DIY Lost Wax Casting: A Collector's Guide to Crafting

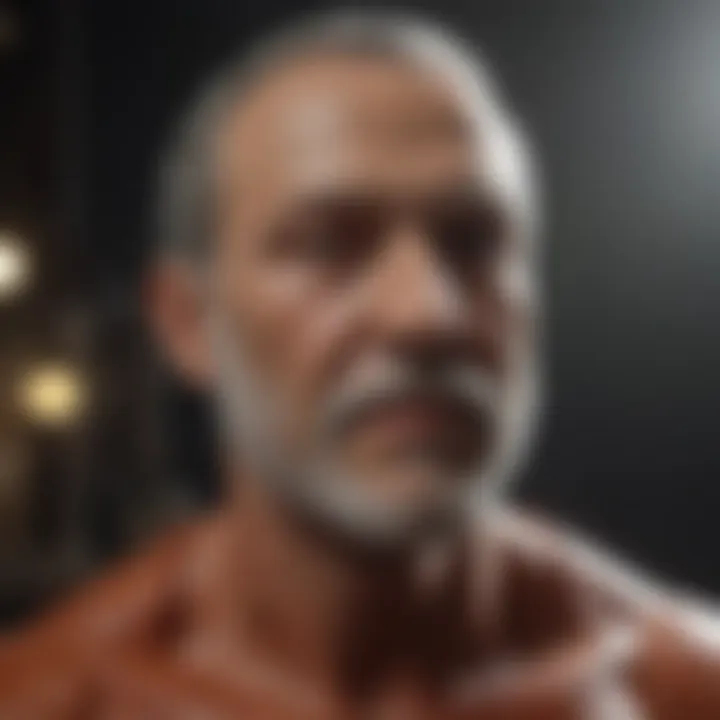
Intro
In the world of artistry and craftsmanship, few techniques possess the rich historical legacy and intricate beauty of lost wax casting. This age-old method is instrumental for collectors aiming to create pieces that are not only visually captivating but also imbued with personal meaning. From jewelry to elaborate sculptures, lost wax casting offers a unique way to transform raw materials into timeless collectibles.
Understanding the process of lost wax casting is akin to peeling back layers of history, culture, and skill. Each piece tells a story, allowing collectors to engage deeply with their creations. This guide is designed to empower enthusiasts of all skill levels, providing them with the knowledge to embark on their own casting adventures. We’ll explore the materials and tools required, discuss safety precautions, and share practical advice that ensures you not only survive the creative journey but thrive in it.
Whether you’re seeking to craft a stunning pendant or an ornate sculpture, this guide will assist in navigating the complexities of the lost wax technique. Let’s dive into the various aspects of this fascinating process, and perhaps, by the end, you’ll find yourself inspired to create something remarkable.
Intro to Lost Wax Casting
Lost wax casting is a time-honored technique, one that stands as a bridge between ancient artistry and modern craftsmanship. The importance of this method arises not just from its historical roots but from its remarkable ability to create intricate and detailed works of art. For collectors, understanding lost wax casting enhances their appreciation for the craftsmanship that goes into every piece. This section will provide an overview of its historical context and significance in collectible arts, setting the stage for why this technique is so valuable to both artisans and enthusiasts alike.
Historical Context
Lost wax casting, or cire perdue, has its origins in ancient civilizations. Evidence shows it was practiced as far back as the 3rd millennium BCE, with cultures like the Egyptians and the Mesopotamians employing the method for both functional and ceremonial objects. Artisans would sculpt an original model in wax, surrounded by a clay or plaster mold, allowing for the casting of metal after the wax was melted away. This technique not only allowed for fine detail but also for the mass production of similar objects. Interestingly, the technique traveled through cultures; the Greeks and Romans perfected it, leading to the creation of remarkable sculptures and decorative objects. In its essence, it’s a method steeped in centuries of innovation and artistic expression.
As these techniques evolved, they remained relevant in various forms through the Middle Ages. During the Renaissance, lost wax casting re-emerged with a flourish. Perhaps most notably, artists like Benvenuto Cellini galvanized this craft, showcasing its potential for creating not just utilitarian objects but breathtaking artistry. The historical context weaves a rich tapestry of human creativity, reflecting how a simple method of modeling can yield both beauty and significance through time.
