Exploring the Functionality of Gemstone Drilling Machines
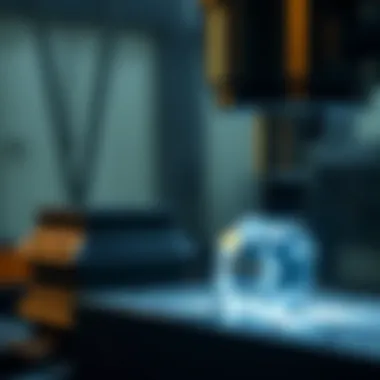
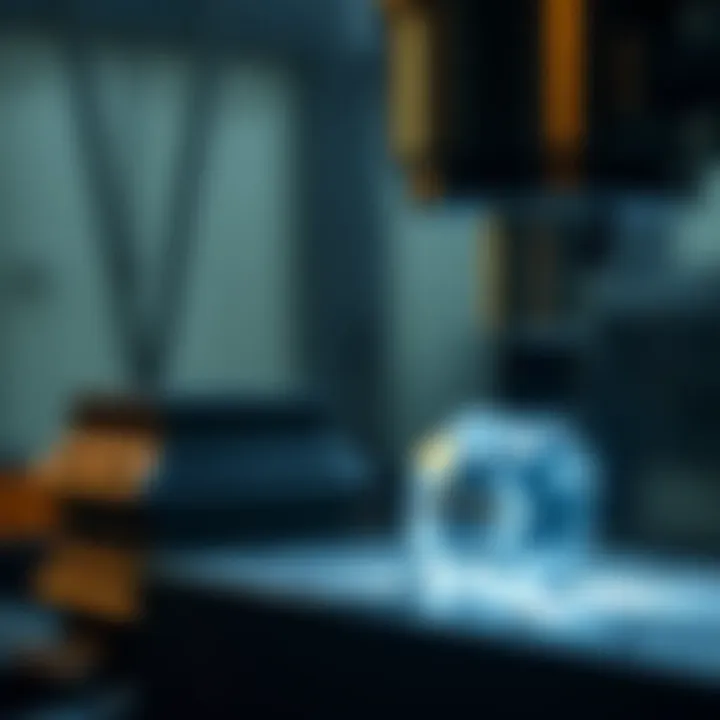
Intro
Gemstone drilling machines represent the nexus of artistry and engineering, acting as pivotal tools in the process of transforming raw gemstones into finely crafted pieces. Understanding how these machines work is not just a matter of interest but also a necessity for those deeply involved in the gemstone industry. From jewelry makers to gemologists, the knowledge of drilling machinery profoundly impacts the quality and precision of their work.
In recent years, technological advancements have revolutionized the capabilities of these machines, enabling craftspersons to achieve results that were once deemed unattainable. This article will delve into the functionalities of gemstone drilling machines, their applications, and the innovations defining current practices in gemstone processing.
As we navigate through this content, readers will find insights into different collectible categories, essential tools for identification, and methods that aid in recognizing valuable stones. Each section intertwines information that is crucial for both novice collectors and seasoned professionals, creating a comprehensive understanding that touches upon both machinery and craftsmanship.
As we embark on this exploration, it’s essential to grasp how these machines impact the broader realm of gemstones. By addressing key topics, this guide aims to enhance readers' awareness of both the challenges and opportunities that lie within the gemstone drilling process.
Preamble to Gemstone Drilling Machines
In the realm of gemstone processing, drilling machines play a pivotal role, acting as the bridge between raw gemstones and their polished final forms. Understanding these machines is not merely academic; it’s an essential step for anyone involved in the jewelry industry or gemstone collectibles. For collectors and professionals alike, grasping how these machines function and their historical context can lead to better decision-making and enhanced craftsmanship.
