Choosing the Best Cut and Polish Compounds for Collectors
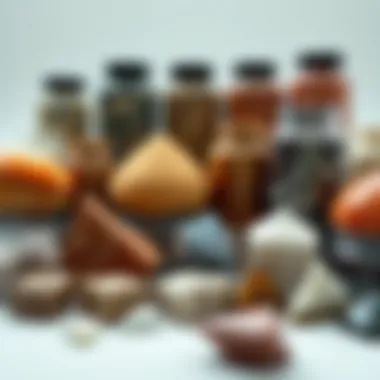
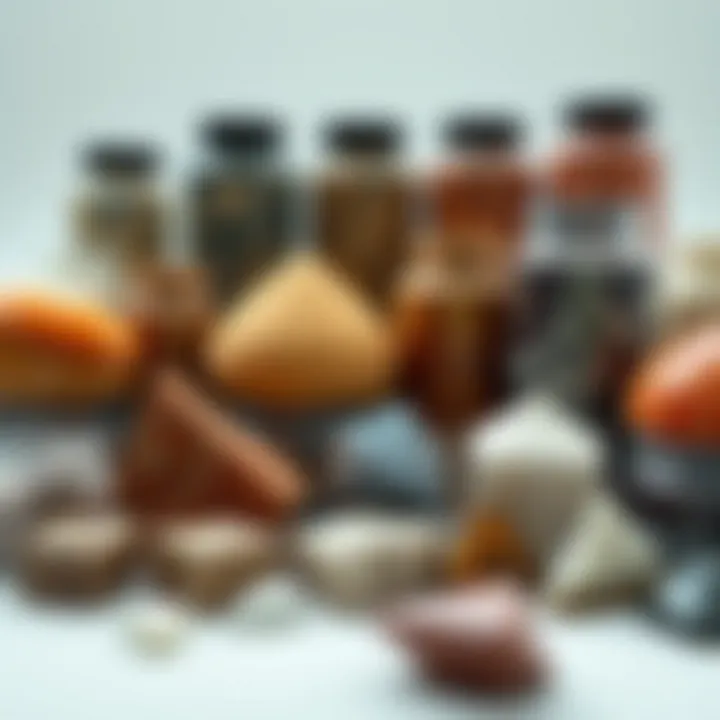
Intro
In the fascinating world of rock and mineral collecting, the beauty of each specimen shines brighter when it is polished to perfection. The cut and polish process fundamentally enhances not just the aesthetic appeal but also the preservation of these geological treasures. With numerous compounds available on the market, selecting the appropriate one can be as challenging as determining the age of a fossil. This guide embarks on a comprehensive exploration of cut and polish compounds tailored to address the specific needs and desires of collectors, whether they're seasoned veterans or just starting out.
Understanding the significance of these compounds helps collectors unlock the true potential of their collections. We will discuss various types of cut and polish compounds, the unique features of each, and how they can influence the final outcomes of polishing tasks. Furthermore, we’ll examine some common hurdles encountered along the path to achieving that illustrious shine, as well as providing expert tips to elevate polishing techniques.
This resource aims not only to serve as a practical guide but also to strengthen your connection to the beauty found in minerals and rocks, ensuring that every piece in your collection captivates the eye as much as it does your heart.
Understanding Cut and Polish Compounds
Cut and polish compounds are vital for unraveling the beauty locked within rocks and minerals. Collectors often find that the true allure of these specimens has been veiled by time, oxidation, and other environmental factors. Simply put, these compounds can unlock a specimen's potential, revealing hidden hues and patterns while providing a smooth, shiny finish. Understanding these compounds forms the cornerstone for any collector seeking to truly appreciate their collectibles.
Definition and Importance
Cut and polish compounds are essentially abrasive substances that assist in refining and enhancing the surface of rocks and minerals. These compounds work by wearing down rough edges, eliminating scratches, and adding a sheen to the surface. Unlike household cleaning products, these compounds are specifically formulated for restorative purposes, catering to the unique needs of various materials.
