Key Materials and Techniques for Mold Making
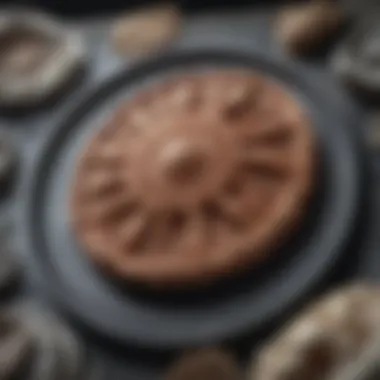
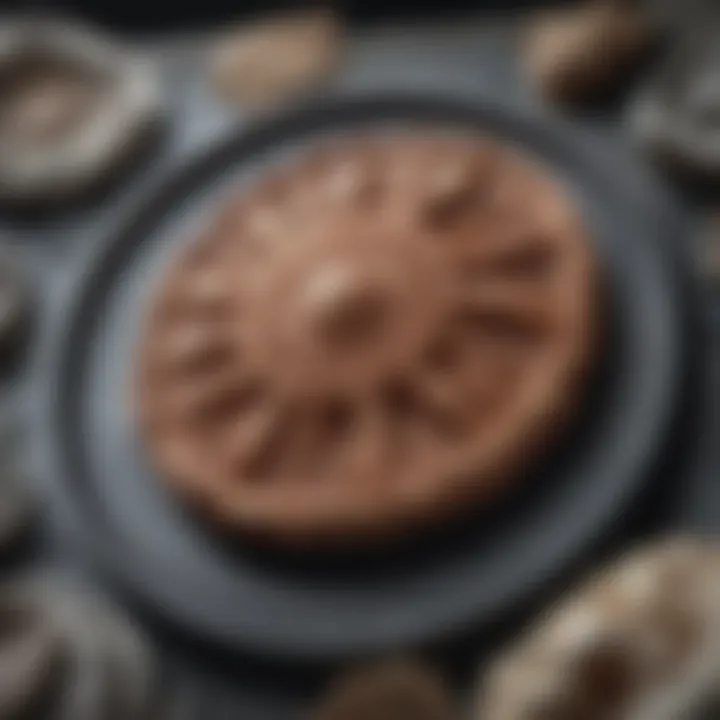
Intro
Mold-making can often feel like a mystery wrapped in a riddle. Yet, at its core, it's all about understanding the essential components that bring molds to life. Whether you're just dipping your toes into this fascinating craft or you have a bit of experience under your belt, knowing the fundamentals will set a strong foundation for your mold-making journey.
This article will guide you through the various techniques, materials, and steps involved, ensuring you have both the knowledge and confidence to create molds that meet your expectations. From the dynamics of materials like silicone and resin to the relevance of accurate measurements and environmental factors, covering this topic comprehensively promises to enhance your skills.
Types of Molds
The world of mold-making offers a variety of mold types, each suited for different applications. Understanding these types is vital for selecting the right approach for your project. Here we break down the main categories of molds.
Overview of Mold Categories
Molds can generally be classified into a few key categories:
- Open Molds: Typically two-dimensional, open molds are used for creating flat surfaces or shallow objects.
- Closed Molds: Also known as two-part molds, these are great for more complex shapes and allow for better detail and durability.
- Flexible Molds: Often made from silicone, these are incredibly versatile and allow for easy demolding, making them great for intricate designs.
- Rigid Molds: Usually made from plaster or resin, these molds provide stability, but can be tricky to remove the final product.
In-Depth Look at Each Category
- Open Molds
- Closed Molds
- Flexible Molds
- Rigid Molds
- Use these when the object does not require any undercut.
- They are easy to make and generally cheaper.
- These molds can capture complex shapes by using a two-part approach, enhancing the detail captured in the final piece.
- A common material for closed molds is fiberglass.
- Silicone is a favorite here. Its flexibility allows for intricate designs without damaging the mold when releasing the final product.
- They are particularly good for casting resins or low-temp metal.
- Best for large castings or when a more stable form is necessary. Examples include plaster molds for ceramics.
- However, care must be taken as the rigid nature can complicate the demolding process.
Techniques and Tools for Mold Creation
The journey of crafting molds demands not only quality materials but also the right techniques and tools to elevate your project from the ordinary to the extraordinary.
Essential tools to have on hand include:
- Mixing cups: For combining different materials.
- Spatulas: Useful for smoothing and leveling your mixtures.
- Scale: Accuracy in measurements can’t be stressed enough.
- Release agent: To ensure easy removal of the final product from the mold.
Each tool has its unique function, but together, they create a seamless workflow that advances the creation process.
"Success in mold-making is less about the materials and more about mastering the foundational techniques."
Understanding Molds
Molds serve as pivotal instruments in both creative and industrial domains, allowing a variety of materials to be shaped with precision. Understanding molds not only illuminates the foundational aspects of the mold-making process but also empowers creators to select the right type tailored for their projects. This knowledge streamlines the process, minimizing errors, and maximizing the potential for success, wether the end goal is intricate artistry or mass production.
Definition and Purpose
At its core, a mold is a hollow cavity designed to give shape to a fluid or pliable material, enabling it to solidify into a specific form. The purpose goes beyond mere aesthetics; a mold allows for precise replication and a broad spectrum of applications. Whether it’s a delicate sculpture or robust industrial component, the mold defines the outcome of the material poured into it.
Common Applications of Molds
Molds find their use in a plethora of fields, including art, industry, and the culinary world. Each sphere showcases molds' versatility and significance.
Artistic Projects
Artistic projects highlight the creative freedom molds provide. Artists can craft unique shapes and textures, making it a favored choice for sculpting with various materials like resin and clay. One of the key characteristics is flexibility; artists can utilize silicone molds, which allow for intricate designs and are easy to manipulate. Additionally, these molds can be used repeatedly without degrading, proving their worth in the long run.
