Mastering Dremel Wet Sanding Techniques for Crafters
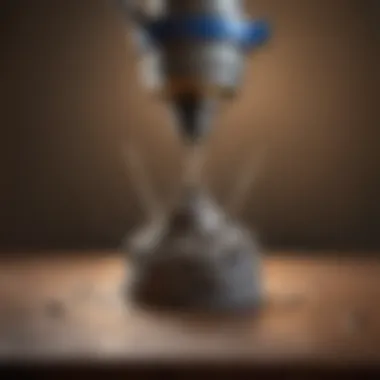
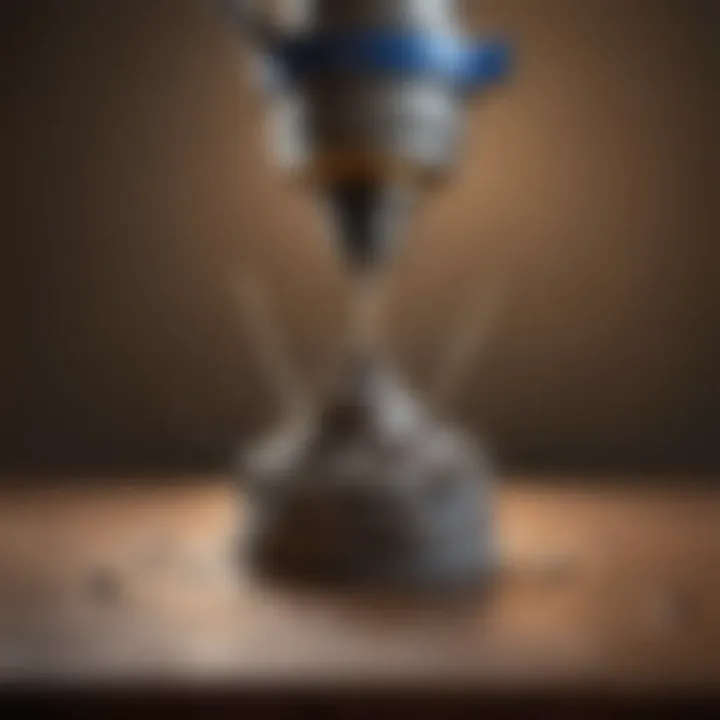
Intro
In the realm of crafting and DIY projects, achieving a flawless finish can feel like searching for a needle in a haystack. However, wielding a Dremel tool coupled with the technique of wet sanding can transform that arduous task into a more manageable endeavor. This guide aims to delve into the nitty-gritty of Dremel wet sanding, exploring the nuanced methods that elevate the quality of your work.
Wet sanding, in essence, is a technique that involves the use of water during the sanding process, lubricating the surface and reducing the risk of dust. Using a Dremel tool for this purpose takes the art of finishing to a whole new level. Whether you’re grooming a prized rock or polishing a fossil, mastering this technique can lead to superior results.
What’s on the Table
This article will unravel the specifics of wet sanding with Dremel tools. You can expect a discussion on the advantages of utilizing this method, a breakdown of the materials you'll need, and step-by-step instructions to execute the technique effectively. Moreover, potential hurdles will be addressed, and strategies will be shared to navigate through them, ensuring you come out the other end with not just an understanding of wet sanding, but a polished skill set.
So, grab your Dremel, and let’s embark on this journey to transform your crafting endeavors.
Understanding Wet Sanding
Wet sanding is not just a quirky choice in the realm of crafting; it plays an essential role when it comes to working with materials that require precision and an impressive finish. This technique involves using water to lubricate the sanding process, which can lead to significant improvements in the final appearance of your work. For many craftsmen and hobbyists, especially those dealing with rocks and fossils, mastering wet sanding can enhance both the aesthetic appeal and durability of their projects.
The Basics of Wet Sanding
To fully appreciate the advantages of wet sanding, it's crucial to grasp its foundational aspects. Unlike traditional sanding, where dust flies everywhere and creates a mess, wet sanding keeps debris in check. Here, the water acts as a bonding agent, holding particles together, which means less of that annoying dust floating around. This means less mess for you to clean up later and a more precise crafting experience overall.
The process involves using special waterproof sandpaper, which can handle the rigors of being submerged in water without falling apart. This gives you not only a smoother surface but also helps in extending the lifespan of your materials and tools.