The importance of using the right cut and polish compound cannot be overstated. For example, applying a compound meant for softer stones on a harder mineral could lead to ineffective polishing or, worse, damaging the specimen. Thus, understanding the properties of different compounds provides collectors with a reliable toolkit for maintaining the quality and aesthetic appeal of their treasured finds.
Applications in Collectibles
The applications of cut and polish compounds are as diverse as the collectibles themselves. From shimmering geodes to eye-catching gemstones, these compounds can be used on a plethora of materials. Here are a few key applications:
- Gemstones: Polishing compounds like cerium oxide and diamond pastes enhance the brilliance of gems, making their colors pop and surfaces smooth.
- Minerals: Collectors often use these compounds to restore mineral specimens that may have lost their luster over time. The right compound can help reveal the vibrant colors and intricate patterns that define the mineral.
- Fossils: For fossil enthusiasts, polishing can highlight details that tell a story about the specimen's past. A well-polished fossil doesn't just look better; it can also give insights into its history and geographical background.
- Artistic Collections: For those dealing with artistic rock formations or sculptures, a good polish can elevate the aesthetic quality and increase the piece's desirability.
In addition to enhancing appearance, the correct use of these compounds can also aid in the preservation of the materials. By smoothening surfaces and removing contaminants, they help to mitigate the wear and tear often caused by environmental factors like humidity and UV light. Proper applications thus ensure that collectibles can be enjoyed for generations to come.
"Taking the time to use the right compounds can mean the difference between a dull rock and a stunning centerpiece in your collection."
As one explores the world of cut and polish compounds, it quickly becomes clear how essential they are for any serious collector. They're not just tools for aesthetics; they're investments in the longevity and integrity of collections. Through a deeper understanding of these compounds, collectors can appreciate their specimens to the fullest extent.
Types of Cut and Polish Compounds
Understanding the types of cut and polish compounds is crucial for collectors since different materials require tailored approaches for polishing. Each compound serves specific purposes, and selecting the right one can significantly influence the final appearance of your collectible. This section will delve into key options such as diamond polishing compounds, cerium oxide, aluminum oxide, and other specialty compounds, presenting their unique benefits and considerations for choosing the right compound for your needs.
Diamond Polishing Compounds
Diamond polishing compounds are among the most effective options available. The presence of real diamond particles allows for superior cutting and polishing capabilities. Used predominantly on harder stones and minerals, these compounds can remove scratches and surface imperfections with ease.
- Effectiveness: They excel in polishing even the toughest materials, making them indispensable for serious collectors.
- Lasting Brilliance: A significant advantage is the high level of gloss they can impart, ensuring your collectibles shine remarkably.
- Cost Consideration: However, these compounds can be somewhat pricey. It might not be suitable for every hobbyist, especially those polishing softer stones.
Cerium Oxide
Cerium oxide is a compound widely praised for its versatility and effectiveness, particularly for glass and softer stones.
- Application: When working with quartz, opal, or certain types of glass, cerium oxide is often the go-to choice for achieving a clear and polished finish.
- Ease of Use: It can be used with various methods, including hand polishing and machine polishing, giving flexibility to collectors.
- Environmentally Friendly: Another benefit is that cerium oxide is considered eco-friendly compared to some synthetic compounds.