- However, a unique feature to consider is the potential cost. Quality silicone molds can be pricey upfront, but investing in durable molds pays off through numerous applications.
Industrial Uses
In industrial contexts, molds are essential for producing components in a systematic and efficient manner. They allow for the mass production of identical parts, crucial in manufacturing sectors like automotive and electronics. One of the defining traits is their robustness; metal molds, for example, withstand high pressure and temperatures, making them ideal for heavy-duty production.
- A significant advantage here is the speed of production; once a mold is made, products can be churned out en masse with minimal labor. However, the initial setup costs may be steep, necessitating careful budgeting and planning.
Food Industry
The food industry also benefits from molds, particularly in creating visually appealing products. Chocolate molds, for example, enable confectioners to produce intricate shapes that enhance the appeal of their treats. One notable characteristic is their wide variety of materials, from simple silicone molds for home bakers to sophisticated, food-grade plastics used in commercial settings.
- An intriguing feature of food molds is their adaptability to different temperatures and environments. They can be used for baking, freezing, or even crafting gourmet treats. Nonetheless, it's crucial to ensure that molds are specifically designed for food use; non-food-grade materials can pose health risks.
Molds are not just tools; they are gateways to unleashing creativity and efficiency across diverse industries.
In summary, understanding molds reveals their multifaceted nature. Each application sheds light on the specific benefits and characteristics molds bring, accentuating their importance in various fields. This knowledge arms creators and manufacturers with the ability to make informed choices, paving the way for successful projects.
Types of Molds
Understanding the various types of molds lays a solid foundation for successful creation. Each type has its own nuances, suitable applications, and unique benefits. The right choice can greatly influence the end product's quality and the user's experience. Here, we take a closer look at four primary types: silicone, plaster, plastic, and metal molds.
Silicone Molds
Flexible Nature
The flexible nature of silicone molds sets them apart in the mold-making world. They can easily bend and twist, which allows for complex shapes and intricate details to be achieved without damaging the mold itself. Unlike rigid molds, silicone molds can release castings without effort, thanks to that flexibility.
Their adaptability makes them a favored choice for many creators. Because it can conform to the finer details of the object being molded, silicone is excellent for detailed artistic projects as well as functional items. However, it can be subject to wear and tear over time, particularly if the molds are used for high-heat applications.
Durability Characteristics
Durability is another standout feature of silicone molds. They withstand various processes, including repeated casting and exposure to different materials. When you brighten the durability factor in mold making, it assures that your investment lasts through many projects without losing shape or functionality.
This material can handle rough usage cases better than other types, making it popular among professionals and hobbyists alike.
However, these molds can be sensitive to harsh chemicals, which might degrade the silicone over an extended period, making it essential to handle them with care.
Usage Scenarios
Silicone molds serve multiple scenarios—from culinary endeavors to intricate artistic pursuits. In the kitchen, for example, they can be used for baking or creating unique chocolate shapes. Meanwhile, artisans often utilize them to reproduce detailed sculptures or craft jewelry.
The unique flexibility and heat resistance expand their realm of application. Nevertheless, they might not be the best choice for high-volume industrial applications due to time constraints in making multiple silicone molds quickly.
Plaster Molds
Cost-Effectiveness
Plaster molds are a wallet-friendly option for those just stepping into mold making. One of the key characteristics is that plaster is inexpensive and readily available. Crafting molds from plaster allows for quick projects without putting a significant dent in the budget.
This affordability makes plaster a go-to choice for educational purposes or simple DIY projects. However, the cost-effectiveness comes at a price—these molds tend to wear out much faster than silica or plastic options, especially when dealing with liquid casts.
Ease of Use
There's no denying that plaster molds are often regarded for their ease of use. Mixing plaster typically requires minimal tools and preparation, making it accessible even for those new to the craft. Pouring plaster into a mold can be a simple and straightforward task. Just mix, pour, and let it set; so, it's hard to go wrong here.
However, beginners must be cautious of their curing time because if they miss the correct window, it could result in poor-quality molds or pieces that simply do not hold.
Limitations
Yet, plaster molds do come with limitations. Once set, they are relatively fragile and can break easily, especially if dropped or mishandled. Additionally, they are unsuitable for high-detail projects due to their limited flexibility and detail-capturing capabilities. Using plaster molds for intricate designs may not yield the desired results, often leading to disappointment.
Plastic Molds
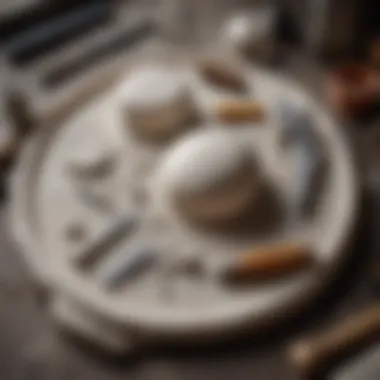
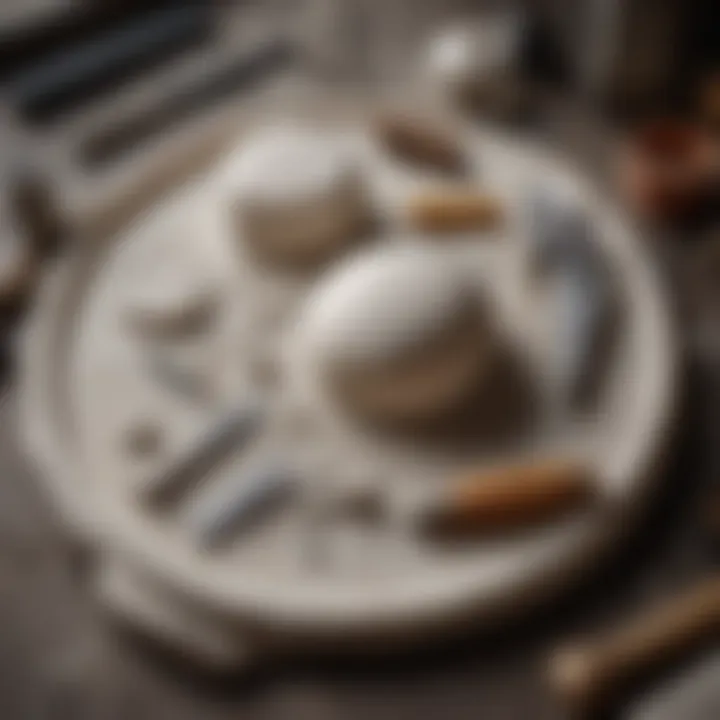
Reusability
Reusability stands out as one of the biggest advantages of plastic molds. These molds are designed for multiple usages, which significantly minimizes long-term material costs. Unlike plaster molds, which may crumble after a few uses, high-quality plastic molds can endure many production runs.