Significance in Collectible Arts
For collectors, lost wax casting is more than a mere process; it symbolizes a connection to art history and to the artists themselves. Each piece tells a story; the unique imperfections and intricate details give individual character that speaks volumes about its origin. Collectibles created through this method often command high appreciation in art markets due to the skill and time involved in their production.
When discussing collectible arts, certain aspects elevate this technique:
- Uniqueness: Every cast from original wax can offer different qualities, making it rare.
- Craftsmanship: It showcases the skill of the artisan. Not all pieces can be replicated with identical finesse.
- Historical connection: Owning an item crafted through this ancient method is like holding a piece of history.
Moreover, lost wax casting extends its influence beyond just art and sculpture into jewelry making. Collectable pieces that are cast using this method can often provide insights into fashion, culture, and individual expression prevalent at the time of creation.
"Every piece created through lost wax casting emerges from a conversation between the artist and their materials, marking a lineage of creativity and craftsmanship."
Understanding the Basics of Lost Wax Casting
Understanding the basics of lost wax casting is crucial for anyone who wants to dive into the rich world of collectible arts. This ancient technique not only allows for the creation of intricate designs but also ensures that artisans can produce highly detailed pieces with precision. Whether you're a seasoned collector or a curious novice, grasping these foundational concepts will serve as the backbone for your crafting journey.
Key Concepts
To embark on your lost wax casting adventure, you first need to familiarize yourself with some key concepts. Here’s a few important ideas that provide essential groundwork:
- Wax Models: The process starts with creating a model out of wax. This model serves as a replica of the final product you wish to achieve. The art lies in how you shape and detail this wax piece.
- Investment Mold: Once your model is made, it’s covered in a special form of plaster known as investment. This creates a mold that maintains the model’s intricate details once the wax is melted away.
- Lost Wax Principle: The term "lost wax" comes from the fact that the wax model is melted and "lost" during the casting process, leaving a hollow cavity in the mold for the metal.
By grasping these concepts, you lay the groundwork for a successful venture into lost wax casting. Each component plays a significant role in the overall outcome, shaping both the process and the end product.
The Casting Process Overview
The casting process in lost wax casting is a delicate interplay of steps that culminate in a stunning final piece. Knowing how each phase operates will help you maneuver through your crafting with confidence.
- Creating the Wax Model: The first step involves sculpting the model you want to cast. This step is where you can express your creativity and ensure detail.
- Mold Creation: After your model is ready, the next step is creating the external mold from the investment. It requires careful pouring to avoid bubbles and imperfections.
- Wax Removal: The mold then undergoes heating, which melts away the wax completely. This makes way for the metal to fill in the void left behind.
- Pouring Metal: Once the mold is prepared, molten metal is poured into the cavity. Timing and temperature are essential here – it's not just about pouring, but pouring right.
- Cooling and Finishing: Lastly, after cooling, the mold is broken open to reveal the cast piece. This is where finishing work begins, enhancing the beauty and removing any imperfections.
Investing time to understand each phase prepares you for the unique challenges you may encounter; it underscores the meticulous nature of the craft. With practice, patience, and an eagerness to learn, embracing lost wax casting could very well become your new passion. It's not just a process; it’s an exploration of art, technique, and personal expression.
Necessary Tools and Materials
When venturing into the realm of DIY lost wax casting, the selection of appropriate tools and materials stands as a cornerstone of the entire process. The success of your creation hinges not just on your artistic prowess but also on the quality and suitability of the items you put to use. In this section, we'll delve into essential components that every aspiring artisan should have, along with their significance during the casting process.
Wax Types and Properties
Choosing the right type of wax is like picking the right paint; it can make or break your piece. Various waxes are available, each with unique properties that influence the final quality of your cast.
- Paraffin Wax: Commonly used for beginners, it's easy to work with and melts at a relatively low temperature. However, it can be less detailed when it comes to complex designs.
- Specialty Wax: Some waxes are formulated for specific casting techniques. For instance, sculpting wax allows for detailed work with added durability. They're usually more expensive but worth the investment for serious collectors.
- Blend Waxes: These combine different waxes to exploit the strengths of each. They can offer a good balance of meltability and detail.
These choices affect how well your model holds detail and maintains its shape during the casting process. Consider how fine the details you want to capture are and choose wax accordingly.