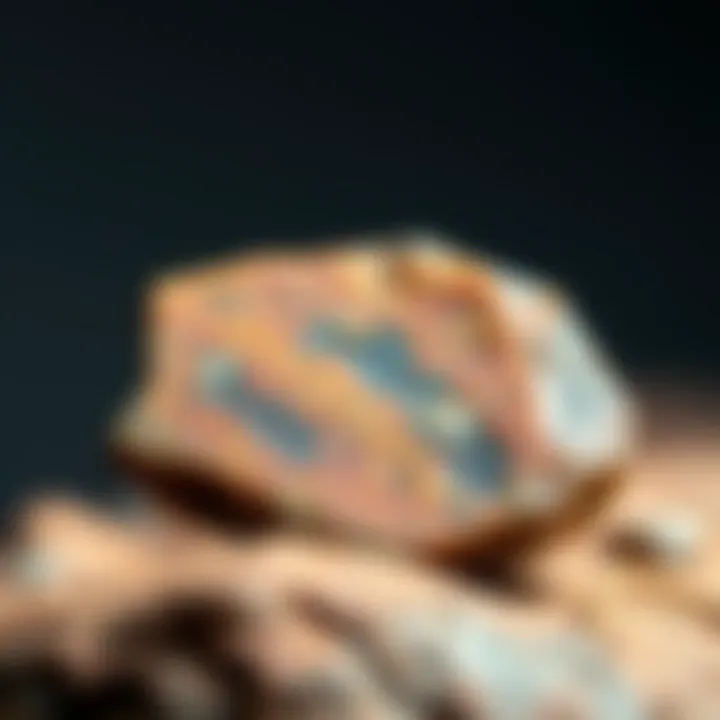
Aluminum Oxide
Aluminum oxide is another staple in the world of polishing compounds. Commonly used for metals and harder rocks, it provides a good balance between performance and cost.
- Variety of Grains: Available in different grades, from fine to coarse, aluminum oxide compounds allow users to choose the level of abrasiveness based on their needs.
- Durability: This compound is both durable and long-lasting, contributing to its popularity among collectors who polish frequently.
- Versatility: It can serve both rough and fine polishing purposes, making it a convenient choice for those working with various materials.
Other Specialty Compounds
There are various other specialty compounds tailored for specific materials or desired finishes. Knowing these compounds can enrich collectors' experiences.
- Tripoli: A favorite for polishing metals, it can prepare surfaces before applying finer compounds.
- Zirconium Oxide: Often used in industrial applications, but some collectors find it effective for certain glass finishes, offering a unique shine.
- Felt Polishing Compounds: Utilized for delicate items, felt pads combined with a soft compound can deliver surprisingly high results for detailed work.
Selecting the Right Compound
Choosing the appropriate cut and polish compound can make all the difference in preserving and enhancing your rock and mineral collections. Not only does a good compound yield a brilliant finish, but it also protects the integrity of the material being polished. Thus, understanding the nuances between different compounds and their respective applications becomes paramount, especially for avid collectors who seek perfection in their specimens.
Considerations for Different Materials
When it comes to selecting a polish compound, one size definitely does not fit all. Each mineral and rock type has its characteristics that may interact differently with various compounds. Here are some key points to ponder:
- Hardness: The Mohs hardness scale is central to make your decision. For instance, softer materials like calcite require gentler compounds to avoid damage, while harder stones like quartz can withstand more abrasive polishes.
- Porosity: Some minerals are more porous, absorbing oils or compounds, which could hinder the polishing process. Materials like malachite or granite can behave differently under specific polishing agents; thus, you might prefer a compound that’s tailored for their unique texture.
- Finish Type: The desired finish also plays a crucial role. Are you looking for a mirror-like finish, or something more subdued? For a glossy effect, cerium oxide may be your best bet, while a satin finish could call for an aluminum oxide compound.
Understanding these elements is like putting the puzzle pieces together in ensuring your rocks shine without losing their unique attributes.
Polishing Objectives
Every collector has specific goals when embarking on a polishing endeavor, which should guide the selection of a compound. Here are a few objectives you might consider:
- Enhancing Appearance: Many collectors aim to bring out the natural colors and patterns in their stones. For instance, using diamond polishing powder focuses on revealing stunning details in agate and jasper, enhancing their aesthetic appeal.
- Restoration: If the goal is to restore an old or damaged piece, you might need compounds with varying abrasiveness. Starting with a coarser compound like aluminum oxide, and then moving to a finer one can help in effectively reducing scratches and imperfections.
- Durability: Some collectors need a lasting finish, especially for items displayed outdoors or exposed to varying elements. In such cases, a compound with good sealing properties should be chosen to ensure longevity, protecting against environmental wear.
- Specialty Needs: For certain unique rocks, specialized compounds might offer better results. For example, using a compound like tin oxide is suited for opals, as it polishes while preventing cracks from developing further.