This factor greatly benefits both hobbyists and professionals working on many projects as they don’t need to create new molds each time, which saves time as well as money.
Types of Plastics Used
The choice of plastics used in molds is varied, including options like polycarbonate, polypropylene, and ABS. Each type presents differing qualities; for example, polycarbonate offers superior clarity, making it ideal for projects requiring visibility during the casting process. Opting for the right plastic enhances the mold’s performance based on the intended use.
However, it is vital to acknowledge that not all plastics handle the same casting materials effectively—something that can lead to complications if not thought through.
Applications in Industry
Plastic molds find themselves in numerous industrial applications, particularly because of their versatility. They’re frequently utilized in manufacturing processes such as automotive parts, electronics housings, and even consumer products. In addition, they are easy to clean and maintain in fast-paced production environments.
Still, one must factor in the setup time for creating these molds, as well as any potential limitations related to temperature sensitivity.
Metal Molds
Strength and Longevity
One of the key attributes of metal molds is their strength and longevity. If you are seeking consistency and durability in a mold, metal often takes the cake. They can handle very high-temperature applications, making them suitable for producing bakery goods or metal castings. Metal molds are designed to withstand wear and tear over time, which, in lengthy production runs, equates to lower overall costs in the long run.
Yet, the heaviness of these molds can make handling them a bit cumbersome, plus they are not as user-friendly as plastic or silicone molds, particularly for beginners.
Manufacturing Process
The manufacturing process for metal molds can be intricate and often requires specialized machinery. This precision in the process means you can create highly accurate and durable molds that replicate the original object nearly perfectly.
Additionally, the longevity of these molds usually justifies the upfront investment.
However, this elevated manufacturing requirement can lead to budget constraints if not considered carefully.
Unique Considerations
While metal molds offer clear advantages, unique considerations must be kept in mind. For instance, you’ll need to think about how these molds might thermal expand or contract based on temperature changes. Depending on the metal type and process capabilities, the mold can exhibit different cooling times, which impacts productivity and overall efficiency.
Selecting the right type of metal for specific applications is also critical—making it essential to have adequate knowledge before venturing forth.
Understanding different types of molds assists creators in selecting the perfect material for their specific needs, whether for industrial purposes or DIY art projects.
Materials Required for Mold Making
When it comes to mold-making, understanding the materials used is absolutely crucial. The right materials can not only streamline the process but also ensure a high-quality outcome. Whether you're embarking on a creative endeavor or a practical project, a solid grasp of the fundamental materials is essential. This section will break down the primary materials used in mold-making along with the supporting elements that enhance performance and efficiency.
Primary Material Choices
Silicone
Silicone stands as a cornerstone in the realm of mold-making due to its flexibility. Its ability to endure extreme temperatures is impressive, enabling it to withstand both hot and cold casting processes without degrading. This makes silicone molds durable and able to hold intricate details flawlessly, preserving every nuance of the original object.
- Key Characteristic: Flexibility and durability. Silicone is exceptionally pliable, allowing for easy demolding. Its resilience prevents it from cracking or breaking, which could be a significant drawback with other materials.
- Unique Feature: Wide range of applications. Whether you're casting edible items or intricate art pieces, silicone molds can cater to diverse projects.
- Advantages and Disadvantages: While silicone comes with a higher initial cost compared to other materials, its longevity and reuse potential often justify the investment. One might find it challenging to work with certain silicone types without prior experience, which could deter some novices.
Latex
Latex provides an economical option for mold-making, especially for those who are just getting started. Its inherent stretchability enables a smooth release of cast pieces. Though not as robust as silicone, it still serves a purpose, particularly in educational settings and art classes.
- Key Characteristic: Cost-effectiveness. Latex molds are generally cheaper to produce, making them accessible for hobbyists and individuals on a budget.
- Unique Feature: Easy to work with. The application of latex is relatively straightforward, often requiring minimal tools or special techniques.
- Advantages and Disadvantages: However, latex molds can have a shorter lifespan, especially when subjected to extensive use or heat. They are not suitable for hot processes and can deteriorate over time.
Polyurethane
Polyurethane molds offer a unique blend of durability and detailed precision. They are particularly favored for projects that require a high level of detail, making them ideal for industrial design or intricate artistic creations.
- Key Characteristic: Strength and precision. Polyurethane can hold intricate shapes remarkably well. It captures every detail from the original piece, providing a high-quality replica.
- Unique Feature: Versatile hardness options. Polyurethane comes in a range of hardness levels, allowing users to select the perfect balance for their specific project needs.
- Advantages and Disadvantages: While they can be more expensive than latex alternatives, the investment typically pays off in the results. However, they may require more expertise in mixing and application, which could pose challenges for beginners.
