Techniques for Drilling into Granite Rock
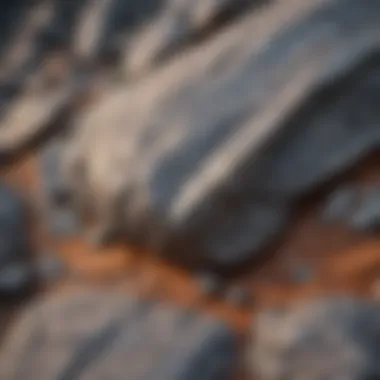
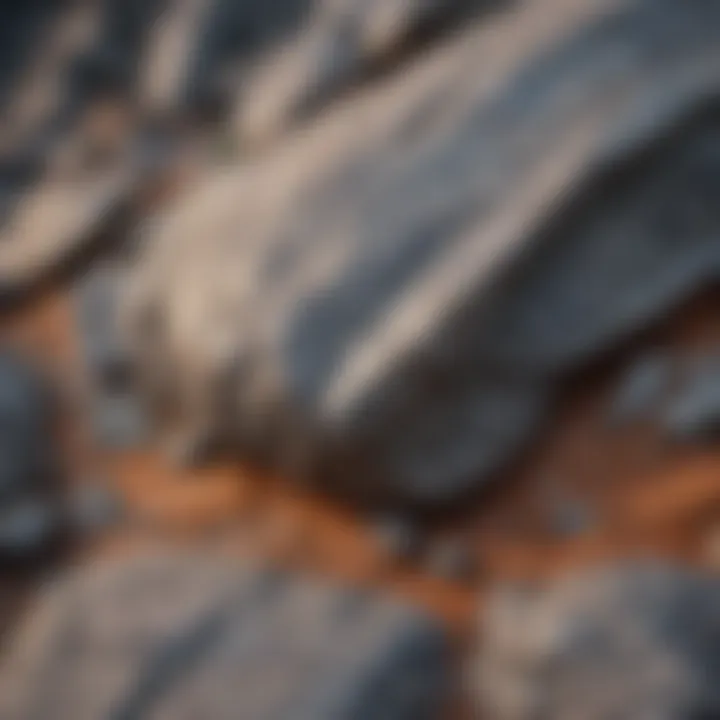
Intro
Drilling into granite rock is no casual feat; it takes a blend of the right knowledge, tools, and techniques to tackle this formidable material. Granite, known for its strength and longevity, presents unique challenges that make it essential for both professionals and enthusiasts to fully grasp the methods and safety protocols involved in this endeavor. If you’re someone who seeks to navigate the complexities of drilling into granite—whether for a construction project or perhaps for a geological study—it’s important to take heed of the nuances and intricacies that come into play.
As we delve into the various methods and technologies available, expect to gain insights into the types of drills and bits best suited for this hard-as-nails rock, alongside the necessary safety considerations. This discussion will unpack granite's geological characteristics, the latest advancements in drilling technology, and practical applications that showcase its significance in our world.
With this grounding, let's first explore the kinds of techniques available for anyone considering this specialized task.
Understanding Granite Rock
Drilling into granite rock involves understanding a material that is both ancient and incredibly resilient. This exploration of granite’s characteristics is crucial not only for specialists but also for enthusiasts looking to engage with this captivating stone. Knowing about granite lays the groundwork for effective drilling techniques and informed decision-making during the drilling process.
Geological History of Granite
Granite is primarily an igneous rock formed from slowly cooled molten rock beneath the Earth's surface. This slow cooling allows large crystals of quartz, feldspar, and mica to develop, giving granite its distinctive speckled appearance. The geological history of granite dates back millions of years—some formations can even stretch into prehistoric eras.
As mountain ranges formed through tectonic activity, granite emerged at the surface due to erosion. The granite in the Sierra Nevada, for example, started forming approximately 100 million years ago. Such a rich history means that granite contains fossils and minerals that tell the story of Earth’s past. Understanding this context can provide insights into what one might encounter when drilling into such enduring material.