Why Choose Wet Sanding?
Wet sanding is more than just a dust-free option; it offers a multitude of benefits that can leave even seasoned creators wondering why they didn't switch sooner.
Reduction of Dust
One of the standout features of wet sanding is the reduction of dust. When you're in the zone, sanding away at a precious specimen, the last thing you want is a cloud of dust blocking your view or, worse yet, coating your tools. By using water, particles are kept wet, minimizing airborne debris. This is especially crucial when working indoors or in limited spaces. Moreover, less dust means you're breathing easier, which is always a plus. Cleaner air offers a healthier workspace, allowing for longer, more productive sessions without the nagging cough.
Enhanced Finish Quality
Another significant aspect of wet sanding is the enhanced finish quality it provides. Because the water reduces friction, you can achieve a smoother finish much faster than with dry sanding. This feature becomes evident when you’re polishing rocks or fossils; the results often speak for themselves. An enhanced finish can mean the difference between a project that looks hastily done and one that’s polished to perfection. Many find that the glossy, professional look of a wet-sanded surface can elevate even the simplest pieces into stunning display-worthy works.
Improved Tool Longevity
Last but not least, the improved tool longevity is a characteristic that shouldn't be overlooked. Sanding drums and other Dremel tools face a lot less wear and tear when wet sanding. Water acts as a lubricant, reducing friction and heat, which can wear down your tools over time. Opting for wet sanding can save you money in tools, as they tend to stay sharper longer. This is vital for anyone who often engages in detailed work that requires precision and efficiency.
"By understanding the nuances of wet sanding, you not only enhance your craft but also contribute to a more enjoyable and fruitful working experience."
Dremel Tools Overview
When diving into the world of wet sanding, knowing your tools is half the battle won. Dremel tools are not just versatile; they bring precision and efficiency to various projects. The right model or accessory can transform a mundane task into a seamless experience. This section provides insights into selecting the right Dremel tools and their compatibility with wet sanding techniques.
Choosing the Right Dremel Model
Choosing the appropriate Dremel model involves more than just picking a shiny tool off the shelf. Factors like power, speed settings, and ergonomics play a pivotal role in your wet sanding journey. For instance, the Dremel 4300 is acclaimed for its powerful motor, making it suitable for tougher materials. On the flip side, the Dremel 3000, while not as robust, is easy to handle and good for lighter tasks.
These models come equipped with variable speed settings, allowing you to adjust the intensity depending on the grit of the sandpaper you are using and the material you are sanding. Remember, a too-powerful tool can damage delicate surfaces, while an underpowered one might frustrate your efforts. Hence, understanding the specifics of each model helps in getting the most out of your wet sanding experience.
Accessory Compatibility
A Dremel tool is only as good as its accessories. Knowing which tools to pair with your Dremel can significantly elevate the quality of your work. Here’s a closer look at the crucial components you should consider:
Sanding Drums
Sanding drums are essential for achieving varied results based on your specific task. They come in different sizes and shapes, allowing for flexibility in sanding curved or flat surfaces. The distinctive feature of sanding drums is their ability to deliver a more aggressive cut paired with a finer finish compared to standard sanding discs. This makes them a favorite for anyone looking to refine textures.
Moreover, these drums are usually easy to replace, making them a popular choice. However, be mindful of their wear; they can degrade if used excessively on hardened surfaces, so rotating among several can afford a longer lifespan.
Sanding Discs
Sanding discs, on the other hand, offer a different experience. Their primary advantage is uniformity; unlike drums, they create consistent finishes across flat surfaces. Most Dremel sanding discs are sized to fit different attachments, enhancing their usability. For wet sanding projects, discs designed specifically for smooth finishes are particularly helpful.
On the downside, sanding discs can clog quicker than you’d expect if you’re not vigilant. This necessitates frequent dips in the water reservoir to keep the surface clean and effective.