Supporting Materials
Supporting materials serve as the backbone of the mold-making process. They help ensure that the primary materials function as intended, enhancing overall efficiency and effectiveness.
Release Agents
Release agents play a pivotal role in demolding processes. They create a barrier between the mold material and the cast, preventing adhesion and facilitating a smooth removal.
- Key Characteristic: Ease of demolding. Utilizing a release agent significantly reduces the risk of damaging your mold during removal.
- Unique Feature: Variety of applications. From spray-on solutions to paste forms, there are many options available to suit different materials and projects.
- Advantages and Disadvantages: While essential, some release agents can interfere with the surface finish of the cast, so it's crucial to choose the right type for your material. Additionally, they may need to be reapplied for more extensive projects.
Casting Resins
Casting resins are integral when creating the final product. They provide the material in which the mold will cast the desired shape.
- Key Characteristic: Versatile properties. Casting resins come in several types, including epoxy and polyester, each with unique characteristics suitable for specific applications.
- Unique Feature: High finish quality. They allow for an exceptional level of detail and polish, enhancing the overall appearance of the final piece.
- Advantages and Disadvantages: The downside is that some resins can be toxic and may require careful handling and specific safety precautions. Understanding the curing times and necessary environmental conditions is essential for accurate results.
Frameworks and Supports
Frameworks and supports provide stability during both the mold-making process and the casting process. Strong supports prevent distortion and maintain the integrity of the mold as the material cures.
- Key Characteristic: Essential for larger molds. As the size of the project increases, the need for supportive structures becomes more apparent to counteract any forces that could compromise the shape.
- Unique Feature: Customizability. Frameworks can be tailored to fit the specific dimensions and weight of the mold being created, adding to the overall quality of the resulting cast.
- Advantages and Disadvantages: While providing necessary support, frameworks can also add complexity to the setup, requiring careful planning and construction to ensure proper alignment and stability.
Grasping the right materials can mean the difference between a perfect mold and a ruined project. Each choice matters. It all adds up to either success or failure down the line.
Understanding the materials and supportive elements is crucial for mold-making professionals and enthusiasts alike. Whether you're crafting art or prototypes for a new product, the right materials can help you navigate the intricacies of mold creation effectively.
Essential Tools for Mold Making
When delving into the world of mold making, selecting the right tools can be the make-or-break factor in any project. Just like a chef's knives are integral to the culinary process, the tools used in mold creation can significantly affect the quality and precision of the final product. Having the appropriate instruments on hand not only enhances efficiency but also ensures a greater degree of accuracy and creativity. This section will explore the essential tools required for effective mold making—specifically measuring instruments, mixing tools, and application tools.
Measuring Instruments
Measuring instruments are the backbone of effective mold making. Precision is key when mixing materials and pouring them into molds, which means that having reliable instruments can make all the difference. This subsection will delve into some crucial measuring tools: scales, calipers, and templates.
Scales
Scales are indispensable for anyone engaged in mold making. They offer a high level of accuracy for measuring materials by weight. A key characteristic of scales is their ability to handle various weight capacities, which makes them a favored choice for both small and larger projects.
The unique feature of scales is the various types available, ranging from digital to analog. Digital scales usually provide a quicker way to read measurements, keeping your workflow smooth. However, they may require batteries and are vulnerable to electrical issues. Analog scales, although sometimes seen as old-fashioned, never fail to operate as long as they are properly calibrated.
Advantages of using scales include their ease of use and accuracy, but it's important to remember that any slight error in measurement can lead to significant inconsistencies in your mold.
Calipers
Calipers are another vital instrument in mold making. The specific aspect of calipers that makes them stand out is their ability to measure interior and exterior dimensions as well as depths, which is crucial for detailed projects. They help you obtain very fine measurements that can be essential, particularly when dealing with intricate molds or detailed designs.
A key characteristic of calipers is their versatility. Most calipers can measure in either millimeters or inches, catering to different preferences. This feature is beneficial because it allows a standardization of measurements across diverse projects.
Though calipers are highly accurate, they do require a careful hand, as mishandling can result in unwanted deviations in measurement. Plus, if they become worn or dirty, it can affect their reliability. Hence, regular maintenance is key.
Templates
Templates serve as a reference point that helps in ensuring consistency when creating molds. The specific aspect of templates is their capacity to provide repeatable shapes, making them useful for projects that require multiple identical pieces, such as tiles or figures.
One standout characteristic of templates is the variety of materials they can be made from, ranging from sturdy plastic to thin paper. This allows for flexibility based on project requirements.
The unique feature of templates lies in their ability to assist in layout marking before any material is mixed or poured. Still, templates can be limiting when creativity calls for unique shapes not easily represented by a pre-existing template.