Physical Properties of Granite
Granite is categorized by its hardness and density, which makes it notably more challenging to drill compared to other materials. With a Mohs hardness rating typically ranging from 6 to 7, granite is resilient to many forms of mechanical wear. This characteristic implies that standard drilling tactics one might employ for softer stone won't yield satisfying results.
The density of granite varies between 2.63 to 2.75 grams per cubic centimeter. Such density contributes to its strength but also poses challenges in terms of required tools and techniques for drilling. Furthermore, granite's low porosity and specific composition can alter the behavior of drilling bits, emphasizing the importance of using proper equipment.
Common Uses of Granite
Granite is not just a geological marvel; its physical properties have led to a wide array of practical applications. Common uses include:
- Construction: Widely utilized in buildings, bridges, and monuments due to its durability and aesthetic appeal.
- Countertops: Sought after for kitchen and bathroom surfaces because of its resistance to scratches and heat.
- Paving stones: As a favorite for driveways and pathways, granite provides long-lasting and visually appealing surfaces.
- Cultural artifacts: Often used in sculptures or memorials, reflecting both historical significance and craftsmanship.
This versatility highlights the reasons why drilling into granite can lean towards being necessary, not just in construction but in further applications in scientific studies or archaeology.
Understanding the characteristics of granite is foundational. It helps anticipate the hurdles that drilling poses and is a critical factor in determining the right approach and tools before starting any drilling project.
The Challenge of Drilling into Granite
Drilling into granite presents a unique set of challenges that can baffle even seasoned professionals. This dense, igneous rock, formed from slow-cooling magma, is not just iconic for its durability and beauty, but profoundly difficult to work with. Each drillist must fully appreciate these obstacles, as the right techniques and tools can mean the difference between success and a frustrating failure. The significance of understanding these challenges is not just about getting the job done; it’s about maximizing efficiency, safety, and achieving high-quality results.
Understanding Hardness and Density
Granite is renowned for its extraordinary hardness, which is a critical factor to consider during drilling. This hardness stems from its mineral composition, which typically includes quartz, feldspar, and mica. Each of these minerals contributes to the rock's toughness, making it exceptionally resistant to wear and requiring specialized drilling strategies.
The density of granite, usually around 2.6 to 2.8 grams per cubic centimeter, adds another layer of complexity. It means that more force is needed to penetrate the granite compared to softer stones. This increased density can lead to issues such as excessive heat generation and drill bit wear. Thus, understanding both hardness and density is paramount for anyone attempting to drill into granite, as it informs the choice of tools and techniques.
"Understanding granite's physical properties isn’t a luxury; it's a necessity for those serious about drilling."
Comparative Drilling Techniques
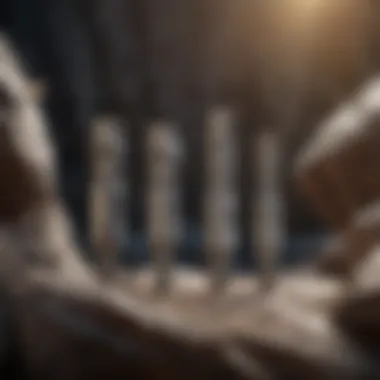
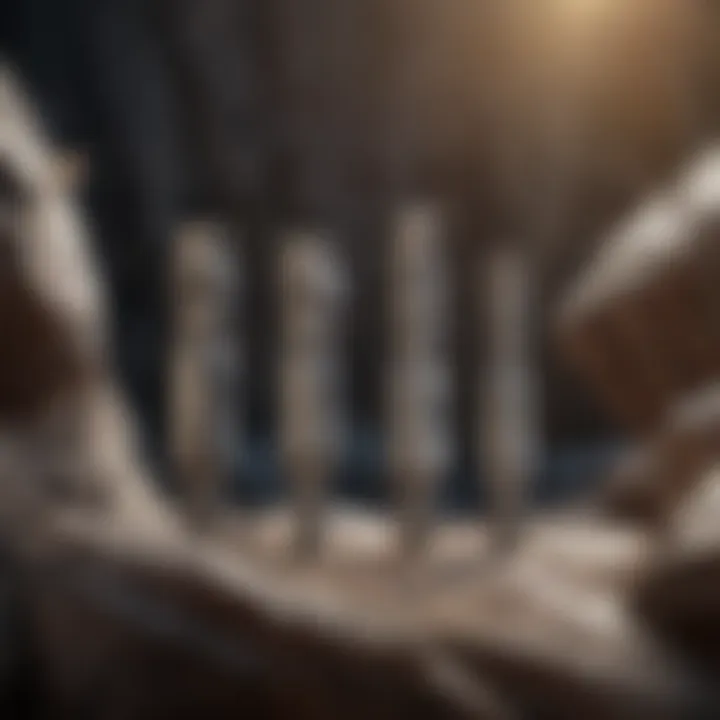
When it comes to drilling into granite, not all techniques are created equal. Each approach has its own merits and demerits based on the situation at hand. Let’s discuss some of the common methods employed in this tough terrain:
- Rotary Drilling: This is the go-to technique for many professionals. It involves a rotating drill bit, usually of a diamond or carbide-tipped variety, which grinds away the rock. The key here is to maintain an appropriate speed and use a sufficient amount of water or fluid to minimize heat and facilitate better cutting.
- Percussion Drilling: For harder granite areas, percussion drilling can come into play. This technique uses rapid hammering to break the rock apart, which can be advantageous in particularly dense regions.
- Core Drilling: This method is used when obtaining samples is crucial. Core drills, typically fitted with diamond bits, create cylindrical holes that preserve the integrity of the sample. This is vital for geological studies or when determining the quality of granite for construction projects.
Each drilling technique has its ideal application, and choosing the wrong method could lead to inefficient results or even damage to the drill and surrounding area. It’s essential for drillers to evaluate their project’s requirements carefully, considering the granite's hardness and characteristics.
Essential Tools for Drilling Granite
Drilling into granite requires precision and the right set of tools. Understanding the nature of granite—its hardness and density—makes it clear why specialized equipment is essential. Proper tools not only enhance efficiency but also contribute to the safety and quality of the project.
Types of Drills Suitable for Granite
When it comes to drilling in granite, not all drills are created equal. A rotary drill may fall flat against this tough surface. Instead, more powerful tools are often required. Hammer drills and diamond-tipped drills are among the top choices.
- Rotary Hammer Drills: These drills work by combining rotation with hammering, delivering powerful bursts of energy that break through granite effectively.
- Diamond Core Drills: They utilize diamond-tipped bits that cut through granite stones cleanly, perfect for creating holes for anchors or plumbing fixtures.
- Electric Rock Drills: Commonly used in mining, this option combines power and versatility for extensive tasks.
Different Drill Bits: Characteristics and Uses
Drill bits vary significantly in design and materials, catering to different needs in drilling granite. Here we'll explore three key types often considered for this specific task.
Diamond Drill Bits
Diamond drill bits are typically seen as the gold standard when drilling into hard materials like granite. These bits are characterized by their ability to maintain sharpness longer than other types. The key characteristic that stands out is the presence of industrial diamonds embedded in the bit which creates a cutting surface.
- Benefits: Their primary benefit lies in their longevity and efficiency in creating clean, precise holes.
- Unique Feature: They generate less heat due to their cutting process, which helps preserve the integrity of the rock.
- Disadvantages: However, they come at a higher cost and may not be suitable for softer materials.
Carbide-Tipped Bits
Carbide-tipped bits are another option widely used in drilling granite. They consist of a steel body with tungsten carbide attached to the tip. Their key characteristic is their durability against wear, allowing for prolonged use.
- Benefits: These bits are often seen as a good middle ground—effective for various materials, not just granite.
- Unique Feature: They can withstand high temperatures, making them suitable for drilling deep holes.
- Disadvantages: However, while they are effective, they do not last as long as diamond bits and can struggle with very dense granite.