Definition and Purpose
Gemstone drilling machines are specialized tools designed to create precise holes in gemstones, a task that is integral for a variety of purposes. The primary aim of these machines is to prepare gemstones for settings in jewelry or for other enhancements. Think of them as the artists’ tools that allow for creativity in how a stone is used, whether in rigorous manufacturing processes or delicate artistic endeavors. They come equipped with robust components designed to handle the hardness and unique properties of different types of stones, from diamonds to softer materials like opal. These machines not only save time but also improve the accuracy of the drilling process, leading to better quality products.
Historical Background
The journey of gemstone drilling machines can be traced back to ancient civilizations that recognized the beauty and value of gemstones. Initially, simple hand tools allowed artisans to carve and pierce stones, but as demands increased, more sophisticated devices emerged. By the 19th century, the advent of mechanical innovation saw the development of powered drilling machines, drastically shifting labor dynamics in workshops. This transformation heralded a new era, where precision and efficiency became paramount. In the modern context, automated systems have further revolutionized bead-making and stone setting, blending artistry and engineering. Understanding this evolution helps today’s gemstone collectors and craftspeople appreciate the advancements that bring us to the cutting-edge technology of gemstone drilling machines used today.
Mechanics of Drill Operation
The mechanics of drill operation play a pivotal role in the gemstone drilling industry, determining not only the efficiency but also the precision and quality of the drilling process. Understanding these mechanics helps users to select appropriate drilling techniques and machines, ensuring that they meet specific requirements for various gemstones. Furthermore, carefully considering each element, from the choice of drilling technique to the components of the machine itself, greatly influences the outcome in gemstone processing and enhancement.
Types of Drilling Techniques
Rotary Drilling
Rotary drilling is one of the most traditional methods used in the industry. Its main characteristic lies in the rotating drill bit that cuts through material with a combination of pressure and rotation. This method is especially enjoyed for its reliability and straightforward operation, making it a popular choice for many gemstone artisans. A unique feature of rotary drilling is that it can be used on a variety of materials, including harder stones like sapphires and rubies, thanks to specially-designed bits.
However, this technique has its downsides. For instance, it might generate more heat than other methods, which could potentially damage sensitive gems. Hence, users often need to balance speed and the integrity of the gemstones being drilled.
Diamond Core Drilling
In contrast to rotary drilling, diamond core drilling uses diamond-tipped bits. The significant aspect of this method is the capability to extract cylindrical cores from stones. These cores can then be used to analyze or craft cutting-edge gemstone features. This technique has become increasingly beneficial due to its precision, making it a go-to choice for high-end applications where detail matters.
Its unique advantage is the very low risk of damaging the gemstone compared to other methods. On the flip side, the costs associated with diamond drill bits can be quite high, which might deter some hobbyists or smaller businesses from utilizing this technique regularly.
Water Jet Drilling
Water jet drilling is perhaps the most innovative method covered in this discussion. It utilizes a high-pressure stream of water to penetrate materials, making it an excellent option for delicate gemstones that require a soft touch. The key characteristic of this method is that it generates minimal thermal impact, thus preserving the quality of the gemstones during the drilling process.
