Dopping Wax in Lapidary: A Detailed Guide
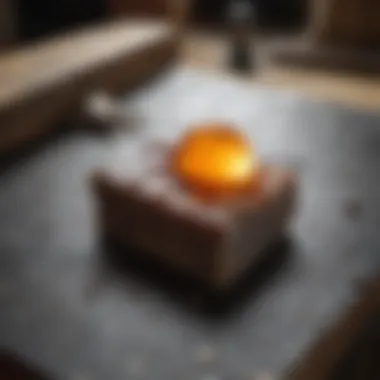
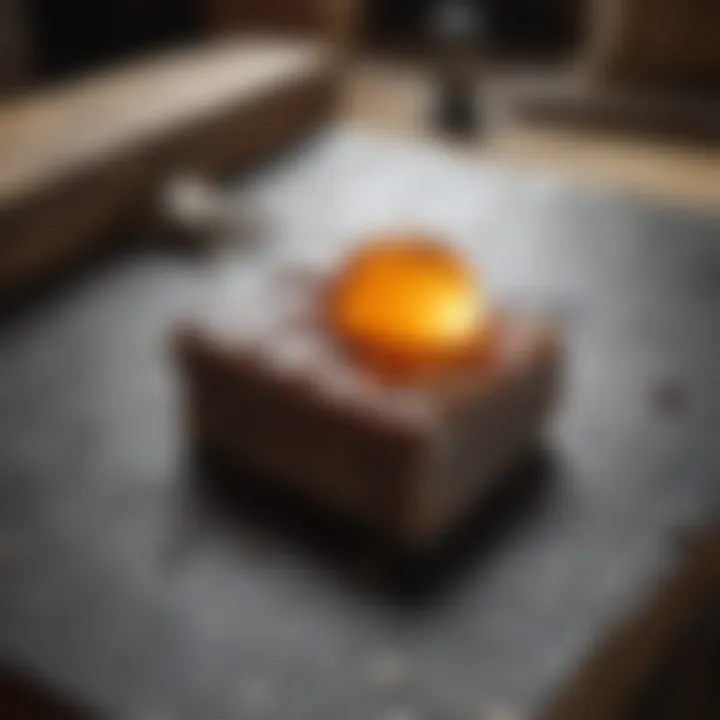
Intro
In the realm of lapidary arts, the beauty of gemstones is not solely derived from their natural brilliance. A crucial player in transforming rough stones into polished wonders is the dopping wax. Often overlooked, this wax functions as a reliable adhesive that connects the gem to a dop stick, facilitating the cutting and shaping process. In this exploration, we’ll break down what dopping wax is, the various types available, how to select the right one, and essential techniques for its effective use.
Understanding dopping wax not just enhances your skills but also enriches appreciation for the art of lapidary work. By delving into its applications and wise practices, this guide is tailored for both amateur hobbyists and seasoned professionals alike, keen to master their craft with perfection.
Types of Dopping Wax
Overview of Wax Categories
Dopping wax can be categorized into several types, each serving specific purposes. The primary classifications include:
- Natural Wax: Sourced from plant-based materials, offering a traditional option with desirable adhesion properties.
- Synthetic Wax: Often manufactured, it tends to provide consistency and durability.
- Low-Temperature Wax: Ideal for more delicate stones, melts at lower heat, thus preventing damage during the dopping process.
- High-Temperature Wax: This type is best suited for harder materials, needing more heat to bond.
In-Depth Look at Each Type
1. Natural Wax
This wax serves as a hallmark for many traditional lapidary methods. The adhesion quality often surpasses its synthetic counterpart in many cases. However, the supply might fluctuate since it relies on natural resources, increasing its unpredictability.
2. Synthetic Wax
With advancements in technology, synthetic wax has gained a reputation for its reliability. Manufacturers produce it in various colors and formulations, making it adaptable for different gemstones. Though cost-effective, it may not replicate the nostalgic feel of natural wax.
