Exploring Gold Smelting Flux Formulas and Their Impact
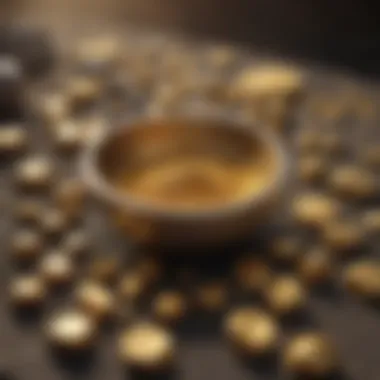
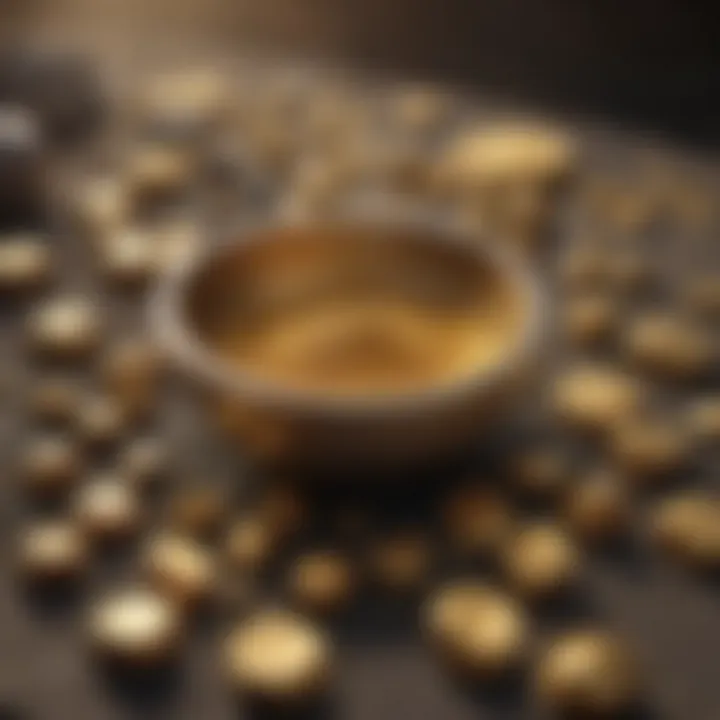
Intro
Smelting gold is a captivating process that merges ancient techniques with modern chemistry. At the heart of this fascinating craft are flux formulas, the unsung heroes that make gold recovery feasible and effective. Anyone who’s ventured into this intricate world knows that the quality of flux can dramatically influence not only the yield of gold recovered but also its purity. This article aims to dissect the various gold smelting flux formulas, breaking them down into their chemical compositions and discussing their different roles in the recovery process.
The importance of understanding flux materials cannot be overstated. Gold smelting is hardly as simple as melting the metal; it is more akin to a chemist’s ballet where each element plays a critical role. In this symphony, flux serves to lower the melting point of ores, helping to separate impurities from the precious metal, thereby making the extraction of gold more efficient.
This exploration is tailored for rock and fossil collectors who are keen to deepen their knowledge in this specialized area. Whether you’re a seasoned smelter requiring a refresher or a novice looking to enter the field, understanding flux’s chemistry and practical applications can redefine your approach to gold recovery.
We will examine the different types of fluxes available, the science behind their formulations, and the meticulous safety protocols necessary for engaging in smelting practices. As we traverse through the realms of gold recovery, we will illuminate key considerations that impact the final output of your endeavors. Let's dive into the intricate world of gold smelting flux formulas.
Preamble to Gold Smelting
The art of gold smelting holds a prominent place in the journey from raw ore to refined metal. This process not only allows for the extraction of gold but also plays a critical role in determining the quality and purity of the final product. For collectors and enthusiasts, understanding the ins and outs of gold smelting helps uncover the full potential of their raw materials, which can vary greatly in composition and purity. In this article, we delve into the fundamental concepts surrounding gold smelting flux formulas, shedding light on their composition, application, and impact on gold recovery.
Definition and Purpose
Gold smelting can be defined as the process whereby gold is extracted from its ore through heating and melting, using specific flux materials to facilitate this action. The primary purpose of flux in gold smelting is two-fold: it assists in separating the desired metals from unwanted impurities and enhances the efficiency of the smelting process itself.