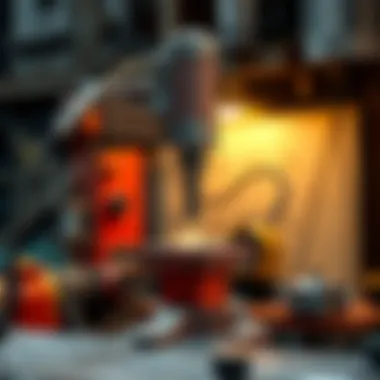
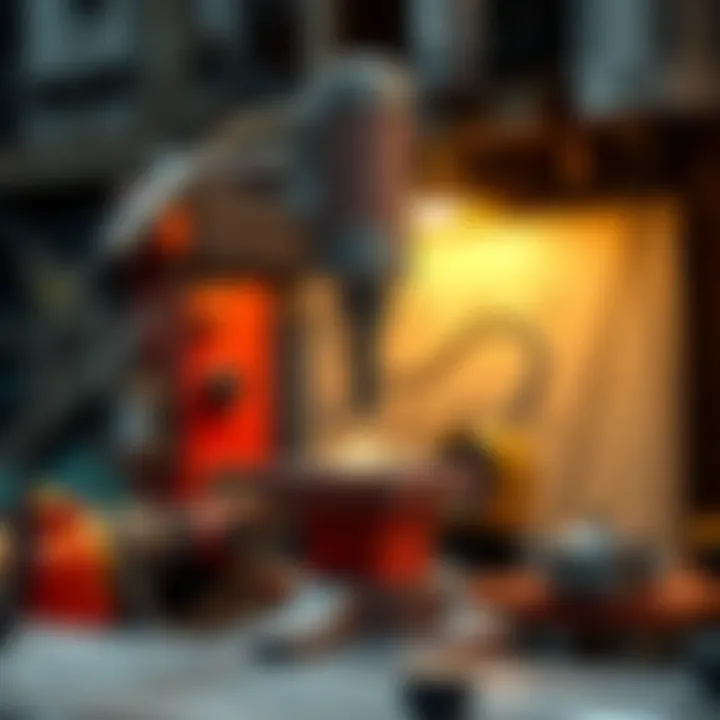
The unique aspect is the fact that water jet drilling can cut through various types of materials without needing contact-based cutting tools, reducing wear and tear on the machinery. However, it might not be the fastest option available, which could potentially be a drawback for operations that prioritize speed.
Components of a Drilling Machine
Drill Bits
Drill bits are essential components of any gemstone drilling machine. They come in various forms, each designed for specific purposes. The primary characteristic of drill bits is their material and design, which directly affect their efficiency and durability.
For instance, diamond bits are preferred for drilling through extremely hard stones. Their unique feature lies in their ability to cut through tough surfaces without significant fracture or damage to the gemstone. However, they can be pricey, so users must weigh the benefits against the initial investment.
Power Sources
The power source of a drilling machine determines its operational prowess. Electric power sources are common, but pneumatic or hydraulic systems might be employed for specific applications. The key aspect of considering power sources is their influence on drilling speed and consistency.
Electric systems usually provide ample power for moderate tasks, while pneumatic systems may offer high efficiency for larger operations. Each type carries its own advantages and disadvantages, particularly in terms of cost and accessibility, which users must consider based on their business needs.
Control Mechanisms
Control mechanisms govern the operation of a drilling machine, affecting everything from speed to precision. The key characteristic of these systems is that they enhance user ability to maintain consistent results. Advanced machines now incorporate digital controls, allowing for greater accuracy.
The unique aspect of modern control systems includes programmable settings for various materials, reducing the risk of human error. However, complexities can arise when users encounter technological issues, and troubleshooting may require a level of expertise that not every user possesses.
Applications in the Gemstone Industry
The role of gemstone drilling machines in the gemstone industry is nothing short of pivotal. These machines serve various essential functions that extend from crafting exquisite jewelry to enhancing the visual appeal of gems. The applications are diverse, each with unique requirements, benefits, and challenges. Understanding these applications allows manufacturers, jewelers, and artisans to harness the full potential of their drilling technology, ensuring the quality and precision that defines their work.
Jewelry Manufacturing
In the jewelry manufacturing sector, precision is the name of the game. When creating intricate pieces, every detail matters. Gemstone drilling is crucial for mounting gems in settings, as well as for adding unique detailing. For example, when drillers use specific techniques to create holes in gemstones, they ensure that the stones can fit securely in a jewelry piece without compromising their structure.
A popular choice among jewelers is the diamond core drill. This drill type yields clean, precise holes, minimizing the risk of chipping or causing fractures in the delicate gemstone material. The ability to drill stones like opal, emerald, and sapphire means a wider variety of options for jewelry designers.
Additionally, drilling machines allow for customization. Jewelers can create bespoke pieces tailored to individual tastes, significantly boosting customer satisfaction.