Water Reservoirs
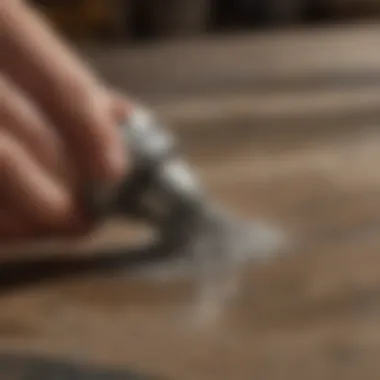
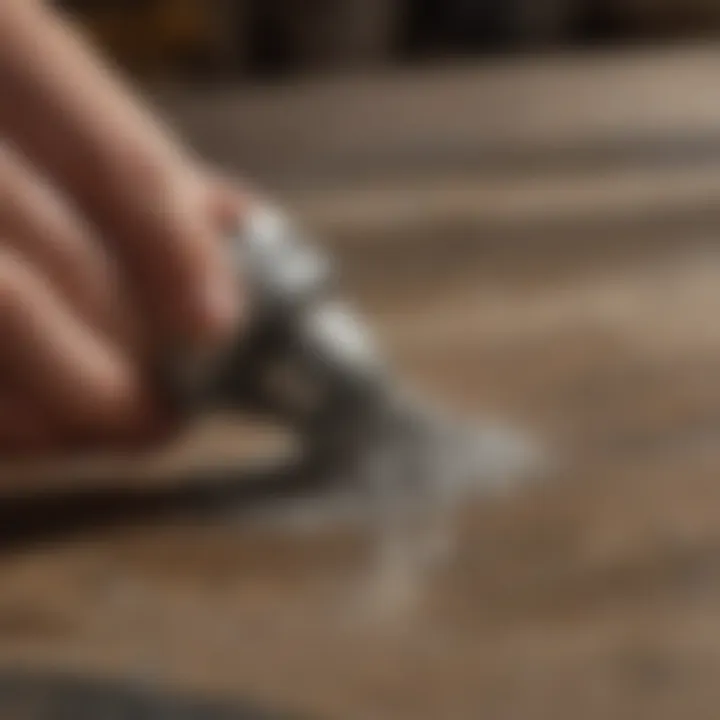
An often-overlooked accessory is the water reservoir. This little addition plays a critical role in preserving the integrity of both your project and your tools. By providing a steady flow of water, it keeps the sanding materials lubricated, which not only reduces the amount of dust kicked up but also minimizes heat buildup.
Choosing a water reservoir that fits your Dremel model is key. Some models come with built-in water supplies; others require additional attachments. Using a reservoir not only extends the life of your sanding materials but also ensures a smoother finish in the long run.
Materials for Wet Sanding
Understanding the right materials for wet sanding is crucial if you want to make the most of your Dremel tools. Choosing the appropriate grit and sandpaper type not only enhances the quality of your finish but also determines the efficiency of your sanding process. A wrong choice might lead to subpar results, leaving you frustrated with uneven surfaces or worse, damage to your project. Therefore, honing in on materials is not just a matter of preference, but rather a fundamental step in achieving the desired outcome.
Selecting the Right Grit
Choosing the right grit is akin to selecting the right shoe for a marathon; not all will serve you equally. Each grit serves its purpose in the sanding process, and understanding the specific role they play can significantly impact your final results. Here’s a breakdown of the grit types:
Coarse Grit for Initial Sanding
Coarse grit is typically in the range of 60 to 80 grit. This is your go-to when you need to level out rough surfaces or remove significant material. In this stage, the aggressive nature of coarse grit really shines, allowing for rapid stock removal. It’s vital for shaping your workpiece, getting rid of imperfections, and preparing it for subsequent refining.
However, while it may quickly smooth out a rough piece, beware: using too coarse a grit for too long can lead to deep scratches that might be challenging to eliminate later on. While it’s a beneficial first step, remember to follow it up with finer grits to ensure a high-quality finish.
Medium Grit for Smoothing
Middle-ground grits, typically ranging from 100 to 220, serve a useful purpose in refining your project after the coarse grit. Using medium grit helps to eliminate the large scratches left by coarse sanding, leading to a smoother surface without removing too much material. Think of it as transitioning from a construction site to a polished showroom.
This grit is often preferred for general-purpose sanding tasks. It strikes that perfect balance, making it ideal for profiles and contours where you need more delicacy. Just be cautious: if used improperly or aggressively, it can still leave scratches, so a gentle hand is often your best bet here.
Fine Grit for Finishing Touches
Fine grit ranges from 240 to 600 and is where the magic truly happens. At this stage, the objective shifts to achieving a polished, glass-like finish. Fine grit effectively eliminates any remaining marks and enhances the overall appearance of your project. It turns those rough edges into smooth territory, allowing you to show off your hard work.