Flux acts like a guardian against impurities, allowing only the noble metals to shine in the final product. Common materials used as flux include borax, soda ash, and silica, among others. This blend not only helps in fusing the metals but also lowers the melting point, making the process more energy-efficient.
Taking a closer look at the formulation of these flux materials is essential for anyone involved in the gold recovery process. The right mix can make all the difference between a heap of useless rock and a valuable yield.
Historical Context
Gold smelting isn't a modern marvel; its roots stretch back thousands of years. Early civilizations like the Egyptians and Romans employed rudimentary methods of extraction that laid the groundwork for today's advanced techniques. The art was as much alchemy as it was chemistry. These ancient smelters utilized fire and primitive fluxes such as wood ash and crushed limestone to purify their gold.
As knowledge spread through cultures and time, so did techniques. Fast-forward to the Middle Ages, when advancements in furnace design and the understanding of chemistry opened new doors. Miners in Europe adopted the use of lead-based fluxes to improve gold yields from complex ores. This laid the foundation for the principles and practices that still drive modern gold smelting today.
Throughout history, smelting has evolved, yet its core principles remain unchanged. With each discovery, the techniques became more efficient, and methods more sophisticated. Today, gold recovery is a precise science, deeply woven into the fabric of both economies and artistry, reflecting how far we've come from those early days of trial and error.
Understanding Flux in Smelting
Understanding flux in smelting is crucial for anyone involved in gold recovery. Flux plays a pivotal role, acting as the intermediary that facilitates the separation of gold from impurities and helps in maximizing recovery yield. This section sheds light on what exactly flux entails and how it influences the gold smelting process.
What is Flux?
Flux refers to a variety of materials used in smelting that help to lower the melting point of ores, making it easier to extract metals like gold. Its fundamental purpose is to bind with unwanted materials—often termed as gangue—present in ores so they can be easily removed from the final product. Several common flux components can be found in many formulations. For instance:
- Borax: This is well-known in the smelting community for its ability to dissolve silica and other impurities.
- Soda Ash: Also referred to as sodium carbonate, this acts as a fluxing agent that helps in lowering the melting point further.
- Silica: Ground quartz is often used to help form a glassy layer that can encapsulate impurities effectively.
- Other additives: Ingredients like lime are also utilized in flux formulas to enhance their functional capabilities.
Understanding the specific role each component plays is crucial for optimizing the smelting process. The proper balance of these materials influences the efficiency and effectiveness of gold recovery, ensuring that precious metals are not wasted during extraction.
Role of Flux in Gold Recovery
The role of flux in gold recovery extends beyond just promoting the melting process. It has a profound impact on the overall quality of the extracted gold and its purity. When flux is properly formulated and applied, it can significantly improve yield and decrease impurities, resulting in purer gold content. Here are a few key points to consider:
- Enhances Separation: Flux binds with the impurities, forming a slag. This allows for a cleaner separation of gold from the waste materials.
- Temperature Control: Flux helps maintain optimal temperatures during smelting, ensuring a smoother extraction process. If temperatures are too high or too low, not only does it affect yield but it also can harm the quality of the gold.
- Reduced Oxidation: By creating an ideal environment where unwanted reactions are minimized, flux can also reduce the oxidation of gold, leading to higher recovery rates.
"Optimizing a flux formula isn’t just about chemistry; it’s about understanding the intricate relationship between ore composition and the desired purity of gold."