The key in jewelry manufacturing is not just how well you can drill but how you can do it without hurting the integrity of the stone.
Gemstone Enhancement Processes
Gemstone enhancement is a process that transforms raw stones into eye-catching jewels. Drilling plays a meaningful role here, especially in treatments like oiling and dyeing.
When drilling into porous stones, such as jade or lapis lazuli, artisans create openings that allow oils or dyes to penetrate the stone. This process not only enhances color but also improves the clarity, making the stone more appealing to the market. Moreover, using water jet drilling can significantly reduce the potential damage to the stone, allowing for intricate design work with minimal disruption.
To maximize effectiveness, understanding the types of enhancements that can be applied through drilled openings is crucial for gemologists and jewelers alike. These enhancements can often turn a standard piece into one that captivates and delights consumers.
Artistic and Craft Applications
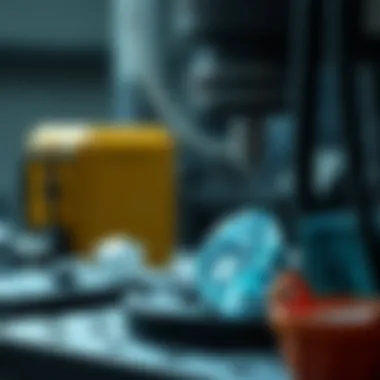
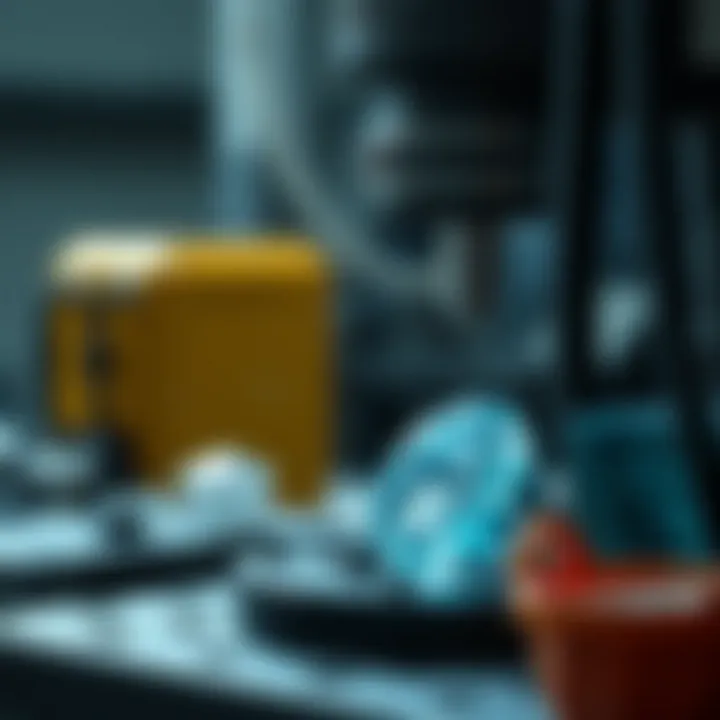
Artisans and craftspeople have taken gemstone drilling to an entirely different realm. Here, the focus shifts from traditional ends to more innovative expressions of creativity. Artists can create intricate sculptures, jewelry setups, and mixed media art, where drilled gemstones can serve as focal points or textures.
Makers may use machines that allow for unique drilling techniques, such as variable speed drilling, to achieve different textures or finishes. For example, a slow drilling speed can help prevent overheating, which is crucial when working with heat-sensitive stones like turquoise or coral. This adaptability enables artists to bring their visions to life, showcasing gemstones in ways that resonate with contemporary audiences.
Craft fairs and galleries often display such artistic pieces, highlighting the synergy between machinery and craftsmanship. Aspiring artisans can gain inspiration from their counterparts and push the envelope further in their own work.