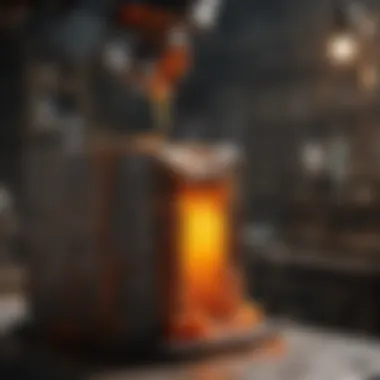
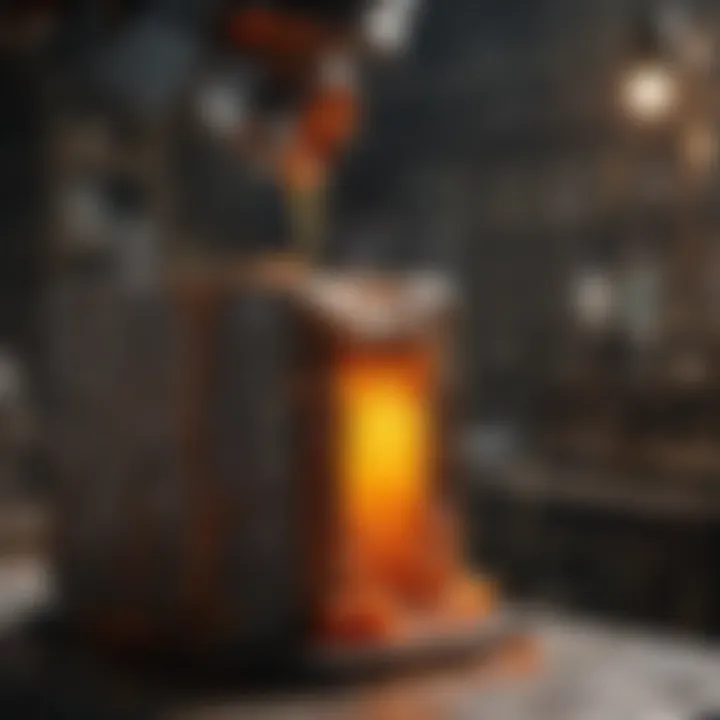
Mixing Tools
Mixing tools can often be underestimated, but they are essential for achieving the perfect combination of materials before they are poured into the molds. Let's discuss the primary types of mixing tools: mixing bowls, stirrers, and measuring cups.
Mixing Bowls
Mixing bowls are fundamental instruments in the mold-making process. They allow for the thorough mixing of materials, ensuring a homogeneous consistency. The key characteristic of mixing bowls is their ability to come in various sizes and materials, allowing you to choose the most suitable one for your specific project.
A unique feature of mixing bowls is the non-stick variants available, created specifically to help with easy material removal once the mixture has set. However, it’s crucial to select a bowl that is chemically compatible with the substances you are mixing.
Advantages of using mixing bowls include ease of handling and versatility, but if one chooses the wrong type, they may suffer from poor mixing or difficulties during clean-up.
Stirrers
Stirrers, whether made of wood, plastic, or metal, are key tools for blending the materials consistently. The specific aspect of stirrers is their ability to reach all corners of the mixing bowl, facilitating a thorough blend without leaving lumps. Their lightweight nature makes them easy to handle, contributing to a smooth mixing process.
A key characteristic is that they come in different shapes and lengths, allowing you to select the ideal stirrer based on the size of your mixing bowl and the viscosity of the mixtures involved.
Despite their benefits, a disadvantage to consider is that plastic stirrers can warp if they come into contact with high heat. Wooden stirrers may absorb some materials, affecting purity in specific applications.
Measuring Cups
Measuring cups are vital as they ensure that the right quantities of materials are combined. Their specific aspect lies in the graduated measurements printed on them, which allows precise measurement of both liquids and solids.
A key characteristic of measuring cups is their construction material—from glass to plastic to metal. This variety grants users the freedom to choose according to their mixing medium.
The unique feature of measuring cups is their transparency, particularly for those made of glass, allowing for easy visibility of the contents. However, plastic measuring cups may become discolored over time, affecting their readability. Another disadvantage is that some materials can stick to the inside, making it challenging to ensure that all material is effectively measured.
Application Tools
Once the molded material is ready and the molds have been created, application tools come into play. These help in applying the materials into the molds accurately and neatly. The three primary application tools discussed here are sponge brushes, spatulas, and pipettes.
Sponge Brushes
Sponge brushes are especially useful in mold making due to their absorption capacity and adaptability. They are great for applying even layers of material without bubbles. The specific aspect of sponge brushes that makes them valuable is their ability to reach intricate details of the mold.
The key characteristic is their soft texture, which prevents scratches on delicate surfaces. This makes them a popular tool in artistic mold projects.
However, one disadvantage might be that sponge brushes can wear out quickly if using them with thicker materials, necessitating a replacement mid-project.
Spatulas
Spatulas are essential for spreading, smoothing, and scraping materials into molds. The specific aspect of spatulas is their variety, ranging from small detail spatulas to larger, wider ones. They excel at moving and molding material into hard-to-reach areas.
A key characteristic of spatulas is their flexible blades, which allow for different angles when applying materials. This flexibility is beneficial for achieving precision during the whole process.
One downside is that certain spatulas may not be suitable for all material types, particularly if the materials are ultra-thick or sticky, which may inhibit their effectiveness.
Pipettes
Pipettes are a handy tool for adding small quantities of liquid material precisely into molds. Their specific aspect is their fine tip, which allows for controlled application avoiding spills or overflows.
The key characteristic of pipettes is their accuracy, crucial when dealing with chemical mixtures that require a careful balance. They are especially beneficial for more intricate projects where precise measurements matter.
However, pipettes can also present challenges; they're generally not suitable for greater volumes of material and can be prone to clogging if the liquid is too thick or viscous.
Choosing the right tools for mold making is crucial to achieving successful outcomes. This involves understanding the specific roles of each tool.
In summary, the essential tools for mold making encompass a range of measuring instruments, mixing tools, and application tools, each with its own unique features and advantages. Selecting the right tools not only simplifies the process of mold creation but can significantly impact the final product's quality.
Safety Considerations
Creating molds can be an exciting endeavor, but it is crucial to approach the process with due diligence regarding safety. The materials and techniques employed in mold-making can involve hazardous substances and equipment, which can pose health risks if not handled properly. By understanding and implementing safety measures, you not only protect yourself but also enhance the overall quality of your work. This section discusses key safety components that every mold maker should keep in mind.
Personal Protective Equipment
Gloves
When it comes to handling mold-making materials, gloves are an absolute must. They provide a critical barrier between your skin and potentially harmful substances. One important aspect of gloves is their chemical resistance. For example, nitrile gloves are a popular choice because they offer protection against various chemicals while remaining flexible and tactile. This means you can handle intricate mold details without sacrificing safety.