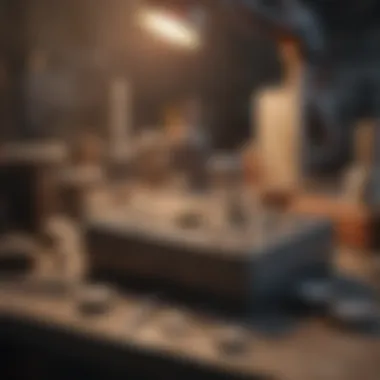
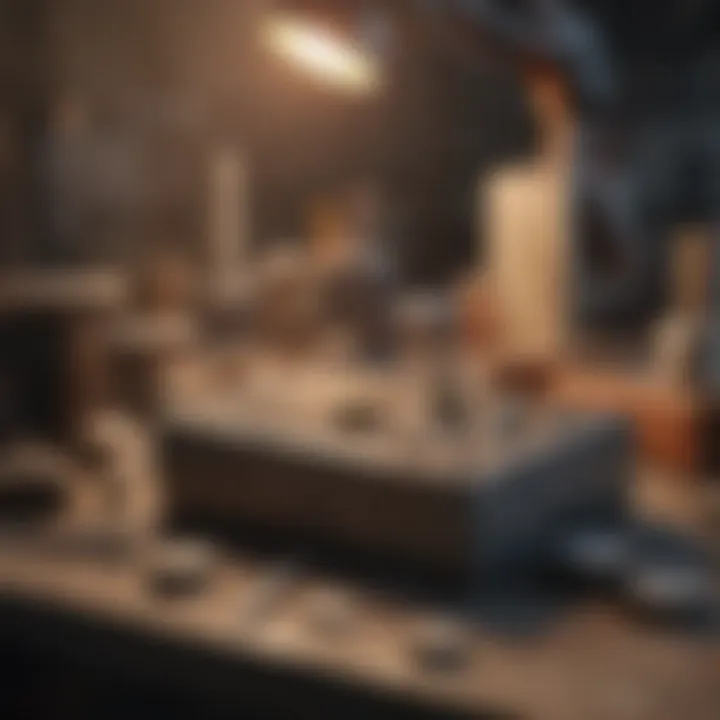
Molds and Their Construction
Molds are like the silent partners in your casting endeavor. They shape the molten metal into the desired form, so their construction can't be overlooked. There are several types of molds you might consider:
- Silicone Molds: Known for flexibility and detail capture, silicone molds allow for easy removal of the cast. They can handle heat well and make excellent repeated casts.
- Sand Molds: Often used in larger projects, they provide stability but may require more effort to construct. A disadvantage is the limited detail they capture.
- Investment Molds: These are typically used for more intricate work and are made from materials that withstand high temperatures.
- Homemade Molds: For those feeling crafty, creating your own molds using silicone or latex can not only save money but also enable customization. Not to mention, this allows you to experiment with designs.
Focus on the mold's ability to retain shape and withstand the heat of molten metal. Also, consider how you’ll release the final product—molds that fit snugly might hinder removal.
Heating and Pouring Equipment
When it comes to casting, having the right heating and pouring equipment is essential for achieving a successful pour without mishaps. This segment influences both safety and the quality of the casting you produce.
- Casting Furnace: A crucial investment, the furnace will melt your metal to the necessary temperature. Options range from small propane furnaces to more advanced induction furnaces, depending on your budget and needs.
- Crucibles: These specialized containers withstand high temperatures, holding the molten metal before it's poured. They come in various materials like graphite or ceramic, offering different benefits—graphite can be lighter, while ceramic might offer more durability.
- Pouring Tools: A ladle or pouring cup is key when moving the hot metal from the crucible to the mold. Opt for tools that are heat-resistant and allow for precision pouring to avoid overflows or drips.
Careful selection of this equipment will not only ensure a safer process but also enhance the quality of your final product. For instance, a great ladle can help prevent unwanted splatter when pouring.
"The difference between a good casting and a great casting often comes down to the tools you use."
In summary, when preparing to dive into lost wax casting, equipping yourself with the right tools and materials will make a world of difference. From discerning the appropriate wax type to constructing molds and investing in heating equipment, each choice you make aligns with your vision as a collector and artisan. Be prudent in your selections, as they directly affect the outcome of your creations.