Core Drills
Core drills serve a specific purpose—removing a core or cylindrical piece of material from the granite. These tools are valuable when a larger diameter hole is needed.
- Benefits: They adeptly extract samples, which is particularly beneficial for geological studies or mining endeavors.
- Key Characteristic: Core drills have a hollow center, enabling them to leave a perfectly round hole, which can be critical for various applications.
- Disadvantages: However, they can require a substantial amount of water for cooling, and the drill size can limit its use in tight spaces.
"Using the right tools makes all the difference in ensuring a successful drilling operation in granite. They not only improve efficiency but also enhance safety and accuracy."
Equipped with this knowledge on drills and drill bits, one can approach granite drilling with more confidence. The right tools and bits are essentials that can’t be overlooked when dealing with such a challenging material.
Drilling Techniques and Best Practices
Drilling into granite rock isn't just a straightforward task; it demands careful planning and execution. Unsurprisingly, the techniques and best practices employed can significantly impact the efficiency and effectiveness of the entire process. From understanding site conditions to controlling the drill's speed and pressure, proper techniques can unlock the secrets of successful granite drilling.
Pre-Drilling Site Evaluation
Before even picking up a drill, a thorough site evaluation is critical. It's your opportunity to gather insights about the granite you'll be working with. Inspecting the area for fractures, veins, and other anomalies can save a whole heap of trouble down the line.

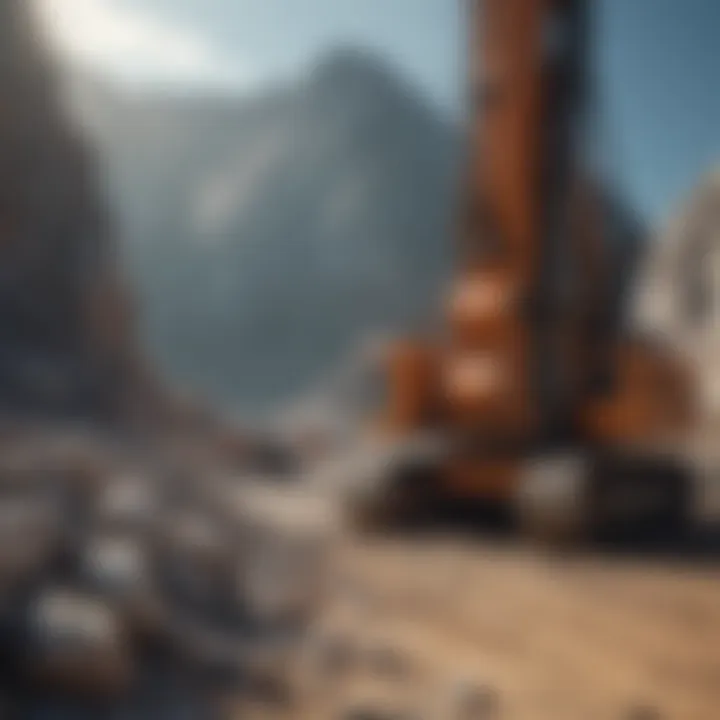
Common considerations during this evaluation might include:
- Identifying Geological Features: Recognizing the type of granite in your target area is key. Some might be more porous or contain quartz veins that can affect drilling conditions.
- Assessing Accessibility: Check if the drilling location is easy to reach. Poor accessibility can complicate logistics and might need additional equipment.
- Safety Hazards: Always keep an eye out for any unstable rocks or environmental hazards that might pose threats during drilling.
Doing a thoughtful evaluation can prevent headaches when the drill starts whirring.
Drilling Speed and Pressure Control
When diving into granite, speed isn't always your friend. Finding the right balance of drilling speed and pressure is crucial. Going full throttle might seem tempting, but it often leads to wear and tear on your drill bits faster than you can blink.
Here are some helpful guidelines to control both:
- Start Slow: Begin with lower speeds to assess how the granite responds. Gradual adjustments can keep the drill bit intact for longer.
- Monitor Pressure: Too much pressure can cause overheating, which is particularly damaging when working with dense rock. Keeping pressure within recommended limits ensures a longer lifespan for your tools.
