materials or for intricate cuts. Recognizing when to replace a blade can make the difference between a clean cut and a messy one. Here are some tips to guide you:
- Inspect Regularly: Look for any signs of dullness or damage, such as jagged teeth or rust. A worn blade can lead to inaccurate cuts.
- Choose the Right Blade: Selecting the correct blade type for your project can enhance performance. For metal, a fine-toothed blade works best, while a thicker blade is ideal for softer materials.
- Change Blades Properly: Ensure the saw is relaxed before changing the blade. Follow the manufacturer's instructions for tightening and tensioning the new blade effectively.
- Keep Spare Blades: Having a variety of blades on hand can save time. They can be stored in a simple pouch to keep them organized and easily accessible.
"A sharp blade is half the battle won in jewelry making; never underestimate its power."
Cleaning and Storage
Cleaning and storage practices play a fundamental role in maintaining the integrity of your coping saw. After every project, it's vital to clean the blade and frame.
- Wipe Down the Blade: Remove any debris or residue that may have accumulated during use. A soft cloth dampened with water or a mild detergent works effectively without causing harm.
- Dry Thoroughly: After cleaning, ensure that the blade is completely dry to prevent rust.
- Store Properly: When not in use, store the coping saw in a dry place. Consider using a protective case or hanging it on a wall for easy access, away from moisture and direct sunlight.
- Periodic Maintenance: Every few months, check for any loose screws or fittings and tighten them as necessary to maintain stability.
Incorporating these practices not only elevates your craftsmanship but also instills a sense of pride in your tools. Caring for your coping saw sets a precedent for excellence in the art of jewelry making.
Common Pitfalls to Avoid
Navigating the realm of jewelers coping saws can be quite the undertaking. Like any skilled craft, the subtle nuances and smallest mistakes can trip up even the most seasoned of artisans. This section focuses on the common pitfalls one may encounter, sheds light on the importance of recognizing these mistakes, and ultimately suggests ways to sidestep them. Awareness of these pitfalls allows jewelers to enhance their efficiency and mastery of the coping saw, which is pivotal in achieving the intricate designs that the craft demands.
Frequent Mistakes
When it comes to using a coping saw, several frequent missteps can hinder both efficiency and the final result. Here are a few mistakes worth noting:
- Improper Tensioning: Many jewelers fail to correctly tension the blade, leading to an unstable cutting experience. A blade that is too loose can wobble, while one that is overly tight could snap.
- Poor Blade Selection: It’s easy to overlook the importance of choosing the right blade for the material at hand. Using a blade unsuitable for a specific material can lead to frustratingly slow progress or poor cuts.
- Not Following the Grain: It might seem basic, but many find themselves cutting against the grain of the material. This can snag the blade and result in jagged or uneven cuts.
- Neglecting Safety Measures: In the heat of creativity, one might forget to wear proper eye protection or stabilize the workpiece adequately. This oversight can be both dangerous and damaging.
Remember, even the simplest things can have a large impact on your craft.
Solutions and Alternatives
Navigating around these pitfalls is not just about acknowledging mistakes; it’s about finding solutions. Here are some effective approaches:
- Ensure Proper Blade Tension: Familiarize yourself with your coping saw. Practice adjusting the tension until you find the sweet spot where the blade is tight enough to prevent wobble but not so tight that it risks breaking.
- Invest in Quality Blades: It pays to examine the various blades on the market. Don’t skimp on quality; choose blades based on the specific materials you're working with. Reading reviews and getting advice from others in the field can be invaluable.
- Understand Material Grain: Take a moment to assess the grain direction of the material before cutting. Planning your cuts accordingly can save time and ensure a smooth finish.
- Prioritize Safety: Always wear appropriate safety gear such as goggles, and consistently ensure that the workpiece is secure. This will help in creating a controlled and safe working environment, allowing you to focus on your craft rather than potential mishaps.
By being mindful of these common traps and embracing the suggested solutions, jewelers can refine their skills and ultimately enhance their overall experience with coping saws. It's all about finding what works best to keep the momentum going forward.
Applications in Jewelry Making
Understanding how jewelers coping saws fit within the broader realm of jewelry making is crucial. These versatile tools not only shape intricate designs but also lay the groundwork for crafting pieces that speak to both artistry and functionality. The ability to navigate complex cuts and fine details contributes significantly to a jewelry maker's toolkit, allowing them to transform a simple idea into a breathtaking reality.