Step-by-Step Guide to DIY Lost Wax Casting
The process of DIY lost wax casting can appear daunting at first glance, yet it opens a pathway to personal creativity and mastery in crafting unique pieces. Engaging in this technique allows artists and collectors alike to create one-of-a-kind items that reflect their individual style and vision. Moreover, mastering each step can not only boost a creator's confidence but also enhance the significance of their collections. Let’s break down this process into manageable steps, so you can dive into this rewarding craft more comfortably.
Creating the Original Model
Creating the original model is where the magic begins. This model can be crafted from various materials, commonly wax, clay, or even some soft metals. The main goal here is to carve a precise representation of the final piece you envisage. Use carving tools or even simple kitchen implements to sculpt your design. Think of it as making a prototype. You have the chance to play around with different shapes and sizes without the worry of permanent commitment. Therefore, if your first attempt goes awry, fear not! This is all part of the creative process.
Making the Mold
Once you're satisfied with your original model, the next step is creating a mold. This mold is what allows for multiple copies of your model. Two-part molds are very popular because they give better detail. Typically, you would encase your original model in a flexible mold-making material, making sure every detail is captured. When it comes to drying time, be patient. Rushed curing could lead to imperfections later, and nobody wants that.
"Taking your time during the mold creation process can save you a wealth of trouble down the line. The better the mold, the better your final product will be."
Preparing for Pouring
Before diving into pouring, there’s a bit of prep work to do. Clean your mold thoroughly—no dust or debris can ruin your efforts. Next, consider lubrication. Applying a light release agent will help your final piece come out easier. Once that’s done, make sure your metal casting material is melted to the ideal temperature for pouring. This step cannot be overlooked, as improper pouring temperatures can lead to defects, meaning more time wasted. Understand your metal's properties well. For instance, silver generally has a lower melting point than bronze.
Pouring the Metal
With everything prepped, it's showtime: pouring the metal! This can be one of the most exhilarating parts of the whole process. Carefully pour the melted metal into the mold, ensuring no air bubbles are trapped inside. If bubbles are spotted, gently tapping the sides of the mold can help release them. Make sure to pour steadily, keeping a watchful eye on the temperature—all elements need to harmonize in this symphony of casting.
Removing the Mold
Finally, once the metal has cooled and solidified, it’s time to unveil your new piece. Gently remove the mold, taking care not to damage your newly cast item. This is often an exciting moment; you get to see all your hard work take form at last. Inspect it for any flaws or details that may require further refinement. At this point, you’ll understand the importance of every preceding step, as each contributes to the final quality of your craft.
Engaging in the step-by-step guide to DIY lost wax casting not only provides a fruitful outlet for creative expression, but it also helps to foster a deeper appreciation for handcrafted artifacts. By following these simple yet comprehensive instructions, collectors and artisans alike can embark on a journey that renders them both artisans and custodians of unique, tangible art.
Common Applications of Lost Wax Casting
Lost wax casting finds its place in a variety of fields, with each application reflecting a unique aspect of creativity and utility. This section will examine the significance of lost wax casting, focusing on its role in jewelry making, sculptural arts, and industrial prototyping. Understanding the applications not only illustrates the versatility of the technique but also highlights its relevance across artistic and practical domains.
Jewelry Making Techniques
In the world of jewelry making, lost wax casting is a beloved method, allowing artisans to breathe life into their designs with remarkable precision. The ability to create intricate patterns and designs makes this technique especially appealing. Jewelers can sculpt detailed wax models, which capture every nuance, from delicate filigree to bold geometric shapes. Once the mold is crafted, pouring metal transforms those wax designs into stunning wearable art.
Key advantages include:
- Customizability: Each piece can be tailored to individual specifications, making personalized jewelry a cinch.
- Reproducibility: Artisans can produce multiple copies of a design with consistent quality, which is essential for larger orders.
- Material Compatibility: Lost wax casting works with various metals, including gold, silver, and platinum, each enhancing the final product's appeal.
Creating jewelry through this method also invites a deeper connection between the artist and the piece. By honing their skills to master this ancient craft, jewelry makers tap into decades of tradition, adding a layer of story to every pendant and ring.