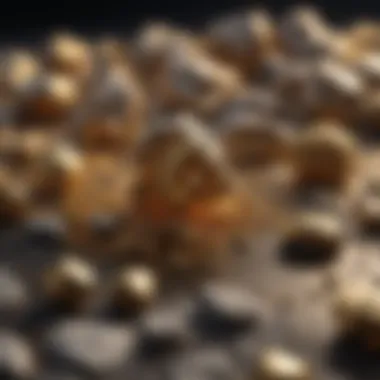
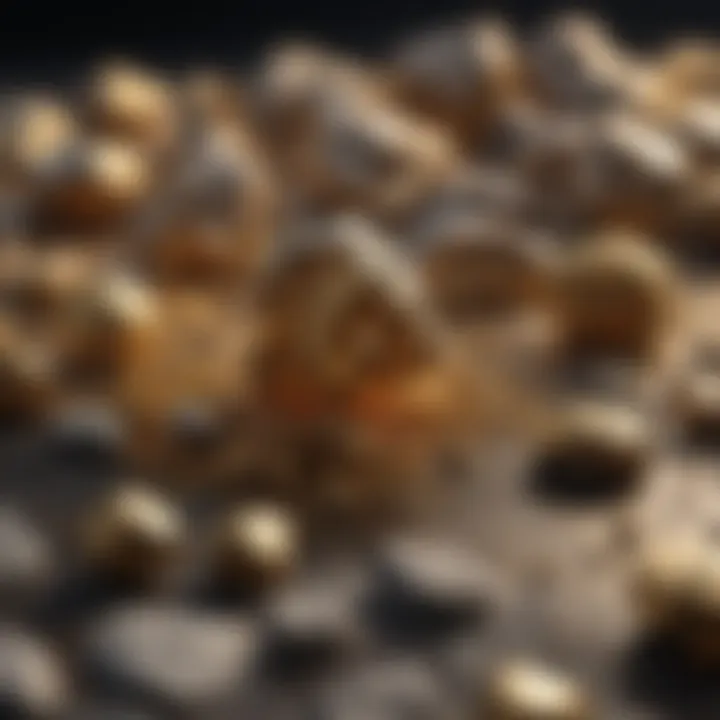
In summary, grasping the concepts around flux is more than an academic exercise, it's an essential part of successful gold smelting practices. The correct application not only aids in extracting maximum yield but also ensures that the quality of the end product meets or exceeds expected standards.
Key Components of Flux Formulas
In the realm of gold smelting, the right flux can be the tipping point between a successful yield and an utter flop. Flux formulas are comprised of various materials, each playing a pivotal role in the smelting operation. In essence, the components of flux not only dictate the efficiency of the smelting process but also influence the quality of the final product. Understanding these key components helps smelters make informed decisions tailored to specific ores and desired outcomes.
Common Flux Materials
Borax
Borax, scientifically known as sodium borate, is often heralded in the smelting world for its ability to lower the melting point of metals and facilitate the removal of impurities. What makes borax a go-to choice is its fluxing action, helping to create a homogeneous liquid that aids in molding the metal. One unique feature of borax is its ability to combine with impurities like lead and sulfur.
Advantages: Its compatibility with various ores makes it a beneficial material for large-scale operations, where multiple types of ore might be processed. However, it's worth noting that its efficiency can decrease when dealing with certain high-sulfur ores, in which case a different approach may be needed.
Soda Ash
Soda ash, or sodium carbonate, is another cornerstone of many flux formulas. Its primary role is to act as a fluxing agent that helps to dissolve silicates and other impurities during the smelting process. A significant characteristic of soda ash is its ability to increase the fluidity of the slag, ensuring a clean separation of precious metals from undesirable elements.
Advantages: It's particularly favored in regions with alkaline materials, enhancing the separation process. However, excessive use can lead to a too-alkaline environment detrimental to the smelting process, requiring careful measurement.
Silica
Silica, commonly found in nature as quartz, serves as a diluent in many flux formulations. Its key contribution lies in forming a protective silica layer over molten metal. This layer prevents oxidation, reducing metal loss during the smelting process. Silica is also known for its high melting point, which proves beneficial in creating a stable structure in the furnace.
Advantages: The consistent quality of silica makes it a reliable choice for achieving desired slag viscosity. Nevertheless, using silica alone can lead to high viscosity, hindering metal recovery and requiring an ideal balance with other flux materials.
Other Additives
Additional materials can significantly enhance flux performance in smelting, including potash, lime, and various metallic oxides. Each additive may target specific impurities or influence specific properties of the flux. For instance, lime (calcium oxide) can help neutralize acidity in the slag, promoting better separation of metals.
Advantages: The use of multiple additives allows for a tailored approach, optimizing the flux for specific ores. That said, over-reliance on additives may lead to increased costs and the introduction of new variables into the smelting process that can complicate outcomes.
Chemical Properties of Flux Components
Understanding the chemical properties of flux components is paramount for anyone engaging in gold smelting. Each material's reactivity plays a role in the overall smelting efficiency. For example, the melting point, solubility, and interaction with the mineral content in the ore directly influence how effectively gold can be extracted.