Technological Advancements
In the realm of gemstone drilling, technological advancements play a pivotal role. They not only enhance the efficiency of gemstone processing but also significantly improve the precision and outcome of the drilling process. As the industry evolves, it is essential for users and manufacturers alike to appreciate the strides made in technology and their implications on daily operations, costs, and sustainability. Here, we will discuss three key areas of technological innovation: automation and precision, software integration, and sustainable design in drilling machines.
Automation and Precision
The automation of drilling processes represents a leap forward in gemstone extraction techniques. With the introduction of automated systems, operators can achieve consistent results while minimizing human error. Machines equipped with sensors can adjust drilling depths and angles in real-time, ensuring that gemstones are drilled with the utmost care and accuracy.
Such precision is crucial for maintaining the integrity of gems, especially those valued for their clarity. For instance, incorporating robotic arms can lead to 24/7 operational capabilities, drastically reducing processing time without sacrificing quality. Users can also enjoy greater flexibility, as these machines allow for multiple drilling configurations tailored to diverse gem types.
The benefits extend beyond just the immediate results. Automation reduces the physical strain on workers, leading to safer work environments and allowing for a more focused workforce. In turn, these advancements lead to increased productivity, which is unmatched in comparison to older manual methods.
Software Integration in Drilling Machines
Modern drilling machines are becoming increasingly sophisticated, thanks largely to the integration of software solutions. Software applications designed for gemstone drilling allow operators to monitor drilling parameters and visualize processes through user-friendly interfaces. A notable example is the use of CAD (Computer-Aided Design) software, which enhances the design of drilling patterns, offering precise specifications ahead of the drilling stage.
Moreover, the use of AI and machine learning algorithms enables predictive maintenance, where software can analyze machine performance and alert operators of potential issues before they arise. This proactive approach can prevent costly downtimes, creating a seamless workflow in gemstone processing. The capability to store data and analyze past performance also opens fascinating avenues for improving future operations.
Sustainability in Machine Design
As the world leans toward sustainable practices, the gemstone drilling industry is no exception. Advances in machine design are allowing manufacturers to create energy-efficient machines that use less power and produce less waste. For instance, adopting materials that are recyclable or have a lower carbon footprint represents a significant shift towards eco-friendliness in production.
This push for sustainability is not merely a trend but a response to growing environmental concerns. By embracing technologies that promote energy efficiency, gemstone businesses can not only reduce their operational costs but also appeal to environmentally conscious consumers who prioritize sustainability in their purchasing decisions. Furthermore, sustainable practices open the doors to government incentives, presenting a financial advantage in a competitive market.
"The intersection of technology and sustainability is where the future of gemstone drilling truly lies, paving the way for innovation while respecting the planet."
Safety and Maintenance Guidelines
Ensuring that gemstone drilling machines operate efficiently and safely is an essential aspect of their use in various applications. Safety and maintenance guidelines help minimize risks to users while extending the machine's lifespan – a vital factor for any serious operator or business in the gemstone industry. A well-maintained drill not only improves performance but also can prevent unnecessary equipment failures that could lead to downtime and financial losses.
Safety Protocols for Users
Working with any type of machinery comes with its own set of risks, and gemstone drilling machines are no exception. Following proper safety protocols is crucial in ensuring a safe working environment. Here are some important guidelines to keep in mind:
- Always wear personal protective equipment (PPE): This should include safety goggles, gloves, and ear protection to guard against flying debris and excessive noise.
- Ensure the drilling area is clear: Before starting the machine, check that no one is within a danger zone. A clutter-free workspace minimizes the risk of accidents.
- Regular machine inspections: Before using the drill, perform inspections to check for wear and tear on drill bits, power cords, and other components. This practice helps catch potential hazards early on.
- Training for operators: Ensure that all users are adequately trained on the machine’s operation and safety requirements. Knowledgeable operators are more likely to adhere to safety standards and make informed decisions during use.
- Emergency protocols: Familiarize yourself and your team with emergency procedures, including proper shutdowns and first-aid responses in case of accidents.
"Safety isn't just a slogan; it's a commitment to excellence in machine operation."