3. Low-Temperature Wax
Considered a preferred choice for softer stones like opals and turquoise, this wax melts easily. Jewelers often use it when working with intricate shapes, providing optimal control and safeguarding the cabochons.
4. High-Temperature Wax
This type stands up to greater heat, making it suitable for challenging materials such as quartz or diamond. It is essential to apply it with care; one must ensure an appropriate temperature to avoid chipping or ruining the gem.
"When selecting the right dopping wax, consider the stone's material and how much heat it can withstand. Know your gems, and the wax will follow."
Factors Influencing Wax Selection
Choosing the right type of dopping wax requires consideration of several factors:
- Gemstone Material: Softer stones need low-temperature waxes, while harder ones work best with high-temperature varieties.
- Working Technique: Some artisans prefer quick-melt wax for efficiency; others opt for longer set times for precision.
- Environmental Elements: Factors like ambient temperature and humidity can impact wax performance.
By understanding these factors, one can switch from trial and error to a more informed approach, thereby saving time and enhancing results.
Maintenance Tips for Dopping Wax
Just like any tool in the lapidary kit, proper care ensures the longevity of your dopping wax. Here are some pointers:
- Store Correctly: Keep wax in a cool place away from direct sunlight. This prevents melting or changing properties.
- Reuse Cautiously: While old wax can be reused, look for cracks or impurities before applying it to new projects.
- Apply with Precision: Avoid over-heating, as this can tamper with both wax and the gemstone.
Ultimately, dopping wax serves as a silent partner that plays a pivotal role in lapidary practices. By understanding its types, application techniques, and maintenance tips, enthusiasts can achieve stone-polishing perfection!
Understanding Dopping Wax
In the realm of lapidary practices, dopping wax stands as a pivotal component that often doesn't get the spotlight it deserves. This article takes a deep dive into this seemingly mundane substance, exploring all facets of its use, significance, and versatility in gemstone cutting and polishing. Having a solid grasp on dopping wax paves the way for smoother, more efficient lapidary work.
Definition of Dopping Wax
Dopping wax is a specialized adhesive material used in the art of gemstone shaping and polishing. It allows lapidarians to securely attach rough stones to a rod or stick, enabling precise control during the cutting and grinding processes. Typically, this wax is a blend of resins and waxes, designed to provide just the right amount of stickiness and malleability. Unlike a standard glue that can be overly rigid or prone to breaking under stress, dopping wax offers flexibility—important when working with delicate materials.
The texture of dopping wax varies, depending on the specific type used. Some formulas are softer and easier to shape, while others are firmer and can withstand higher temperatures. Understanding how these characteristics affect performance is crucial for both hobbyists and professionals alike. Choosing the right dopping wax hinges on factors like the type of stone being worked on and the specific techniques employed throughout the lapidary process.
History of Dopping Techniques
The origins of dopping techniques can be traced back centuries. Early lapidarians employed natural substances like beeswax to attach stones to tools, a method effective yet limited in terms of performance and adaptability. As civilizations advanced, so did the materials used in gemstone cutting. Various cultures have their unique stories of how dopping wax evolved; for instance, ancient Egyptians utilized simple dopping methods that laid the groundwork for contemporary practices.
Dopping really picked up momentum during the 19th century, especially in Europe and America, with industrial advancements providing access to more sophisticated materials. Understanding this history is vital as it highlights not only the evolution of tools and methods but also how user feedback influenced advancements in dopping wax formulations. Just like a fine wine, the quality of dopping wax comes from a long and celebrated tradition of craftsmanship and innovation.