While this grit offers an incredible finish, it requires an understanding of its use. It’s not ideal for stock removal or rough shaping, so patience is key. Remember, fine grit doesn’t work well on rough surfaces; if you start here, you'll end up frustrated with suboptimal results. In short, it’s a finishing touch that elevates your work to the next level.
Best Practices for Paper Selection
Once you've selected the right grit, the next crucial aspect lies in choosing the appropriate type of sandpaper. Each type of paper brings unique characteristics that can either enhance or hinder your project.
Waterproof Sandpaper
Waterproof sandpaper, or wet/dry sandpaper, deserves its place in the spotlight when it comes to wet sanding. Made with a special coating that allows it to withstand moisture, this type of sandpaper prevents degradation during the wet sanding process. Using waterproof sandpaper not only prolongs its life but also ensures a smoother finish because it reduces the likelihood of tearing.
Moreover, its ability to work effectively while wet improves dust control and flushes away debris, keeping your workspace cleaner. However, it’s important to note that waterproof sandpaper is generally more expensive than standard types, so consider your budget accordingly. Still, the benefits often outweigh the costs.
Flexible Sanding Sheets
Flexible sanding sheets are a game-changer when it comes to sanding irregular surfaces. These sheets, unlike traditional sandpaper, can adapt to curves and contours, allowing for a thorough finish even in hard-to-reach areas. Their flexibility means you can sand with freedom and creativity, eliminating those hard edges that traditional sheets might miss.
However, be mindful that they might not last as long under heavy use, so gentle handling is advised. Their ability to perform in tight spaces makes them a valuable addition, particularly for intricate designs, though they may not be necessary for every basic sanding project.
In summary, selecting the right materials and techniques for wet sanding using Dremel tools is vital for success. From understanding the grit types to wisely choosing your sandpaper, every decision counts towards achieving that flawless finish you seek.
Preparation for Wet Sanding
Getting ready for wet sanding isn't just a step; it's the foundation of a successful crafting session. A well-prepared workspace can make your wet sanding process smoother and more effective. Taking the time to set everything up correctly helps you avoid potential mishaps that could lead to frustrations.
Additionally, ensuring that you have a clean and organized environment not only aids in your current project but can also prevent damage to your Dremel tools and the items being worked on. Finishing is an art, and having your tools, materials, and workspace ready sets the stage for creativity to flow without interruptions.
Setting Up Your Workspace
To kick things off, find a spacious surface that can handle a bit of water, as wet sanding can get a little messy. A sturdy workbench or table covered with an old tarp or newspaper works wonders. Organizing your tools so they are easily accessible can save time and hassle. You should have your Dremel tool, sanding attachments, waterproof sandpaper, and a container for water all within arm’s reach. Don’t forget some towels for potential spills – they happen more often than you'd think.
Being cautious about the surrounding area is also essential. Turn off any fans that could blow debris around and create a mess. A little forethought can save a lot of cleanup later.
Safety Precautions
When diving into wet sanding, safety can't take a backseat. Protective gear might not seem like a big deal, but it plays a crucial role in your well-being during the crafting process.
Protective Gear
Consider your eyes and skin; both can be sensitive to materials and dust. Safety goggles are a must. They shield your precious peepers from flying particles, especially when you're using coarser grits. Additionally, a quality dust mask prevents inhalation of any particles that go airborne. You might think you can skip it, but prevention is always better than cleaning up after an irritating cough sets in.
A good pair of gloves helps too. They can protect your hands from the moisture while allowing you to grip your tools securely. Neoprene gloves often stand out as a solid choice, offering both durability and water resistance. Remember, comfort is key when handling tools that require precision.