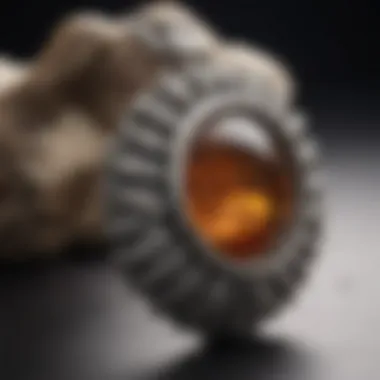
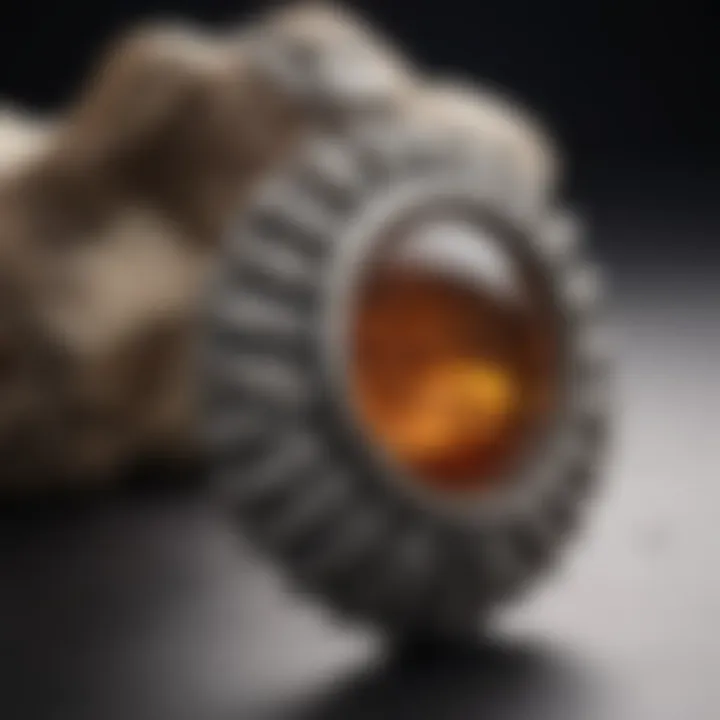
Sculptural Arts and Collectibles
For sculptors, lost wax casting serves as a gateway to transform ideas into tangible forms. Whether it's a life-sized statue or an intricate figurine, sculptors have found this technique invigorating. The casting process allows for remarkable detail, enabling artists to bring forth their visions with a level of precision unattainable by other means. The durability of cast metal lends permanence to sculptures, making them timeless pieces that can grace public spaces or private collections alike.
In addition to artistic expression, the collectibility aspect cannot be overlooked. Sculptures made using lost wax casting often gain value over time, driven by artistic reputation and the quality of craftsmanship. Collectors appreciate the uniqueness of each piece, often based on the artist's individual style and methodology, fostering a deep appreciation for both the art and the artist.
Industrial Uses in Prototyping
Beyond artistry, lost wax casting finds a home in the industry, particularly in prototyping. Engineers and designers often use this method to create detailed prototypes of components. The precision that comes with this casting technique ensures that prototypes reflect true dimensions, aiding in the development of intricate parts that require exact specifications.
Advantages of using lost wax casting in industrial prototyping include:
- Complex Geometry: The process allows for the creation of complex shapes that would be impossible to achieve through traditional machining methods.
- Material Integrity: The final products demonstrate high strength and structural integrity, making them reliable for various applications.
- Cost-Effectiveness: While initial setup may involve costs, the ability to reproduce high-quality components in bulk helps mitigate expenses over time.
These varied applications underscore that lost wax casting is not merely an artistic endeavor but a multifaceted tool that finds relevance in both creative and industrial spheres. Understanding its uses enriches one’s appreciation for the intricacies involved in the process and its outputs.
"Lost wax casting represents not only an art form but also a significant technological marvel, bridging the gap between creativity and functionality."
Challenges in Lost Wax Casting
Lost wax casting is a rewarding but intricate process, where each misstep can lead to less-than-desirable outcomes. Understanding the challenges involved is paramount for anyone serious about mastering this art. This section delves into the common pitfalls and defects that can occur during the casting process, as well as how to navigate them, ensuring your efforts result in beautiful and collectible pieces.