In summary, reflect on what you want to achieve before diving into the polishing process. The clearer your goals, the sharper your results can be. Understanding the interplay between material properties and polishing goals lays the groundwork for a successful polishing experience. As one seasoned collector wisely noted, "Without the right tool, the journey is often more strenuous than the destination."
The Polishing Process
The polishing process is the backbone of achieving that lustrous finish on your collectibles. Understanding it is crucial for any rock and mineral enthusiast, as this step determines not only the aesthetics but also the longevity of your specimens. It’s not just about making rocks shine; it’s about preparing them in such a way that their natural beauty is enhanced, while also ensuring their preservation for years to come.
Pre-Polishing Preparations
Before diving into the actual polishing, some groundwork is required; this is where pre-polishing preparations come into play. First things first, gather all your tools and materials. You’ll need the appropriate compounds, a polishing wheel, a clean workspace, and safety gear, such as goggles and gloves. Make sure the collectible’s surface is dirt and grime-free. You wouldn’t want to grind dirt into your specimen while polishing. A thorough wash using mild soap and water can work wonders, followed by a drying session.
Here’s a quick checklist to ensure you’re ready:
- Gather polishing compounds specific to your material.
- Clean the collectible.
- Arrange your workspace for ease of access.
- Have safety equipment on hand.
Once everything is in place, and you have a clear idea of how you plan to proceed, you can begin the polishing process with confidence.
Step-by-Step Polishing Techniques
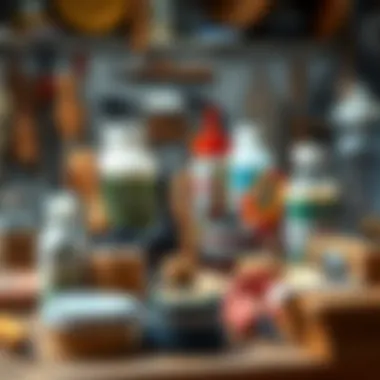
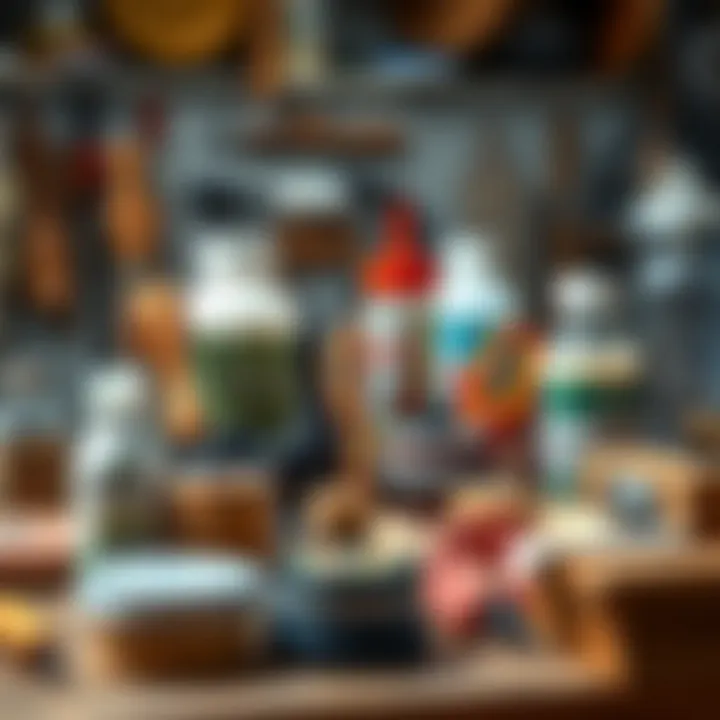
Moving on to the polishing itself, it’s crucial to follow a systematic approach. Every collectible is different, but generally, this is how to proceed:
- Choose the Right Compound: Depending on your material, pick a suitable compound as discussed in the previous sections. For example, diamond compounds work wonders for harder materials, while cerium oxide might be best for softer stones.
- Start with Coarse Grit: Begin with a coarse grit compound to shave off more significant scratches. Using a felt wheel can help distribute the compound evenly.
- Move to Finer Grits: Gradually work your way to finer grits. This not only smooths out the surface but also reduces the appearance of micro-scratches.