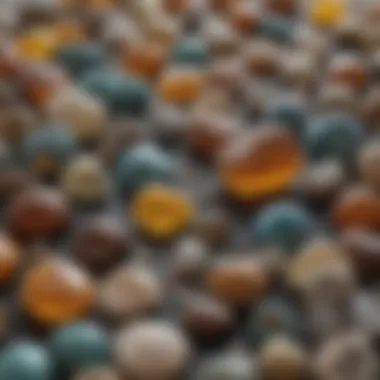
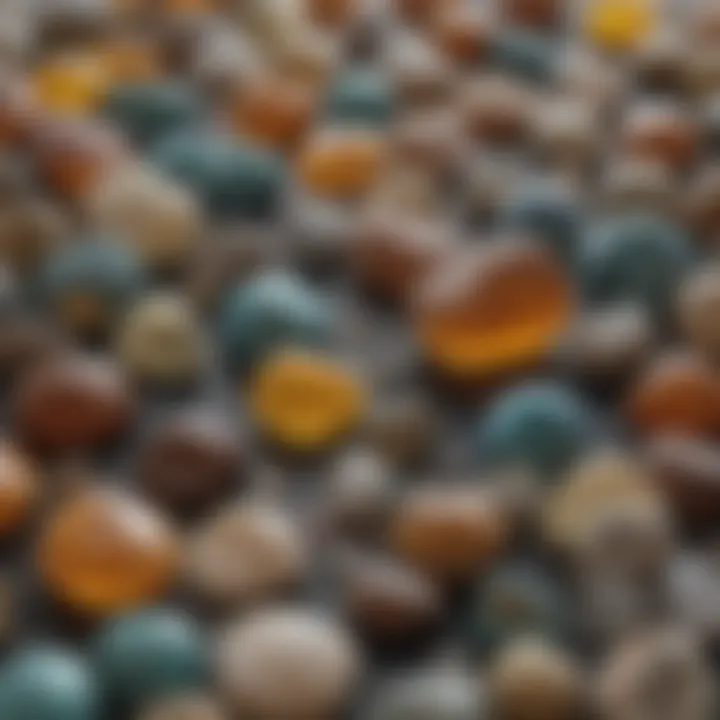
Importance in Lapidary Work
Dopping wax serves multiple essential functions in lapidary work, making it integral to the craft. Firstly, it promotes safety by securing gemstone pieces, reducing the risk of slips and accidents while utilizing cutting tools. Moreover, it allows for versatility; whether you're shaping a fragile opal or grinding a robust agate, having the right wax can enhance your control over the lapidary process.
Here are some key points illustrating its importance:
- Enhanced Precision: By stabilizing gemstones during the cutting phase, lapidarians can achieve accurate angles and smoother finishes.
- Easy Removal: Quality dopping wax allows for straightforward disengagement from the stone afterward, a huge bonus for those working with valuable materials.
- Increased Longevity of Tools: When used correctly, high-quality dopping wax helps minimize wear and tear on both the gemstone and the cutting tools, extending their lifespan.
"A craftsman only shines when products reflect their skill. In this sense, dopping wax is not mere accessory, but essential arsenal."
Types of Dopping Wax
When it comes to lapidary work, understanding the different types of dopping wax is essential. Each type serves a unique purpose, and knowing their specific properties can significantly enhance your crafting experience. From traditional to synthetic options, the right choice can make all the difference between a challenging task and a smooth workflow. Selecting the appropriate dopping wax impacts both the quality of your finished piece and efficiency of your work process.
Traditional Dopping Waxes
Traditional dopping waxes have been around for quite some time. Made from natural resins and waxes, they are appreciated for their simplicity and effectiveness. Many lapidary enthusiasts still favor these options due to their historical significance and reliability.
One of the most common types of traditional dopping wax is made from beeswax. It provides good adhesion to gemstones which is crucial when you're shaping or polishing. Another option is shellac, which is known for its impressive holding ability and ease of manipulation.
The primary advantage of these waxes is their easy application. They can be warmed up slightly using a heat source and molded around the stone reasonably quickly. This quality makes them particularly well-suited for those who enjoy hands-on, craft-focused work. However, be aware that traditional waxes often have temperature limits. They can soften too much in high heat, which is a concern depending on the working environment.
Synthetic Dopping Waxes
On the flip side, synthetic dopping waxes have gained popularity over the years, primarily due to their enhanced performance characteristics. These waxes are often formulated to include additives that improve their adhesion properties and make them heat resistant.