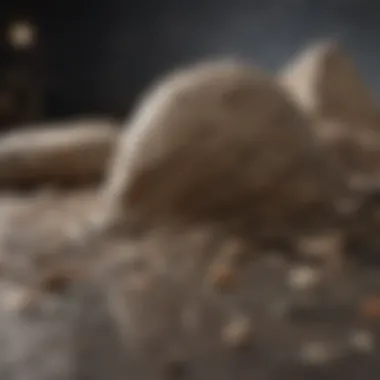
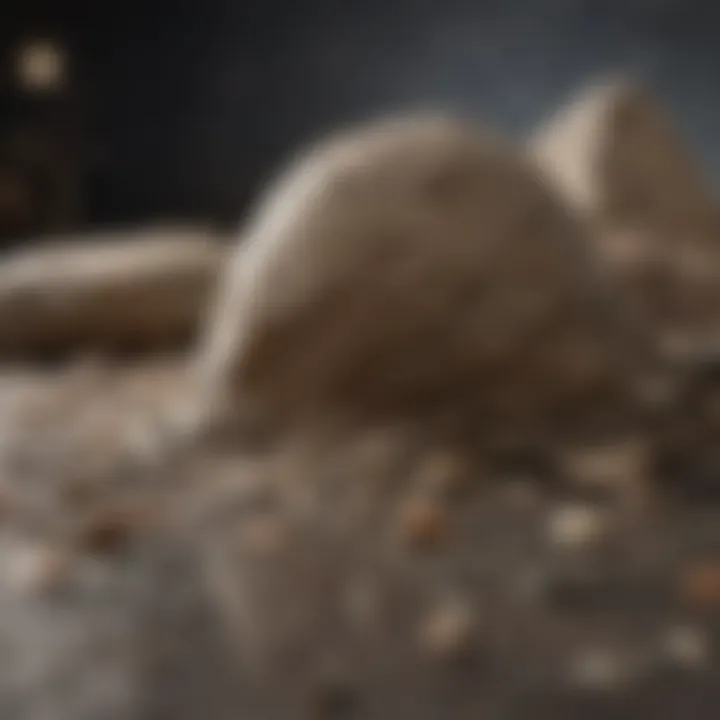
Ventilation Considerations
Now let’s talk about the air. Proper ventilation is invaluable when you're sanding. The key characteristic here is airflow. When you're working with materials that might produce gases or fine dust, ensuring good airflow helps maintain a safe environment. It's not just about comfort; it’s about health.
Setting up your workspace near open windows or in well-ventilated areas is a smart choice. Fans can help, too, but be cautious about where they blow the dust. You want it moving away from you, not right into your face.
Advantages of good ventilation include reducing the risk of inhaling harmful particles, and keeping your workspace fresh and airy enhances your overall crafting experience. It goes beyond just safety; it contributes to a more pleasant working atmosphere, allowing you to focus on your project.
"Spend a minute setting up your workspace and you'll save yourself hours of frustration later!"
Executing the Wet Sanding Process
Getting into the nitty-gritty of wet sanding using Dremel tools can feel like stepping into a whole new realm of crafting. It’s not just about throwing water onto sandpaper and going to town. Oh no, it’s a bit more intricate than that. Executing the Wet Sanding Process is vital because it determines the overall quality of your finish. When done right, it not only smooths out imperfections but can also add a unique touch to your project. This skill can be a game changer, especially for those who seek perfection in the details of their work.
Wet sanding is particularly advantageous for rock and fossil collectors. These materials often demand a certain finesse, where precision is non-negotiable. By mastering the technique of wet sanding, you'll see that it minimizes surface scratches while enhancing the sheen, bringing out the natural beauty of your finds. As a result, this technique can elevate your overall project outcomes remarkably.
Preparations are key, so ensure your workspace and tools are adequately set up. You can't just dive in with gusto. There’s plenty to consider at each stage, from the tools you use to the specific techniques that best suit your project.
Step-by-Step Guide
Feeling unsure about where to kick things off? Let’s break it down step by step. Wet sanding doesn't have to be a daunting task. If you follow a straightforward process, you’ll find that it can even be quite enjoyable. Here’s how you can do it:
- Choose Your Sandpaper: Start with choosing the right grit for your specific task. If you’re working on a rougher surface, you might want coarser grit. But for polishing, go finer.
- Prep the Workspace: Set up a comfortable and well-lit area where you can work. Having a water source nearby is essential.
- Apply Water: Soak your sandpaper in water. This helps reduce friction and eliminates dust, making for a cleaner process.
- Start Sanding: Begin gently, applying light pressure as you work. You want to take your time, allowing the grit to work effectively.
- Inspect Regularly: Check the surface frequently to assess your progress. It helps to prevent over-sanding in one area.
- Clean Up: After you finish, clean your workspace, and make sure to rinse your tools.
Trust me, once you get this process down, it will become second nature.