- Use a Soft Cloth: After reaching your desired polish, switch to a soft cloth and lightly buff the surface, removing any residue from the polishing compound.
- Inspect Your Progress: Keep a close eye on your collectible. If you notice any imperfections, you might need to repeat the polishing with the previous grit before moving to a finer one.
Following these steps closely will yield impressive results.
Common Mistakes to Avoid
While the polishing process may seem straightforward, there are pitfalls that even seasoned collectors might fall into. Here are some common missteps:
- Using the Wrong Compound: Each material requires a specific type of compound. Using one that’s too abrasive can damage softer stones.
- Skipping Cleaning: As mentioned earlier, neglecting to clean before polishing can lead to unwanted scratches or a dull finish.
- Over-polishing: It might seem tempting to keep at it, but over-polishing can strip away the natural characteristics of a stone.
- Inadequate Sealing Post-Polish: Finishing up without sealing can lead to quick deterioration, especially for softer materials.
“An ounce of prevention is worth a pound of cure.” This adage couldn’t be more applicable when it comes to collecting and polishing.
Enhancing your collection involves more than just aesthetics; it requires knowledge and an understanding of the polishing process that can dictate the quality of your showcased specimens.
Maintaining Your Collectibles
Collecting rocks and minerals can be an enriching hobby, but proper maintenance is crucial for ensuring that these pieces remain in excellent condition over time. Just like a fine wine needs the right temperature and storage, your collectibles require thoughtful care to preserve their luster and structural integrity. Neglecting maintenance can lead to deterioration, diminishing both the aesthetic appeal and overall value of your collection.
Storage Solutions
When it comes to storing your precious collectibles, you must choose options wisely to prevent damage. Using appropriate containers can make a world of difference.
- Display Cases: Consider using glass display cases to showcase your collection while protecting it from dust and physical harm. Glass allows for visibility, making it a great method for admirers to appreciate the beauty without direct contact.
- Acid-Free Materials: Always opt for acid-free storage materials. Boxes, sleeves, and cushioning made from these materials help prevent deterioration. Corrosive chemicals found in ordinary cardboard can slowly damage your specimens.
- Temperature and Humidity Control: Maintain a stable environment where temperature and humidity fluctuations are minimal. A temperature range of 65-75°F, along with humidity levels of 40-50%, is ideally suited for most minerals.
- Placement: Avoid direct sunlight as UV rays can fade colors and harm structural integrity. Storing your items in a shaded area or using UV-filtering glass in display cases can mitigate this issue.
"When it comes to storage, always remember: a little care today can save a lot of heartache tomorrow."
Regular Maintenance Practices
Periodically, you will need to perform certain maintenance tasks to keep your collectibles looking their best. Here are several practices you should incorporate into your routine:
- Dust Regularly: Use a soft, lint-free cloth to gently wipe down your collectibles. Dust can accumulate quickly, covering the fine details of your pieces. Avoid using any cleaning chemicals that might scratch or tarnish.
- Inspect for Damage: Regularly check your collection for signs of damage, such as cracks or discoloration. Early detection of any problems allows for prompt action, which can save your items from further harm.
- Reseal if Necessary: Some minerals may need resealing to maintain their finish. If you notice any deterioration in protective coatings, consider reapplying suitable wax or sealant using a soft, controlled technique.
- Keep Records: Maintain an inventory with details on each item, including its condition and any maintenance performed. This can help you track changes over time and assist in identifying when specific pieces might need extra attention.
In essence, maintaining your collectibles is not just about enhancing their beauty; it's also about preserving their value for future enjoyment and potential resale. With diligent care and smart storage, your collection will remain a source of pride for years to come.
Challenges in Polishing
Polishing your beloved collectibles is not just a task but an art form, and like any art, it doesn’t come without its hurdles. Understanding the challenges in polishing can not only save you time but also improve the health and appearance of your precious minerals and specimens. Whether you're dealing with rock, fossils, or other collectibles, acknowledging these challenges can lead to better decision-making and successful polishing outcomes.