However, it's essential to note that not all gloves are created equal. Some may be thin and prone to puncture, which compromises their effectiveness. Always select gloves suited for specific tasks—thicker gloves for resin work and thinner ones for silicone, for instance. Remember, if your gloves get damaged, replace them promptly to maintain that essential layer of protection.
Face Masks
Face masks are another critical piece of personal protective equipment. The fumes produced during the mixing and curing of certain materials can be quite toxic. Wearing a mask shields your respiratory system from these harmful vapors. Key characteristics of effective face masks include a snug fit and a particulate filter. N95 masks, for instance, are designed to block at least 95% of airborne particles, making them a solid choice for mold-making tasks.
One unique feature of some masks is their ability to accommodate respiratory filters for additional safety. However, the drawback is that wearing a mask for long periods can be uncomfortable, particularly in warmer environments. It's wise to take breaks to remove your mask in a safe location to avoid fatigue.
Eye Protection
Eyes are particularly vulnerable during mold creation. Eye protection, like safety goggles, is vital for shielding your eyes from splashes or chemical irritants. The key characteristic of safety goggles is their ability to provide a complete seal around the eyes, preventing materials from entering. This means you can work with assurance, knowing your vision is safe from unexpected accidents.
A unique aspect of some safety eyewear is their anti-fog properties, allowing for a clear line of sight while you work. Nonetheless, like face masks, they can become uncomfortable after extended use, necessitating occasional breaks. Consider investing in comfortable options that encourage consistent wear, which is paramount when working on detailed projects.
Ventilation Requirements
Impact on Health
Proper ventilation is essential for maintaining a safe working environment. Poor airflow can lead to a buildup of fumes and chemicals, negatively affecting health over time. One key characteristic of effective ventilation is that it helps to disperse harmful vapors, keeping air quality within acceptable limits. Inadequately ventilated areas can cause headaches, dizziness, and long-term respiratory issues.
When planning your workspace, consider whether you'll be mixing materials with strong odors. Adequate ventilation should be a priority not only for comfort but also for safety. It's a beneficial arrangement to have a fan or opening windows to promote airflow, but remember that this may not always be feasible. Always adhere to product safety guidelines regarding ventilation requirements.
Optimal Airflow
Achieving optimal airflow in your workspace requires thoughtfulness in setup. Proper airflow keeps the area fresh and reduces the risks associated with vapor exposure. Key features of an optimal setup may include strategically placed windows that facilitate cross-ventilation, as well as utilizing exhaust fans.
Without sufficient airflow, the environment can quickly become hazardous. This is especially relevant when using materials that emit volatile organic compounds (VOCs). Investing in air purifying systems can also be advantageous, providing an extra layer of safety against airborne pollutants.
Workspace Setup
The setup of your workspace plays a fundamental role in mold-making safety. Keeping it organized and clutter-free reduces the potential for accidents. A key characteristic of a safe workspace is clear demarcation of areas where materials are handled. Utilizing designated zones helps prevent cross-contamination and exposure to hazardous substances.
Consider having a well-lit environment that minimizes shadows, further enhancing safety as you work. You might even dedicate an area for mixing materials away from finished objects to avoid mishaps. By ensuring your workspace is thoughtfully designed, you not only promote safety but also encourage a more efficient and enjoyable mold-making process.
Key takeaway: Obtaining and using personal protective equipment and ensuring proper ventilation creates a safer, healthier working environment, which ultimately leads to better mold-making results.
Steps to Create a Mold
Creating a mold is not just an art; it’s a science. There are various steps that one needs to follow, and each comes with its own set of crucial considerations. This section aims to highlight the foundational elements and benefits, providing a roadmap for both amateurs and seasoned mold makers. Understanding these steps can influence the overall quality, effectiveness, and durability of the mold created.
Preparing the Object
Cleaning and Drying
Cleaning and drying the object is like laying the groundwork for a sturdy building; it sets the stage for everything that follows. This step involves removing dust, oils, or any other residues from the surface of the object. A key characteristic of effective cleaning is thoroughness. By ensuring the object is completely free from contaminants, you can avoid any imperfections in the mold. This makes cleaning a beneficial choice for mold creators.
However, some might overlook this process, thinking a quick wipe will suffice. Nevertheless, ignoring this detail can lead to defects in the final product. While drying is also crucial, leaving moisture trapped can compromise the molding material's adhesion, turning a potential masterpiece into a complete bust.
Sealing Surfaces
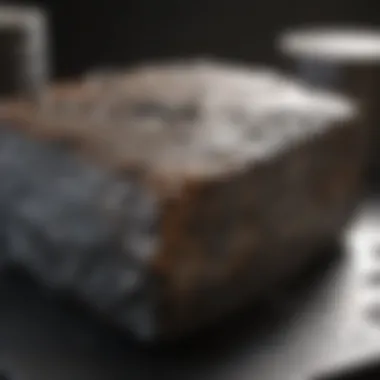
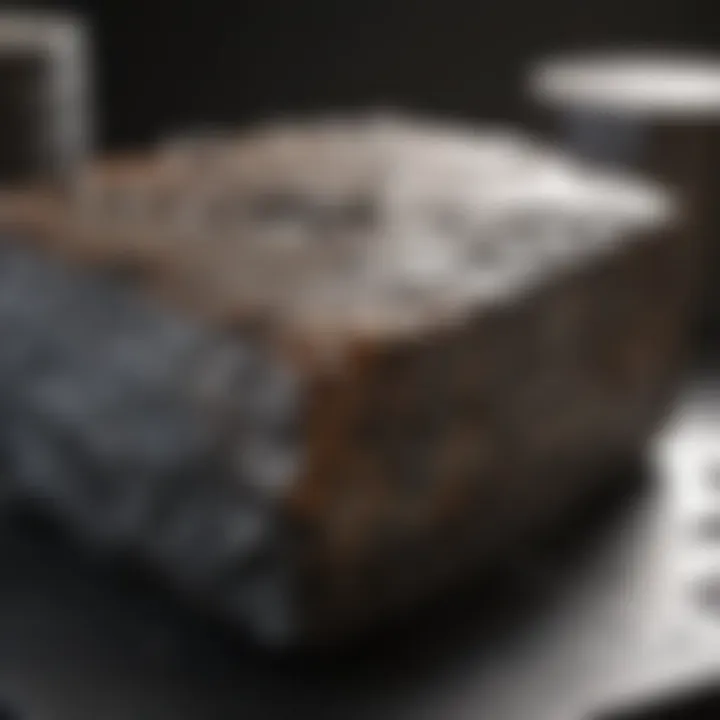
Sealing surfaces is another pivotal aspect when preparing the object. This step involves applying a suitable sealant to the object’s surface. A defining characteristic of this technique is its preventative nature. Sealing ensures that mold material doesn’t seep or cling to the object, making removal much easier later on. This is why sealing surfaces is popular in mold creation.