The interplay between these components showcases the complexity of formulating effective flux. Take, for instance, the relationship between borax and silica. When combined, these materials can create a flux with lower melting temperatures, thus maximizing the potential for recovery. Collectors and enthusiasts must consider these chemical properties when curating a custom flux formula for their specific smelting missions.
Formulating Effective Flux for Gold Smelting
Creating the right flux for gold smelting is no small feat. The formula must consider different variables, each contributing to the final product's efficiency and quality. In this section, we'll break down the essential elements that make up effective flux and the numerous benefits of tailoring a formula specifically suited for the tasks at hand.
Basic Formula Structure
When we talk about flux, it seems simple enough. But getting the structure right can make all the difference. A basic flux formula usually comprises several core ingredients that work in harmony. Some common ingredients include:
- Borax: a star performer for lowering the melting point of gold.
- Soda Ash: helps in removing excess impurities.
- Silica: forms a liquid glass that encapsulates impurities, making them easier to separate.
- Lime: often added to neutralize acidity.
Each formula might appear different but at its heart, it generally follows the same principles. Balancing these components to create a melt that is hot enough yet not damaging to the gold is critical. The ratios depend on various factors like the ore type and the desired purity level.
"A well-structured flux can mean the difference between gold that's ready for the market and material that’s barely more than scrap."
Customization Based on Ore Type
Not every ore is cut from the same cloth; various types require different handling methods. And that’s where customization comes into play. Simply applying a one-size-fits-all approach to flux formulation can lead to disappointing results.
Consider this: if you’re working with a high-sulfur ore, the traditional materials might not yield the best outcomes. In such cases, adjusting the flux might involve incorporating specific additives that enhance the efficiency of the smelting process.
A practical step in customizing your formula involves conducting preliminary tests. Analyze the specific composition of the ore you’re dealing with. Factors such as:
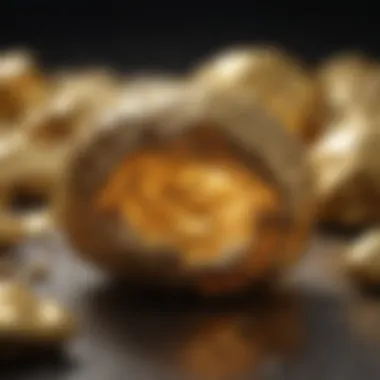
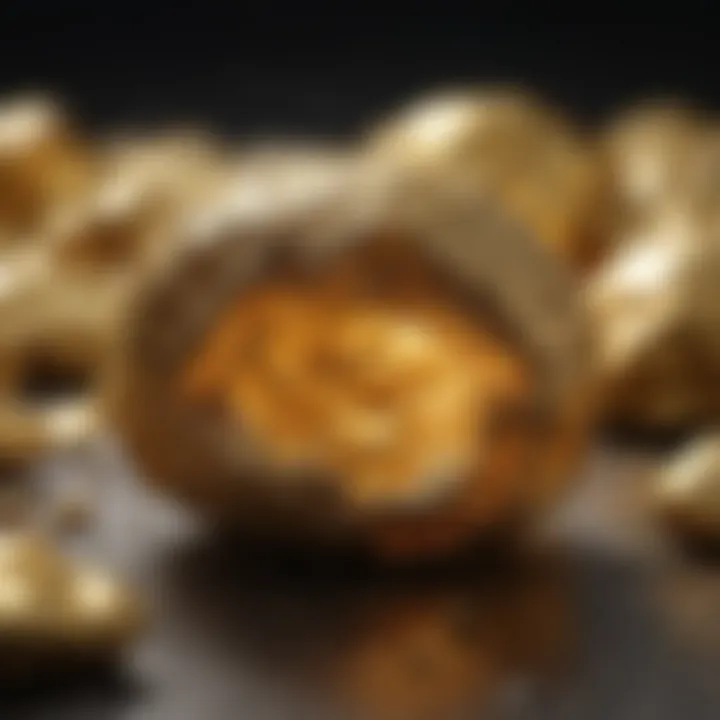
- Mineralogy: Different mineral compositions can react unpredictably with standard flux materials.
- Moisture Content: Higher moisture levels can affect melting efficiency and lead to additional complications.
- Metal Content: More complex ores and those containing multiple metals require careful evaluations.
Tailoring your flux can drastically affect not only the yield but also the purity of the gold extracted. The goal is to create a situation where the flux not only aids in the smelting but actually enhances the whole process.