Dealing with Surface Imperfections
Surface imperfections can be a double-edged sword. On one hand, they can detract from the visual appeal of your piece, while on the other, they can present an opportunity for learning and growth as a collector. These imperfections often manifest as scratches, pits, or dull spots that can arise from improper storage or previous handling.
To tackle these imperfections, collectors usually recommend a careful assessment of the surface. Different types of materials react uniquely under abrasives and polishing compounds. For instance, softer minerals might scratch easily compared to harder varieties like quartz or agate. Understanding this variation will help you select the right compound and technique. Here are some tips to deal with these challenges:
- Identify the Material: Not all polishing compounds work equally well on different materials. Ensure you are aware whether you’re dealing with a soft mineral or a tough gemstone.
- Select Appropriate Compounds: Use compounds designed for the specific type of imperfection. For instance, cerium oxide is often recommended for removing fine scratches on glassy surfaces.
- Light Touch: It may be tempting to press harder to get rid of the imperfection quickly, but a gentle approach often yields better results without damaging the piece.
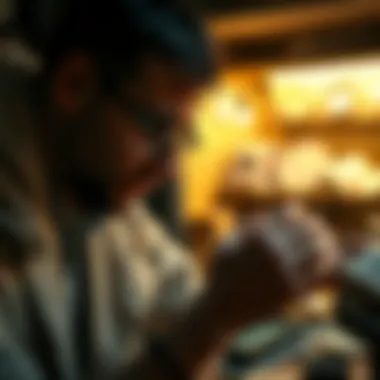
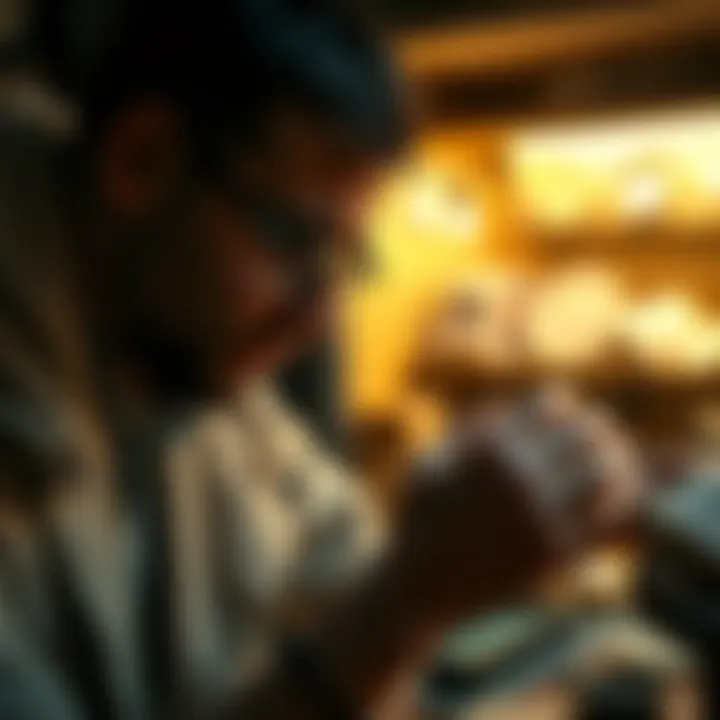
Remember, dealing with imperfection can be frustrating, but its part of preserving the history and character of your collectible.
Managing Time and Effort
Polishing is not just about making things shiny; it’s a meticulous process that requires patience and, quite frankly, a fair bit of time. Many collectors underestimate the effort involved in achieving that pristine finish, leading to rushed jobs that often compromise quality.
When you set out to polish your collectibles, consider the following:
- Plan Your Sessions: Mapping out how much time you’ll spend on each piece may help avoid burnout. Decide on a time limit for each polishing session to maintain enthusiasm.
- Prepare Your Workspace: A cluttered workspace can slow you down. Ensure that you have all your tools and compounds organized before starting the polishing process.
- Focus on Quality Over Speed: It’s easy to want to rush through pieces to see the end results, but quality should always take precedence over speed. This holds especially true with valuable collectibles, where half-done jobs can lead to irreversible damage.