- Adjust Based on Feedback: Modern drills often come with readouts that provide feedback on performance. Staying in tune with these readings can be beneficial to adapt your approach in real time.
Cooling and Lubrication Techniques
The heat generated while drilling through granite can be monumental. Ignoring the need for cooling or lubrication is like throwing a match on a can of gasoline. Implementing proper cooling techniques can mean the difference between fine-tuning your work and replacing expensive bits.
Cooling strategies might include:
- Water Cooling: This method involves using a water supply to cool down the drill bit while keeping dust and debris at bay. It's effective, but ensure proper drainage to prevent muddy conditions.
- Oil-Based Lubricants: In certain scenarios, oil-based lubricants can be used. They create a barrier that reduces friction and can prolong drill life.
- Cyclic Cooling: Alternate between drilling and pausing to allow heat dissipation. This rhythm can keep the equipment running more smoothly.
Employing effective cooling methods not only enhances the lifespan of your equipment but also improves drilling accuracy, which is vital in delicate projects where precision is key.
Maintaining the right practices through each phase of the drilling process is where the distinction between amateur and seasoned professionals lies. With thorough evaluations, mindful speed and pressure control, along with careful cooling strategies, anyone can tackle that granite rock like a pro.
Safety Considerations when Drilling
When it comes to drilling into granite, safety is paramount. The very nature of granite—rigid and dense—poses a variety of risks during the drilling process. Ignoring these safety considerations can result in serious injuries or accidents. It’s crucial to understand the hazards associated with drilling to ensure both the well-being of the operator and the efficacy of the work being performed. These practices not only protect individuals but also enhance overall operational effectiveness through systematic risk management.
Personal Protective Equipment
Proper Personal Protective Equipment (PPE) is indispensable. Ensuring that workers are equipped with the right gear minimizes exposure to hazards that drilling into granite presents. This includes:
- Safety Goggles: Protecting the eyes from flying debris is essential. Granite can produce small particles that can cause significant eye injuries.
- Hard Hats: In cases of overhead hazards, a hard hat ensures protection against potential falling objects, like drill bits or stone fragments.
- Ear Protection: The noise produced during drilling is notoriously loud and can lead to hearing loss over time. Using earmuffs or earplugs can mitigate this risk.
- Respirators: As particles become airborne, inhalation can pose a serious health risk. A respirator protects against fine dust particles and silicates found in granite.
- Sturdy Work Boots: Footwear should be reinforced and slip-resistant, as uneven surfaces and heavy equipment increase the risk of slips and falls.
By wearing the right protective gear, workers can significantly reduce the likelihood of injuries while focusing on achieving drilling objectives effectively.
Mitigating Dust and Debris Risks
Granite drilling generates a substantial amount of dust and debris. This has implications not only for safety but also for the environment and the quality of the work being completed. Here are strategies to mitigate these issues:
- Water Suppression Techniques: Applying water during the drilling process can help to suppress dust, keeping the air cleaner and reducing the risk of respiratory issues. A wet drilling approach is often employed, enabling the drill bit to operate more efficiently while controlling water usage.
- Dust Extraction Systems: Invest in effective dust extraction systems that vacuum up particles as they are created. This technology not only keeps the work area tidier but also protects the health of those working in the vicinity.
- Site Preparation: Preparing the work environment to minimize dust accumulation is essential. This may involve securing loose materials, using barriers, or creating designated work zones.
- Regular Clean-Up: Consistent maintenance of the site is imperative for safety. Employing regular clean-up routines during and after drilling can prevent accidents related to tripping over debris.
"An ounce of prevention is worth a pound of cure.” Taking preventative measures ensures that safety remains a priority in drilling practices, protecting both workers and the environment.
Applications of Drilling in Granite
When it comes to drilling into granite, its many applications demonstrate its significance across various sectors. Granite, with its unparalleled durability and aesthetic appeal, is a material of choice in numerous industries. Understanding the applications of drilling in granite is vital as it sheds light on not just the technical processes involved, but also the economic and functional advantages that this rock genus provides.