Common Techniques
When it comes to wet sanding, there are two popular techniques that you can adopt. Each offers unique benefits, and knowing when and how to use them can make all the difference.
Circular Motions
Using circular motions is akin to a painter’s brush strokes on a canvas. It allows you to cover a larger area without creating linear marks. This technique is favored by many because it encourages even pressure distribution.
"Circular motions can really minimize scratches and leave you with a smoother finish."
One of the key characteristics of this approach is that it prevents the build-up of material clogs. When you keep moving in circles, debris doesn’t get a chance to settle. However, it requires a bit more control to ensure that all areas receive equal attention, especially on contoured surfaces.
Linear Passes
On the flip side, linear passes are more about precision. This method involves moving the sandpaper back and forth in straight lines and is particularly effective for flat surfaces. With linear passes, you can focus on specific areas that may need extra attention.
The key characteristic here is the ability to attack deeper scratches or imperfections more directly. However, one has to be cautious not to over-sand or you might end up with uneven patches. Balancing pressure is essential to your success when employing this technique.
In summary, whether one method or the other is better largely depends on the project at hand. By understanding the nuances of these techniques, you’ll elevate your wet sanding game considerably.
Troubleshooting Common Issues
When it comes to wet sanding with Dremel tools, encountering difficulties can happen, whether you’re a novice or seasoned pro. Understanding how to troubleshoot common issues becomes essential. It not only helps in enhancing your final results but also ensures that you maintain the integrity of your tools throughout the sanding process. Proper knowledge of issue resolution can save time, effort, and materials.
Dealing with Material Clogs
Material clogs can seem like a right pain in the neck when you’re knee-deep into a project. They occur when the grit on your sanding drum or disc becomes overwhelmed by debris, which can happen easily if you’re working with large amounts of material. These clogs can lead to ineffective sanding and might even burn the surface, causing irreversible damage.
Consider these tips to handle clogs:
- Regularly Inspect Your Tools: Take a moment to check your Dremel tool and the sanding surface. If you notice a buildup of material, it’s high time to clean it off. Use a soft brush or even your fingers to gently remove the debris.
- Use a Water Spray Bottle: Keep a spray bottle filled with water nearby. A light misting of water can help reduce friction and material build-up, making the sanding process smoother.
- Choose the Right Grit: If you find yourself constantly dealing with clogs, it may be time to rethink your choice of sanding grit. For tougher materials, starting with a course grit and transitioning to finer ones often helps prevent clogs.
These solutions ensure your sanding remains efficient and enjoyable. Moreover, keeping your workspace clean can significantly reduce clogs.
Surface Swirls and Marks
Surface swirls and marks can become a source of headache for many, especially when aiming for a flawless finish. Even the most skilled hands can inadvertently leave these imperfections on a project. Often, these occur because of improper technique or using the wrong tools.
To mitigate and prevent these issues, try the following:
- Consistent Pressure and Motion: While sanding, maintain a steady pressure and motion. Uneven pressure can lead to surface inconsistencies. Try employing overlapping strokes to help diffuse the potential for swirl marks.
- Use Innovative Techniques: Techniques like doing figure-eight motions or circular patterns can help blend any potential swirls and create a smoother finish overall.
- Fine-Tuning Your Technique: If you notice swirls, dial down the speed of your Dremel tool. Going slower with a finer grit can yield a smoother surface, as it reduces the chances of skipping and leaving marks behind.