Common Pitfalls to Avoid
When engaging in lost wax casting, certain hurdles tend to trip up newcomers and even seasoned artisans. Here are some pitfalls you might face and tips on dodging them:
- Inadequate Wax Preparation: Not all waxes are created equal. Using the wrong type can lead to deformation or poor detail capture. Make sure you select a wax that matches your final product’s requirements.
- Mold Issues: If the mold isn't constructed properly, it can lead to cracks or incomplete casts. Pay attention to the mold-making process, ensuring a seamless and well-formed cavity that captures every intricate detail.
- Temperature Control: Metal needs to be heated to specific temperatures. No one wants a lukewarm pour! If the metal isn’t hot enough, the cast may contain imperfections; too hot, and you risk damage to your mold.
- Insufficient Venting: Bubbles can form if gases have nowhere to escape during pouring. Incorporate vents in your mold design, which allows trapped air to escape and results in a smoother finish.
- Neglecting Finishing Steps: Skipping out on the polishing and finishing stages can detract from the final piece's attractiveness. It’s like frosting a cake without decorating it—unimpressive.
Addressing Defects in the Final Product
Even the best-laid plans can result in defects. However, knowing how to recognize and address these issues can elevate your work from mediocre to magnificent. Here’s how to tackle some common defects:
- Air Bubbles: Often caused by inadequate venting, air bubbles can ruin the surface quality. If caught early, you might be able to melt and re-pour the piece.
- Shrinkage Marks: These occur when metal cools too quickly. To mitigate this, ensure a gradual cooling process. Some recommend keeping a heat source nearby to maintain warmth during the solidification phase.
- Surface Imperfections: If the outer layer appears rough, consider sanding or polishing the surface after casting. Using progressively finer grits can help achieve that sought-after shine.
- Missing Features: If your final piece is missing details, it likely relates to mold issues or wax preparation failures. Analyzing the issue often leads back to how the original model or mold was made.
"Every defect tells a story; learn from them, and your skills will grow."
By anticipating these challenges and preparing for them, collectors can truly enjoy the process of lost wax casting without letting glitches spoil the creative experience. Approach each casting session with a willingness to learn and adapt, and you’ll find that challenges become opportunities for growth in your craft.
Safety Considerations
In the realm of DIY lost wax casting, ensuring safety is paramount. This technique, though rewarding, involves several materials and processes that can pose risks if not handled with care. From high-temperature metals to various chemical substances, acknowledging the safety considerations will not only protect you but also enable you to enjoy the art of casting without worry. By integrating safety protocols into your casting process, you effectively minimize potential hazards, creating a safer environment for yourself and others around you.
Protective Equipment Required
When diving into lost wax casting, having the right protective equipment is as vital as the tools for the actual casting. Here’s a list of essential gear you should consider:
- Safety goggles: Protects your eyes from flying debris and harmful fumes.
- Gloves: Heat-resistant gloves are critical when handling hot metals. Leather or Kevlar options work well.
- Apron: A heavy-duty apron shields your clothes from splashes of molten metal.
- Respirator mask: Particularly useful when working with materials that might emit harmful particles or fumes during melting or pouring.
- Ear protection: If working in a noisy environment, earplugs could be beneficial.
Equipping yourself with these items ensures you are ready to tackle the tasks of creating beautiful pieces without risking your safety. A small investment in proper gear goes a long way to preserving physical well-being.
Workplace Safety Tips
Establishing a safe workspace is equally crucial. Here are some practical tips:
- Ventilation is key: Always work in a well-ventilated area. Use fans to circulate air if you're indoors, or choose an outdoor space when possible.
- Organize your tools: Keep your workspace tidy. Clutter can lead to accidents, especially when dealing with hot or heavy materials.
- Know your materials: Familiarize yourself with the substances you’re working with, including their hazards and safety data sheets.
- First aid kit: Always have a basic first aid kit handy. In case of minor mishaps, it's great to have supplies ready for immediate use.
- Emergency procedures: Be informed about what to do in case of accidents. Quick access to fire extinguishers, eye washes, and spill kits can make all the difference.
"Safety is not just a word; it's a way of life."