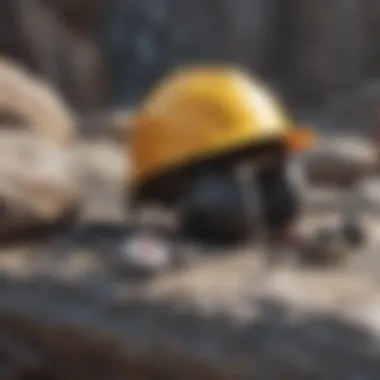
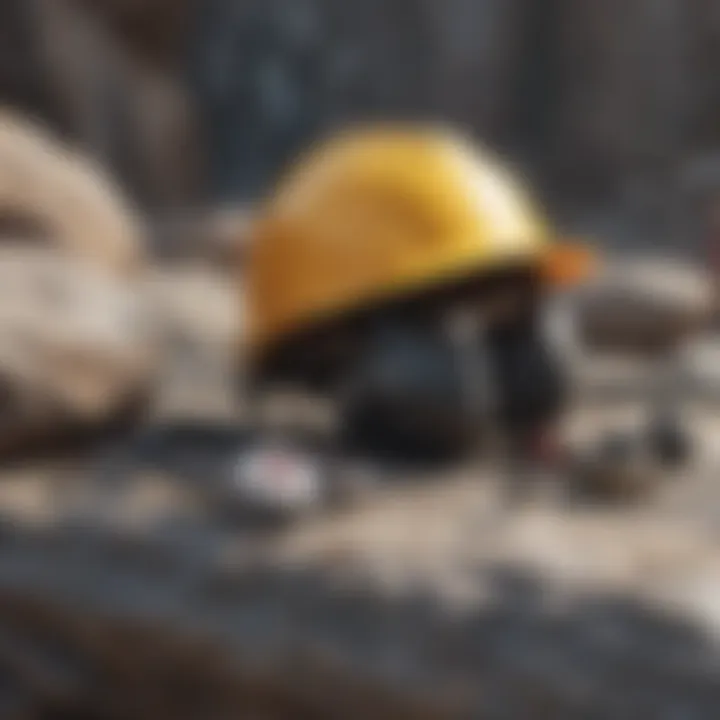
Construction Industry Uses
In the construction realm, granite is often utilized for everything from countertops to cladding materials in buildings. Drilling into granite for anchoring purposes, such as installing bolts or other fixtures, enhances structural integrity. Notably, granite's longevity means that structures incorporating it can withstand harsh environmental conditions, a characteristic that is even more pronounced when proper drilling techniques are applied to ensure durability.
Moreover, as urban areas expand, granite is frequently mined to meet the demand for sturdy construction materials. Drilling techniques allow for precise cuts and adaptations of granite blocks, which can then be shaped as per design specifications in contemporary architecture.
Mining and Quarrying Applications
Granite mining and quarrying are resource-intensive processes, calling for proficient drilling to extract large stone blocks. The techniques involved here are often quite specialized, aimed at producing minimal waste while ensuring maximally usable stone. Drillers using diamond-tipped bits can achieve cleaner cuts, greatly reducing the need for subsequent processing.
The economic impact is undeniably significant; skilled teams can quarry granite effectively, meeting market demands without compromising on quality. Projects such as road construction and infrastructure development benefit immensely from granite’s strength, and the drilling methods in use directly correlate with the resource efficiency witnessed in these operations. The relationship between innovative drilling techniques and sustainable quarrying practices is a topic worth further exploration.
Scientific and Archaeological Drilling
Drilling into granite also extends into more academic realms, such as geology and archaeology. In scientific exploration, researchers utilize advanced drilling equipment to retrieve core samples, allowing them to analyze subsurface geology. This plays a crucial role in understanding earth's history and transformations over millennia.
From an archaeological perspective, drilling into granite can help unearth historical artifacts without causing damage to surrounding areas. Techniques developed to minimize disturbance have made it easier for scientists to study sites of significance, revealing cultural insights while preserving the integrity of ancient structures.