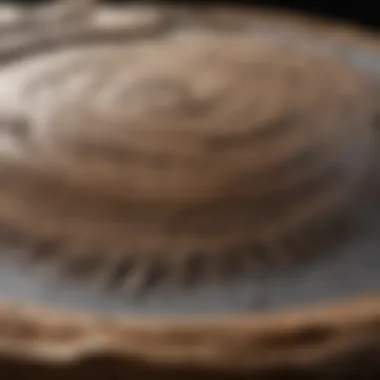
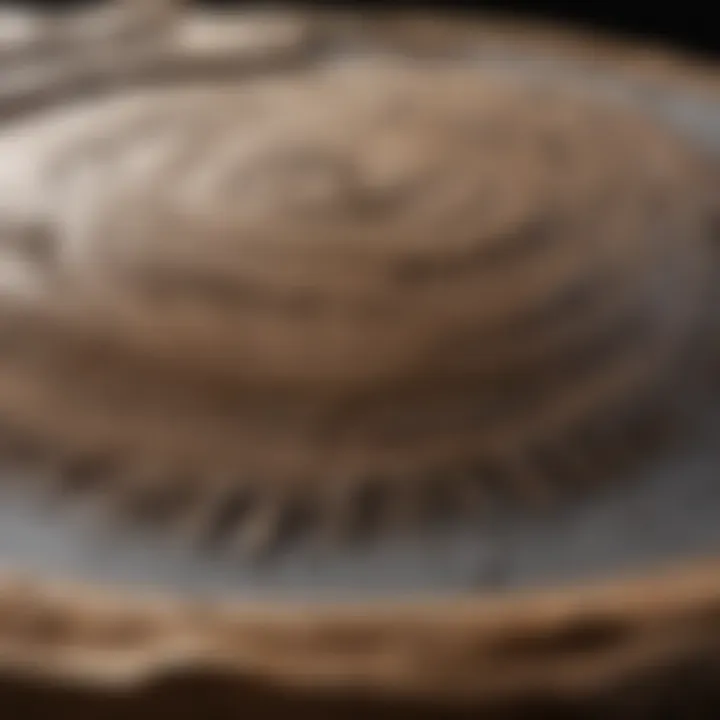
Swirls may seem minor, but they can impact the quality of the entire finish, making understanding their causes crucial.
Being aware of these common challenges along with their solutions means you can tackle wet sanding with confidence. No project is without its bumps in the road, but with careful maneuvering and the right techniques, you can achieve great results, impressing even the most discerning eyes.
Maintenance of Dremel Tools
Maintaining your Dremel tools is not merely a chore; it's an essential part of ensuring they function optimally and serve you well over time. Just think about it like keeping a vintage car in top shape—oiling the engine, checking the tires—the same principle applies here. Dremel tools are precision instruments designed for specific tasks such as wet sanding. If you neglect their maintenance, you risk not only performance issues but also a potential decline in the quality of your projects.
Regular maintenance dramatically extends the lifespan of your tools, allowing you to invest your time and finances wisely. Here are some pivotal benefits to consider:
- Enhanced Performance: Regular cleaning ensures that all components work effectively without interruption or failure.
- Improved Safety: Well-maintained tools are less likely to malfunction, minimizing risks associated with tool mishaps.
- Cost Efficiency: By prolonging the life of your Dremel tools through proper upkeep, you save on replacements and repairs—good for the budget.
By reinforcing these habits into your workflow, you become not just a user of tools but a custodian of their reliability.
Cleaning After Use
Cleaning your Dremel after use is an imperative task. No one wants to be left with a tool that is loaded with dust and debris after a wet sanding session. Here’s a straightforward approach to ensure your tool is clean:
- Unplug the Tool: Always make safety your first priority by disconnecting your Dremel from power before beginning the clean-up.
- Remove Accessories: Take off the sanding drum or disc that you’ve used; keep them aside for separate cleaning if necessary.
- Dirt Removal: Use a brush or compressed air to remove any accumulated debris. Pay attention to vents and crevices, as moisture can seep into places you don’t usually notice.
- Wipe Surfaces: A damp cloth works wonders on the housing of the tool. Avoid saturating it; just enough to eliminate grime will do.
- Inspect for Damage: As you clean, take a moment to inspect all components for wear and tear. It's far easier to catch issues early than to deal with them when they escalate.
Ensuring thorough cleaning is done each time will help maintain the integrity of your Dremel tools, leaving them ready for your next crafting adventure.
Storage Guidelines
Storing your Dremel tools properly can sometimes be overlooked, but it plays a crucial role in their longevity. What’s the point of having tools if they are going to rust away in the dark corner of a garage? Here are some key storage considerations:
- Cool, Dry Location: Tools thrive in environments free from moisture. Storing in a dry area prevents rust and corrosion from taking over. A tool chest or cabinet works well for this.
- Organized Storage: Keeping tools organized not only saves time but also minimizes the risk of accidental damage. Use dividers to separate your various Dremel attachments and accessories.
- Avoid Heavy Loads: Don't pile things on top of your Dremel tools. Weight could lead to warping or other damage that’ll affect how they operate.
- Use Protective Cases: If possible, invest in hard cases for your Dremel and its accessories. They provide an excellent layer of protection from external damage.