Implementing these safety measures may seem cumbersome at first, but they form the backbone of a sustainable and enjoyable DIY lost wax casting experience. Embracing these precautions allows you to focus on the art, tapping into your creative energies without distraction from preventable hazards.
Finishing Techniques for Enhanced Quality
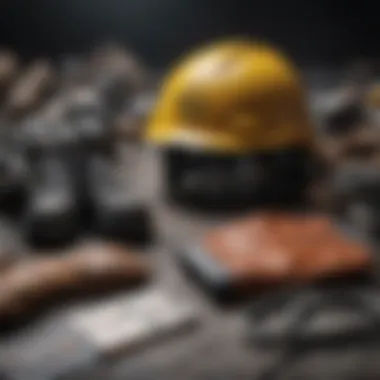
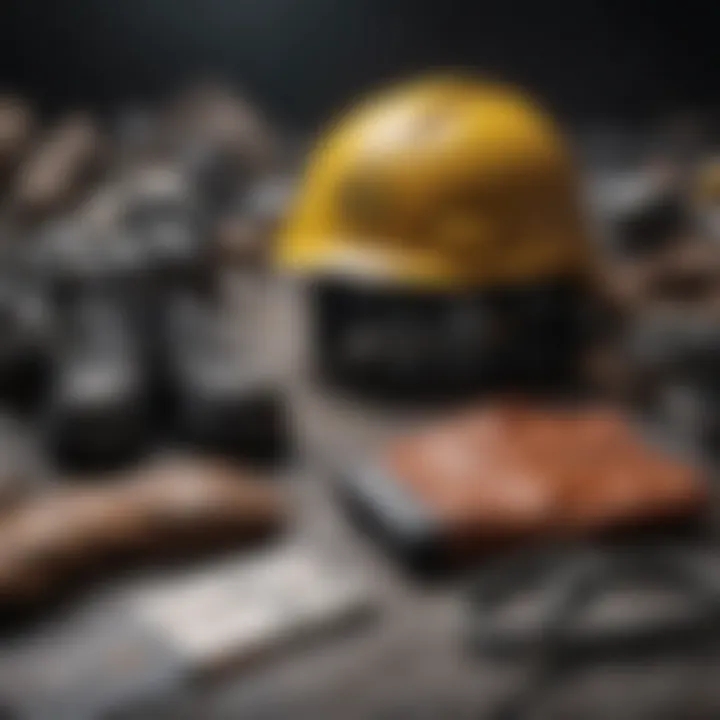
In the realm of DIY lost wax casting, the finishing phase is where your creation truly comes to life. It's not just about pouring the metal and popping it out of the mold – that's merely scratching the surface. Finishing techniques can elevate your piece from a rough cast to a polished work of art. These steps are as critical as the casting itself, allowing you to refine details, enhance aesthetics, and ensure longevity. Skipping or rushing through this part can leave you with a lackluster piece that's far from what you envisioned.
Polishing and Buffing
Polishing and buffing are at the forefront of finishing techniques. The objective here is simple: bring out the shine. After the initial removal of the mold, you might notice that the piece has casting marks, sprues, or rough edges. Instead of turning a blind eye, you can use various tools to address these imperfections.
Start with medium grit sandpaper and progressively work your way up to finer grits. For more delicate areas, smaller sanding tools are handy. After sanding, a polishing wheel attached to a bench grinder can be invaluable. Applying polishing compound to the wheel will help deliver a stunning gloss to your work. This step is like the icing on a cake – it's where your labor begins to truly shine.
- Benefits of Polishing:
- Removes minor scratches and blemishes.
- Enhances the visual appeal.
- Creates a protective layer that resists tarnish and oxidation.
Being diligent during this stage not only beautifies the piece but also adds a layer of protection, ensuring it stands the test of time.
Applying Patinas and Coatings
While polishing adds shine, applying patinas and coatings introduces color and depth to the finished product. This technique can transform the look of your piece, making it something unique. The beauty of patinas is that they can change the surface's entire character, introducing earthy tones or rich, vibrant hues.
There are several ways to apply patinas, including chemical bath treatments or heat methods. For a more hands-on approach, use a brush for detail work, or dip the entire piece for an even coat. When considering coatings, clear enamel or lacquer can seal the surface, both for aesthetic appeal and durability.
- Things to Consider:
- Choose your patina based on the metal type; not all metals will respond the same.