"The technologies used in drilling can sometimes get overlooked, but they are at the heart of successful extraction and exploration tasks."
Future Developments in Drilling Technology
In the world of granite drilling, keeping up with the latest advancements is integral for efficiency and effectiveness. This part of the article sheds light on what lies ahead in drilling technology. As granite has become a popular material in construction and other sectors, the need for better drilling methods has surged. Innovating how we drill can mean quicker projects, reduced costs, and enhanced safety.
Innovations in Drill Designs
The future of drill designs seems promising and dynamic. Recent advancements focus on enhancing durability and improving suction capabilities for dust removal. For instance, drills are being designed with materials that withstand higher temperatures and increased wear, countering granite's toughness.
- Hybrid Drills: Combining traditional methods with newer technologies is on the rise. These hybrid drills may utilize laser technology, melting through granite with precision while minimizing physical wear on the drill itself.
- Ergonomics: Tools are also becoming user-friendly. More comfortable grips and lighter materials help workers maintain efficiency during prolonged use.
- Smart Sensors: Integrating sensors that monitor drill bit performance in real time can alert operators to when a bit is becoming dull or overheated. This can save time and prevent potential accidents.
These innovations may reshape the drilling landscape, but it’s crucial to consider their implications on cost and accessibility. As manufacturers innovate, these new designs may initially come with a heavy price tag, which could deter small-scale operations.
Potential for Automation in Drilling
Automation is another major trend poised to impact drilling into granite. With the push toward smart construction, the use of robotics and automated systems brings new advantages to the table. It’s not just about replacing workers; it’s about enhancing what they can do.
- Autonomous Drilling Rigs: These machines can function without constant human oversight. Programmed to drill through various rock types, they can adapt to conditions, potentially improving accuracy and speed.
- Data-Driven Decisions: Using big data alongside AI can lead to better decision-making in drilling projects. With predictive analytics, operators can foresee issues before they manifest, optimizing workflow.
- Remote Operations: Imagine controlling a drilling operation from a thousand miles away. Automated systems might not only boost safety but allow projects in remote areas to be managed with greater ease.
As we embrace these technologies, it's equally important to assess their reliability and the training required for personnel to operate them effectively.
"Technological integration in drilling not only promises improvements in efficiency but can also drive down long-term operational costs, opening new avenues for exploration and construction."
The ongoing trends in drilling technology indicate an exciting phase for the industry. For rock and fossil collectors, these advancements could translate into more precise and less invasive drilling methods, allowing for better preservation of sites rich in geological history.
Finale and Final Thoughts
When contemplating the realm of drilling into granite, it’s clear that understanding the techniques and considerations involved is paramount for success. The unforgiving nature of granite rock, both in its hardness and density, presents unique challenges that can deter even seasoned professionals. However, by leveraging the insights gathered throughout this article, readers can navigate these challenges more effectively.
Summary of Key Points
In summary, here are some key elements that stand out:
- Granite Characteristics: Knowing the geological aspects of granite helps in choosing the right tools and strategies for drilling.
- Drilling Techniques: Effective techniques extend beyond merely selecting the drill and bit; they include proper site evaluation, speed management, and cooling measures to avoid damage.
- Safety Protocols: A strong emphasis on safety, from protective equipment to dust management, protects not only the worker but also the integrity of the drilling site.
- Impacts of Technology: Awareness of current advancements in drilling technology allows individuals to stay ahead of the curve and utilize the best practices.
- Practical Applications: Understanding how granite drilling fits within the broader context of construction, mining, and scientific research opens avenues for innovative uses of drilled granite applications.
As you move forward, consider how each of these points contributes not just to the act of drilling but to the overarching goals tied to your specific projects. Whether in artistic endeavors or practical applications, having a comprehensive grasp of these aspects will pave the way for success. capping off this exploration, it's essential to return to the mindset of continual learning and adaptation as technology evolves, ensuring that you remain proficient and informed in your endeavors related to drilling granite.