Nonetheless, one unique feature of sealing is the variety of materials you can choose from, allowing flexibility depending on the object and mold material used. A drawback could be that improper sealing may lead to adherence issues. So, it’s essential to choose the right sealant depending on both the object and the mold material.
Choosing the Right Mold Type
Choosing the right mold type is a decision that shapes the entire project. Different projects often demand distinct mold types, and this selection significantly influences the resulting item’s quality. A key characteristic in this choice is suitability. For instance, silicone molds are flexible and great for detailed shapes, while plaster molds might be more appropriate for simpler designs.
Having this variety allows creators to tailor their approach more precisely to the intended outcomes, making it a beneficial aspect of the mold-making process. A unique feature of this choice is its direct impact on the ease of demolding—some types of molds are inherently easier to release than others. However, one potential disadvantage is the confusion that may arise from too many choices, which can overwhelm a novice.
Mixing the Mold Material
Correct Ratios
Achieving correct ratios when mixing mold materials is as vital as baking a cake; the right balance determines the success of the final product. This aspect hinges on precision because incorrect ratios can result in weak or ineffective molds. A primary consideration is the chemical properties of the materials you utilize.
Getting the ratios wrong can cause the mold to cure improperly, leading to cracks or brittleness. Like a well-calibrated recipe, this step is beneficial in ensuring consistency and reliability in the outcome. A distinct feature here is the possibility of adjusting ratios based on the project's needs, allowing flexibility, but it can make it tricky for beginners without exact instructions.
Mixing Techniques
Mixing techniques play a significant role in ensuring that all components combine evenly. A pivotal characteristic of this step is ensuring uniformity in texture and consistency. This is a favorable choice in mold-making because a well-mixed compound will cure more evenly, resulting in a high-quality mold.
It’s beneficial to use specific tools for mixing, as they can aid in achieving a homogenous blend. That said, a unique feature of this process is that excessive mixing can introduce unwanted air bubbles, which may weaken the mold. Striking a balance is the key here.
Time Considerations
Time considerations are equally important in the mold-making process. The timing of mixing and pouring can affect the quality of the final product, especially how quickly the materials begin to set. A critical characteristic is the setting time of each material being used; knowing this is essential for successful operations.
This is beneficial because it allows for safe preparation of the working environment before the material solidifies, making the project run smoother. However, a unique challenge is the need to act swiftly once mixing begins since certain materials can cure quickly, leaving you with little time for adjustments.
Pouring and Curing
Pouring Techniques
Pouring techniques are fundamental to the success of mold creation. The manner in which the material is poured can greatly affect how well it fills the mold and sets around the object being molded. A key characteristic is to pour slowly and steadily; this minimizes the creation of air bubbles, which can cause weaknesses in the final product.
This meticulous approach to pouring makes it a favorable choice in mold-making. A unique feature here is the variety of pouring methods available, such as pouring from different heights for various effects. However, improper techniques may lead to uneven filling, which can compromise the quality of the mold.
Curing Timeframes
Curing timeframes are another essential aspect that must not be neglected. This refers to the time required for the molding material to fully set and become solid. A defining characteristic of this is the potential variation depending on the materials used.
Understanding this timeframe can ensure that you do not rush the demolding process too soon, which could lead to deformities or breakage. This is vital since a wrong move can be counterproductive. Although waiting can be frustrating, it allows for quality results that last, a unique feature that speaks to the significance of patience in mold-making.
Environmental Factors
Environmental factors are often those behind-the-scenes aspects that greatly influence the outcomes of mold creation. Temperature, humidity, and airflow all play critical roles in how mold materials cure. For example, excessive heat may cause a rapid cure, resulting in a weaker mold.
Understanding these conditions can prove beneficial for optimal curing results, ensuring that your molds set precisely as intended. This unique feature of being adaptable to various environments can be a game-changer for artists and makers. Yet, finding the right balance requires vigilance and attention to detail—straying into the extremes can hinder success.
Post-Mold Creation Techniques
After undergoing the intricate process of mold making, the steps followed for post-mold creation can significantly affect the quality and usability of the finished mold. This phase is crucial for removing the mold from the original object safely and for preparing it adequately for future applications. By understanding the proper techniques, one ensures the integrity of both the mold and the castings produced from it. Additionally, effective finishing techniques can enhance the functionality and aesthetics of the mold, making this section a vital piece in the mold making puzzle.
Demolding Process
Techniques for Safe Removal
The demolding process is a pivotal step in ensuring that both the original object and the newly created mold remain intact. Careful removal techniques are essential, primarily because mishandling at this stage can lead to damage. A popular choice in this arena is to use a gentle leverage approach, where tools are employed to ease the mold away from the object without forcing it. This method alleviates strain on both the mold and the original piece, therefore prolonging their usability.