- Test on a small or spare piece before going full scale.
- Coatings can alter the color slightly, so keep that in mind.
"Finishing techniques, like polishing and patinas, breathe life into your creation, letting your craftsmanship truly shine."
Ultimately, investing time in finishing techniques is crucial. It’s this attention to detail that distinguishes novice from expert, ordinary from extraordinary. As a collector, the beauty and quality of your work will resonate with others, showcasing not just the material, but the heart and soul of your craftsmanship.
Resources for Further Learning
In any creative pursuit, having access to the right resources can turn potential into proficiency. Within the realm of DIY lost wax casting, the significance of ongoing education can't be overstated. Knowledge equips artisans not just with techniques but also with insights that transform basic creation into art. Here, we’ll uncover various avenues for expanding one’s knowledge and skill set—not just through traditional means, but also by connecting with others who share similar passions.
Books and Online Courses
Books and online courses serve as foundational stones in developing expertise in lost wax casting. Consider diving into specialized books that cover both theory and hands-on practices. These texts often incorporate detailed illustrations and case studies, allowing readers to grasp the complex aspects of metalworking easily.
Popular books may include titles like Lost Wax Casting: A Complete Guide by Susan Smith, which addresses not only the casting process but also tips for overcoming common challenges.
Online learning platforms, such as Coursera or Udemy, offer excellent courses on the subject. These platforms typically feature instruction from seasoned professionals who share insights that might come from years of experience. The visual nature of these courses makes learning more accessible, especially for those who benefit from seeing techniques demonstrated live.
"Education is not preparation for life; education is life itself." – John Dewey
Community Forums and Groups
No artisan works alone, and community forums can be a goldmine for gaining insights in the crafting world. Engaging with communities—whether on Reddit, Facebook, or dedicated forums—offers not just camaraderie but real-time problem-solving. Group discussions often reveal shortcuts, useful tips, or resources that a solo practitioner might miss.
For rock and fossil collectors, mingling in circles where lost wax casting is discussed can provide tailored advice that merges their existing knowledge with casting techniques. Specific groups may focus on collectible art forms that resonate with wider interests, thereby fostering a more enriching experience.
Consider visiting subs on Reddit like r/MetalCasting or Facebook groups dedicated to DIY artisans. Not only will you find advice, but often you'll encounter camaraderie that might lead to collaborative projects.
Summary
Continual learning through books and engaging with community resources creates a supportive environment for any aspiring artist or collector. In the dynamic landscape of DIY lost wax casting, fostering a thirst for knowledge can pave the path toward mastery and innovation. Embrace the journey of learning; after all, every great artisan began by acquiring knowledge piece by piece.
Closure
The journey through DIY lost wax casting opens up a trove of possibilities for collectors, providing both a practical skill set and a deeper understanding of the artistry involved in creating unique pieces. This technique, rich with historical significance and modern applications, offers enthusiasts a hands-on approach to craftsmanship.
The Future of DIY Lost Wax Casting
As we look ahead, the future of DIY lost wax casting indeed seems gleaming. More collectors and artisans are embracing this age-old method, blending tradition with contemporary aesthetics. The craft is evolving, incorporating modern materials and techniques which make the process more accessible, while still honoring its ancient roots.
Benefits of embracing this craft:
- Personalized Creations: Artists can create one-of-a-kind artworks, turning their visions into tangible pieces with emotional resonance.
- Community Growth: Online platforms and forums, such as Reddit and specialized Facebook groups, are fostering a vibrant community where enthusiasts share tips and showcase their works.
- Sustainable Practices: With a growing awareness around sustainability, many artisans are focusing on using eco-friendly materials, thus reducing waste and promoting responsible sourcing.
- Education and Resources: As more resources become available, including online courses and detailed guides, novice and experienced practitioners alike can refine their skills.
In short, engaging with the lost wax casting technique is not just about the act of creating; it’s about being part of a larger narrative that connects past and present. Collectors can take great pride in their ability to create as well as collect. The art of lost wax casting allows individuals to stamp their signature style on the pieces they make, making them more than merely items in a collection.
As the craft continues to gain traction, its methodologies and the stories behind each piece will surely evolve. So, for those thinking about diving into this practice, the waters are ripe for exploration, inviting all who dare to create.