- Learn as You Go: Each polishing session is a learning experience. Take notes on what works and what doesn’t. This data will be invaluable for future projects.
In the end, adequately managing your time ensures that each collectible receives the attention it deserves, improving both its aesthetic and market value. Finding a balance between effort and reward can transform not just your polishing routine but also your satisfaction as a collector.
“The road to success is dotted with many tempting parking spaces.” - Will Rogers
Being mindful of these challenges and understanding how to handle them not only leads to better results but strengthens your connection to the collectibles you cherish.
Expert Recommendations
When it comes to cut and polish compounds, getting insights from seasoned professionals can make all the difference to rock and fossil collectors. Their experience in the field provides valuable tips that can save time, prevent mistakes, and ultimately yield better results.
Understanding which compounds work best for various materials and seeing their techniques can help collectors enhance their skills.
Insights from Professional Collectors
Many professional collectors have spent years honing their polishing techniques and can offer practical advice. They often emphasize the importance of choosing the right compound which aligns with the specific type of material being polished. For instance, a collector noted, "Using cerium oxide on quartzite yielded a crystal-clear finish that I hadn’t achieved before."
These insights are more than mere truths; they often stem from countless trials and errors. Collectors suggest starting with small batches, especially for costly or rare specimens. This trial-and-error method helps in accurately determining the right compound, pressure, and time needed for polishing. Collectors also recommend keeping an open mind about experimenting with various brands and types of compounds, as individual preferences can greatly influence the polishing outcome.
Key insights include:
- Testing compounds on sample materials before using them on important collectibles.
- Understanding the specific requirements for different types of stones, like softer stones requiring gentler compounds.
- Having a comprehensive look at manufacturer recommendations, as they often provide valuable guidance on application techniques.
"Finding the right compound is like matching a puzzle piece — it requires patience, but the end result is a masterpiece."
Best Practices for Effectiveness
To ensure that collectors maximize the potential of the chosen compounds, adhering to best practices is crucial. Professionals suggest several core methods that have stood the test of time:
- Prepare the Surface: Always start with a clean workspace and ensure the specimen is free of dust and grease. This groundwork sets the stage for a superior finish.
- Use Proper Tools: High-quality polishing pads that match the compound type enhance results. There's a clear distinction between materials suitable for water-based compounds versus those designed for oil-based ones.
- Polishing Technique: Maintain a consistent hand and use even pressure during polishing. Uneven application can lead to unsatisfactory results or surface damage.
- Follow Up: After polishing, rinse the specimen thoroughly to remove any residue. It’s a simple step but incredibly effective for long-lasting brilliance.
By integrating these expert hints, collectors can refine their processes and elevate their polishing game, which not only maintains the integrity of their collections but also enhances their enjoyment of the hobby.
Culmination
In wrapping up our exploration of cut and polish compounds, it's clear that these substances play a crucial role in the preservation and enhancement of rock and mineral collectibles. Choosing the right compound isn't merely a matter of preference; it significantly impacts the longevity and aesthetic appeal of each specimen. Collectors must consider the composition of their items, the desired finish, and the specific properties of the compounds available.
Among the key takeaways from this article is the importance of understanding how different polishing compounds interact with various materials. For instance, diamond polishing compounds offer unmatched precision for hard stones, while cerium oxide shines when polishing softer minerals. Knowing when to use which compound can make or break the look of a prized collection.
Additionally, the polishing process itself cannot be overlooked. A systematic approach to polishing—from preparatory steps to the actual application of the compound—ensures a smooth finish and minimizes the risk of damaging the materials.
Maintaining collectibles also emerges as a significant theme. Proper storage and regular maintenance, including cleaning and re-polishing, can dramatically prolong the vibrance and integrity of the items. These practices are particularly relevant in light of the sensitive nature of many geological specimens.
Finally, our dive into expert recommendations emphasizes the value of community and experience within the collector’s sphere. Engaging with other enthusiasts through forums, social media, or local clubs can provide insights that aren't always obvious in literature or tutorials.
"Knowledge is power, and when it comes to polishing your collectibles, accurate knowledge can elevate your entire collection".