Epoxy-based waxes have become a favorite among lapidary professionals. They offer excellent durability and a strong bond to various gem types. They can withstand higher temperatures compared to their traditional counterparts, making them ideal for extended working sessions or challenging materials.
Also, you’ll find thermoplastics among synthetic options. These can be softened and reshaped multiple times by applying heat. This is beneficial for those who might need to adjust the positioning of the stone during various steps of the lapidary process.
While synthetic waxes can be more expensive, their consistent performance under a variety of conditions often justifies the cost.
Comparative Analysis of Types
In comparing traditional and synthetic dopping waxes, there are several factors to take into account.
- Adhesion: Traditional waxes tend to bond well with certain stones, but synthetic options often provide a stronger and more reliable bond overall.
- Heat Resistance: Synthetic waxes usually outperform traditional ones in high heat scenarios, allowing for a wider range of working conditions.
- Manipulation: Traditional waxes are often easier and quicker to set up, especially for beginners, while synthetic waxes may require more precision and care during application.
- Cost: Generally, traditional options are more budget-friendly, but the longevity and durability of synthetic waxes might save you money in the long run as they require less frequent replacement.
Determining the right type of dopping wax is crucial. Each serves a unique role, and your choice could enhance creativity while crafting or present challenges to your lapidary process.
In essence, the choice between traditional and synthetic dopping wax really comes down to personal preferences, working conditions, and the specific requirements of the materials you're working with. Each type offers its own set of advantages and disadvantages, so it’s beneficial to experiment and find the one that aligns with your technique and materials.
Selecting the Right Dopping Wax
Choosing the appropriate dopping wax is pivotal in achieving quality results in lapidary work. Each type of wax offers different properties and advantages, making it crucial to understand them before embarking on your project. The right wax not only facilitates better adhesion between the gemstone and dop stick but can also enhance the overall working experience.
Factors to Consider
When selecting dopping wax, there are several important factors to keep in mind:
- Type of Stone: Different gemstones have varying hardness levels. Softer stones may require a wax that offers gentle grip, while harder stones need a firmer hold.
- Working Temperature: Some dopping waxes perform better at certain temperature ranges. Consider your workspace environment when making a choice.
- Setting Time: The time it takes for the wax to set is crucial, especially when working on intricate pieces. A faster setting wax can be beneficial for efficiency.
- Reusability: Some dopping wax types can be melted and reused, while others may break down after a single application.
- Environmental Impact: Consider if the materials used in the wax align with your values regarding sustainability and environmental health.
Matching Wax to Materials
Finding the right match between wax and the gemstones you are working with can feel like pairing fine wine with cheese; the right combination elevates the entire experience. Here’s how to align the two effectively:
- For Soft Stones: If you're working with softer, more delicate stones like alabaster or some varieties of opal, choose a wax that has a lower melting point. This way, you can ease into the dopping process.
- For Hard Stones: Stones such as granite or sapphire require a robust wax that can withstand more rigorous processing. A high-temperature synthetic wax might be your best bet here.
- Special Material Considerations: Antique gemstones or stones with special treating might require specific wax formulations that cater to their unique characteristics. Always check with suppliers for tailored recommendations.