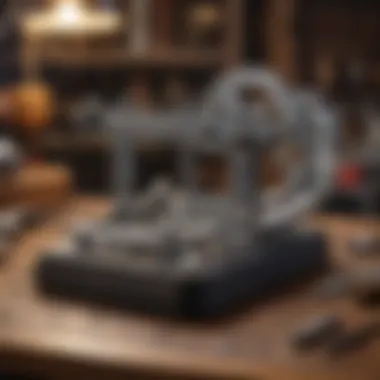
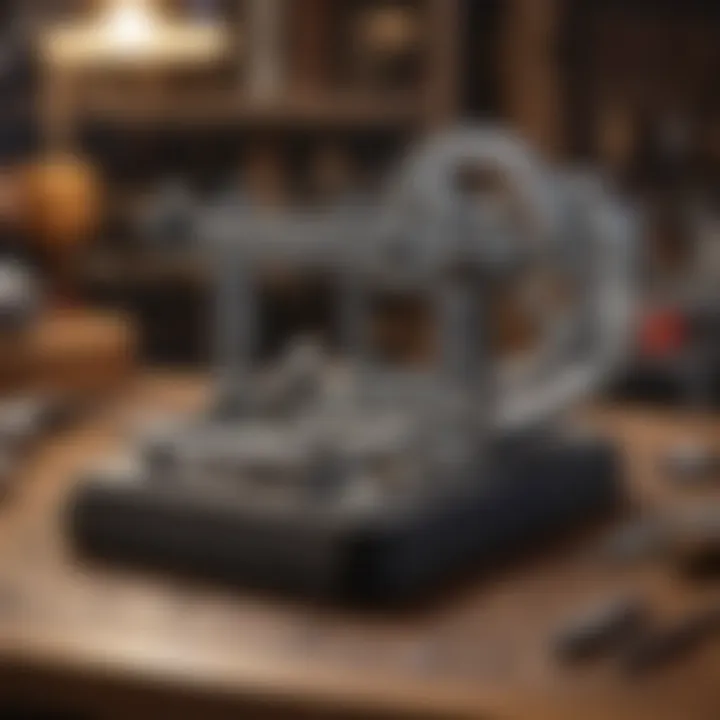
Creating Intricate Designs
Creating intricate designs can often feel like balancing on a tightrope between precision and creativity. When working with materials such as metal or wood for jewelry, jewelers coping saws come in handy. These saws allow artisans to make delicate cuts that other tools simply can't achieve. For instance, consider a jeweler who wants to make a pendant that features a unique filigree pattern. A coping saw's fine blade enables them to navigate tight curves and detailed work, ensuring that the finished piece reflects their vision without compromising on quality.
The art lies not only in the design but also in how well the cuts correspond to the envisioned piece. Having the right saws on hand can make or break a creation. Jewelers frequently experiment with different techniques, using the coping saw for both straightforward shapes and super intricate designs. The flexibility of adjusting the blade tension allows for various cutting styles, accommodating both beginners and seasoned pros.
"Precision is the foundation of exceptional jewelry making; with the coping saw, the possibilities are endless."
Integration with Other Tools
The beauty of jewelery making often unfolds where different tools intersect. Jewelers coping saws don’t work in isolation; they harmonize with a plethora of other tools, enhancing both the work process and outcomes.
For instance, after utilizing a coping saw to cut out intricate patterns, a jeweler might switch to a file to smooth the edges. This combination transforms a rough cut into a polished finish. The transition from one tool to another is not just practical, but it reflects a holistic approach to craftsmanship. Knowing how to seamlessly integrate these tools emphasizes a jeweler's skill level.
- Pairing Saw with Files:
- Collaboration with Power Tools:
- Smoothing the edges after cutting
- Creating varied textures
- Using dremel tools for detailed engravings
- Employing polishing machines for a superior finish
Integrating a coping saw with such tools is about understanding how each piece fits into the creation cycle. This interconnectedness ultimately leads to efficient workflow, ensuring that each element of the final piece is meticulously crafted. Whether it's cutting, shaping, or finishing, a jewelers coping saw is a vital part of this tapestry, weaving together the many threads of a successful jewelry-making venture.
Innovative Uses Beyond Jewelry
The realm of jewelers coping saws extends far beyond just crafting exquisite jewelry pieces. This section aims to shed light on the innovative uses outside the jewelry domain, offering insights into how this versatile tool can inspire diverse crafting possibilities. The ability to adapt and apply coping saw techniques across various crafts not only enhances skillsets but also fosters creativity.
Applications in Other Crafts
Coping saws can be a game-changer in numerous craft circles. Their precision and ability to navigate tight corners make them a prized tool in woodworking, model-making, and other artistic endeavors.
- Woodworking
Using a coping saw allows artisans to make intricate cuts, such as joinery in furniture or decorative patterns on wooden surfaces. The thin blade and fine teeth ensure clean cuts without splintering—a major consideration when working with fine wood. - Model-Making
Whether creating scale models of buildings or intricate train sets, a coping saw provides the needed control to carve out detailed features. This can be especially beneficial in hobbyist circles, where precision can make all the difference between a mediocre model and a masterpiece. - Crafting with Plastics and Composites
With the rise of plastic-based products, jewelers coping saws can easily handle materials such as acrylic sheets or thin composite panels. They allow for designing custom pieces that might just fit into a broader creative project.