A unique feature of using this gentle approach is that it tends to minimize issues like tearing, which can happen with more aggressive methods. While the effort may take slightly longer, the benefit of preserving detail in the mold far outweighs quicker, riskier methods.
Common Issues
Each process comes with its own set of challenges, and the demolding step is no exception. Common issues include sticking due to inadequate release agents or even miscalculations during the curing time. These factors can create significant headaches during the retrieve phase, often resulting in breakage of the mold or the original item.
These problems are of notable concern because they could render the mold unusable or jeopardize the quality of items cast from it. Using proper release agents is key, but also understanding the drying times of the mold material can alleviate many frustrations. An advantage of being aware of these common issues is that it prepares the creator to foresee potential pitfalls and act accordingly, thus ensuring a smoother post-mold experience.
Finishing Techniques
Sanding
Once the mold is successfully removed, the finishing techniques come into play, and sanding emerges as a fundamental process. Sanding helps to smooth out any imperfections left from the casting materials. This practice is fundamental for ensuring that the surfaces intended to make contact with the final product are as even and smooth as possible.
The key characteristic of sanding is its ability to refine detail, which is crucial for achieving professional-quality molds. However, one must navigate carefully; over-sanding can lead to loss of detail that is sometimes hard to reclaim. Thus, patience is crucial when engaging in this process.
Cleaning
Cleaning molds after creation is another essential step that cannot be bypassed. Residue from casting materials can build up and affect future castings if left unattended. Regular cleaning not only improves longevity but also ensures that the mold remains functional and that the next item casted won't have unwanted additives.
An important aspect of cleaning is choosing the right solvents and techniques suitable for the material of the mold. Some cleaned improperly can degrade the mold's structure, while others can enhance its durability. The unique feature here is that a good cleaning regimen can prevent contamination in future uses of the mold, thus maintaining quality control in casting.
Reinforcement Options
Reinforcement options are valuable when finishing molds, particularly when a mold is under threat of warping or breaking under stress. Different methods, such as adding fiberglass or using metal rods, can significantly enhance the strength of the mold.
The key advantage of using reinforcements is longevity; irreparable molds often stem from stress fractures, and fortifying them brings peace of mind for creators. However, care must be taken to evaluate how reinforcement could affect the casting process. Each unique method offers various strengths and weaknesses, making it an essential consideration to keep the finished product in mind.
Exploring Advanced Techniques
The significance of exploring advanced techniques in mold creation cannot be overstated. These methods not only enhance the precision of the final product but also expand the potential applications of molds in various fields. Understanding what sets advanced techniques apart allows both experienced and new mold makers to elevate their craft.
In this section, we delve into specific breakthrough methods that are making waves in today's mold-making scene. This doesn't just simply boil down to a choice of materials, it’s also about how those materials interact and perform together in innovative ways to achieve complex designs and high fidelity in reproduction. Let's look a bit closer into vacuum molding and 3D printing, and see how they stack up.
Vacuum Molding
Overview and Benefits
Vacuum molding stands out due to its capacity to create precise replicas with minimal material waste. This technique utilizes a vacuum to pull material into a mold, ensuring thorough coverage of details. The key characteristic that makes vacuum molding pop is its adaptability to various materials, including plastics and rubber compounds. This adaptability makes it a favored choice not just for high-volume production but also for intricate designs that may seem daunting through traditional methods.
Another unique feature of vacuum molding is its efficiency in both time and cost. It allows for rapid prototyping, letting you churn out test samples before committing to full-scale production. However, it's worth noting that vacuum molding does require specific equipment which might be a hurdle for hobbyists or those just dipping their toes into mold making. Still, the benefits far outweigh the limitations for many professionals.
Applications
As for applications, vacuum molding finds its home in numerous industries including automotive, aerospace, and even consumer products. The ability to produce lightweight yet durable parts is a distinct advantage in these sectors. The clarity and detail achieved through this technique are unmatched.
Furthermore, the ease of production means prototypes can be developed with shorter turnaround times, improving innovation cycles. However, a downside is that while vacuum molding works wonders for flat and slightly curved surfaces, complex geometries may present challenges, requiring skilled handling to navigate.
3D Printing and Mold Making
Integration of Technologies
3D printing has revolutionized the landscape of mold making in a fairly short time. By integrating 3D printing with traditional mold techniques, creators can achieve levels of creativity and complexities in design that previously seemed impossible. The hallmark of 3D printing lies in its ability to create molds with intricate geometries directly from a computer model, reducing the generating time significantly.
What makes this technique so appealing is the customization it allows. Designing unique molds tailored to specific needs becomes a reality rather than a distant goal. One unique aspect of this integration is the ability to use various materials, from flexible filaments to robust thermoplastics, making it a versatile choice for mold makers.
Limitations and Capabilities
Even though the technologies have great potential, they also come with limitations. One key drawback is the speed compared to traditional methods when scaling production; 3D printing often falls behind in efficiency. Moreover, while the initial investment for a good 3D printer can be steep, this could be a limiting factor for many small-time mold makers.
On the flip side, the capability of 3D printing allows for rapid iteration on designs. Mistakes can be corrected on the fly with adjustments made to digital files rather than physical models, which is a game changer in the mold-making process. In summary, while there are both strengths and weaknesses to consider, the integration of 3D printing into mold making is likely to continue growing, changing the future of how materials are shaped and utilized.
"Choosing the right technique in mold-making is essential. It's not just about picking one and forgetting about it; every project may call for something different. Be adaptable."
In the ever-evolving world of mold making, integrating advanced techniques like vacuum molding and 3D printing reflects a commitment to efficiency, creativity, and precision. As technologies develop and diversify, molding enthusiasts and professionals alike must stay abreast of these innovations to optimize their techniques and produce outstanding results.