Application-Specific Recommendations
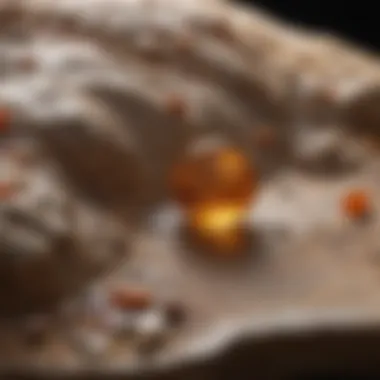
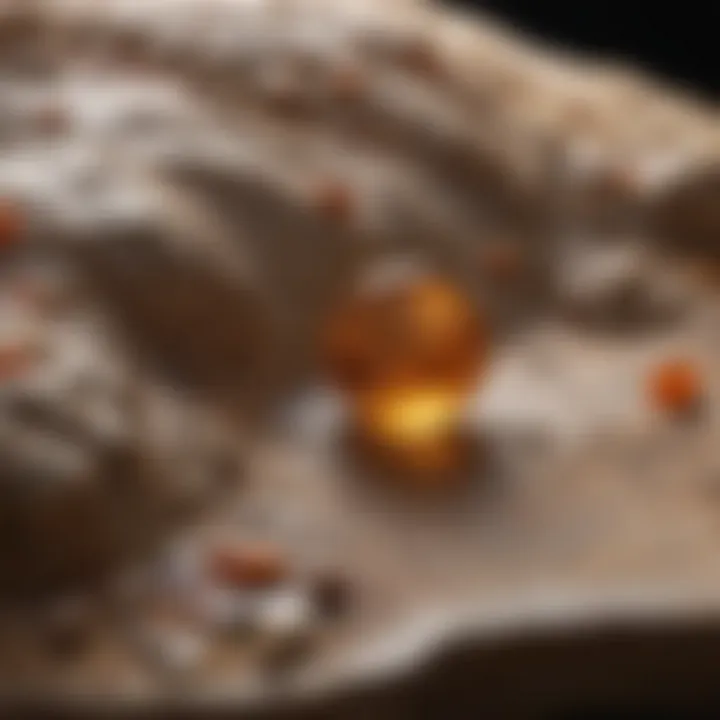
Different applications call for different wax properties. By tailoring your wax choice to the specific project at hand, you can be sure to achieve optimal results. For example:
- General Lapidary Work: Standard paraffin-based dopping wax is a reliable all-around option for most amateur works.
- Intricate Detail Work: For fine detailing, you might want to explore a blend that melts at lower temperatures, allowing for adjustments and reapplication without damaging the stone.
- Heavy Duty Uses: If tackling high-impact projects, opt for synthetic waxes that can endure more force without degrading, ensuring your stones remain secured throughout the process.
"The right dopping wax can make or break your lapidary project. It's worth taking the time to understand the various types to maximize your success".
By considering these aspects when selecting the appropriate dopping wax, you can significantly improve the efficiency and quality of your lapidary work. This process enhances both the craftsmanship involved in lapidary while ensuring a smoother working experience.
Techniques for Using Dopping Wax
Using dopping wax effectively is a cornerstone of successful lapidary work. It’s not just about sticking a stone onto a stick; it involves skills and techniques that can make or break a piece. Proper technique ensures that the wax holds the gemstone securely during shaping and polishing, which avoids frustrating mishaps that can damage the workpiece. Each technique plays a significant role — from preparing the setup, applying the wax, to the final steps of cooling and setting — mastering these will undoubtedly improve both the quality of your work and your overall efficiency.
Preparing the Dopping Setup
Before applying wax, it's crucial to have your setup ready. Start by gathering all necessary tools and materials. You should have your gemstones, dopping sticks, and of course, the dopping wax at hand.
- Choose the Right Dopping Stick: Wooden sticks or metal pins are your best bet. Make sure they are clean and free of any debris.
- Clean Your Gemstone: Any dirt or grease can hinder the adhesion of the wax. Use a mild soap and water solution to clean it. Pat it dry gently.
- Heat the Wax: Depending on the type of wax, you might want to warm it slightly. Just enough to soften, not melt it completely. This can be done using a heat gun or placing it in a double boiler.
Once you have everything organized, consider the layout. A stable workstation minimizes distractions and keeps your focus on the task at hand.
Effective Wax Application
Now comes the crucial part. Applying the wax properly not only helps secure the gemstone but also allows for an easier removal later.
- Apply the Wax Generously: Don’t skimp on the wax. A thick layer provides a more stable bond. Brush or spread it uniformly over the dopping stick end where you'll attach your stone.
- Position the Stone Correctly: Press the gemstone onto the dopping stick, ensuring it aligns properly. A misalignment can lead to uneven cuts and polish.