By paying keen attention to the specifics of your ore, and adjusting flux components accordingly, you set the stage for a more successful extraction process.
The Impact of Flux on Gold Purity
The choice of flux used in gold smelting can make or break the purity of the final product. This section dives into why flux matters not merely for the process, but specifically for achieving a higher grade of gold. From the chemical interactions that take place during smelting to the ability of certain fluxes to minimize contamination, the importance of flux in the gold recovery process is manifold.
When gold ore is processed, it often contains impurities and base metals. This is where the flux’s role comes into play. Using the right flux helps to create a slag that captures these unwanted elements, thereby enhancing the overall purity of the gold. Moreover, the effectiveness of the flux ultimately affects how much gold can be extracted during the smelting process.
Optimizing Yield and Purity
Optimizing yield and purity is not just about the amount of pure gold one desires from a run but also ensuring that the metal’s quality is uncompromised. To strike this balance, several factors should be considered:
- Type of Ore: Different ores contain various impurities. A flux that works wonders for one type of ore may fail for another. For instance, when dealing with high-sulfur ores, a flux rich in calcium might help to neutralize the sulfur, leading to better outcomes.
- Flux Composition: The ratio of different flux components can significantly influence the recovery rates. Using the right amounts of borax, soda ash, and other additives can initiate optimal reactions during the heating process.
- Temperature Control: Keeping a firm hand on the temperature is essential. If it’s too high, flux components could vaporize or degrade, and too low could mean incomplete melting and separation.
"The alignment of flux composition and metal content ensures a smoother, more productive smelting process, leading ultimately to higher purity."
Achieving an optimal smelting environment often requires repetitive testing, sometimes revisiting old formulas to tweak them for new ore sources. The process can be akin to a chef adjusting a recipe; a pinch more salt in a pie can scrap an entire batch, or transform it into a gourmet treat.
Comparative Analysis of Different Formulas
Carrying out a comparative analysis of different formulas is crucial for refining the smelting experience. There are multiple formulas, utilized around the world, which vary not just in chemical components but also in results. Here are a few common comparisons:
- Borax vs. Soda Ash: While borax is often regarded for its ability to lower melting points, soda ash aids in fluxing silica and other impurities. Depending on the desired yield and purity level, one might be favored over the other.
- Boric Acid Additions: Introducing boric acid to your flux can help not only with lowering melting points but can add an additional cleaning effect, especially when dealing with ferrous metals.
- Commercial Flux Mixes: Ready-made commercial flux formulas, like those from Fisher Scientific, typically come with a guaranteed composition aimed at specific types of ores and impurities. However, users should weigh these benefits against the cost and efficiency in their specific smelting scenarios.
In the smelting community, experimenting with various combinations can lead to discoveries that advance personal practices or offer paths to better ratios for maximizing quality yields. Ultimately, each formula brings its own advantages and potential pitfalls that can determine the success of a smelting session.
Common Challenges in Smelting with Flux
Smelting, while a key process in gold extraction, does not come without its share of challenges. Understanding these hurdles is essential for achieving optimal results. From the inherent variability in the materials used to the inevitable presence of contaminants, each factor can significantly affect the smelting process.
In the world of gold collectors and enthusiasts, awareness of these common challenges not only enhances their knowledge but also prepares them to tackle the intricacies that come with flux usage. Addressing these challenges can lead to improved efficiency and effectiveness in gold recovery efforts.
Handling Variability in Metal Content
One major challenge in gold smelting is the variability in the metal content of the ore. When smelting gold-bearing ores, you can end up with different concentrations of precious metals. This variation could be attributed to several factors like the geological environment from which the ore is extracted or even differences in processing methods.
This variability plays a critical role in how much flux is needed and what composition should be applied. Too much flux can dilute the metal content, leading to losses in yield. Conversely, not enough can hinder the smelting process, leaving undesirable materials behind in the smelting crucible. Collectors need to analyze their specific ore composition to design a formula that accommodates these variances.
A thorough testing phase before smelting can help conditional formulation and adjustments. Effective use of assay techniques assists in determining the exact metal ratios, which can directly impact the choice of flux used during the smelting process. This attention to detail helps manage expectations and conserves precious resources.