These examples illustrate the versatility of a coping saw. By embracing its application in different crafts, one opens a treasure chest of creative possibilities.
Educational Uses
Beyond practical crafting applications, the coping saw has significant utility in educational settings as well. Understanding and mastering the use of a coping saw can greatly enhance the learning process in various subjects, including art, physics, and even geometry.
- Art Education
In an art classroom, having students engage with tools like the coping saw can promote hands-on learning. Projects involving cutting shapes or constructing models help nurture a sense of three-dimensional design and improve fine motor skills. - Physics Classes
Demonstrating concepts like tension and force application through the use of a coping saw can create a practical learning experience. Students can physically observe how the tensioning mechanism of the saw impacts its cutting ability and overall efficiency. - Geometry Workshops
Learning about angles, shapes, and dimensions can become tangible through the use of a coping saw. When students create geometric shapes and understand how they fit together, they gain a deeper appreciation of geometry beyond theoretical frameworks.
By integrating coping saws into educational curriculums, institutions can inspire a generation of crafters and thinkers.
"Tools like the coping saw not only serve functional purposes but also ignite learning and creativity across disciplines."
Future Trends in Tool Design
The landscape of tool design for jewelry making is evolving, particularly regarding coping saws. As artisans seek to balance functionality and creativity, understanding future trends is essential. This section explores the innovations in materials and technology influencing the design and efficiency of coping saws. Such insights not only enhance the user experience but also redefine standards in craftsmanship.
Advancements in Materials
In recent years, the materials used in crafting coping saws have seen significant improvements. Traditional saws often relied on steel, which, while durable, could sometimes lead to fatigue during extended use. Today, manufacturers are experimenting with lighter, more robust materials such as carbon fiber and advanced alloys. These innovations lead to several benefits:
- Reduced Weight: Lighter materials minimize hand fatigue, allowing for longer working periods without compromising comfort.
- Increased Durability: Modern alloys resist bending and breaking better than older options, ensuring longevity.
- Enhanced Flexibility: New composites allow for better tension capabilities, catering to intricate designs with precision.
As a result, jewelers can expect faster, cleaner cuts with tools that are easier to handle and maintain.
Technological Integration
The rise of technology in the crafting world is particularly noticeable in the arena of coping saws. Tools that were once primarily manual are now benefiting from advancements in robotics and smart technology. Consider how these integrations can redefine the crafting process:
- Smart Features: Some modern saws are now equipped with sensors to provide feedback on cutting depth and angle. This directs the user in making more informed decisions while working.
- Electric Coping Saws: These saws bring efficiency into the equation. They can handle intricate cuts with better accuracy and speed, reducing the time needed for manual control.
- Software Integration: Certain brands are starting to develop software assisting in design planning. Users can visualize intricate patterns digitally before commencing with physical materials, greatly reducing the margin for error.
"The future of tool design isn't just about improvement—it's about reimagining how we connect with the art of craftsmanship."
As technology continues to grow, it engages more artisans, opening doors to creative capabilities that have previously been unimaginable. Going forward, it's essential for jewelers to stay attuned to these advancements to maintain a competitive edge in the craft.
Understanding these trends not only prepares jewelers for the future but enhances their workflow today. Keeping abreast of these developments can lead to a powerful skill set, making for a more creative, efficient, and enjoyable process in jewelry making.
The End
In wrapping up our exploration of jewelers coping saws, it’s essential to recognize the profound impact these tools have on the craft of jewelry making. Not only do they enable craftsmen to transform raw materials into intricate, delicate designs, but they also serve as instruments that can enhance creativity and precision. The ability to navigate the complexities of a coping saw opens up a world of possibilities for both novices and seasoned artisans alike.
Summary of Key Points
- Definition and Purpose: A coping saw is vital for achieving intricate cuts, essential in jewelry making.
- Anatomy Understanding: Getting familiar with the components like the frame, blade, and tensioning mechanism is crucial.
- Usage Techniques: Mastering basic and advanced techniques can significantly improve your cutting efficiency.
- Maintenance: Knowing when to replace the blade and proper storage can extend the life of your saw.
- Common Missteps: Being aware of potential pitfalls can help avert frustration during your projects.
- Applications: Beyond jewelry, the coping saw stands as a revered tool in various crafting scenarios, broadening its utility.
- Future Trends: The integration of advanced materials and technology is on the horizon, potentially enhancing performance further.
Encouragement for Continued Learning
The journey into the world of jewelers coping saws doesn’t have to end here. Engaging with communities on platforms like Reddit or dedicated forums can provide ongoing learning opportunities and forums for sharing tips and tricks.
Delve deeper into the craft by attending workshops or joining local artisans' groups. This not only enhances your skills but also fosters connections with fellow enthusiasts. Remember, the more you practice, the more intuitive your technique becomes. Embrace the learning process, and don't hesitate to experiment with new techniques and styles. Each cut you make will teach you something valuable. So, keep that saw handy and continue to explore your creative potential!