- Twist for Good Adhesion: Once the stone is in place, twist it gently while pushing it down into the wax. This ensures that the wax seeps around the stone, creating a stronger bond.
It’s advisable to take your time during this stage; skipping steps will likely lead to frustrations later on.
Cooling and Setting Techniques
Once you've applied the wax and placed the stone, you’ll need to let everything set. Cooling is just as important as the application itself.
- Avoid Rapid Cooling: Don’t rush by throwing the piece into the freezer. Rapid changes in temperature can cause the stone to crack. Instead, let it cool naturally at room temperature.
- Check for Stability: Once the wax has cooled, check the attachment. It should feel solid. If not, consider reapplying the wax, especially if you’re dealing with larger stones.
- Use Heat Wisely: For removal later, heat the dopping wax again to soften it. Use a heat gun or warm water bath to enable a quicker release without risking damage to the stone.
Understanding these techniques around dopping wax not only elevates one's lapidary skills but also fosters a greater appreciation for the craft. The process can be nuanced, but with patience and practice, mastery is within reach.
Safety Considerations
When working with dopping wax in lapidary processes, safety should never be an afterthought. The materials, heat sources, and tools involved pose several risks that, if not adequately managed, can lead to injuries or accidents. Creating a safe and secure working environment ensures that the experience remains enjoyable and productive for enthusiasts and professionals alike.
Handling Dopping Wax Safely
Dopping wax, while essential for proper handling of stones, can be hazardous if not treated with respect. Here are key considerations to keep in mind:
- Heat Sensitivity: Dopping wax is applied to heated tools, and it’s important to handle these tools with care. Always use heat-resistant gloves or tools to prevent burns.
- Melting Point Awareness: Different waxes have unique melting points. Take note of these when selecting your wax to avoid overheating, which can cause the wax to smoke or degrade.
- Spills and Residue: Be mindful of any wax residue that may end up on your working surface. This can make surfaces slippery, posing a tripping hazard. Clean up any spills immediately using paper towels or a suitable cleaning solution.
- Proper Disposal: When you’re finished with excess wax or if it has reached the end of its useful life, dispose of it in accordance with your local regulations. Avoid flushing it down drains, as it can clog plumbing.
Workspace Safety Measures
A well-organized workspace can significantly reduce risks associated with the use of dopping wax. Consider these tips for maintaining a safe environment:
- Designated Work Area: Establish a specific area for your lapidary work, free from distractions. This should ideally have good ventilation to dissipate any fumes released by heated materials.
- Appropriate Lighting: Ensure your workspace is bright enough. Poor lighting can lead to accidents as you may misjudge where tools and materials are placed.
- Emergency Equipment: Keep a first-aid kit handy and know where it is located. In case of burns or cuts, quick access can make all the difference.
- Wear Protective Gear: Goggles and gloves should be a staple in your lapidary toolkit. These protect your eyes from small flying debris and your hands from sharp tools and hot materials.
"A little bit of precaution goes a long way in ensuring a safe lapidary experience."
By adopting these safety measures alongside proper handling techniques, you not only protect yourself but also enhance the overall quality of your work. Collectors and hobbyists must prioritize safety to ensure a positive and productive encounter in their lapidary pursuits.