Dealing with Contaminants
The presence of contaminants is another tough nut to crack when it comes to gold smelting. Common sources of contamination may include other minerals, oils, or even impurities within the flux itself. These contaminants can compromise purity and yield, making it a critical focus area for those involved in smelting.
To mitigate this issue, it's crucial to implement stringent screening processes for both raw materials and flux components. Implementing a filtration or refining process before smelting will go a long way in reducing contaminants. Additionally, specialized flux formulas that cater to specific contaminants can be an effective remedy. For instance, if certain minerals are consistently noted as impurities, incorporating fluxing agents that can react with these specific compounds may lead to an enhanced purification process.
Moreover, maintaining a clean working environment is equally significant. A cluttered workspace may inadvertently introduce foreign substances, which can interfere with the smelting process. Achieving a high level of purity in the final product requires diligence and attention to detail at every step, from raw material selection to the final smelting procedures.
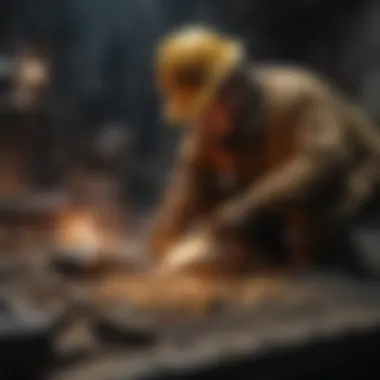
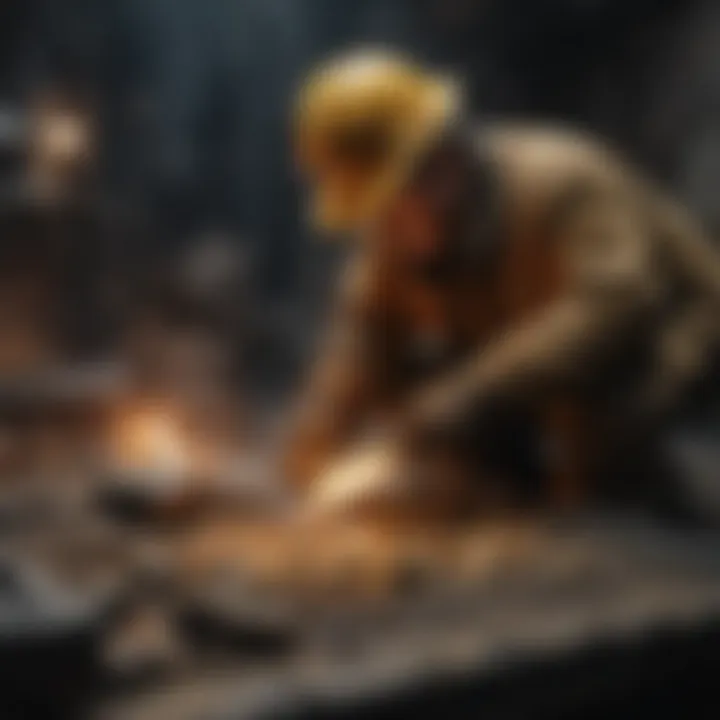
"Paying attention to every element, from ore composition to workspace cleanliness, is vital for achieving successful gold recovery through smelting with flux."
In summary, while the journey of smelting gold comprises various challenges, understanding and addressing these obstacles can significantly improve outcomes. By focusing on the specific variability of metal content and actively managing the presence of contaminants, collectors and enthusiasts can sharpen their skills in the artisanal craft of gold smelting.
Safety Protocols in Gold Smelting
In the intricate world of gold smelting, adhering to safety protocols is not just a recommendation; it is a necessity that can significantly impact both your well-being and the success of the smelting process. This area has its share of hazards, and understanding how to navigate them is paramount. A strong commitment to safety enables smelters to protect themselves and ensure optimal conditions during the smelting operations. This section will explore the key components of safety in gold smelting, specifically focusing on Personal Protective Equipment and the critical importance of maintaining proper ventilation and atmospheric safety.
Personal Protective Equipment
When venturing into the realm of gold smelting, the first line of defense lies in Personal Protective Equipment (PPE). This gear is indispensable for safeguarding one's health against potential hazards associated with high temperatures, toxic fumes, and harmful particulates. A comprehensive PPE plan typically includes:
- Heat-Resistant Gloves: Protects hands from extreme heat during handling of molten materials.