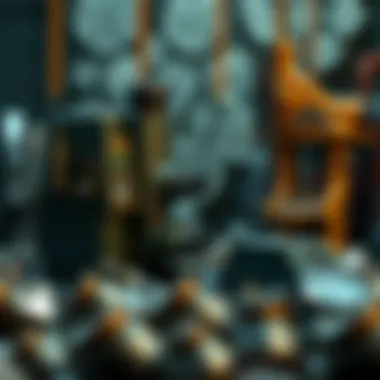
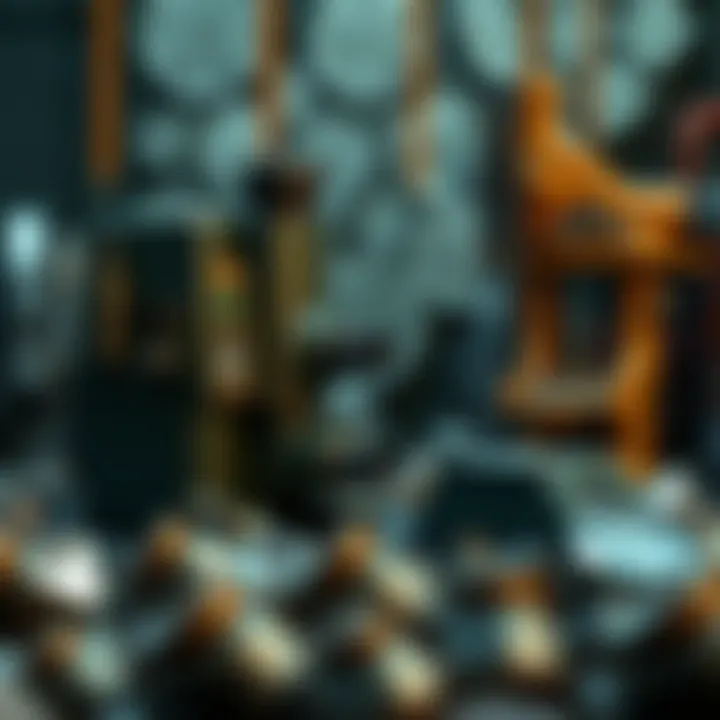
Following these protocols can dramatically reduce the risks associated with using gemstone drilling machines and promote a healthier workplace.
Routine Maintenance Practices
Routine maintenance is the backbone of any effective gemstone drilling operation. Regular servicing ensures that the machine functions at its best, minimizing downtime and improving efficiency in drilling tasks. Here’s a look at some critical practices:
- Daily clean-up: After each use, clean the machine to remove dust, debris, and any resin build-up. This simple habit prevents wear on mechanical parts and prolongs their lifespan.
- Lubrication: Just like any other machinery, drilling machines require regular lubrication of moving parts to reduce friction and prevent breakdowns. Use the manufacturer’s specified lubricant for best results.
- Inspection of drill bits: Periodically examine drill bits for signs of wear, such as chipping or dullness. If issues arise, replace them promptly to maintain drilling efficiency.
- Checking power sources: Ensure that all electrical connections are secure and functioning properly to avoid power-related issues during operations. Inspect cords and connectors for damage.
- Record-keeping: Maintain a log of maintenance activities. Keeping track of service dates and actions taken can help anticipate future needs and provide insights into machine performance over time.
By incorporating these maintenance practices, users can significantly extend the lifespan of their gemstone drilling machines. Just as maintenance is crucial for any piece of equipment, making it a priority reflects a commitment to quality craftsmanship and operational excellence in the gemstone industry.
Economic Considerations
In the realm of gemstone drilling, economics plays a pivotal role. Whether you're a seasoned miner, a budding designer, or a collector, understanding the financial implications of drilling equipment can greatly influence your operations. The price tag attached to these machines often necessitates a detailed analysis and consideration of their long-term benefit to both production quality and operational efficiency.