Maintenance Tips for Dopping Wax
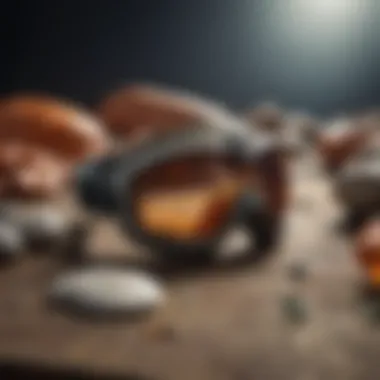
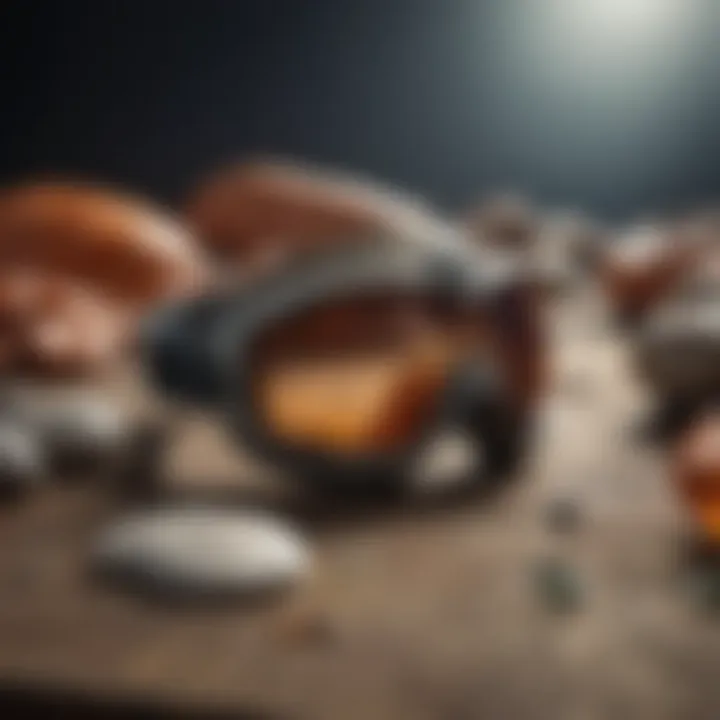
Maintaining dopping wax is crucial for ensuring effective lapidary work. A well-kept wax not only enhances the quality of gemstone shaping but also prolongs the lifespan of tools and materials involved. Lapidary work requires precision, and any slip-ups can lead to wasted materials and time. Proper maintenance can help mitigate such risks, keeping your workflow smooth and efficient.
Cleaning and Storing Wax Properly
Cleaning dopping wax might seem trivial, but neglecting this task can lead to significant issues down the line. Wax can accumulate dust, debris, or even remnants of previous projects. These contaminants can affect adhesion and, consequently, the overall effectiveness of the dopping process.
To clean your wax:
- Use a soft cloth: Gently wipe away dust and debris without scratching the surface.
- Mild solvents: If necessary, a mild solvent will help to dissolve any stubborn residues. Just keep the application light—too much solvent can disrupt the wax's integrity.
- Store in a cool place: Ensure that your dopping wax is kept in a stable environment, away from extreme heat or direct sunlight. Extreme temperatures can alter the chemical properties of the wax, leading to degradation over time.
When it comes to storage, consider using airtight containers. This practice will protect the wax from contaminants and moisture. Remember, moisture can lead to unwanted wax clumping, making application difficult when the time comes to use it again.
Recognizing When to Replace Wax
Being aware of when to replace your dopping wax is central to maintaining a streamlined lapidary process. Wax doesn’t necessarily last forever, and over time it might lose its effectiveness. Here are some signs indicating that it's time to consider a replacement:
- Cracks or chips: Any visible signs of physical damage mean the wax will likely not adhere well.
- Dull appearance: Fresh dopping wax usually has a certain sheen. If the wax looks too matte or patchy, it might not perform optimally.
- Loss of adhesiveness: If stones start to detach during polishing or shaping, you can bet the wax might be past its prime.
Regularly evaluating your dopping wax for these indicators will help maintain the quality and efficiency of your lapidary work. Investing a little time in maintenance can yield significant dividends in the long run!
Dopping Wax in Professional Settings
In the realm of lapidary, the use of dopping wax extends well beyond mere convenience; it’s a cornerstone of professional gem cutting and polishing. As lapidaries seek perfection in their craft, understanding the role of dopping wax in professional settings becomes crucial. For serious craftsmen and artists alike, insight into the specificity of wax applications can elevate their work to a new level. This section unpacks the nuances that underscore the importance of dopping wax, from industry standards to cutting-edge innovations.