- Safety Goggles: Shields the eyes from flying debris and chemical splashes that can occur during processing.
- Respirators or Masks: Essential for filtering out harmful particles and gases that may be present in the air, especially when working with flux materials.
- Protective Clothing: Flame-retardant suits or aprons that minimize exposure to extreme heat and potential chemical burns.
Using PPE effectively not only prevents serious injuries but also fosters an environment where focus on the smelting process is enhanced. When individuals feel secure, the quality of work naturally improves.
"The importance of safety gear in gold smelting cannot be understated; neglecting it can lead to accidents that could have been easily avoided."
Ventilation and Atmospheric Safety
Equally vital to the use of PPE is ensuring proper ventilation and maintaining atmospheric safety within the smelting environment. Inadequate air circulation can lead to a buildup of toxic gases and fumes, which pose significant health risks. To mitigate these dangers, consider the following:
- Use of Exhaust Fans: Installing exhaust systems helps remove harmful vapors from the workspace, promoting fresh air flow.
- Maintain Open Spaces: Ensuring that the smelting area is spacious can aid in natural ventilation, allowing for the free movement of air.
- Regular Monitoring: Utilizing air quality monitors to keep track of potential gas concentrations can preemptively address issues before they escalate.
- Training on Emergency Procedures: Educating workers on how to respond in case of gas leaks or fire hazards ensures that everyone knows their role if an emergency arises.
Creating an environment where air quality is prioritized not only protects the health of those involved but also ensures a smoother operational process, ultimately leading to better outcomes in the smelting efforts.
In summary, implementing effective safety protocols in gold smelting is critical for protecting both individuals and the success of smelting operations. By prioritizing personal protective equipment and ensuring proper ventilation and atmospheric safety, smelters can navigate this complex process with confidence and care.
Future Trends in Gold Smelting Techniques
The world of gold smelting is always evolving, reflecting broader changes in technology and environmental consciousness. As we move forward, understanding these trends is crucial for both collectors and professionals alike. The advancement of techniques and the push for sustainable practices shape the future of the industry. These futures don’t just affect large-scale operations; they carry implications for small-lot smelting as well, influencing everything from yield to environmental footprint.
Advancements in Flux Research
Research into flux formulations has gained momentum, driven by the need to improve efficiency and reduce contamination during the smelting process. Recent developments have introduced novel flux materials that enhance the purity of gold while minimizing the release of harmful byproducts. For instance, scientists are exploring the use of organic fluxes, which could provide environmentally friendly alternatives to traditional methods.
The chemical complexity of these new fluxes involves a refined balance of silica and sodium bicarbonate, among other components. These ingredients not only promote better separation of gold from impurities but also require lower smelting temperatures.
- Benefits of New Fluxes:
- Enhanced gold recovery rates.
- Lower energy consumption.
- Reduced environmental impact.
"Innovative flux research is a gold mine for potential, unearthing practices that could reshape smelting for good."
As flux technology continues to progress, it enables smelters to adapt to varying types of ores and impurities, which is often the Achilles' heel of many operations. This adaptability can dramatically improve the overall process.
Sustainability in Smelting Practices
The gold smelting sector is not immune to the sustainability wave sweeping across industries. Collectors and miners are increasingly aware of the environmental implications of their practices. More stakeholders are advocating for methods that not only recover metals efficiently but do so with regard to ecological preservation.
To this end, several techniques are gaining traction:
- Recycling of Flux Materials: Using spent fluxes or other waste materials can minimize resources needed for new flux. For example, adapting waste glass as an alternative flux is seeing experimental interest.
- Water Management: Improved methods for handling water during the cooling phase of smelting are being implemented, reducing water wastage and contamination risk.
- Energy Efficiency Innovations: Emerging technologies like induction heating are proving to be more energy-efficient alternatives to traditional furnaces, reducing greenhouse gas emissions during gold recovery.
The interplay between flux technology advancements and sustainability efforts is vital. Sustainable flux formulas that minimize environmental harm while maximizing recovery are an area of active pursuit.
In sum, the trends in gold smelting practice not only serve to refine techniques but also to elevate the discipline toward a more conscientious and environmentally friendly future. For those invested in the art of smelting—whether amateurs or seasoned experts—this evolution represents both a challenge and a tremendous opportunity.