Cost Analysis of Drilling Equipment
When delving into the cost of drilling machines, several factors come into play. First and foremost is the initial investment. The cost can vary greatly depending on the sophistication of the machine—for instance, a basic rotary drill may range from thousands to tens of thousands, while specialized models like those with automated features can skyrocket into the six-figure territory.
Moreover, one should also consider:
- Maintenance Expenses: Regular upkeep isn’t just a formality. Neglect can escalate costs substantially. A poorly maintained machine can lead to breakdowns, costly repairs, or even compromised productivity.
- Operational Costs: This includes energy consumption, labor, and any consumables such as drill bits and lubricants. A high-efficiency machine might have a steeper upfront cost but can save on energy and material expenses in the long run.
- Financing Options: Many businesses consider leasing equipment rather than buying outright. This can mitigate initial costs but may incur more over time due to interest and fees.
Understanding this cost landscape not only aids in informed decision-making but also sets realistic budgeting expectations.
Return on Investment for Gemstone Businesses
Calculating the return on investment (ROI) for gemstone drilling machines is crucial for any business eyeing long-term success. The ROI can be viewed through various lenses—each pointing toward increased yield, enhanced quality, and competitive edge.
- Increased Yield: High-performance drilling machines can extract more material in less time, translating to higher productivity rates. More stones mean more products for sale, subsequently boosting revenue.
- Enhanced Quality: Superior drilling processes lead to fewer flaws. This is critical, especially for high-value gems where any imperfection can mean a substantial loss in value. A quality tool preserves the integrity of the gemstones, which is invaluable.
- Competitive Advantage: In a field where precision and quality set businesses apart, the ability to leverage advanced drilling technology can position a company ahead of the pack. Consumers are often willing to pay a premium for products that are clearly superior.
"Investing in quality machinery is investing in quality outcomes."
Future Prospects in Gemstone Drilling
The landscape of gemstone drilling is undergoing a significant transformation, driven by technological advancements and evolving market demands. In this section, we delve into the factors shaping the future of gemstone drilling, considering how innovation is poised to enhance both efficiency and precision in this specialized field. It's only fair that we explore what the future may hold for gemstone drilling machines, as understanding these potential developments can provide insights into their benefits and the broader implications for the gemstone industry.
Emerging Trends and Innovations
Recent years have witnessed several emerging trends within the gemstone drilling sector. These innovations are primarily fueled by the need for higher efficiency, greater accuracy, and sustainability. Key areas of development include:
- Smart Drilling Technologies: Incorporating IoT (Internet of Things) technology into drilling machines allows for real-time monitoring and analysis of performance metrics, leading to informed decision-making.
- Enhanced Materials for Bits: Advances in material science have led to the development of drill bits that are not only more durable but also capable of precise operations, reducing breakage rates and extending the lifecycle of the equipment.
- Eco-Friendly Solutions: With increased awareness of environmental impact, companies are exploring sustainable alternatives to traditional drilling methods, such as waterless drilling techniques and energy-efficient machinery.
"The future of gemstone drilling is not just about technology; it’s also about harmonizing production with sustainability."
Moreover, the integration of artificial intelligence into drilling operations is making waves. AI algorithms can predict drill wear, optimizing performance and minimizing downtime. This leads to smoother operations and lowers costs—two critical factors for businesses looking to remain competitive.
Potential Market Growth
As the gemstone market continues to evolve, so too does the demand for effective drilling solutions. Factors driving this potential market growth include:
- Increased Interest in Natural Stones: More consumers are turning towards natural gemstones, which increases the need for high-value drilling techniques that preserve the integrity of the stone.
- Customization and Branding: Businesses in the gemstone trade are looking to differentiate themselves. Efficient drilling technologies allow for more intricate designs and personalized products, tapping into the consumer desire for unique and bespoke items.
- Global Market Expansion: Emerging markets, particularly in Asia and Africa, show a growing demand for gemstones, pushing the need for efficient processing technologies to meet this rising demand.