Industry Standards and Practices
Dopping wax is not just a batch of melted substance; it is governed by certain standards that dictate its effectiveness. In professional lapidary operations, standards like ISO 9001 emphasize quality management principles which include consistent outcome quality and improved operational efficiency. Professionals are expected to select dopping wax that aligns with materials they are working on, ensuring durability and precision in their work.
Moreover, certain practices have become norms in professional lapidary circles. For instance, the temperature control during the wax melting process is often monitored with thermometers to avoid overheating, which can compromise the wax's properties. High-grade dopping waxes, like those from brands such as Auld Dopping Wax and Scully Wax, are preferred in workshops due to their consistency and reliability.
A few key points that illustrate the industry standards include:
- Consistency: Dopping wax must maintain uniform properties across batches to ensure predictability in application and performance.
- Compatibility: The wax should be compatible with various gemstones, allowing for different levels of adhesion depending on the material properties.
- Transparency: For lapidaries working with colored stones, using a transparent dopping wax helps in maintaining visual clarity, thereby avoiding any aesthetic discrepancy in the final product.
"When you use quality dopping wax, you're not just adhering a stone to a stick; you're setting the stage for a masterpiece."
Innovations in Dopping Wax Use
In recent years, advancements have taken the world of dopping wax beyond its traditional applications. The advent of synthetic waxes has opened doors to possibilities that were once considered unattainable. New formulations are continuously being developed to enhance adhesion, improve cooling times, and reduce the environmental impact—an important consideration in a world becoming increasingly conscious about sustainability.
For instance, some companies have introduced non-toxic, biodegradable waxes that maintain functionality without compromising safety. This shift speaks volumes to the changing values of craftspeople who not only seek to perfect their art but also protect the planet.
There’s also been a notable integration of digital technologies into the lapidary process. Lapidaries can now utilize temperature sensors and automated heating devices to maintain precise control during the dopping process, ensuring that the wax reaches optimal melting points, particularly when using polymer-based or specialized waxes.
Furthermore, industry leaders are increasingly investing in research and development to refine the properties of dopping wax. Efforts are focused on creating waxes that cure faster and adhere better under various conditions, making them more adaptable to diverse gem types.
In summary, from stringent industry standards to innovative breakthroughs, the landscape of dopping wax in professional settings continues to evolve. As lapidaries embrace these changes, the quality and diversity of their work will undoubtedly flourish.
Closure
In wrapping up this exploration of dopping wax within the realm of lapidary, it becomes evident that this seemingly simple tool is pivotal in enhancing the quality of gemstone work. Its versatility and effectiveness cannot be overstated. Whether you are a seasoned professional or just starting out in the hobby, understanding the nuances of dopping wax is essential for achieving the best results in your projects.
Summarizing Key Points
To revisit some key elements discussed:
- Dopping wax serves as a crucial adhesive that secures gemstones to dop sticks, enabling precise shaping and polishing.
- Two main categories of dopping wax exist: traditional and synthetic, each with unique benefits and applications.
- Selecting the appropriate wax is fundamental for ensuring compatibility with various materials, affecting the overall outcome of your lapidary work.
- Safety and maintenance tips can prolong not just the life of the dopping wax but also enhance your working environment, ultimately promoting better results.
This understanding arms you with the knowledge needed to troubleshoot common challenges, select suitable products, and apply techniques effectively. Mastering these elements can lead to significant improvements in both the quality and enjoyment of your lapidary endeavors.
Future Directions in Lapidary Tool Use
As the world of lapidary art continues to evolve, so do the tools and practices involved in it. Future advancements could likely focus on the application and formulation of dopping wax, incorporating smarter materials that adapt better to different gemstone types and working conditions. We may witness an emergence of eco-friendly options that reduce the environmental impact of our craft while maintaining or even enhancing performance.
Additionally, education plays a vital role. Workshops and online forums, such as those on Reddit or specialized Facebook groups, could foster a community where artisans share insights about innovative techniques and experiences using dopping wax. Such interactions could lead to shared discoveries that push the boundaries of traditional practices.