By attending to these guidelines, you ensure that your Dremel tools remain in peak condition, ready to deliver flawless results the next time you embark on your wet sanding journey.
Remember: A well-maintained tool speaks volumes about the quality of work it can help you achieve.
Advanced Techniques in Wet Sanding
When it comes to perfecting finishes through wet sanding, having a repertoire of advanced techniques can elevate your craftsmanship. These methods allow for unique manipulation of textures and surface quality, ensuring that tailored results are not just a dream but a reality. Incorporating advanced techniques not only enhances the aesthetic appeal of pieces but also introduces a level of sophistication that resonates with the discerning eye, particularly among rock and fossil collectors.
Creating Unique Textures
Pattern Sanding
Pattern sanding is an artful process that goes beyond mere surface smoothing. It introduces deliberate designs and patterns that enhance the texture of the material being worked on. This technique is especially useful for those who want to add a personal touch to their projects, allowing for distinct and individualized designs that can attract collectors and enthusiasts alike.
One key characteristic of pattern sanding is the variance in sanding pressures and movements, which creates a unique finish that evokes depth and contrast. This not only makes pieces visually interesting but also functional, as it may enhance grip on objects that require a tactile element. The choice of patterns can range from simple stripes to complex geometric designs, offering an artist myriad options depending on their vision.
However, it’s worth noting that while pattern sanding can yield stunning results, it might require a bit of practice to perfect. Misalignment or uneven pressure can lead to unintended outcomes. Thus, the technique demands a steady hand and a sharp eye for detail.
Layered Finishes
Layered finishes represent a holistic approach to wet sanding, combining various grits and techniques to create a depth that shines through in the final product. This layering effect can amplify the inherent colors and textures of the material, giving it a multi-dimensional look that stands out. Layering can effectively highlight intricate details in fossils or beautifully banded rocks, accentuating their natural beauty.
The primary characteristic of layered finishes involves the blending of grits, each contributing something different to the overall appearance. Starting with coarser grit and gradually moving to finer options brings out details while maintaining a smooth surface. This method is particularly beneficial for collectors looking to showcase unique features in their specimens.
Nevertheless, achieving the ideal layered finish can be somewhat labor-intensive and time-consuming. Each layer necessitates careful application and thorough drying time before proceeding to the next stage, meaning patience is key. The payoff, however, is a beautifully polished and detailed piece that stands as a testament to the crafter’s diligence.
Incorporating Compounds
Polishing Compounds
Polishing compounds play a crucial role in achieving that coveted luster in wet sanding projects. These compounds, often made from fine abrasives suspended in a wax or oil base, add a glossy sheen to surfaces, making them appear more refined and professionally finished. For rock and fossil collectors, this can be especially important, as the visual appeal greatly enhances the perceived value of a specimen.
The key characteristic of polishing compounds is their ability to fill in microscopic scratches left by sanding, thereby smoothing out surfaces and leaving a brilliant finish. Those who use these compounds often find that even the dullest of rocks can be transformed into sparkling gems.
However, one should tread carefully; using too much compound can result in an overly slick surface that might hide essential features of the material. Balance is essential here to ensure that the natural beauty of the piece remains intact while still benefiting from a polished look.
Chemical Enhancers
Chemical enhancers are another innovative aspect that can refine the wet sanding process. These are often specially formulated solutions that react with the surface of the materials being worked on, intensifying colors or enhancing the textural presence of the piece. This aspect can be especially valuable in the world of rock and fossil collection, where showcasing the true essence of the material is critical.
The defining feature of chemical enhancers is their unique ability to penetrate surfaces, elevating their visual appeal without altering their natural state. When used effectively, they can draw out the vibrant colors in minerals or fossils that might otherwise go unnoticed.
Bear in mind that chemical enhancers may require some caution. Not all materials react the same way, and inappropriate use can lead to unwanted effects. Always do a small test patch before applying on a larger surface to avoid potential missteps.
In summary, employing advanced wet sanding techniques like pattern sanding, layered finishes, and the incorporation of polishing or chemical compounds can significantly elevate the craftsmanship involved in working with rocks and fossils. A thoughtful integration of these methods brings out the beauty and uniqueness of every piece, enhancing not only its visual appeal but also its intrinsic value to collectors.
By familiarizing yourself with these techniques, you position yourself not just as a crafter, but as an artist bringing nature’s wonders to life.